In the vast landscape of chemical engineering, few processes stand as iconic and fundamental as distillation. At the heart of this critical process lies the distillation column – a towering, cylindrical apparatus that plays a pivotal role in separating and purifying mixtures, ranging from crude oil to alcoholic spirits. This article aims to demystify the distillation column, exploring its inner workings, applications, and significance in various industries.
What is the Distillation Process?
Distillation is a separation technique that capitalizes on the differences in boiling points of components within a mixture. When a mixture is heated, the component with the lower boiling point vaporizes first, rises through the column, and condenses back into liquid form as it cools down. This vaporization-condensation cycle repeats, causing a gradual separation of the mixture into its individual components. Distillation columns enhance this process by providing ample surface area for efficient vapor-liquid contact and separation.
What is a Distillation Column?
A distillation column resembles a tall vertical cylinder, often hundreds of feet high, equipped with an array of trays or packing materials. These components aid in creating multiple vapor-liquid contact stages, maximizing the separation efficiency. Fig. 1 shows a typical distillation column.
A distillation column is a tall, cylindrical static equipment used in chemical engineering and industrial processes to separate and purify mixtures of liquid components based on their differing boiling points. The column facilitates the process of fractional distillation, where the mixture is heated to cause vaporization of the component with the lowest boiling point. As the vapor rises through the column, it comes into contact with liquid on trays or packing materials, leading to equilibrium and separation of components. The condensed vapors, referred to as distillate, are collected and further processed, while the remaining liquid, known as the bottoms, may contain the higher boiling point components. Distillation columns are essential in various industries, including petroleum refining, chemical manufacturing, pharmaceuticals, and beverage production, playing a crucial role in achieving product purity and quality.
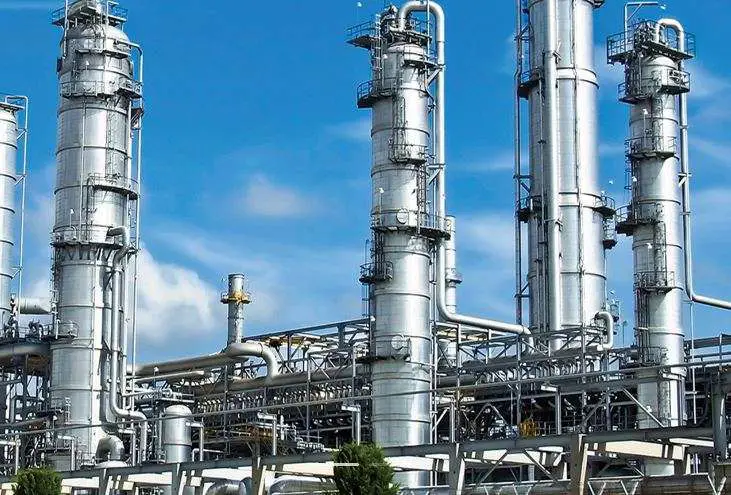
Components of a Distillation Column
A distillation column is a complex apparatus composed of several key components that work in harmony to facilitate the separation and purification of mixtures. These components ensure efficient vapor-liquid contact and separation. The main components of a distillation column include:
Reboiler:
Located at the bottom of the column, the reboiler is responsible for heating the liquid mixture to initiate vaporization. As heat is applied, the component with the lowest boiling point vaporizes and rises through the column.
Distillation Trays or Packing Materials:
These are situated within the column at specific intervals. They provide a surface area for vapor-liquid interaction, promoting equilibrium between the vapor and liquid phases. Trays consist of perforated plates placed horizontally across the column while packing materials (such as rings, saddles, or structured packing) increase surface area for better separation efficiency.
Column Shell:
The cylindrical body of the distillation column provides structural support and houses the trays or packing materials. It is designed to withstand the internal pressure and temperature conditions.
Vapor Outlets:
These are located at the top of the column and allow the separated vapor components to exit the column and proceed to the condenser.
Condenser:
Positioned at the top of the column, the condenser cools down the vaporized components, causing them to condense back into liquid form. This condensed liquid is then collected and referred to as the distillate.
Distillate Receiver:
This is a vessel or container that collects the condensed distillate from the condenser. It is designed to separate the condensed liquid from any remaining vapor.
Reflux System:
The reflux system is responsible for returning a portion of the condensed liquid (distillate) back to the column. This reflux helps maintain proper temperature and vapor-liquid equilibrium, improving separation efficiency.
Reflux Drum:
The reflux drum is a vessel that collects and temporarily stores the returning reflux liquid before it is reintroduced into the column. It helps regulate the flow of reflux and prevents sudden disturbances in the column operation.
Bottoms Outlet:
Located at the bottom of the column, the bottom outlet allows the heavier components of the mixture to be withdrawn as a liquid stream. This stream may contain the least volatile components.
Column Internals:
These include various accessories and devices used to optimize column performance, such as distributors for even liquid distribution on trays, collectors for vapor distribution, and demisters to prevent the entrainment of liquid droplets in the vapor stream.
Pressure Relief System:
Distillation columns are operated under specific pressure conditions. A pressure relief system, such as safety valves or rupture discs, is incorporated to ensure the column’s integrity in case of pressure buildup.
Working Principle: Fractional Distillation
The fundamental principle behind distillation is fractional distillation, which leverages the concept of equilibrium. As the vapor rises through the column, it encounters the liquid on the trays or packing. The vapor-liquid equilibrium leads to the separation of components, with the component of a lower boiling point vaporizing more readily and rising to a higher tray. The trays or packing materials facilitate this equilibrium at multiple stages, enhancing the separation efficiency. Fig. 2 below shows the typical products that are obtained from a crude distillation column at different temperatures.
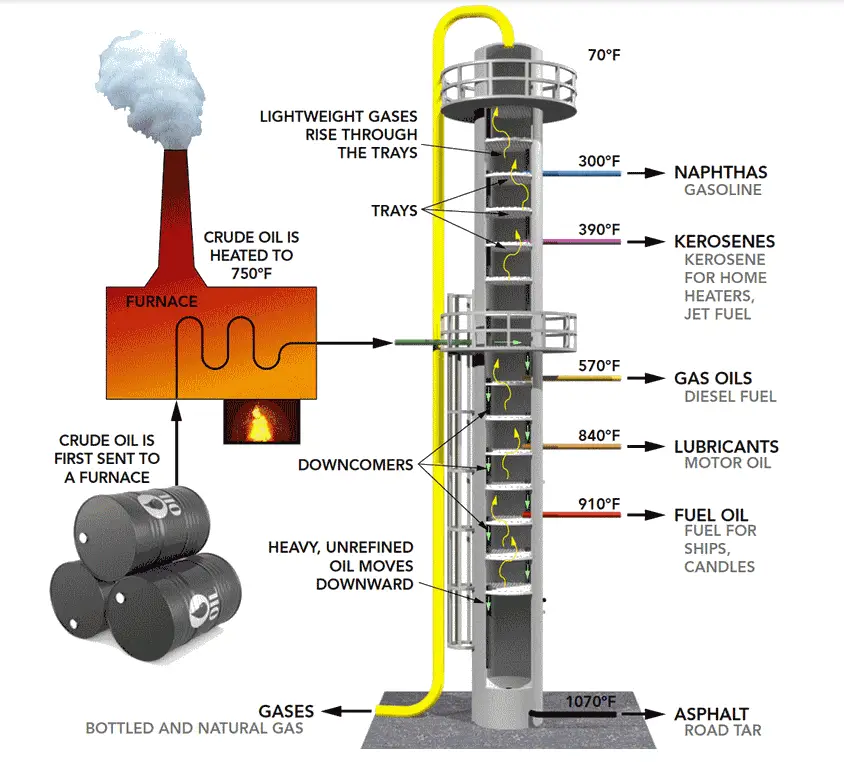
Types of Distillation Columns
Distillation columns come in various types, each designed to address specific separation challenges and optimize efficiency based on the characteristics of the mixture being processed. Here are some common types of distillation columns:
Batch Distillation Column:
In batch distillation, a fixed amount of mixture is loaded into the column, processed, and then the products are collected. It’s suitable for small-scale operations, research, and when dealing with mixtures that are difficult to separate. Batch distillation is commonly used in the production of high-quality spirits and certain pharmaceuticals.
Continuous Distillation Column:
Continuous distillation columns manage an uninterrupted flow of feed. Only in the event of an issue with the column or adjacent process equipment do interruptions occur. These columns excel at accommodating substantial throughput and represent the more prevalent than batch distillation columns. Continuous Distillation columns can be further divided into the following:
- Fractionating Column: This is the most common type of distillation column and is widely used in various industries. It includes trays or packing materials to create multiple vapor-liquid equilibrium stages, enabling the separation of a wide range of components based on their boiling points. Fractionating columns are extensively used in petroleum refining, chemical manufacturing, and beverage production.
- Packed Distillation Column: These columns are filled with packing materials (such as rings, saddles, or structured packing) that provide a large surface area for vapor-liquid interaction. Packed columns are often used for applications where heat and mass transfer are critical, making them suitable for separating heat-sensitive or difficult-to-distill mixtures.
- Azeotropic Distillation Column: This type of column is designed to handle azeotropic mixtures, where two or more components have similar boiling points and form a constant-boiling mixture. Special techniques, such as the addition of an entrainer or using extractive distillation, are employed to break the azeotrope and achieve effective separation.
Reactive Distillation Column:
In reactive distillation, chemical reactions occur simultaneously with the separation process. This integration of reaction and separation allows for higher product yields, reduced equipment footprint, and improved energy efficiency. Reactive distillation is commonly used in the production of chemicals, such as esters and biodiesel.
Vacuum Distillation Column:
Vacuum distillation operates at reduced pressure to lower the boiling points of components, making it suitable for separating heat-sensitive materials or reducing thermal degradation. Vacuum distillation is commonly used in the refining of crude oil and in the production of high-quality products, such as essential oils.
Steam Distillation Column:
This method involves the introduction of steam into the distillation process. Steam distillation is particularly useful for separating volatile compounds from heat-sensitive materials, such as extracting essential oils from plants.
Extractive Distillation Column:
In extractive distillation, an entrainer or solvent is added to the mixture to alter the relative volatility of the components, making separation easier. This technique is often used for separating azeotropic mixtures or for challenging separations that cannot be achieved through conventional distillation.
Molecular Distillation Column:
Molecular distillation is a high-vacuum distillation process used to separate compounds with very high boiling points or those that are thermally sensitive. It is commonly employed in the production of pharmaceuticals, edible oils, and other high-value products.
Applications of Distillation Column
Distillation columns find applications across various industries, each with its unique requirements:
- Petroleum Refining: In crude oil refining, distillation columns separate crude oil into fractions based on different boiling points, yielding valuable products like gasoline, diesel, and jet fuel.
- Chemical Production: Distillation is vital in the production of chemicals, pharmaceuticals, and specialty chemicals, enabling the separation and purification of complex mixtures.
- Beverage Industry: Distillation columns are integral to producing alcoholic beverages like whiskey, vodka, and gin. They separate alcohol from fermented mixtures to create high-proof spirits.
- Environmental Applications: Distillation columns play a role in environmental processes such as water purification and wastewater treatment, removing impurities through separation.
Challenges and Innovations
While distillation columns are highly effective, they also face challenges such as energy consumption and the separation of azeotropic mixtures (where components have similar boiling points). Ongoing research focuses on enhancing energy efficiency, utilizing advanced column designs, and incorporating hybrid separation technologies to overcome these challenges.
Conclusion
The distillation column stands as an engineering marvel that underpins countless industrial processes. Its ability to separate and purify mixtures has revolutionized industries ranging from energy to beverages. As technology advances and sustainability becomes increasingly important, the distillation column will continue to evolve, ensuring the efficient and environmentally responsible separation of mixtures for generations to come.
Morning Kurmar can i please have your contact details?
fetsmosia4@gmail.com
Always insightful and helpful. Simple and straight to the point.