What is Pressure Piping?
Pressure piping is any piping that carries fluid under internal or external pressure. ASME B31 serves as the design code for pressure piping. All process piping, power piping, and pipelines all are examples of pressure piping.
What is High-Pressure Piping?
High-pressure piping is the piping that the owner designates as being a high-pressure fluid service. Appendix IX of ASME B 31.3 provides design rules for High Pressure Piping. These rules are slightly different from normal pressure piping. A high-pressure piping system as per ASME B31.3 is a system for which the design pressure is more than that allowed by the ASME B16.5 Class 2500 (PN 420) rating for the specified design temperature and material group. For stress analysis of piping systems suitable dynamic analysis and fatigue analysis is performed to avoid or minimize conditions that lead to detrimental vibration, pulsation, or resonance effects in the piping. However, in this article, we are not discussing these piping systems.
Effect of Pressure on Piping System
With an increase in fluid pressure in a piping system
- Pipe thickness increases increasing the rigidity of the system
- Flange rating increases which increases flange and valve thicknesses.
- An increase in thickness increases the loads on pipe supports and tie-in points.
- The overall cost of the piping system and design increases
Effects of Temperature on Piping System
- Temperature change creates expansion or contraction in the piping system creating thermal stresses.
- At high temperatures (T>Tmelting/3), creep starts.
- With an increase in temperature, allowable stress values (Sh) reduce, making the system more prone to failure.
- With the change in temperature, the corrosion mechanism and corrosion rate change.
- At lower temperatures, reduction of Charpy V-Notch values and KIC (Fracture Mechanics) are observed requiring special considerations.
High Temperature and High-Pressure Piping
With an increase in temperature and pressure, piping systems become more and more critical from a stress point of view. So, Piping Stress Engineers have a really tough time qualifying all their systems as material allowable drops with an increase in temperature. This article will try to list the impacts that these two process parameters impart in piping stress systems.
Major Characteristics of High Temperature and High-Pressure Piping
With respect to high temperature and high-pressure conditions in piping, the following are the typical features-
The higher the pressure in the pipe, the higher is the thickness of the pipe. Higher thickness means more rigid and less flexible. All these cause a higher load on the supports, and higher frictional components acting axially and laterally, which in turn can cause higher loads on the equipment nozzles.
The higher the temperatures, the higher are the pipe movements – vertical, axial, and lateral. This also causes higher frictional forces in the system. At the same time, high-temperature piping has low allowable stresses as with an increase in temperature material allowable stress value reduces. So the qualification of stress systems becomes more difficult.
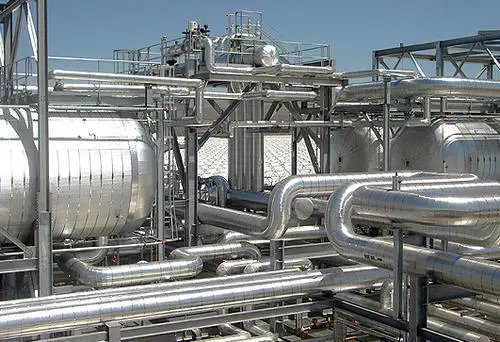
Due to high movements, there are high strains and stresses in the piping system. This, in turn, leads to higher forces and moments on the supports and equipment nozzle.
Pipe supporting becomes complicated with the need to use special type supports like spring hangers, snubbers, anti-friction slide plates, etc. Also, with an increase in thermal movement long shoe supports come into the picture.
Depending upon the layout limitation use of expansion joints may become essential. Expansion joints are very expensive and difficult to maintain. Design Life of expansion joints is normally very less as compared to the piping systems.
The higher the temperature, the lesser is the allowable strength of the material. Consequently the more, the pipe and fittings will become prone to failure. The valves, gaskets, studs, etc. have to be of material to withstand that high temperature.
The choice of Studs/bolt materials becomes important at high temperatures.
For lines with high operating temperatures, hot bolting is done to take care of the expansion of the bolts at that high temperature.
Another thing that needs to be considered is the relaxation of bolts over a period of time. Special washers might be required to be used in such cases.
Welding external attachments/ appurtenances on very high-temperature pipes can cause thermal differential and induce cracking in the attachments.
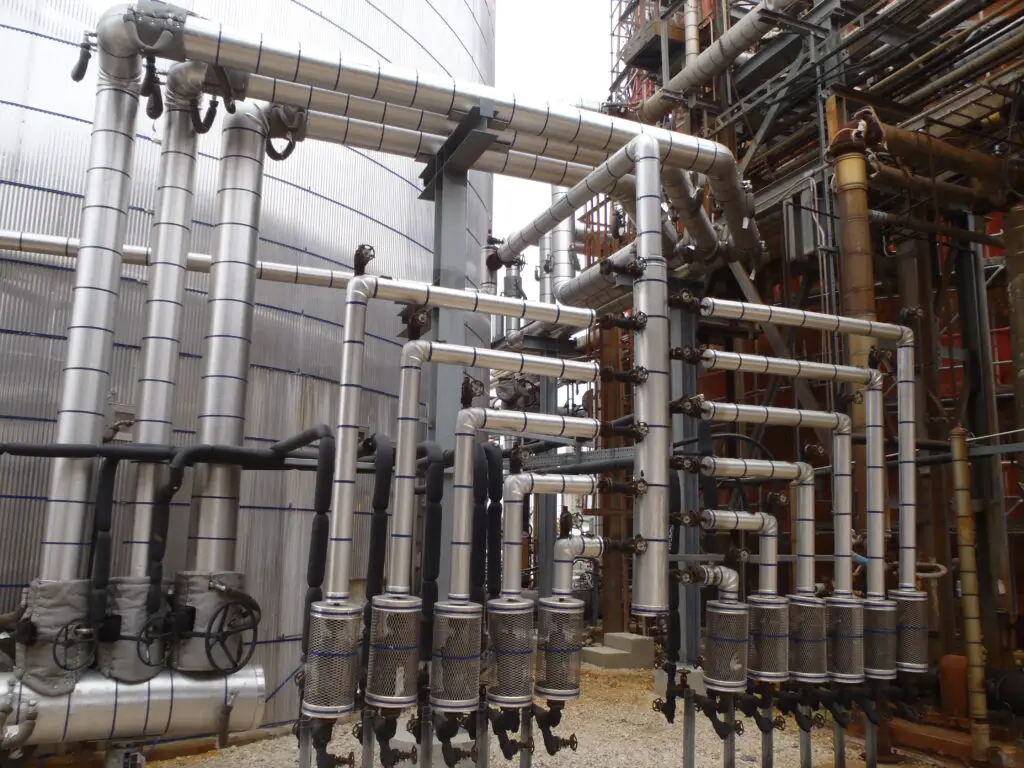
During plant start-up, there is a possibility of two-phase flow in long pipes seeing high temperatures leading to thermal bowing.
At very high temperatures, the line may operate in a creep range leading to the permanent yielding of the materials. Thus such piping when cooled down during plant shutdowns does not come back to the original position of the piping. This is termed as the phenomenon of Thermal shakedown.
The material selected for high-temperature and high-pressure piping should be resistant to corrosion at higher temperatures.
As the temperatures increase in high-temperature piping systems, the insulation thickness is increased. Also at temperatures of the order of 650-700 degrees C, Ceramic wool is to be used instead of Rockwool which is used for normal 300-400 degree C piping. More insulation thickness means more weight loads in the system.
In places where the pipe displaces to a high degree over supports, cold pulls or offsets might be required.
Examples of High-Temperature Piping Systems
Some examples of the high-temperature piping system are listed below:
- The Aromatics Platformer Reactor lines are at a temperature of about 520 degrees C
- The Slop Wax / Vacuum Residue lines from the bottom of the Crude Column are at a temperature of 424 degrees C
- The Vacuum Column – Heater Transfer line from the Vacuum Heater to the Vacuum Column is at a temperature of 396 degrees C
- The FCCU Flue Gas line going to the Expander – Power Recovery Train at a temperature of 714 degrees C
- In Coker, the coke cutting (hydro-jetting) lines see a pressure of 350 kg/cm2.
- In Vacuum Gas Oil Unit the Reactor Circuit has lines with 360 degrees C and 97 kg/cm2
- In CPP the Turbine lines at a temperature of 524 degrees C and Pressure of the order of 126 kg/cm2.
- The typical HP Steam (High-Pressure Steam) system has a temperature of up to 400 degrees C and a pressure of approximately 45 kg/cm2.
- The typical MP Steam system has a temperature of up to 260 degrees C and a pressure of approximately 18 kg/cm2.
- The typical LP (Low-Pressure) Steam system has a temperature of up to 200 degrees C and a pressure of approximately 5 kg/cm2.
Based on the temperatures and the pressure in the piping, the material of construction needs to be selected.
- Carbon Steel can be used up to 427 degrees C
- Alloy Steel can be used up to 650 degrees C
- Stainless Steel can be used up to 550 degrees C
Few more Resources for you..
Piping Design and Layout
Piping Materials
Piping Stress Analysis
Piping Stress Analysis using Caesar II
Piping Stress Analysis using START-PROF
Friction force is not dependent on temperature, neither it increases with the increase in pipe movement. See your bullet : 5
Dear Sir, Where Can I buy high temperature 3-inch high pressure copper pipe in Toronto, Ontario
I am trying to gather budgetary costs for a piping system that will circulate 350 C water based fluid at 3500 psi. Corrosion is not anticipated to be a significant issue although we expect cycling from hot to ambient periodically. I’m not experienced in piping design but would like to know what grade I could get by with for 2″ nominal (2.375″ OD) schedule 160 or possibly sch 80 if it met the pressure and temperature requirement. The system will be in use for less than one year, about 1000 to 1500 hrs total.
Ciao
Thank you for this information dear collegue!