What is Micro Tunneling?
Micro Tunneling (M/T) is a process that uses a remotely controlled Micro Tunnel Boring Machine (MTBM) combined with the pipe jacking technique to directly install product pipelines underground in a single pass. This process avoids the need to have long stretches of an open trench for pipe laying, which causes extreme disruption to the community.
Important Features of Micro Tunneling
Micro tunneling is currently the most accurate pipeline installation method. Line and grade tolerances of one inch are the micro tunneling industry standard. This can be extremely important when trying to install a new pipeline in an area where a maze of underground utility lines already exists.
Micro tunneling can be used to install pipes from eight inches (200 mm) to twelve feet (3600 mm) in diameter. Therefore, the definition of micro tunneling does not necessarily include size. The importance of trenchless pipe jacking for the laying of supply and disposal conduits and for replacing pipes is growing continuously.
Importance of Micro Tunneling in the Oil Industry
Increasingly, the existing technologies are failing to install new pipelines in demanding oil fields and rough terrains. This happens due to:
- High groundwater
- Difficult ground condition. (E.g. Mountains – situated nearby many oil fields, rocky ground, perennial rivers, etc.)
- Ground with Mixed Gravel
While drilling in gravel with the present HDD technique, the chances of ground collapse are high. So, in this case, no drilling is possible through HDD.
Solution for all the above-mentioned problems – MICRO-TUNNELING
Advantages of Micro Tunneling
- Reduced disruption of the community
- Reduced liability for personal injury and property damage
- Increased service life and asset value for the utility owner
- Increased worker safety
- Reduced restoration costs
- Precise installation
- Wet Conditions/Marine Crossings: often the only option
- The faster rate of progress than the convention
- A reduction of earth movement to a minimum
- Consideration of residents and the environment
- Lowering of groundwater is unnecessary
- Minimal influence on traffic
Wherever horizontal directed drilling technology (HDD) cannot be used:
- for difficult and rough gravel soils,
- soils with erratic blocks,
- in city centers,
- where there is no space to extend and retract,
Micro tunneling methods are a true alternative.
Shaft/Well Construction
Construction of a Shaft / Well is one of the primary jobs for carryout Micro Tunneling.
Purpose: To get a safe working platform under the desired depth.
Bottom Plugging
Plug the bottom of the shaft with Reinforced Cement Concrete using a concrete box with the help of divers and a crane. Additives are used to prevent the cement from dissolving in water and increase the plasticity of the concrete for achieving a better flow of concrete into the cutting edge.
After successful bottom plugging the shaft is ready for Micro Tunneling work.
Micro Tunneling Machine(Fig. 1)
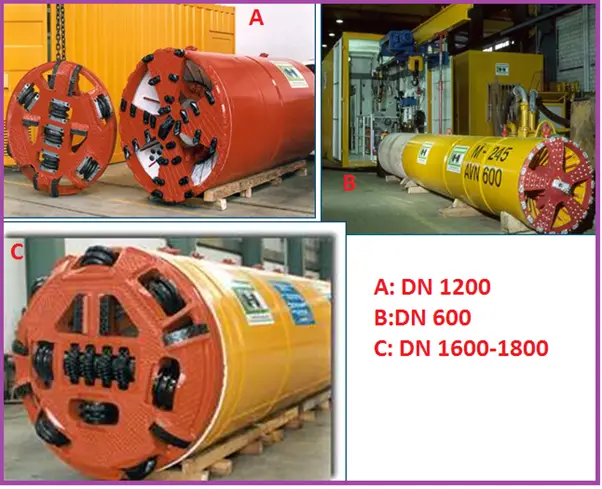
Micro Tunneling Method (Fig. 2)
Micro tunneling is a high-performance and environmentally friendly alternative to pipeline construction with trenches; it can also be used in the most demanding of circumstances: groundwater and difficult geologies are no problem for micro tunneling, and it has proven to be a very good method of avoiding obstructions in city centers.
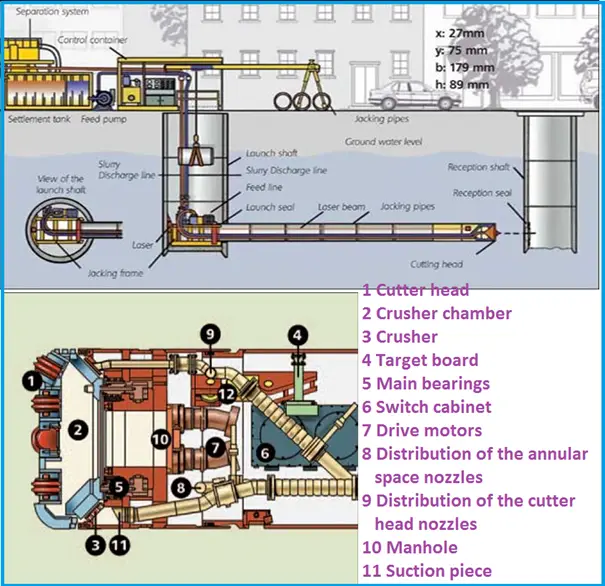
The cutter head (1) removes with its tools – cutters, knives, chisels, or discs – the surrounding soil. This is taken to the crusher chamber (2). This is where any stones are crushed (3). Water is initially pumped into the crusher chamber in a closed circuit, mixed with the soil there, and then pumped back out of the drill hole.
The separating system then separates the water from the soil. The soil is disposed of and the water is pumped back into the crusher chamber. The pipe is pushed into the soil using the hydraulic cylinders in the jacking frame. A laser beam dictates the location of the pipe axis. The target board (4) reports the position of the laser point to the machine operator in the control container. Hydraulic cylinders (12) mean that the cutter head can be angled, thus correcting the position. The operator controls the entire system from the control container.
Pipe Jacking Method
Pipe Jacking is a method of Tunnel Construction where hydraulic Jacks are used to push especially made pipes through the ground behind a tunnel boring machine or shield. The method provides a flexible, structural, watertight finished pipeline as the tunnel is excavated.
Pipe jacking utilizes a jacking device to push pipe horizontally into the ground, forming a continuous string of pipe. Material is excavated as the pipe is pushed in. A thrust wall is constructed to provide a reaction against the jack. High-pressure jacks provide the substantial forces required for jacking concrete pipes.
Pipe jacking is an economical alternative to and much less disruptive than using open-cut construction to install new underground pipes. Because it is performed with a closed system, pipe jacking decreases the risk of environmental contamination during construction.
Jacking Frame (Fig. 3)
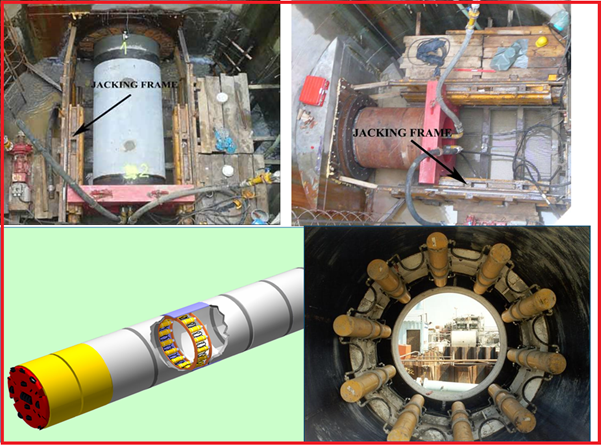
The jacking frame is the main device that plays a vital role in Pipe jacking. The pipe is pushed into the soil using the hydraulic cylinders in the jacking frame.
Inter jack (Fig. 3)
An inter-jack station is a ring of hydraulic jacks within a steel framework that is inserted into the pipe string at strategic points. Each inter jack divides the pipe string into more manageable jacking lengths. Each length, whether between jacking frame and inter jack, inter jack and inter jack, or inter jack and face, can be advanced individually and independently from the rest of the pipe string. It is the equivalent of having several smaller pipe jacks in operation at the same time in one bore, with each inter jack using the pipe length behind it as its thrust wall.
The use of inter jack reduces the potential for pipe failures since the maximum force on any individual ‘sub-string’ depends on the number of pipe sections plus the friction factor over that length of pipe. Each inter jack is controlled independently from the operator’s station and can, where necessary, be individually lubricated with the correct control and lubrication pump set-up.
ELS (Electronic Laser System) Control system for pipe jacking
In order to recognize the position of the Tunnel Boring Machine (TBM) (horizontal and vertical deviations, the pitch and roll tendency of the machine, and the yaw angle) suitable sensor technology is necessary to guide a TBM. ELS is an intelligent sensor unit with a sturdy metal case. The device is roughly the size of a shoebox and is watertight up to 5 meters submersion. It is dry-filled with an inert gas under slight pressure. The ELS is installed on the back of the tunneling machine so that the guidance laser makes contact with the target. The device is connected via a cable that supplies the power and transmits the measurement results.
Bentonite / Micro tunnel Lubrication Units
Designed primarily for the mixing and pumping of Bentonite and Polymers used as lubricants for Microtunnel and Pipejack construction, the Concrete Eurodrill range of Microtunne Lubrication Units (MLUs) offer complete systems including mixers, storage tanks, and injection pumps to meet a variety of requirements. They all incorporate the well-proven Colcrete Colloidal Mixer, which produces a very stable product, which resists water separation and retains its lubrication properties for longer when injected. A variety of pumps can be fitted, usually based on well-proven grout pumps such as the Mocol and Minicol ranges.
JACKING PIPES
Micro tunneling techniques require the jacking of a pipe into the ground using often high jacking forces, the correct choice of pipe with the ability to withstand the required jacking forces during installation and the right properties in terms of final product performance is as important as choosing the right machine to install it in the first place.
A wide range of pipe materials is available for installation using pipejacking and micro tunneling techniques, the choice depending on the requirements of the client, the ground conditions, transportation costs, and the length of the pipeline. Materials including reinforced and un-reinforced concrete, polymer concrete (concrete aggregate within a matrix of resin), glass fiber/resin-based pipes, vitrified clayware (both glazed and unglazed), steel, ductile iron, and also plastics are available as jacking pipe. In the majority of cases, the pipe material is either concrete or clayware, manufactured for pipe jacking to strict standards.
Separation Plant
The separating system separates the water from the soil. The soil is disposed of and the water is pumped back into the crusher chamber.
Different soil conditions – Different M/T Machine
Rocks: Modern technology offers new, uncomplicated options even when drilling through rocks with high degrees of hardness. In places that previously required detonation or mortise work, micro tunneling is now seen as a reliable alternative.
Stones and erratic blocks: Innovative technology creates new options: The use of mixed drill heads, which are fitted with knives and cutters for cohesive soils, as well as chisels and discs that can crush erratic blocks or rock layers, means that even the most difficult of soils can be drilled.
Flowing soils: Soil-aligned apertures in the cutter head mean that the soil excavation can be adjusted to suit the mass required by the pipe displacement.
Special Areas of Use: You can reap the rewards of micro tunneling, especially in demanding areas: no river is too broad, and no water is too deep.
River Crossings: River tunnels with excavations are largely a thing of the past. Even the broadest currents can be crossed safely using micro tunneling.
Overview of Construction Site (Fig. 4)
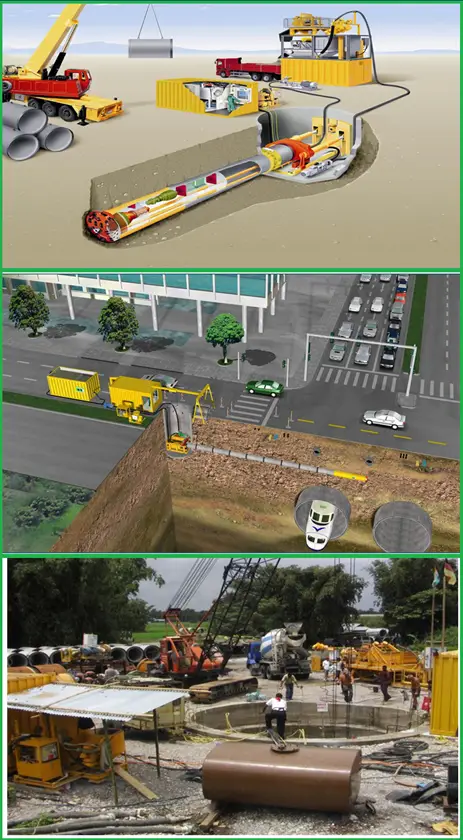
Online Video Courses related to Pipeline Engineering
If you wish to explore more about pipeline engineering, you can opt for the following video courses
- Pipeline Stress Analysis using Caesar II
- Design of Underground Pipeline Supports
- Hot Tapping in Piping and Pipeline Industry
- Buried or Underground Pipeline Stress Analysis using Caesar II
Few more Pipeline related useful Resources for You..
Underground Piping Stress Analysis Procedure using Caesar II
Comparison between Piping and Pipeline Engineering
A Presentation on Pipelines – Material Selection in Oil & Gas Industry
Corrosion Protection for Offshore Pipelines
Start up and Commissioning of the Pipeline: An Article
DESIGN OF CATHODIC PROTECTION FOR DUPLEX STAINLESS STEEL (DSS) PIPELINE
AN ARTICLE ON MICRO TUNNELING FOR PIPELINE INSTALLATION
A short presentation on: OFFSHORE PIPELINE SYSTEMS: Part 1
Factors Affecting Line Sizing of Piping or Pipeline Systems
very interesting
Does the above technology of Micro tunneling is possible for Oil & Gas Steel pipelines having double random length i.e 15 to 20 meters (API 5L pipeline).
Secondly if possible then what would be the methods for testing pipelines i.e Radiography of joints & hydro tests.
I shall be highly obliged on your reply.
Zeeshan Ahuja
Senior Piping Design Engineer
SMEC Oil & Gas
Islamabad Pakistan
Hi Hello,
just want to ask if it is possible that through MT we can install directly the carrier pipe? no using of a casing?
Hope to hear from you.
thank you,
Anita
I am looking for a quote for 24″ steel casing installation by micro tunneling.
Please contact me at (415) 994-0895