Welding is a fundamental process in many industries like oil and gas, construction, manufacturing, shipbuilding, automotive, and aerospace. It is used to join metals together by applying heat, pressure, or both to form a strong, permanent bond. While welding is a reliable and efficient method of joining materials, it must be done correctly to ensure the structural integrity of the welded joint and to avoid defects or failures. One critical aspect of the welding process is maintaining the proper minimum distance between two welding operations.
In this article, we will explore the minimum distance requirements between two welding operations, why they matter, and the factors that influence this distance.
What Is the Minimum Distance Requirement?
The minimum distance between two welding operations refers to the space that must be maintained between two adjacent welds. This is important for several reasons, such as avoiding heat-affected zone (HAZ) overlap, ensuring adequate access for welding tools, and promoting the overall quality and strength of the weld.
Welding operations are generally separated by a certain distance to:
- Prevent Heat Interference: Overlapping heat-affected zones can weaken the material around the weld, compromising the joint strength.
- Minimize Distortion: If two welds are too close together, the heat from one weld can affect the other, causing distortion in the welded materials.
- Allow for Proper Cooling: Sufficient space allows the welded material to cool down between operations, reducing the risk of thermal stress and cracking.
- Ensure Accessibility: Proper spacing ensures that the welder can work efficiently and safely, reducing the risk of weld defects due to inadequate access.
- Compliance with Industry Standards: Certain industries or specific applications have strict welding standards that must be adhered to, including guidelines on the minimum distance between adjacent welds.
Why Is It Important to Maintain a Minimum Distance Between Two Welds?
Ensuring a proper distance between welds helps maintain the quality, strength, and safety of the structure being welded. Below are the key reasons why this distance is crucial:
Avoiding Overlapping Heat-Affected Zones (HAZ)
Welding creates a localized region of high heat, known as the heat-affected zone (HAZ), which can alter the microstructure and mechanical properties of the material. When two welds are made too close together, the HAZ of one weld can interfere with the HAZ of the adjacent weld. This can lead to reduced strength, increased brittleness, and a greater likelihood of cracking.
Prevention of Distortion and Warping
Welding generates significant heat, which causes the welded material to expand. As the weld cools, it contracts, leading to residual stresses. If two welds are too close, the thermal expansion and contraction of one weld can distort the adjacent weld, leading to warping or misalignment of the material.
Ensuring Proper Cooling
Cooling rates play a critical role in determining the final properties of a weld. The cooling process can be affected by the proximity of adjacent welds. When the cooling rate is not controlled or uniform, it can lead to issues such as weld cracking or inadequate solidification. Keeping an adequate distance between welds allows each weld to cool properly.
Providing Space for Inspection and Repair
Weld inspection is a critical part of the quality control process. A sufficient gap between two welding operations ensures that the inspector has the necessary space to assess each weld for defects such as porosity, undercuts, and cracks. Additionally, if a repair is needed, the welder will have enough space to carry out the repair work without damaging the surrounding area.
Reducing the Risk of Hydrogen-Induced Cracking
Hydrogen-induced cracking (HIC) is a common issue in welding, especially with high-strength steels. When the base metal is exposed to moisture or hydrogen during the welding process, it can lead to the formation of cracks. Maintaining a minimum distance between welds reduces the likelihood of hydrogen accumulating in one weld, which could then migrate to the other and cause cracking.
Factors Influencing Minimum Distance Requirements
Several factors influence the required distance between two welding operations. These include the material being welded, the welding process used, and the application’s requirements.
Material Type
The type of material being welded plays a significant role in determining the minimum distance between welds. For example:
- Low-carbon steel: Low-carbon steels are more forgiving and may tolerate smaller gaps between welds.
- High-strength steel: Higher-strength materials, such as high-carbon steels or alloys, are more sensitive to heat input and require more space between welds to prevent cracking or warping.
- Non-ferrous metals: Materials like aluminum and titanium have different thermal properties and may require a different minimum distance compared to steel. For instance, aluminum requires a slower cooling rate to avoid brittleness, necessitating more space between welds.
Welding Process
The welding process used affects the heat input and cooling rate, which, in turn, influences the minimum distance between welds:
- Arc Welding: Arc welding processes like Shielded Metal Arc Welding (SMAW) or Gas Tungsten Arc Welding (GTAW) tend to have higher heat input, requiring a larger minimum distance.
- Laser Welding: Laser welding, which produces a concentrated heat source, may require smaller gaps due to the rapid cooling associated with the process.
- TIG or MIG Welding: These processes offer more control over heat input and could potentially reduce the need for larger gaps between welds, depending on the material and application.
Weld Size
Larger welds produce more heat and can affect adjacent welds. As the size of the weld increases, the required minimum distance between welds also increases to prevent issues like distortion or overlapping HAZ.
Type of Joint
The configuration of the joint being welded can also influence the distance between adjacent welds. Butt joints, fillet welds, and lap joints each have different heat distribution characteristics, which will affect the recommended minimum distance.
Service Conditions
The intended service conditions of the welded structure can impact the minimum distance requirement. For example, structures subjected to high stress, pressure, or extreme temperatures may require more stringent requirements to maintain joint integrity.
Industry Standards and Codes for Minimum Distance Between Welds
Various organizations and standards bodies have developed guidelines for welding practices, including the minimum distance between welds. The minimum distance between welds is determined by the relevant codes and standards being followed. Below are some guidelines from commonly referenced codes and standards:
- American Welding Society (AWS) D1.1: The minimum spacing between welds should be at least four times the thickness of the thinner part being joined, with a minimum of 1 inch (25 mm).
- American Society of Mechanical Engineers (ASME) Boiler and Pressure Vessel Code (BPVC) Section VIII, Division 1: The minimum distance between welds should be at least three times the thickness of the thinner part being joined, with a minimum of 1 inch (25 mm).
- European Welding Federation (EWF) and International Institute of Welding (IIW): The minimum distance between welds should be at least three times the thickness of the thinner part joined, but no less than 2 mm.
It is important to recognize that these guidelines are not comprehensive, and other codes and standards may have varying requirements. The actual minimum distance between welds can also depend on factors such as the materials used, the intended application, and the welding method employed. For precise guidance on the minimum distance between welds for a particular application, it is essential to refer to the relevant code or standard and/or consult a qualified welding engineer.
Minimum Distance Between Welds as per International Codes and Standards
The required minimum distance between welds is influenced by the welding process being employed. In most cases, this distance is determined by factors such as the material being welded, the joint design, and the parameters of the welding process. For instance, the typical minimum gap between fillet welds is around 1/16 inch (1.6 mm), though this value may change based on the material, joint configuration, and welding technique used.
Here is a table listing the minimum weld distance requirements by some of the widely used codes and standards:
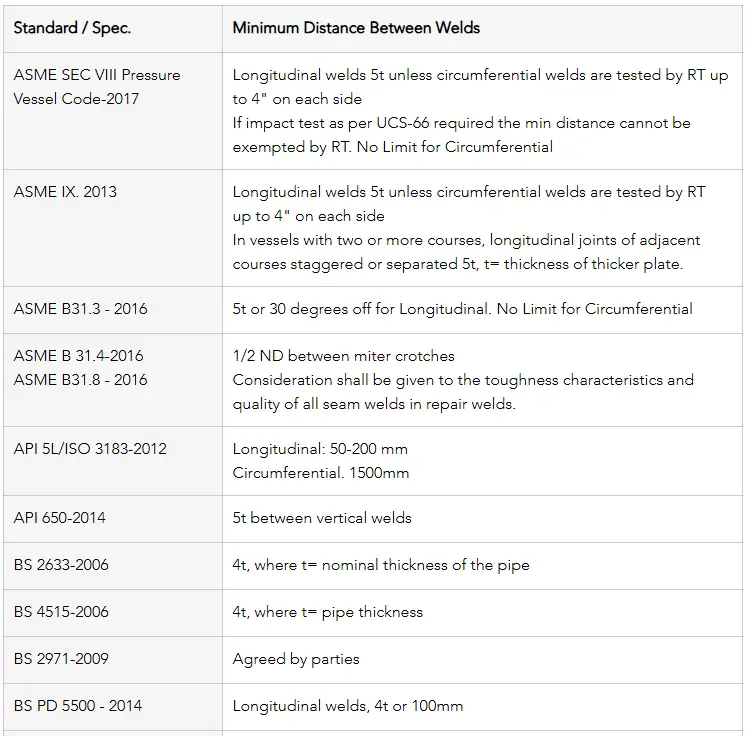
AWS vs CWB
The American Welding Society (AWS) and the Canadian Welding Bureau (CWB) are two important organizations in the welding industry, each serving their respective countries. Although they share a similar focus on promoting welding safety, education, and certification, they differ in several key areas.
Founded in 1919, the American Welding Society (AWS) is a non-profit organization based in Miami, Florida, with over 70,000 members globally. The AWS is dedicated to advancing welding science, technology, and applications, which include processes like brazing, soldering, and thermal spraying. To achieve this, the organization develops codes, standards, and educational initiatives while also certifying welding professionals and inspectors.
The AWS is responsible for more than 200 codes and standards related to welding and joining processes. One of the most well-known standards is the D1.1 Structural Welding Code for Steel. These documents provide essential guidelines for welding procedures, welder qualifications, and inspection protocols. In addition, the AWS offers various educational opportunities such as webinars, seminars, and online courses. It also provides certification programs for welders and welding inspectors to ensure competency in the field.
On the other hand, the Canadian Welding Bureau (CWB), a non-profit organization founded in 1947 and based in Milton, Ontario, focuses on welding safety, education, and certification within Canada. The CWB serves over 6,000 members worldwide and offers a range of certification services for welding personnel and welding inspectors.
Similar to the AWS, the CWB has its own set of codes and standards, including CSA W59 Welded Steel Construction, which is comparable to the AWS D1.1. The CWB also provides training and educational resources, such as seminars, courses, and online tools. Additionally, the CWB certifies welding professionals and inspection experts through its certification programs.
Despite many similarities between AWS and CWB, there are notable differences. The AWS has a broader international presence and its standards are used globally, while the CWB is primarily focused on the Canadian market. Moreover, while both organizations offer certification for welding personnel and inspectors, the criteria and requirements for certification may vary between them.
In summary, the AWS and the CWB are both key players in the welding industry within their respective countries. They emphasize welding safety, education, and certification, and each has a set of standards to guide welding practices. However, their global reach and certification procedures differ, reflecting their distinct roles in the industry.
In conclusion, the minimum distance between two welding operations is a critical factor in ensuring the quality, strength, and safety of the welded structure. By maintaining adequate spacing between welds, you can avoid overlapping heat-affected zones, minimize distortion, promote proper cooling, and facilitate effective inspection and repair.
To determine the specific minimum distance for a particular welding project, consider the material being welded, the welding process used, the joint type, and the service conditions. Adhering to industry standards and codes will help ensure that your welding operations meet the necessary requirements for safety and performance.
Ultimately, the right spacing between welds contributes to the long-term durability and reliability of the structure, ensuring that it can withstand the demands placed upon it.