Managing a project is not so easy. There is every possibility that something can go wrong. Starting from the project initiation to its successful closure, every project has to go through several phases of the project life-cycle. Depending on the type and scope of projects, the number and name of these project phases may vary. Still, there are some main phases that are applicable to all types of projects. Each project phase has its own goals, deliverables, activities, and processes that must be completed before moving to the next one. In this article, we will explore each phase of an oil and gas project in more detail.
What is a Project?
A project is a series of tasks that need completion to get a specific outcome. Every project is unique in that it is not a routine operation. A specific set of inputs & outputs are designed for a singular goal in the form of a project or service.
Projects can range from simple to complex. Depending on the complexity of the project, one or more people can manage the project. Projects are often described by a project manager or executive of the client. It is required to finish the work within a time frame because every project has its deadlines.
What is Project Management?
Project management is the art of planning, controlling, and executing a project to ensure a successful outcome. The primary challenge of project management is to achieve all the project goals within the deadlines.
The aim of project management is to produce a complete project meeting the client’s objectives. Often the goal of project management is to shape or reform the client’s objectives. The client’s objectives influence all decisions of project managers, designers, contractors, and sub-contractors.
Project Life Cycle
A project life cycle specifies the sequences of stages that a project involves from its initiation to its closure. Refer to Fig. 1 which clearly explains the Project Life Cycle for any project.
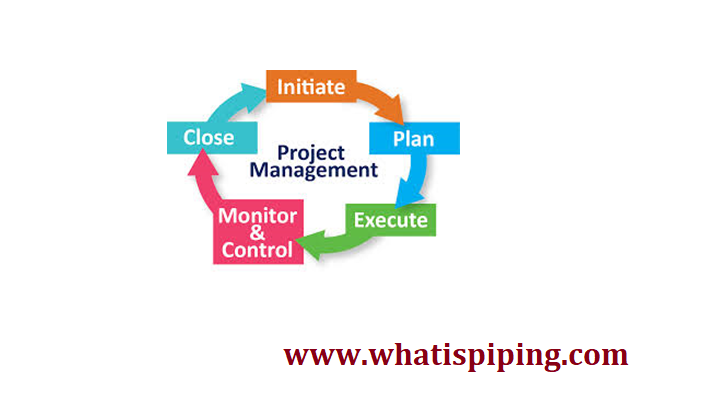
Project Phases / Stages
There are 12 major phases/stages involved in oil & gas projects. Refer to Fig. 2 which specifies all these project phases.
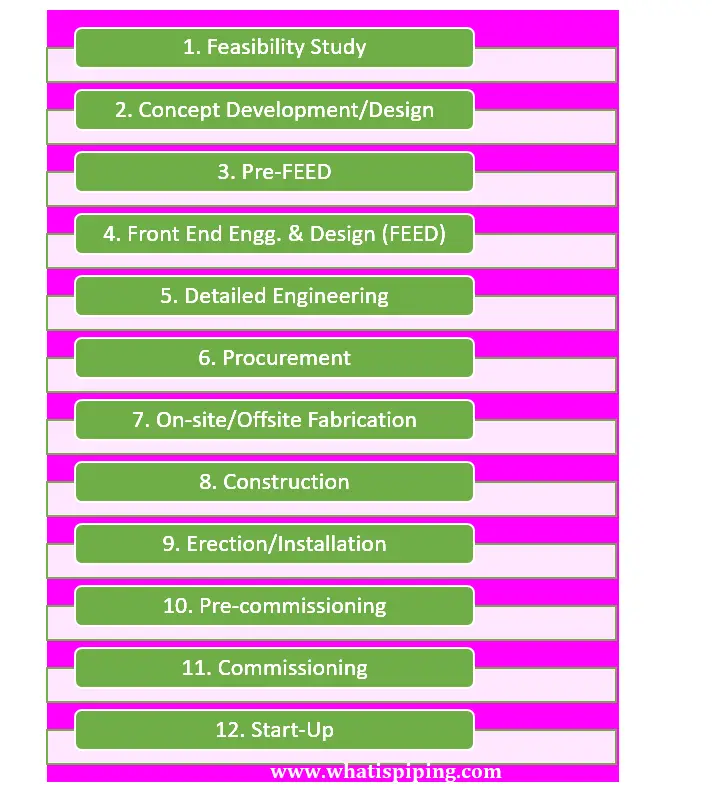
What is a Feasibility Study of a Project?
A Feasibility Study/analysis is a process to determine the validation of an idea. The feasibility Study ensures that a project is legally, technically, and economically justifiable. It tells the owner/client whether a project is worth the investment.
In some cases, a project may not be beneficial. Various Parameters like requiring too many resources, low market demand, and unavailability of nearby resources, etc. can contribute to such assessment. Such projects are not profitable.
Types of Feasibility
Four types of feasibility assessments are done before proceeding with a project. These are:
- Economic Feasibility.
- Legal Feasibility.
- Operational Feasibility.
- Scheduling Feasibility.
Concept Development / Conceptual Design
Concept development is the first step of the multiphase process involved in creating a new product. For any project or product design process, Conceptual design is the very first stage. The drawings or models are used to describe the proposed product. A set of integrated ideas and concepts are decided in this stage.
Conceptual design is a set of disciplines that contributes to identifying the optimal design at nominal operating conditions of industrial processes/products in the field of engineering.
It evaluates the best design variables and operating conditions to maximize the profit of the organization.
Deliverables of Conceptual Design
- PFD (Process Flow Diagram).
- Functional requirement.
- Process Design.
- HMB (Heat and Material Balance).
Note that the Feasibility Study and Conceptual Design is performed by the Company or Owner
Pre-FEED (Preliminary Front-End Engineering Design)
Pre-FEED develops the project design basis and places boundaries to constrain and define the concept. This process can be simplified by the following activities:
- A design basis is developed that outlines the operating characteristics of the project.
- The technical and economic feasibility of the design basis will be determined during this exercise.
- The allocation of additional funds is evaluated for proceeding with engineering and design.
- Project boundaries are developed to deal with rules and regulations, National and local laws, governance, and content issues.
Engineering Deliverables of Pre-FEED Stage
- Material selection and specification.
- Plant capacity requirements.
- Product specifications.
- Critical plant operating parameters.
- Available utility specifications.
- Process regulatory requirements.
- All other operating goals and constraints desired by the plant owners/operators/engineers.
- Definition and sizing of main equipment resulting in in-process specifications.
- Preliminary plot plan.
FEED (Front End Engineering Design)
FEED or Front End Engineering Design is the most basic engineering conducted after the completion of the conceptual design and feasibility study. At this stage, various studies take place to figure out technical issues and estimate rough investment costs.
This work is normally contracted to the EPC (Engineering, Procurement, and Construction) contractors. The final product of this stage is the FEED Package. FEED package amounts to dozens of files and will be the basis of bidding for the EPC Contract. It is important to reflect the client’s intentions and project-specific requirements in the FEED Package. It avoids significant changes during the EPC Phase. It is essential to maintain close communication with the client. Sometimes, the client stations at the Contractor’s office during the work execution.
Deliverables of FEED
- Final Plot Plan.
- P&ID (Piping and Instrumentation Diagram)
- MDS (Mechanical Data Sheet)
- Line List
- Instrument and Valve data sheets.
- General Arrangements Drawings for main equipment and main pipework.
- Cost estimating.
- HAZOP Report.
- Project Execution Plan, HSE Plan
- Operational philosophies
Detailed Engineering
Detailed engineering is a study, which creates every aspect of project development. Detailed Engineering includes all the studies before the project construction starts. Detail engineering includes
- the extraction of all the essential information from the basic engineering drawings/FEED
- calculations to provide the exact drawings in detail for the production, fabrication & erection items
- the details of the entire project along with the precise bill of quantities and specifications for each of the equipment.
- It also involves 3D modeling.
Deliverables of Detailed Engineering
- Equipment List.
- Process data-sheet.
- Management/review of vendor drawings.
- Thermal rating and vibration analysis of heat exchangers.
- Review of P&ID – Jointly with Client.
- Valve List
- Control valve datasheet.
- Relief valve datasheet.
- Detailed piping drawings, including isometrics and stress calculations.
- Bill of Quantity (BOQ).
- MTO (Material Take-off)
- Start-up procedures, Operating and Commissioning manuals.
Click here to learn about the major differences between Feed and Detailed design projects
Procurement Phase
The Procurement phase of a project involves a series of activities and processes by the purchase or procurement team. It is necessary to acquire the necessary products or services from the best suppliers/vendors at the best price and quality. Such products include raw materials, equipment, machinery, instruments, etc.
An effective procurement strategy involves:
- a financial plan to manage the budget.
- a good plan to manage the workflow and production deadlines.
- keeping everything aligned with the client’s objectives.
- ensuring a smooth supply of required items for construction.
In the oil and gas industry, procurement plays an important role in ensuring the supply of products, items, and services within budget allocation, ensuring on-time delivery on-site and cost savings without compromising quality and safety.
Procurement Cycle
In Procurement, the Procurement cycle lists the key steps in a cyclical order. This makes understanding each procurement step easier. Refer to Fig. 3 for a typical Procurement Cycle with important procurement steps.
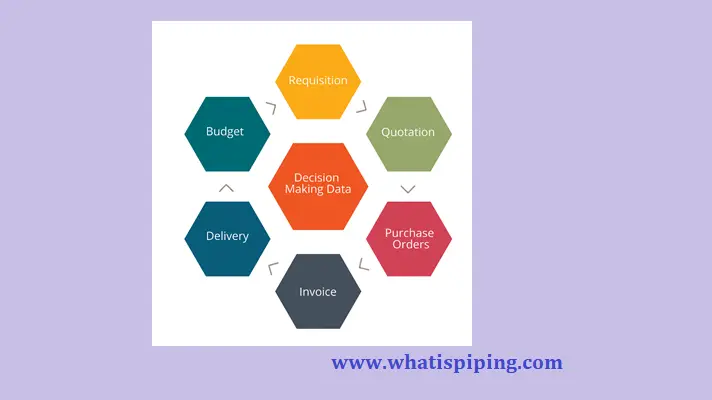
Note that Pre-FEED, FEED, Detailed Engineering, and Procurement are performed/executed by the EPC Contractor
Onsite and Offsite Fabrication
Offsite Fabrication is a process of fabrication and assembly of parts or systems at a location away from the project like a workshop. Offsite fabrication provides a cost-benefit, allowing the assembly of units that would not be able to be fabricated on-site due to cost, tooling, availability of resources, or space restrictions. Nowadays it is at a peak in the industry.
Onsite Fabrication is the fabrication held at the project site. After the offsite fabrication, it is still required to do fabrication work at the site for connecting the different pieces of equipment, pipes, and other systems for installation purposes.
Note: Fabrication is executed by the Contractor/vendors.
Construction Phase
Construction is the activity of putting different elements and objects together. It should follow a detailed design plan, and the installation drawing to create a structure, equipment, building, etc. While constructing large structures/buildings, A clear action plan is a must.
One should know the dimensional coordinates of the specific location. It involves clearing, excavating, and leveling the land. It also involves other activities associated with the structure, building, and other properties of the plant.
Erection and Installation Phase of the Project
Erection is the process of cleaning and preparing the place for the installation of a new machine or equipment. It involves arranging equipment/elements or tools for the installation purpose. This is part of the mechanical completion.
Installation is the process of assembling the different parts of the system by welding or mechanical joints. The process involves connecting the electrical connections for the creation of a single system.
Mechanical completion:
The activities involved in the installation of the equipment and piping system are known as mechanical completion. It is done to make sure everything is installed as per the drawing and after the clearance of this stage commissioning and testing occurs.
Note: Construction, Erection, and Installation are executed by the Contractor.
Pre-commissioning Phase
Pre-Commissioning activities start after the system achieved mechanical completion. Pre-Commissioning activities include cleaning, flushing, drying, leak test, and hydro-testing of the equipment, piping system, and other operating systems. Sometimes pre-commissioning activities are included in mechanical completion but this depends again on the contract conditions or the requirement of the project.
Note: Pre-commissioning & commissioning is executed by the Contractor and the operator of the plant.
Commissioning Stage
Commissioning is a verification process used to confirm that a facility or the process has been designed, procured, fabricated, installed, tested, and prepared for operation or production by the blueprint, design drawings, and specifications provided by the client. It is the second last stage of the project.
Note: After the completion of the commissioning, if no error is found in the system then the referred drawing becomes an “as-built drawing”.
As-built drawing: This is the final drawing sheet of the plant and is used for future modification, maintenance, and review purposes.
Start-up Phase
After the successful completion of the testing of the processing system or the plant, It is time for the green signal to start production.
The write up is so educative. I will need more of it through my email
I’m an Mechanical Engineer . I know the engg gives us a path to work in different industries but I love to work in design field So, I did Post graduation diploma in Piping Engineering . I got the knowledge that how industries were work , By using my technical skills I will explored this industries.
Hi I am an mechanical engineer I want to know from where you have completed your Post graduation diploma in Piping.
Please let me know the details of the institute
Very good article. Keep up the good work sir.
is there any guidance, it may some sort of international standards or codes which rules phases of project described above?
Well detailed and quite educative.
Thanks so much for sharing.
It is very safe to say that there are at least 1000 project management tools, but there are reasons behind the success of Primavera P6 and the loyalty of its users.
An absolute beautiful article. Thanks
Most of the technical specifications are generated at FEED stage, not detailed engineering.
M. Benashur
DEAR SIR,
The article is comprehensive and very well done. Thank you.
I only have one general comment. Sometimes the phases from the pre- Feasibility, Feasibility, and BED/FEED are considered as the conceptual phases.
An excellent article write up, simple, Informative and direct to the subject. very well done