Pipe Support friction plays a significant role in pipe stress analysis. All piping stress engineers must be aware that while modeling supports or restraints we have to enter the frictional coefficients at the pipe support surfaces. The value of this coefficient depends on the supporting surface material and surface roughness. During the project bidding stage (ITB Document) the client generally provides the information regarding which friction factor to be used for which surface.
Also, every EPC organization prepares its own guideline for using standard friction factors in case not available in the ITB document. The following write-up will try to provide an idea regarding which coefficient of friction to be used in what situation. This can be used as a guide only. However, project-specific data or information will override any word mentioned here.
What is Friction Coefficient?
The coefficient of friction provides a measure of the amount of friction existing between two sliding surfaces. The coefficient of friction is defined as the ratio of the Normal force to the resisting force. As the friction coefficient is a ratio of two forces, it is a unit less or non-dimensional.
Coefficient of Friction for Various Surfaces
The coefficient of friction factor depending upon the supporting interface (i.e, the junction between the Top of the Steel and the Bottom of the Pipe or Bottom of the Shoe/Cradle) shall be applied at all vertical restraints (+Y or Y supports) locations as mentioned below. But if ITB for any project provides separate data then those data shall be considered.
- Carbon Steel to Carbon Steel: 0.3
- Polished Stainless Steel to Polished Stainless Steel/Graphite: 0.15
- Teflon to Teflon/ Polished Stainless Steel: 0.10
- Concrete to Carbon Steel: 0.5
- Pipe to Roll Support: 0.01 to 0.05
- Teflon to Carbon Steel: 0.2
- Pipe on Sand Soil (pipe laying on the sand): µ=0.4
There is various philosophy among EPC companies regarding the use of coefficient of friction for guide and directional anchor supports. Some organizations prefer not to use any frictional co-efficient for horizontal support. However if used the same can be taken from the above table (normally 0.3 is used if no special arrangement is made).
Using Support Friction in Caesar II
Refer to Fig. 1 to understand the Support Friction Co-efficient application philosophy in the Caesar II input screen.
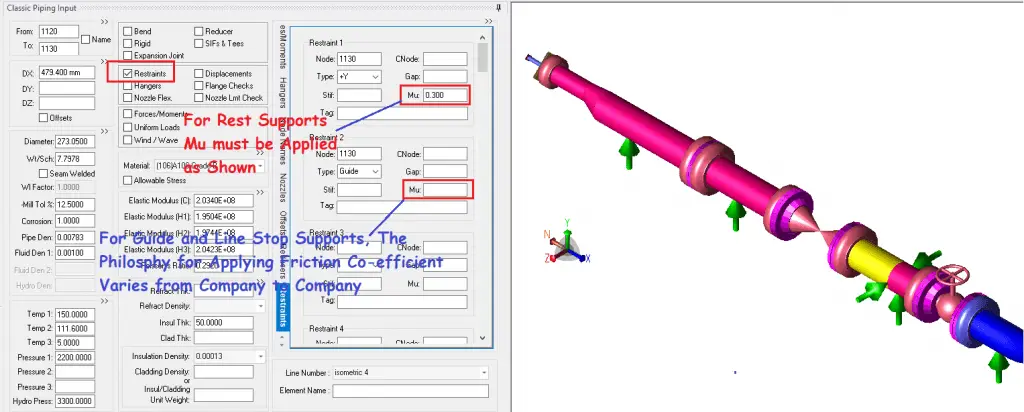
Friction coefficient must be applied for all vertical sliding restraints or Rest types of supports. However, there is variation in the philosophy of friction coefficient application for guide and line stop supports. Some organization uses friction co-efficient for guide and limit stops while some organizations do not use it.
Again there are differences in support friction considerations for occasional stress calculations. Some organizations make friction multiplier in caesar ii load cases as zero. They believe that occasional events like seismic, wind, slug, etc being dynamic events the application is quick and friction does not get time to act in those instances. Where some organization keeps the friction multiplier value as 1. So, follow what your organization is following during the aboveground pipe stress analysis.
Significance of Support Friction
As you can see in Fig. 1, In CAESAR II, the friction is activated at any restraint by entering a non-zero Mu value. Generally, no friction factor is used while supporting using rigid hangers.
In general, friction will always be present whenever a pipe will move. The frictional force will act against the pipe movement. The maximum frictional force against the pipe sliding will be Mu (Coefficient of friction) times the vertical restraint force. If a pipe movement is in the +X direction the frictional force will act in the -X direction. Friction creates a non-linear effect on the piping system.
As friction opposes pipe displacement, it will create high stress on the pipe and higher loads on the connecting equipment.
Many a time in Caesar you may find that due to the non-linear effects, the iteration in Caesar II analysis does not converge. In that situation deleting the friction from that specific support node can converge the solution and the result is obtained.
Reducing Pipe Support Friction Forces
To optimize structural design, qualify expansion stresses, and qualify nozzle loads, it may be required to reduce frictional loads. As we know,
Frictional force=Coefficient of Friction (Mu) * Vertical Normal Force at the support location.
As vertical force is usually constant, the friction force can easily be reduced by changing the friction coefficient.
This is the reason that pipe stress engineers sometimes used SS/PTFE/Graphite plates at the contact surfaces to reduce friction coefficient which in turn reduces the horizontal frictional force. Special support design arrangements are made to use PTFE/Graphite/SS plates.
However, some organizations argue that with the passing of time, the reduced friction coefficient does not remain valid and the friction coefficient increases. Also, there may be the inclusion of sand particles in between the contact surfaces where a frequent sand storm is expected. So, many organizations do not prefer to use PTFE/Graphite slide plates to reduce frictional loads.
Sometimes, pipe roller supports or Spring Hanger Supports are used in place of normal resting supports to reduce support friction.
Some Important Consideration related to Pipe Support Friction Coefficient
In case when Sliding Plate is required, add the comment “(PTFE/Graphite) Sliding Plate Required” and mention friction factor μ=0.1 /0.15 respectively depending on temperature” on the stress sketch. Use Teflon (PTFE) Slide plate up to a temperature of 204 degrees Centigrade, above which use a graphite plate (up to 540 degrees Centigrade).
Normally the friction factor shall not be applied when modeling bottom type spring. But sometimes ITB document/Client could insist on friction modeling of bottom type springs, in that situation friction factor could be applied as per requirement.
When the pipe/shoe is supported on the welded rod on the structure, a friction factor of 0.25 shall be considered.
For buried or underground pipes frictional forces are very high.
For Compressor and Turbine piping systems, some organization wants to qualify the equipment nozzle loads in both cases, using friction and without friction.
For Zigzag pipelines, it’s preferable to check pipeline displacements without support friction and decide on the sleeper or support dimensions. There are many instances of pipe movement at the support location to be more than the pipeline design displacements considering support friction. So, by designing support dimensions without considering the friction effect solves the problem.
Further Studies on Support Friction in Pipe Stress Analysis
To learn more about pipe support friction and its implication the following paper by L C Peng is highly beneficial: Treatment of Support Friction in Pipe Stress Analysis by L C Peng
Online Course on Pipe Support Engineering
If you want to learn more details about pipe support engineering then the following online course is a must for you:
Thanks
Is is necessary to apply friction at anchor points and limit stops ?
Anchor means fully locked in the 6 direction by welding with structure. There is no possibility of sliding.How friction will come?
With reference to Sathya, Is it also to include friction at Guide locations ?
As per Standard industry practice friction is not considered for guide and line stop supports. However practically there will be friction. So its up to you whether to use friction or not. Check client requirement regarding the same.
It is depend on the arrangement/type for guide and line stop support. If you use strut/restrut/ 3way (rest+guide+ axial stop) shoe support without gap then friction is not applicable.
Where Can I have this kind of information please
Where should I add friction factor in CAESAR II piping input for bottom type spring ?
Thanks.
It is available in the Caesar II manual.
Is it applicable for all size pipe?
Hi from mexico,
How should I consider friction if i have a antivibrating support that uses rubber.
Related to this, I have some doubts about the gap too, because rubber is elastic so, when pipe expands there is a movement allowed by the rubber, I´m very interested to know the opinion from a more experienced person, I have looking all around but I have not found anything about this, so I think it is more related to experience considerations.
(sorry for my english)
The friction factors quoted are significantly different to those from engineering text books especially the steel to steel value of 0.3. How can such a low value be substantiated in view of this?
Thanks a lot for your always kind and informative post.
I’m a piping stress engineer in DSME and want you to advise on how to apply co-efficient differently for the following cases in Caesar II.
1. When using U-bolt(Carbon steel) with Teflon sliding pad to support carbon steel pipe.
2. When using Plastic clamp(Polypropylene) to support carbon steel pipe.
As far as I know, Plastic clamp is preferred to be used to support the lines with high pressure and I currently need to know the differences between two restraint types above in Caesar II programme.
Thanks in advance.
I see nobody has any comment regarding to exceptionally low friction factor of 0.3 for steel to steel. The use of this value is against all recognisable engineering data – so why do people not question it???
Simply follow the client requirements and provide. It will be vary from client to clients
Thanks for the awesome post.
hi Anup,
What support type would you use in Caesar to model a pipe riser with 2-3 clamps (friction supports) and how would you deal with the grip slip force?
Thanks
Hello, can you reference a text or code where I can find recommended friction factors for each support typology.
Thanks
Thank you, its help me a lot to better understanding.
Please could someone tell me the friction coeficient to soil -HDPE