Both ASME Sec VIII Div 1 and Div 2 are used for pressure vessel design. Both divisions contain mandatory requirements, specific prohibitions, and non-mandatory guidance for pressure vessel materials, design, fabrication, examination, inspection, testing, certification, and pressure relief. So in a broad sense, both may seem to be similar but there are few distinct differences between both Divisions. In this article, we will explore the major differences between ASME Sec VIII Div 1 and Div 2.
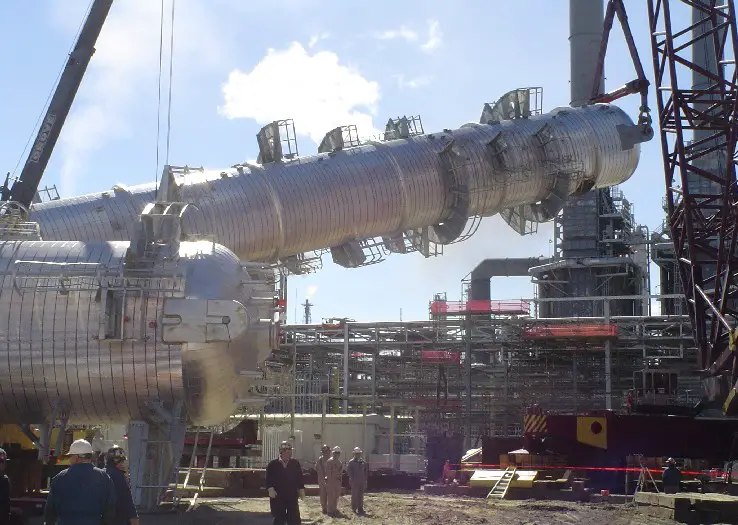
ASME Sec VIII Division 1 vs ASME Sec VIII Division 2
ASME Section VIII, Division 1 is a straightforward design-by-rule method used by engineers to design pressure vessels based on rules. It’s conservative and usually leads to a sturdier design.
ASME Section VIII, Division 2 requires more detailed calculations and allows vessels to handle higher stresses, making it suitable for vessels with specific purposes and fixed locations.
The key difference between Division 1 and Division 2 is in how they handle stress. Division 1 uses normal stress theory, while Division 2 uses maximum distortion energy theory (Von Mises). The major differences between the two divisions of ASME BPVC Sec VIII Div 1 and Div 2 are tabulated below:
Parameters | ASME Sec VIII-Division 1 | ASME Sec VIII-Division 2 |
Design Approach | ASME Sec VIII Division 1 is focused on a design-by-rule approach | ASME Sec VIII Division 2 on the other hand, is based on a design-by-analysis approach |
Design Factor | The design Factor used is 3.5 on tensile and other yields and temperature considerations. | Design Factor of 3 (3.0 for Division 2, Class 1 and 2.4 for Division 2, Class 2) on tensile and other yield and temperature considerations. |
Pressure Limit | Pressure typically up to 3000 psig. ASME Sec VIII Div 1 is more suitable for low-pressure applications. | Pressure is usually 600 psig and larger (less than 10000 psi). ASME Sec VIII Div. 2 caters to high-pressure applications. |
Design Rules | Membrane – Maximum stress Generally Elastic analysis. Very detailed design rules with Quality (joint efficiency) Factors. Little stress analysis required; pure membrane without consideration of discontinuities controlling stress concentration to a safety factor of 3.5 or higher | Maximum Shear stress theory is the basis for Shell of Revolution. Generally Elastic analysis Membrane + Bending. Fairly detailed design rules. In addition to the design rules, discontinuities, fatigue, and other stress analysis considerations may be required unless exempted and guidance provided for in Appendix 4, 5 and 6. |
Design Calculations | Simple Calculations. | requires more detailed calculations than Division 1 |
Failure Theory of Design | ASEM Sec VIII Division 1 is based on the normal stress theory | ASME Sec VIII Division 2 is based on maximum distortion energy (Von Mises criteria) |
Experimental Stress Analysis | Experimental methods of stress analysis are not required in normal cases. | Experimental stress analysis is introduced and may be required |
Material and Impact Testing | Few restrictions on materials; Impact required unless exempted; UG-20, UCS 66/67 provides extensive exemptions. | More restrictions on materials; impact required in general with similar rules as Division 1. |
NDE Requirements | In ASME Sec VIII Div. 1, the NDE requirements may be exempted through increased design factors. | Div. 2 has more stringent NDE requirements; extensive use of Radiographic tests, Ultrasonic Tests, Magnetic Particle Tests, and Penetration Tests. |
Welding and fabrication | Different types with butt welds and others. | Extensive use/requirement of butt welds and full penetration welds including non-pressure attachment welds. |
Fatigue Evaluation | Not mandatory. | AD 160 for fatigue evaluation |
Manufacturer | Manufacturers are to declare compliance with the data report. | Manufacturer’s Design Report certifying design specification and code compliance in addition to a data report. |
Professional Engineer Certification | Normally not required. | Professional Engineers’ Certification of User’s Design Specifications as well as Manufacturer’s Design Report Professional Engineers shall be experienced in pressure vessel design. |
Code Stamp and Marking | U Stamp with Addition markings including W, B, P, RES; L, DF, UB, HT, and RT. | U2 Stamp with Additional marking including HT. |
Hydrostatic Test Pressure | 1.3 times design pressure. | 1.25 times design pressure. |
Allowable Stress Value at a specified design temperature | Lower, hence higher design margin. | Higher, hence lower design margin. |
Shell thickness at the same design pressure | Thicker | Thinner. |
Material Cost | Higher. | Lower. |
Minimum Pressure Design Thickness Calculation Equation | t=PD/2S – 1.2P | t=D/2{Exp(P/S)-1} |
Hydrotest Stress Calculation | In ASME Sec VIII Division 1, hydro test stresses are not specifically limited, and partial penetration nozzle welds are permitted. | In the ASME Sec VIII Division 2, hydro test stress calculations are mandatory as they are limited, and full penetration nozzle welds are required |
No of Vessels produced Annually | Larger | Lower |
Reference Standards | ASME B 1.13M AND ASME B 1.21M related to Screw threads are not listed | Both standards are given as references. |
Good work!
Good job
Thank you very much and Good Job, its very easy to understand the difference.
I am a Rotating Equipment Engineer, who finds this page useful and concise on the subject topic. Thank you so much for sharing.
Very useful, concise comparison.
Anup – great job on the summary comparison. I work in an Oil & Gas major and my background is in rotating equipment engineering and now also Quality Management. This is a very useful summary of Div 1 vs Div 2.
Sam
great work. it is very useful.
Hi Anup Kumar Dey ,
really appreciate your valuable information , defiantly benefited from it
do you have any any smiler comparison Difference Between ASME Sec VIII Div. 2 and ASME V Div PD/5500
have good day
Good work, very appropriate to my work. Thanks
Nice and very informative comparison
CAN YOU PLEASE MAKE A COMPARISON TABLE BETWEEN ASME SECTION VIII DIV 1 AND EN 13458 – 2 FOR THE DESIGN OF CRYOGENIC PRESSURE VESSELS.
Good Job Anup.
Thank you for share it.
Hi,
thank you for your website.
I would like to comment that Division 2 comprises both Design by Rule and Design by Analysis requirements, not only DbA.
It is not fair to oppose both codes based on DbR vs DbA 😉
Part 4 Design by Rule Requirements (approximately 400 pages out of 870)
Part 5 Design by Analysis Requirements (approximately 30 pages out of 870)