What is Nitriding?
Nitriding is a type of heat treatment process to create a case-hardened surface by diffusing Nitrogen. The most common applications of the nitriding process are valve parts, gears, forging dies, crankshafts, extrusion dies, camshafts, firearm components, bearings, textile machinery, aircraft components, turbine generation systems, plastic mold tools, etc. The material widely used for the nitriding treatment process are low-alloy steels, aluminum, molybdenum, and titanium. Depending on the case depth, the nitriding process can take 4 to 60 hours.
Developed early in 1900, the nitriding process is widely used in many industrial applications. During nitriding, no phase change occurs. It is one of the simplest case-hardening processes.
What are the Purposes of Nitriding?
The main purposes of nitriding treatment are:
- To get high hardness on the surface. Hardness achieved in nitriding is usually higher than carburizing method.
- To increase the wear resistance.
- To improve fatigue life and other fatigue-related properties.
- To improve the corrosion resistance of the material.
- To obtain a high-temperature property of the surface (Resistance to tempering or softening up to the nitriding temperature).
- To get anti-galling properties.
Also, the nitriding process helps in reducing notch sensitivity. It is a diffusion-related surface treatment process that causes very small volumetric changes. Nitriding treatment can significantly improve properties like fatigue strength, resistance to wear, corrosion resistance, friction, and hardness.
What is the Principle of Nitriding?
Nitriding is a thermochemical treatment process to enrich the surface with nitrogen for the purpose of increasing the surface’s hardness. The process is based on the low solubility of nitrogen in the ferritic crystal structure to promote the precipitation of iron nitrides or alloy nitrides. The connecting nitriding is connected to a diffusion zone where precipitated nitrides are evenly diffused in the steel matrix. The usual nitriding temperature range is 350°C to 590°C. With a decrease in temperature, the nitriding time to reach a given depth increases. The depth of nitriding hardness may reach 500 μm with maximum hardness levels of > 1000 HV.
The nitriding layer formation occurs in the following steps:
- adsorption of nitrogen atoms on the surface of the component,
- absorption of nitrogen atoms by the component surface, and
- diffusion of the nitrogen atoms along the grain boundaries and within the grains.
What are the Types of Nitriding?
There are three types of nitriding processes that are commonly used in industries. They are:
- Gas Nitriding,
- Plasma Nitriding, and
- Salt-bath Nitriding.
What is Gas Nitriding?
In the gas nitriding process, the metal is heated to a suitable temperature (5000C to 5750C for Steel) and held in contact with a nitrogenous gas, usually ammonia. This is why the process is sometimes known as ammonia nitriding. When ammonia comes into contact with the heated steel, it breaks down into hydrogen and nitrogen. This nitrogen then diffuses onto the metal surface and creates a nitride layer. Depending on the temperature the solubility of nitrogen into iron varies as can be seen from the attached iron-nitrogen equilibrium diagram in Fig. 1.
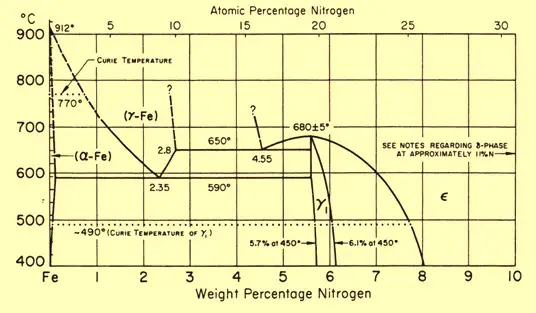
The effectiveness of the gas nitriding process depends on various factors like
- Gas Flow
- Temperature
- Time
- Gas activity control
- Process control
- Process chamber maintenance, etc
What are the Advantages and Disadvantages of Gas Nitriding?
The main advantages of gas nitriding over other types of nitriding treatment are:
- Possibility of larger batch sizes (limited by the furnace size and gas flow)
- An all-around nitriding effect is achieved.
- Relatively low equipment cost as compared with plasma nitriding.
The disadvantages of gas nitriding are:
- Ammonia as a nitriding medium can be harmful if inhaled in large quantities. Also, it has the risk of explosion when heating in the presence of oxygen; so must be controlled carefully.
- Reaction kinetics are heavily influenced by surface conditions. Poor contaminated surface delivers poor results.
What is Plasma Nitriding?
Also popular as ion nitriding or glow-discharge nitriding, plasma nitriding uses a plasma discharge of reaction gases to heat the metal surface and supply nitrogen for the nitriding process. The main advantage of plasma nitriding is that the process is not dependent on the decomposition of ammonia gas to release nascent nitrogen. Invented by Dr. Bernhardt Berghaus of Germany, Plasma nitriding has a shorter cycle time. Fig. 2 below shows a typical schematic diagram of the plasma nitriding furnace layout.
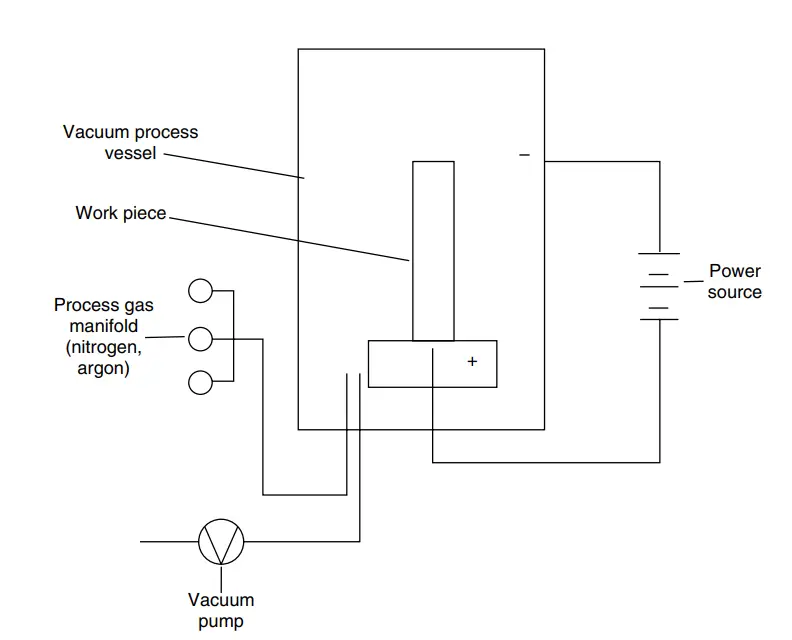
In plasma nitriding, intense high-voltage electric fields in a vacuum are used to generate ionized nitrogen gas molecules. This highly active gas with ionized molecules, known as plasma accelerates to impinge on the work surface. This ion bombardment cleans the surface, heats the workpiece, and provides active nitrogen ions. Plasma nitriding helps in close control of the nitriding microstructure and its efficiency is not dependent on the temperature.
Metallurgically versatile, the ion nitriding process provides excellent retention of surface finish and ensures repetitive metallurgical properties. Ion nitriding can be conducted at temperatures lower than those conventionally employed. The plasma nitriding process does not cause any pollution and insignificant gas consumption which are important economic and public policy factors.
What are the Advantages and Disadvantages of the Ion Nitriding Process?
The main advantages of plasma nitriding are:
- Close control of Nitrided microstructure.
- The working lifespan of the component also increases.
- No polishing or machining is required post-nitriding process.
- Causes very little or no distortion.
- Energy-efficient and the fastest process.
The disadvantages of the plasma nitriding process are:
- Limited only on the compound zone thickness.
- Poor temperature control.
What is Salt Bath Nitriding?
Salt bath nitriding used molten salt as the source of nitrogen. The nitriding process uses the nitrogen liberated from the decomposition of cyanide to cyanate. The process also releases carbon and thus the process is also known as a nitrocarburizing treatment. The metal is normally submerged in a bath of preheated molten cyanide salt. The high concentration of nitrogen in the liquid chemically combines with iron to produce a hard and ductile iron nitride (Fe3N) thin outer layer.
What are the Advantages and Disadvantages of Salt-bath Nitriding?
The advantages of salt nitriding are:
- Quick processing time and higher diffusion in the same period.
- A simple operation involving the heating of the salt and workpieces to a temperature of 550 to 5700C and submerging for the specified duration.
The disadvantages of the salt bath nitriding process are:
- Used cyanide salts are highly toxic.
- Only one process is possible with a particular salt type.
What are the Prerequisites for Nitriding?
To get the best results in nitriding the following prerequisites should be followed:
- The steel should be hardened, quenched, and tempered to get a uniform structure.
- The surface must be cleaned to remove oils, grits, etc using vapor degreasing or abrasive cleaning.
Advantages of the Nitriding Process
The nitriding process provides various advantages like:
- Quick processing time.
- Low-temperature process.
- Clean pollution-free operation.
- Economic and energy-efficient operation.
- Lower friction coefficient.
- Improved fatigue properties.
- Uniform surface.
- High surface hardness.
- Distortion is very less.
- Improved corrosion resistance.
- Quenching is not required for getting high hardness.
Disadvantages of the Nitriding Process
The drawbacks of the nitriding process are
- High initial cost.
- Closer process control is required.
- Skilled personnel requirement.
Nitriding vs Carburizing: What is the difference between nitriding and carburizing?
The main differences between Nitriding and Carburizing are:
Nitriding | Carburizing |
In nitriding, the nitrogen is diffused to increase the surface hardness | On the other hand, Carbon is diffused in Carburizing process. |
The temperature range for nitriding treatment is lower. | Carburizing is done at very high-temperature ranges. |
Energy-efficient and quick process. | Higher energy requirement. |
information about the nitriding is good and this is a good blog . thank you for sharing useful information. Brainstorm Infotech is headquartered in Bengaluru, the start-up capital of India. It has carved a niche for itself in the field of structural steel detailing and allied services with a credit of completing over 1250 projects so far. We started small with a team of five professionals in 2010 but have earned the trust and respect of our clients that has led to long-standing associations.