Tensile strength is the maximum stress up to which a material can be loaded without failure. When the tensile strength is exceeded, the material breaks or fails. This is also known as ultimate tensile strength or UTS in abbreviated form. The Tensile Strength of a material is a very important parameter in mechanical design as all components are designed in such a way that the generated stress in that part does not exceed tensile strength during the design life of the component. In this article, we will discuss more regarding Tensile Strength, its definition, its significance, measuring methods, and typical values.
Definition of Tensile Strength
Mathematically, the tensile strength of a material is defined as the ratio of the maximum load that the material can support to its original cross-sectional area. So, UTS=Maximum force to create failure of the body/Cross-Sectional Area=F/A.
From the above equation, it is evident that the unit of Tensile strength is N/m2 or Pa (pascal) in SI systems. In the FPS system, the unit of tensile strength is psi or lb/in2. Usually, the tensile strength of materials is expressed in MPa or psi.
In the stress-strain curve of a material, it is the maximum stress value before failure as shown in Fig. 1 (Image Credit: https://mechanicalc.com/reference/mechanical-properties-of-materials) below.
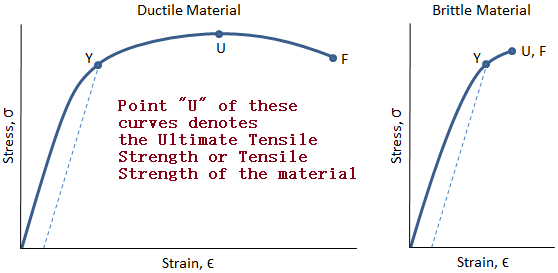
Significance of Tensile Strength
Tensile strength is the maximum stress generated before fracture. So, it can be stated as for a given cross-section, the maximum load that the material can be subjected to can be easily calculated. This maximum load or stress value is very important. Tensile Strength data is required for various purposes as mentioned below:
- Structural and Mechanical Design
- Material Evaluation
- Preparing Material Specification
- Quality Control
- Failure Analysis
- Modeling to predict material behavior under complex loading conditions.
The tensile strength is the material’s resistance to tension. The more the tensile strength of a part, the more difficult it is to stretch, and more force is required to stretch it.
Factors Affecting Tensile Strength
Tensile Strength is an intensive property of a material and independent of the size of the specimen. The value of tensile strength varies from one material to the other. The factors that affect the tensile strength in metals are:
- Temperature: With an increase in the temperature of a material the tensile strength decreases.
- Surface Defects: Specimens with defects have less tensile strength as compared to materials without defects.
- Specimen Preparation: Tensile strength of a material depends on the surface preparation of the materials. This is the reason that a standard philosophy as outlined in Codes and Standards is followed for specimen preparation.
- Heat Treatment: Heat treatment can modify the tensile strength of metals.
- Amount of Cold Work on the material
Measuring Tensile Strength
Tensile strength measures a material’s resistance to breaking. The tensile test for metals is measured by performing tensile testing in a universal testing machine. Various ASTM codes provide guidelines for the tensile testing procedure. For example, ASTM E8 provides standard test methods for metallic materials and ASTM D638 provides tensile testing procedures for plastic materials.
A universal testing machine has two crossheads where the specimen is fitted and an increasing tensile load is applied to extend the specimen till it breaks. the elongation against the applied force is plotted automatically by the instrument from which the stress-strain curve is generated. The tensile strength is decided from that curve (Refer to Fig. 1) as the maximum stress point in the curve during failure.
Common codes and standards that are followed for tensile testing are ASTM E8/E8M, ISO 6891, JIS Z2241, ASTM D3039, ASTM D638, ASTM D828, ASTM D882, ISO 37, MPIF Test Standard 10, etc.
The tensile strength of a material can be measured by the above-mentioned process. But Scientists in research organizations have already standardized tensile strength values for all common materials in various codes and standards like ASME BPVC codes, ASME B codes, etc. So, Engineers need to simply follow the relevant code and standard and find out the tensile strength of the material from standardized tables provided in those codes.
Tensile Strength vs Yield Strength
Yield Strength is the property of ductile materials. For brittle materials, distinct yield strength is not obtained. Hence, proof stress is determined by drawing a parallel line to the straight elastic region of the stress-strain curve starting from 0.2% of strain. The main differences between Tensile Strength and Yield Strength are tabulated below:
Tensile Strength | Yield Strength |
Tensile strength is measured at the point of fracture. | Yield Strength is measured at the point of plastic deformation. |
Tensile strength is a design parameter for brittle materials. | Yield strength is the design parameter for ductile materials. |
The value of tensile strength is always higher than yield strength. | The value of Yield Strength is lower than tensile strength. |
After tensile strength, the material fails. | After Yield Strength, the material loses its elastic behavior. |
Tensile Strength of Steel
The tensile strength of steel provides the value of tensile stress that a steel component can withstand until it leads to failure in any of two ways: ductile or brittle failure. Click here to know more about ductile and brittle failure.
The tensile strength of common steels for industrial use is provided in the following table (Table 2):
Steel Material | Tensile Strength (MPa) | Yield Strength (MPa) | Tensile Strength (ksi) | Yield Strength (ksi) |
Structural Steel, ASTM A36 | 400-550 | 250 | 58-80 | 36 |
Mild Steel, 1090 | 841 | 247 | 122 | 36 |
Maraging Steel, 2800 | 2693 | 2617 | 391 | 380 |
Chromium Vanadium Steel | 940 | 620 | 136 | 90 |
API 5L X65 | 531 | 448 | 77 | 65 |
ASTM A514 | 760 | 690 | 110 | 100 |
Chromium-Nickel Austenitic Stainless Steel | 520-720 | 210 | 75-104 | 30 |
Molybdenum Chromium Nickel Austenitic Stainless Steel | 520-670 | 220 | 75-97 | 32 |
Duplex Steels | 640-850 | 460 | 93-123 | 67 |
Stainless Steel AISI 302 | 860 | 502 | 125 | 73 |
Ferritic Stainless Steel | 500 | 280 | 73 | 41 |
Martensitic Stainless Steel | 650 | 350 | 94 | 51 |
Precipitation Hardening Stainless Steel | 1100 | 1000 | 160 | 145 |
Ordinary Carbon Steel | 315-610 | 195-275 | 46-88 | 28-40 |
Tool Steel-Annealed | 280-700 | 180-360 | 41-102 | 26-52 |
Tool Steel-Normalised | 530-760 | 380-430 | 77-110 | 55-62 |
Tool Steel-Cold Hardened | 750-1200 | – | 109-174 | – |
Alloy Structural Steel | 500-750 | – | 73-109 | – |
API 5L X42 | 414 | 290 | 60 | 42 |
API 5L X52 | 455 | 359 | 66 | 52 |
API 5L X60 | 517 | 414 | 75 | 60 |
A106 B | 414 | 241 | 60 | 35 |
API 5L B | 414 | 241 | 60 | 35 |
A333-6 | 414 | 241 | 60 | 35 |
A516-70 | 483 | 262 | 70 | 38 |
Tensile Strength of Other Materials
The following table (Table 3) provides the tensile strength of some common materials.
Material | Tensile Strength (MPa) | Yield Strength (MPa) |
Diamond | 2800 | 1600 |
Bamboo | 265 | 142 |
Brass | 250 | |
Cast Iron, ASTM A48 | 200 | 130 |
Copper | 220 | 70 |
HDPE | 37 | 26-33 |
Marble | 15 | |
Rubber | 15 | |
Tungsten | 1510 | |
Aluminum | 40-50 | 15-20 |
Gold | 100 | |
Iron | 350 | 80-100 |
Lead | 12 | |
Nickel | 140-195 | 14-35 |
Silver | 170 | |
ABS plastics | 40 | |
A53 Seamless and Welded Standard Steel Pipe – Grade A | 331 | 207 |
A53 Seamless and Welded Standard Steel Pipe – Grade B | 414 | 241 |
A106 Seamless Carbon Steel Pipe – Grade A | 400 | 248 |
A106 Seamless Carbon Steel Pipe – Grade C | 483 | 276 |
A252 Piling Steel Pipe – Grade 1 | 345 | 207 |
A252 Piling Steel Pipe – Grade 2 | 414 | 241 |
A252 Piling Steel Pipe – Grade 3 | 455 | 310 |
A501 Hot Formed Carbon Steel Structural Tubing – Grade A | 400 | 248 |
A501 Hot Formed Carbon Steel Structural Tubing – Grade B | 483 | 345 |
A523 Cable Circuit Steel Piping – Grade A | 331 | 207 |
A523 Cable Circuit Steel Piping – Grade B | 414 | 241 |
A618 Hot-Formed High-Strength Low-Alloy Structural Tubing – Grade Ia & Ib | 483 | 345 |
A618 Hot-Formed High-Strength Low-Alloy Structural Tubing – Grade II | 414 | 345 |
A618 Hot-Formed High-Strength Low-Alloy Structural Tubing – Grade III | 448 | 345 |
API 5L Line Pipe | 310 – 1145 | 175 – 1048 |
Acetals | 65 | |
Acrylic | 70 | |
Aluminum | 110 | 95 |
Boron | 3100 | |
Brass | 250 | |
Cast Iron 4.5% C, ASTM A-48 | 170 | |
Cellulose, cotton, wood pulp, and regenerated | 80 – 240 | |
Cellulose acetate, sheet | 30 – 52 | |
Cellulose nitrate, celluloid | 50 | |
Chlorinated polyether | 39 | |
Concrete, High Strength (compression) | 40 | |
Copper | 220 | 70 |
Douglas fir Wood | 50 | |
Epoxy resins | 26 – 85 | |
Marble | 15 | |
Nylon-6 | 45 – 90 | 45 |
Nylon-66 | 60 – 80 | |
Phenolic cast resins | 33 – 59 | |
Phenol-formaldehyde molding compounds | 45 – 52 | |
Pine Wood (along the grain) | 40 | |
Polyacrylonitrile, fibers | 200 | |
Polycarbonates | 52 – 62 | |
Polyethylene HDPE (high density) | 15 | |
Polyethylene Terephthalate, PET | 55 | |
Polyamide | 85 | |
Polyisoprene, hard rubber | 39 | |
Polyimide aromatics | 68 | |
Polypropylene, PP | 28 – 36 | |
Polystyrene, PS | 30 – 100 | |
Polyurethane cast liquid | Oct-20 | |
Polyurethane elastomer | 29 – 55 | |
Silicon Carbide | 3440 | |
Steel, High Strength Alloy ASTM A-514 | 760 | 690 |
Steel, stainless AISI 302 | 860 | 502 |
Steel, Structural ASTM-A36 | 400 | 250 |
Titanium Alloy | 900 | 730 |
Can you please elaborate
1. whether and when we should use tensile or yield strength for calculating thickness of vessel or pipe.
2. Since there is a range of values of tensile strength shall we use lower value to calculate thickness
3. From where we can get variation in value of tensile and yield strength with temperature.
Thanks
What is the tinsel strength of api5l 36” X70 625 wall ERW pipe.
When pulling a bore what is the maximum amount of pounds you can put on it
When you pull back the bore pipe