Flange gaskets may not be the most glamorous components in the industrial piping world, but they play a critical role in maintaining the integrity and efficiency of flanged connections. Whether you’re familiar with them or just starting to explore their importance, this comprehensive guide will take you through the ins and outs of piping flange gaskets, their types, applications, and best practices.
What is a Flange Gasket?
A flange gasket is one of the basic elements for flanged joints in the piping system of operating plants. A flange gasket is defined as a sealing material or a combination of materials clamped between two separable mechanical members of a mechanical joint (flanged joint) which produces the weakest link of the joint. The leak-proof sealing is ensured by different types of gaskets. In oil and gas, chemical, petrochemical, and other heavy industries, many different types of gaskets are widely used. Flange gaskets come in a variety of shapes, sizes, and materials to accommodate different pressures, temperatures, and media.
A flange gasket is a soft sealing material closed between two flanges in order to make a leak-free sealing application. For proper functioning and cost-effectiveness of flanged joints:-
- Flanges must be enormous stiff and massive.
- Flange faces should be super smooth.
- Flanges should be closed without tension on the pipes
- Flanges should be 100% parallel.
But the above is economically not feasible.
Functions of a Flange Gasket in a Piping Flanged Joint
Flange Gaskets in piping are used to create a static seal between two stationary members of a mechanical assembly (the flanged joint) that maintains a leak-proof sealing during operation. The gasket material flows (interpose a semi-plastic material between the flange facings) into the imperfections between the mating surfaces by an external force (bolt tightening force) and maintains a tight seal (seals the minute surface irregularities to prevent leakage of the fluid) under all operating conditions.
The amount of flow (seal) of the gasket material that is required to produce a tight seal is dependent upon the roughness of the surface. The gasket must be able to maintain this seal under all the operating conditions of the system including extreme upsets of temperature and pressure. Therefore, it is important to ensure proper design and selection of the gaskets to prevent flange-leakage problems and avoid costly shutdowns of the process plants.
So the main functions of a flange gasket are:
- The gasket material has to fill the uneven surface of the flange in order to prevent leakage between the gasket and the flange surface.
- The gasket material has to overcome the misalignment of the flanges in order to prevent leakage between the gasket and the flange surface.
- Leakage through the gasket has to be reduced to the minimum against internal pressure-Emission
How does a Flange Gasket Work?
Refer to the above figure (Fig. 1) which shows the three major forces acting on the gasket. Normally the gasket is seated by tightening the bolts on the flanges before the application of the internal pressure. Upon the application of the internal pressure in the joint, an end force (Hydrostatic end force) tends to separate the flanges and decrease the unit stress (Residual stress) on the gasket. Leakage will occur under pressure if the hydrostatic end force is sufficiently great and the difference between the hydrostatic end force and the bolt load reduces the gasket load below a critical value. To explain it in clear language, we can say that there are three principal forces acting on any gasket joint. They are:
- Bolt Load which applies the initial compressive load that flows the gasket material into surface imperfections to form a seal.
- The hydrostatic end force tends to separate flanges when the system is pressurized.
- Internal pressure acting on the portion of the gasket exposed to internal pressure tends to blow the gasket out of the joint and/or bypass the gasket under operating conditions.
Even though there are other shock forces that may be created due to sudden changes in temperature and pressure. Creep relaxation is another factor that may come into the picture. The initial compression force applied to a joint must serve several purposes as listed below:
- It must be sufficient to initially seat the gasket and flow the gasket into the imperfections on the gasket seating surfaces regardless of operating conditions.
- The initial compression force must be great enough to compensate for the total hydrostatic end force that would be present during operating conditions.
- It must be sufficient to maintain a residual load on the gasket/flange interface.
Now from a practical standpoint, residual load on the gasket must be “X” times internal pressure if a tight joint is required to be maintained. This unknown quantity “X” is what is specified as the “m” factor in the ASME Pressure Vessel Code and will vary depending upon the type of gasket being used. Actually, the “m” value is the ratio of residual unit stress (bolt load minus hydrostatic end force) on the gasket to the internal pressure of the system. The larger the value of “m”, the more assurance the designer has of obtaining a tight joint.
Types of Flange Gaskets
Depending on various parameters, gaskets for pipe flanges are classified as follows:
- Gasket types based on gasket materials
- Types of gaskets depending on gasket configurations
- Gasket types based on the face of gaskets
- Miscellaneous types of gaskets
Types of flange gaskets based on gasket materials
Based on the gasket materials used to manufacture the gasket, three types of gaskets are widely used in industrial applications. They are
- Non-metallic Gaskets
- Semi-metallic or Composite Gaskets, and
- Metallic Gaskets
Non-metallic Gaskets
Usually, composite sheet materials are used with flat-face flanges and low-pressure class applications. Non-metallic gaskets are manufactured of non-asbestos material or Compressed Asbestos Fibre (CAF). Non-asbestos types include aramid fiber, glass fiber, elastomer, Teflon (PTFE), and flexible graphite gaskets. Full-face gasket types are suitable for use with flat-face (FF) flanges and flat-ring gasket types are suitable for use with raised-face (RF) flanges.
There are various types of rubber gaskets. Rubber gaskets are used to seal two surfaces together and prevent leakage of fluids or gases. There are several types of rubber gaskets available in the market, each with its own unique properties and characteristics. Some of the common types of rubber gaskets are:
- Neoprene Gaskets: These gaskets are made from neoprene rubber, which is resistant to oil, weather, and abrasion. They are commonly used in automotive and industrial applications.
- Silicone Gaskets: Silicone gaskets are made from silicone rubber, which is resistant to extreme temperatures and chemicals. They are commonly used in high-temperature applications such as oven doors and engine components.
- EPDM Gaskets: These gaskets are made from ethylene propylene diene monomer rubber, which is resistant to weather, ozone, and UV radiation. They are commonly used in outdoor applications such as roofing and window seals.
- Nitrile Gaskets: Nitrile gaskets are made from nitrile rubber, which is resistant to oil, fuel, and other chemicals. They are commonly used in automotive and oil industry applications.
- Viton Gaskets: Viton gaskets are made from fluoroelastomer rubber, which is resistant to high temperatures, chemicals, and fuels. They are commonly used in aerospace, chemical processing, and automotive applications.
- Natural Rubber Gaskets: These gaskets are made from natural rubber, which is resistant to abrasion and tear. They are commonly used in applications where flexibility and toughness are required.
The choice of rubber gasket will depend on the specific requirements of the application, such as the type of fluid or gas being sealed, the temperature and pressure of the system, and the environmental conditions.
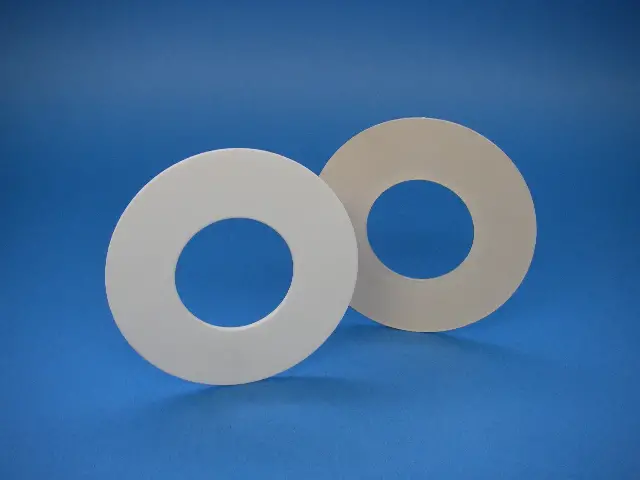
Semi-metallic or Composite Flange Gaskets
Semi-metallic gaskets are composites of metal and non-metallic materials. The metal is intended to offer strength and resiliency while the non-metallic portion of a gasket provides conformability and sealability. Commonly used semi-metallic gaskets are spiral wound, metal jacketed, Cam profile, and a variety of metal-reinforced graphite gaskets. Semi-metallic gaskets are designed for the widest range of operating conditions of temperature and pressure. Semi-metallic gaskets are used on raised faces, male and female, and tongue and groove flanges.
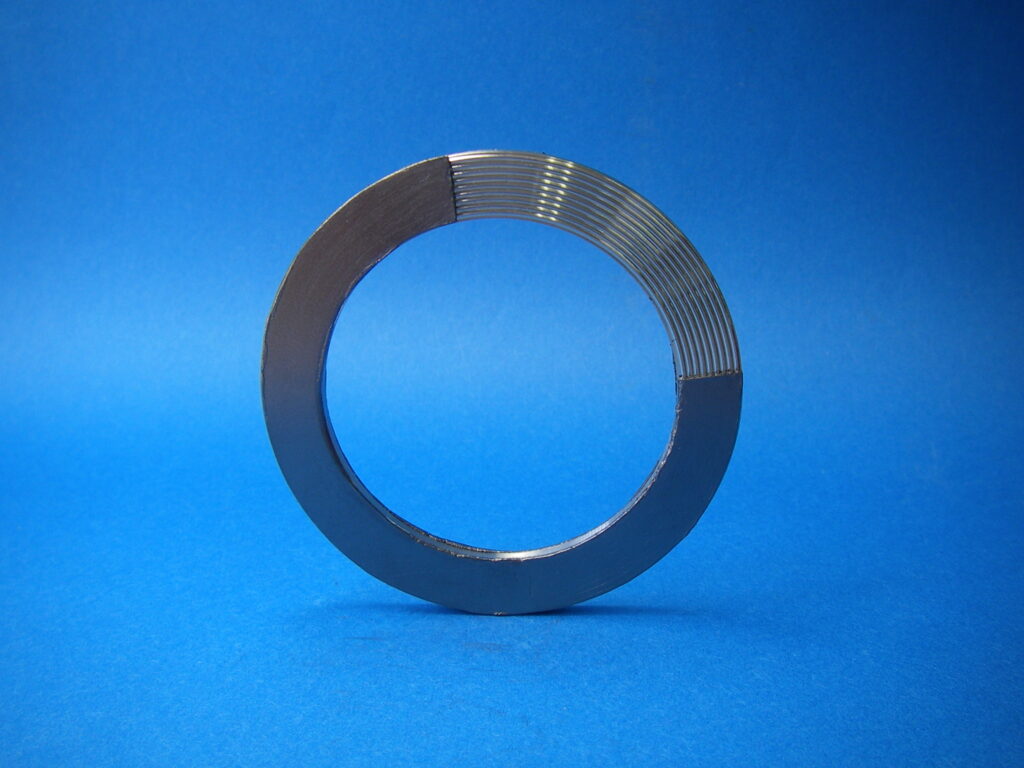
Metallic Gaskets
Metallic gaskets are fabricated from one or a combination of metals to the desired shape and size. Common metallic gaskets are ring-joint gaskets and lens rings. They are suitable for high-pressure and temperature applications and require a high bolt load to seal.
Flange Gasket types based on gasket configurations
Aside from the choice of gasket material, the structure or configuration of the gasket is also significant. The following paragraphs explain four major types of gaskets.
Graphite foil Gasket
The physical and chemical properties of graphite foil make it suitable as a sealing material for relatively arduous operating conditions. In an oxidizing environment, graphite foil can be used in the temperature range of –200 to +500°C, and in a reducing atmosphere, it can be used at temperatures between –200 and 2,000°C. Because graphite foil has no binder materials, it has excellent chemical resistance and is not affected by most of the commercially used common chemicals. It also has very good stress-relaxation properties.
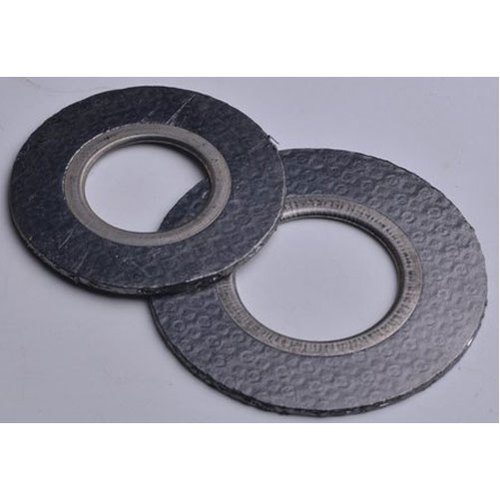
Spiral-wound Gasket
As the name implies, the spiral-wound gasket is made by winding a preformed metal strip and a filler on the periphery of a metal winding mandrel. All spiral-wound gaskets are furnished with a centering ring. In addition to controlling compression, these rings serve to locate the gasket centrally within the bolt circle. Inner rings are used where the material (such as a gasket with PTFE filler) has a tendency for inward buckling. The ring also prevents the buildup of solids between the inside diameter of the gasket and the bore of the pipe. Under vacuum conditions, the ring protects against damage that would occur if pieces of a broken component were drawn into the system. Spiral-wound gaskets can operate at temperatures from –250 to 1,000°C, and pressures from vacuum to 350 bar. Spiral-wound gaskets up to 1-in. diameter and up to class number 600 require uniform bolt stress of 25,000 psi to compress the gasket. Larger sizes and classes require 30,000 psi to compress the gasket.
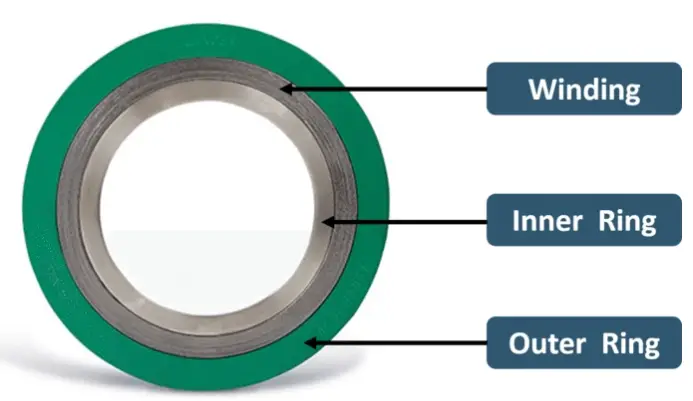
There are several types of spiral wound gaskets available in the market, each with its own unique properties and characteristics. Some of the common types of spiral wound gaskets are:
- Basic Spiral Wound Gaskets: These gaskets are the simplest type of spiral wound gaskets and are composed of a single metal strip and a soft filler material. They are commonly used in low-pressure and low-temperature applications.
- Inner Ring Spiral Wound Gaskets: These gaskets have an additional metal ring on the inside of the spiral wound structure, which provides extra support and stability. They are commonly used in high-pressure and high-temperature applications.
- Outer Ring Spiral Wound Gaskets: These gaskets have an additional metal ring on the outside of the spiral wound structure, which provides extra support and prevents the soft filler material from flowing out of the gasket. They are commonly used in applications where the gasket is subjected to high pressure.
- Centering Ring Spiral Wound Gaskets: These gaskets have an additional metal ring in the center of the spiral wound structure, which helps to center the gasket in the flange and prevents it from slipping out of position. They are commonly used in applications where alignment is critical.
- Jacketed Spiral Wound Gaskets: These gaskets have an outer metal jacket that provides additional protection against corrosive or abrasive media. They are commonly used in chemical processing and petrochemical applications.
Ring-Joint Gasket
Ring-joint gaskets are commonly used in grooved flanges for high-pressure-piping systems and vessels. Their applicable pressure range is from 1,000 to 15,000 psi. These gaskets are designed to give very high gasket pressure with a moderate bolt load. These joints are not generally pressure-actuated. The hardness must be less than that of the flange material so that the proper flow of material occurs without damaging flange surfaces. The most widely used ring-joint gaskets are of the oval and octagonal types. Oval types of gaskets contact the flange face at the curved surface and provide a highly reliable seal. However, the curved shape makes it more difficult to achieve accurate dimensioning and surface finishing. Oval gaskets also have the disadvantage that they can only be used once, so they may not be the best choice for sealing flanges that have to be opened routinely. On the other hand, because they are constructed of only straight faces, octagonal-type gaskets are usually less expensive, can be dimensioned more accurately, and are easier to surface finish than oval-type flange gaskets. However, a greater torque load is required to flow the gasket material into imperfections that may reside on the flange faces. Octagonal gaskets can be used more than once.
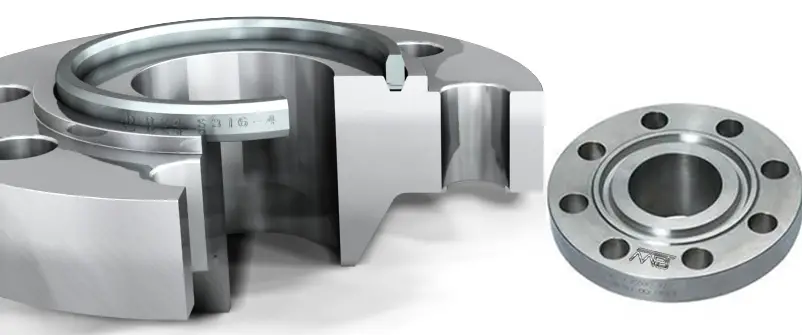
There are several types of ring joint gaskets available in the market, each with its own unique properties and characteristics. Some of the common types of ring joint gaskets are:
- R Style Ring Joint Gaskets: These gaskets are oval or octagonal in shape and are designed to be used with R-style flanges. They are commonly used in high-pressure applications in the oil and gas industry.
- BX Style Ring Joint Gaskets: These gaskets are trapezoidal in shape and are designed to be used with BX style flanges. They are commonly used in high-pressure applications in the oil and gas industry.
- RX Style Ring Joint Gaskets: These gaskets are similar to R style gaskets but have a modified design that allows them to be used with RX style flanges. They are commonly used in high-pressure applications in the oil and gas industry.
- IX Style Ring Joint Gaskets: These gaskets are designed to be used with IX style flanges, which are used in subsea and offshore applications. They have a unique design that allows them to seal effectively in high-pressure and high-temperature environments.
- SRX Style Ring Joint Gaskets: These gaskets are similar to RX style gaskets but have a modified design that provides a tighter seal. They are commonly used in critical applications where leakage cannot be tolerated.
Corrugated-metal Gaskets
This type of flange gasket is available in a wide range of metals, including brass, copper, copper-nickel alloys, steel, Monel, and aluminum. Corrugated metal gaskets can be manufactured to just about any shape and size required. The thickness of the metal is normally 0.25 or 0.3 mm, with corrugations having a pitch of 1.6, 3.2, and 6.4 mm. The sealing mechanism is based on point contact between the peaks of the corrugations and the mating flanges
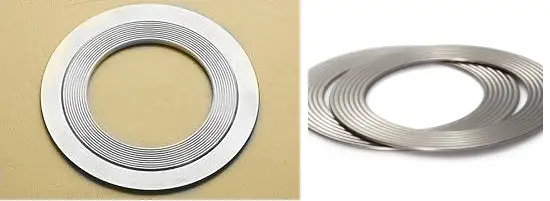
Gasket types based on the Face of gaskets
Depending on the face of the gaskets, two types of gaskets are found. These two types of gaskets most commonly known are ring gaskets and full-face gaskets. The latter as the name implies covers the entire flange face and is pierced by the bolt holes. They are intended for use with flat-face flanges. Ring gaskets extend to the inside of the flange bolt holes and consequently are self-centering. They are usually used with raised face or lap joint flanges but may also be used with flat-faced flanges.
Miscellaneous Gasket Types
Flat Ring Gaskets
Flat-ring types of gaskets are widely used wherever service condition permits because of the ease with which they may be cut from a flat sheet and installed. They are commonly fabricated from such materials as rubber, paper, cloth, asbestos, plastics, copper, lead, aluminum, nickel, Monel, and soft iron. These gasket types are usually made in thickness from 1/64 to 1/8 in. Paper, cloth, and rubber gaskets are not recommended for use above 120° C. Asbestos-composition gaskets may be used up to 350° C or slightly higher, ferrous, and nickel-alloy metal gaskets may be used up to the maximum temperature rating of the flanges.
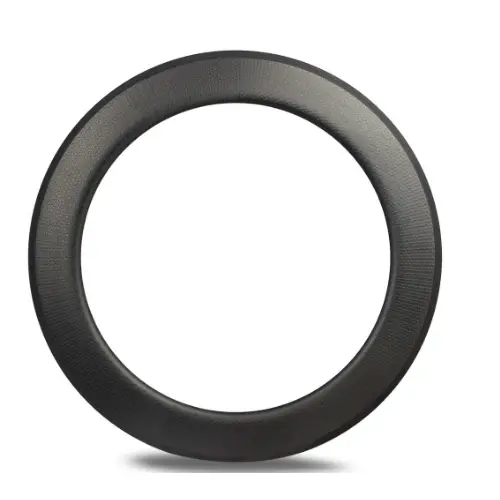
Axial and Radial Gasket Flow under Compression
Upon initial compression, a gasket will flow both axially and radially. The axial flow is required to fill depressions in the flange facing and prevent leakage. Radial flow serves no useful purpose unless the gasket is confined. Where a flange joint is heated, a greater gasket pressure is produced due to the difference between the flange body and the bolts. This greater pressure coupled with the usual softening of the gasket material at elevated temperatures causes additional axial and radial gasket flow. To compensate for this, the flange bolts are usually re-tightened a second or third time after the joint is heated to the normal operating temperature.
Thin Gasket vs. Thick Gasket
A thick gasket will flow radially to a far greater extent than a thin gasket. Some thin gaskets show practically no radial flow at extremely high unit pressures. Consequently, for high temperatures, a thin gasket has the advantage of maintaining a permanent thickness while a thick gasket will continue to flow radially and may leak, in time, due to the resulting reduced gasket pressure. However in attempting the utmost utilization of the thin gasket advantage, one may find that the gasket selected has an insufficient thickness to seal the irregularities, in the commercial flange faces.
Spiral-Wound Asbestos-Metallic Gasket
The spiral wound asbestos-metallic gasket combines the advantages of both the thick and thin gasket. Although a relatively thick gasket (most common types are 0.175” thick) its spirally laminated construction confines the asbestos filler between axially flexible metal layers. This eliminates the radial flow characteristics of a thick gasket and provides the resiliency to adjust to varying service conditions. Spiral wound gaskets are available with different filler materials such as Teflon, Grafoil, etc. to suit fluid compatibility. Spiral wound gaskets used with raised face flanges usually have an inner metal ring and an outer centering ring.
Laminated gaskets
Laminated gaskets are fabricated with a metal jacket and a soft filler, usually asbestos. Such gasket types can be used up to temperatures of about 400° C to 450° C and require less bolt load to seat and keep tight than solid metal flat ring gaskets.
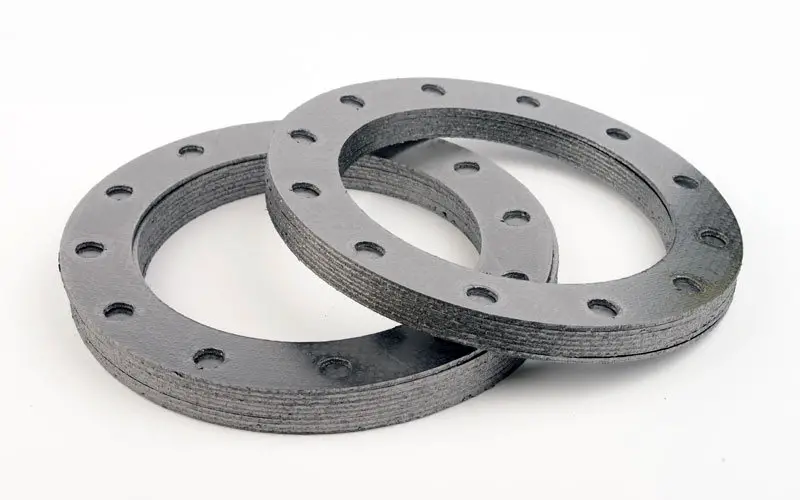
Serrated Metal gaskets
Serrated metal gaskets are fabricated of solid metal and have concentric grooves machined into the faces. This greatly reduces the contact area on initial tightening thereby reducing the bolt load. As the gasket is deformed, the contact surface area increases. Serrated types of gaskets are useful where soft gaskets or laminated gaskets are unsatisfactory and the bolt load is excessive with a flat-ring metal gasket. Smooth-finished flange faces should be used with serrated gaskets.
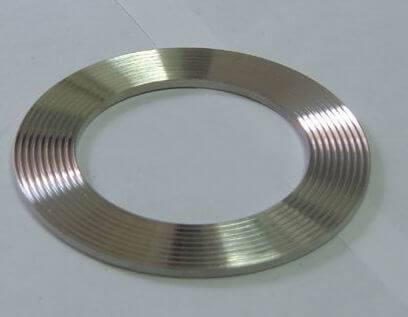
Corrugated Gaskets with Asbestos filling
Corrugated gaskets with asbestos filling are similar to laminated gaskets except that the surface is rigid with concentric rings as in the case of serrated gaskets. Corrugated gaskets require less seating force than laminated or serrated gaskets and are extensively used in low-pressure liquid and gas services. Corrugated metal gaskets without asbestos may be used to a higher temperature than those with asbestos filling.
Ring-Joint Gaskets
Two standard types of ring-joint gaskets are available for high-pressure service. One type has an oval cross-section, and the other has an octagonal cross-section. These rings are fabricated of solid metal, usually soft iron, soft steel, Monel, 4-6% chrome, and stainless steel. The alloy-steel rings should be heat treated to soften them.
It is recommended that the ring joint gasket be used for class 150 flanged joints. When the ring joint or spiral wound gasket is selected, it is recommended that line flanges be of the welding neck type.
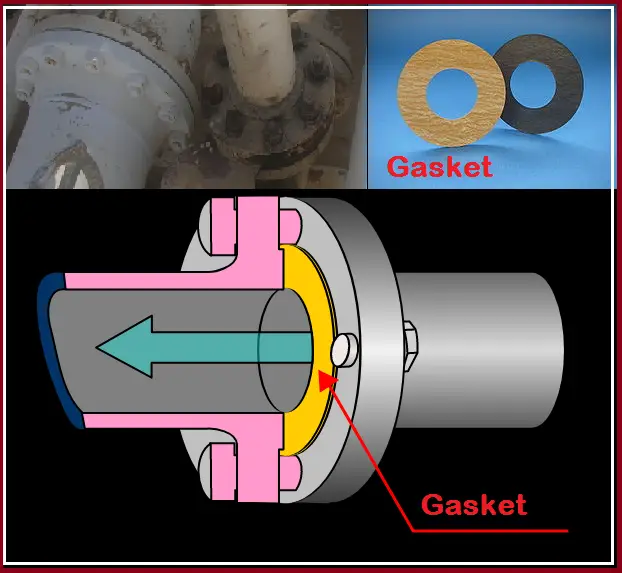
Parameters Affecting Flange Gasket Performance
The performance of the gasket in a flanged joint is affected by a number of factors. All of these factors must be taken into consideration when selecting a gasket:
Effect of Flange Load
All gasket materials must have sufficient flange pressure to compress the gasket enough to ensure that a tight, unbroken seal occurs. The flange pressure or minimum seating stress, necessary to accomplish this is known as the “y” factor. This flange pressure must be applied uniformly across the entire seating area to achieve perfect sealing. However, in actual service, the distribution around the gasket is not uniform. The greatest force is exerted on the area directly surrounding the bolts. The lowest force occurs mid-way between two bolts. This factor must be taken into account by the flange designer.
Effect of Internal Pressure
While in service, as soon as pressure is applied to the vessel, the initial gasket compression is reduced by the internal pressure acting against the gasket (blowout pressure) and the flanges (hydrostatic end force). To account for this, an additional preload must be placed on the gasket material. An “m” or maintenance factor has been established by ASME to account for this preload. The “m” factor defines how many times the residual load (original load minus the internal pressure) must exceed the internal pressure. In this calculation, the normal pressure and the test pressure should be taken into account.
Effect of Temperature
The effects of both ambient and process temperature on the gasket material, the flanges, and the bolts must be taken into account. These effects include bolt elongation, creep relaxation of the gasket material, or thermal degradation. This can result in a reduction of the flange load. The higher the operating temperature, the more care needs to be taken with the gasket material selection. As the system is pressurized and heated, the joint deforms. Different coefficients of expansion between the bolts, the flanges, and the pipe can result in forces that can affect the gasket. The relative stiffness of the bolted joint determines whether there is a net gain or loss in the bolt load. Generally, flexible joints lose bolt load.
Effect of Fluid
The media being sealed is usually a liquid or a gas with gas being harder to seal than a liquid. The effect of temperature on many fluids causes them to become more aggressive. Therefore, a fluid that can be sealed at ambient temperature, may adversely affect the gasket at a higher temperature. The gasket material must be resistant to corrosive attack from the fluid. It should chemically resist the system fluid to prevent serious impairment of its physical properties.
Surface Finish of the Gasket
The surface finish of a gasket — which consists of grooves or channels pressed or machined onto the outer surface — governs the thickness and compressibility required by the gasket material to form a physical barrier in the clearance gap between the flanges. A finish that is too fine or shallow is undesirable, especially on hard gasket materials, because the smooth surface may lack the required grip, which will allow extrusion to occur. On the other hand, a finish that is too deep will yield a gasket that requires a higher bolt load, which may make it difficult to form a tight seal, especially when large flange surfaces are involved. Fine machining marks applied to the flange face, tangent to the direction of applied fluid pressure can also be helpful. Flange faces with non-slip grooves that are approximately 0.125 mm deep are recommended for gaskets more than 0.5 mm thick; and for thinner gaskets, grooves 0.065 mm deep is recommended. Under no circumstances should the flange-sealing surface be machined with tool marks extending radially across the gasket-sealing surface; such marks could allow leakage.
Effect of Flange Gasket Thickness
For a given material, it is a general rule that a thinner gasket is able to handle higher compressive stress than a thicker one. However, thinner materials require a higher surface finish quality. As a rule of thumb, the gasket should be at least four times thicker than the maximum surface roughness of the flange faces. The gasket must be thick enough to occupy the shape of the flange faces and still compress under the bolt load. In situations where vibration is unavoidable, a thicker gasket than the minimum required should be employed.
Gasket Width
In order to reduce the bolt load required to produce a particular gasket pressure, it is advisable not to have the gasket wider than is necessary. For the given gasket stress, a raised face flange with a narrow gasket will require less preload and thus less flange strength than a full-face gasket. In general, high-pressure gaskets tend to be narrow.
Stress Relaxation
This factor is a measure of the material’s resiliency over a period of time and is normally expressed as a percentage loss per unit of time. All gasket material will lose some resiliency over time, due to the flow or thinning of the material caused by the applied pressure. After some initial relaxation, the residual stress should remain constant for the gasket.
Effect of Gasket Outer Diameter
For two gaskets made of the same material and having the same width, the one with a larger outer diameter will withstand higher pressure. Therefore, it is advisable to use a gasket with an external diameter that is as large as possible.
Codes & Standards for Gasket Design
The following standards are normally adopted for specifying gaskets.
- ASME B16.21 Non-metallic flat gaskets for pipe flanges.
- ASME B16.20 Metallic Gaskets for steel pipe flanges, Ring Joints, Spiral Wounds, and Jacketed
- IS2712 Specification for compressed Asbestos fiber jointing.
- BS 3381 Spiral Wound Gaskets to suit BS 1560 Flanges
How to Select a Gasket? Flange Gasket Selection
The gasket material selected should be one that is not adversely affected physically or chemically by the service conditions.
The following factors dictate the proper selection of gaskets.
- The gasket material should be compatible with the fluid service.
- Ability to withstand the pressure-temperature of the system.
- The service life of the gasket
- Gasket material must be corrosion-resistant against the service fluid.
- The gasket shall be readily available.
- Economy- Clients always prefer cheap and reliable gaskets.
- Flange Construction- The thickness of the flange has an effect on the bolt load and therefore seating stress. Thin and deformed flanges need softer gaskets.
- Standardization
- Quality Stud bolts
- Emission Parameters- Each selected gasket has different emission parameters.
- Flange Misalignment- Maximum misalignment of flanges will be 0.4 mm.
Gasket Materials
Depending on service, temperature, and pressure gaskets can be of various materials as listed in the table below:
Metallic | Non-Metallic | Winding Strips of Spiral Wound Gaskets | Filler Material for Winding |
Low Carbon Steel | PTFE | Stainless Steel | PTFE |
Stainless Steel | Compressed Asbestos | Duplex Steel | Graphite |
Soft Iron | Rubber | Monel | |
Chrome-Moly | Ceramic Fiber | Titanium |
Color-coded chart for the type of flange gasket identification
Spiral wound gaskets with stainless steel core and PTFE or graphite as the filler material is the most widely used gasket for process industries. For inspection and identification purposes, ASME B16.20 provides a Color Coding Chart as shown in Fig. 11 below:
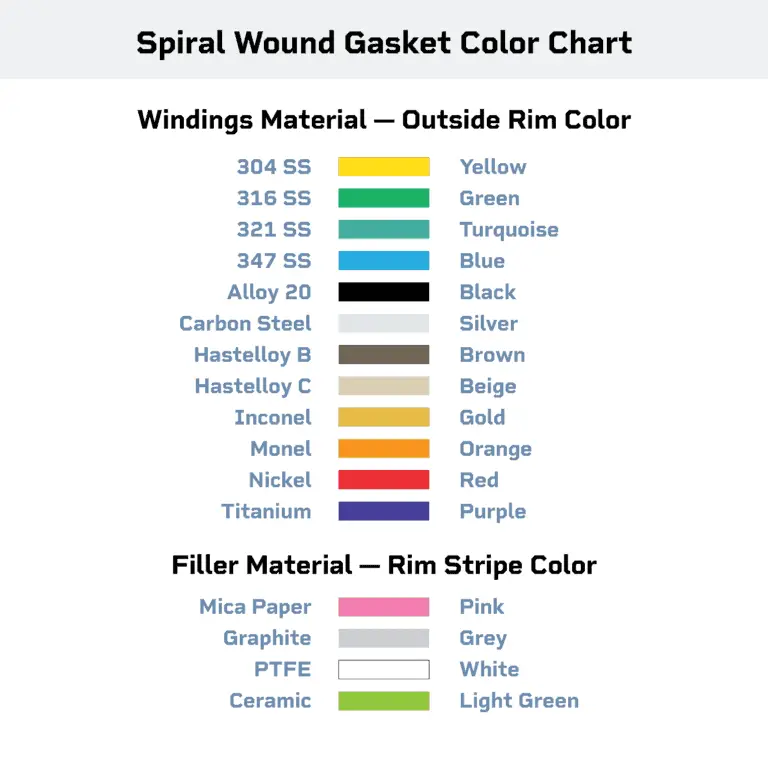
The color coating is painted on the ring’s outside surface allowing the inspector to identify the windings material.
Characteristics of a Gasket
- The gasket material has to be soft in order to compress this in the irregularities of flanges.
- The gasket should be Gas-Liquid tight so that it does not leak or cause emissions.
- The gaskets should not creep under the influence of stress and temperature. This could result in lower bolt stresses and possible leakage.
- The resilience of the gasket should take static and dynamic effects due to stress, temperature, and pressure.
- The gasket has to withstand internal pressure without being blown out.
- The gasket should be capable of achieving sealing at elevated temperatures.
- It has to be resistant to the chemical attack of the medium without polluting the media.
- It should possess anti-stick properties such that when opening the flange, the gasket has to lose easily from the flange.
- It has to be stiff enough to make installation as easy as possible.
Why do Gaskets Leak?
Gaskets may leak due to any one or more of the following reasons:
- Damage during assembly
- Poor Gasket selection
- Excessive flange rotation
- Gasket damage or relaxation due to flange rotation
- Gasket damage due to differential thermal expansion
- Incorrect assembly bolt load
- Load loss due to thermal fluctuation
- Gasket load loss due to pressure and or piping loads
- excessive gasket relaxation
- Excessive gasket load
What costs are involved with a flange gasket failure?
- Low profit due to leakage
- Cost of online sealing with clamps
- Cost of re-matching
- Cost of replacement equipment
- Cost of Engineering and maintenance hours spent addressing leakage
- Report of incidents and additional paperwork
- Pollution of environment
- Cleaning costs
- Possible personal injuries
- Cost of disassembly, repair, and machining
What could engineering do to prevent leakage through Gaskets?
- Proper selection of the correct assembly bolt stress
- Correct location, constraint, and width of the sealing
- Consideration of bending loads, and misalignment.
- Quantify effects of gasket creep/relaxation
- Quantify the effects of temperature and pressure
- Maximum permissible assembly load
- Correct gasket selection
- Root cause analysis
Basic Calculations for Gasket Selection for a Flanged Joint
Basic calculations required during gasket selection are provided in the following image (Fig. 12)
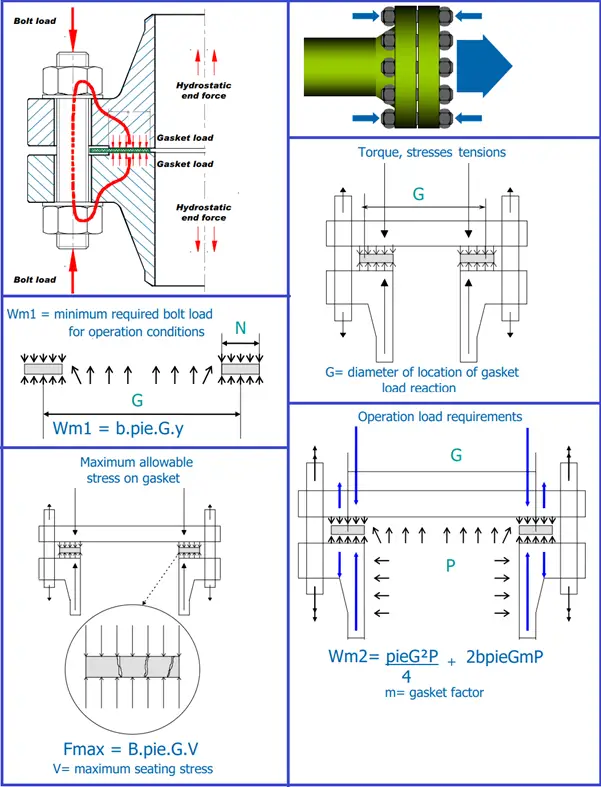
Advantages and Disadvantages of Flange Gaskets
Advantages of gaskets:
- Sealing Performance: Gaskets are designed to provide a reliable and leak-free seal between two mating surfaces. They are capable of sealing under high pressures and temperatures, as well as in corrosive and abrasive environments.
- Flexibility: Gaskets are available in a wide range of materials, sizes, and shapes, making them suitable for a variety of applications. They can be easily customized to meet the specific requirements of the application.
- Cost-effective: Gaskets are generally less expensive than other sealing methods, such as welding or brazing. They can also be easily replaced if they become damaged or worn out.
- Easy to Install: Gaskets are easy to install and require minimal equipment or tools. This makes them ideal for applications where downtime needs to be minimized.
Disadvantages of gaskets:
- Compatibility Issues: Gaskets are made from a variety of materials, and not all materials are compatible with all fluids or gases. It is important to select the correct gasket material for the specific application to ensure compatibility and prevent leakage.
- Maintenance: Gaskets require regular maintenance to ensure they remain in good condition and provide a reliable seal. This can include inspecting, cleaning, and replacing gaskets as needed.
- Compression Set: Over time, gaskets can lose their ability to seal due to compression set. This occurs when the gasket is compressed for an extended period and does not return to its original shape when the pressure is released. This can result in leakage and reduced sealing performance.
- Flange Condition: Gaskets rely on a flat and smooth flange surface to provide an effective seal. If the flange is damaged or corroded, the gasket may not be able to seal properly, resulting in leakage.
Difference between Seals and Gaskets
Both gaskets and seals are used to prevent fluid or gas leakage between two mating surfaces, but there are some key differences between them:
- Design: Gaskets are typically flat, static components that are placed between two mating surfaces and compressed to form a seal. Seals, on the other hand, are dynamic components that move relative to each other and may require a more complex design, such as lip seals or O-rings.
- Material: Gaskets are usually made from compressible materials, such as rubber, cork, or paper, that can conform to irregularities in the mating surfaces. Seals are typically made from materials that can resist wear, abrasion, and chemicals, such as polyurethane, Viton, or Teflon.
- Function: Gaskets are primarily used to seal static applications, such as pipe flanges or valve covers, while seals are used to seal dynamic applications, such as rotating shafts or hydraulic cylinders.
- Pressure: Gaskets are generally designed to withstand lower pressures, while seals are designed to withstand higher pressures and provide a more secure seal.
- Placement: Gaskets are usually placed between two flat surfaces, while seals are typically placed around a rotating or moving component.
Applications of Flange Gaskets
Flange gaskets find applications across a plethora of industries and scenarios:
- Oil and Gas Industry: In pipelines, refineries, and petrochemical plants, flange gaskets prevent the leakage of hazardous fluids, ensuring safety and operational efficiency.
- Food and Beverage Industry: Flange gaskets are essential in maintaining hygienic conditions by preventing contamination and leakage in food processing and beverage production.
- Chemical Industry: Chemical processes often involve aggressive substances. Flange gaskets prevent leaks that could lead to dangerous chemical reactions and environmental contamination.
- Water Treatment Plants: Gaskets ensure leak-free connections in water treatment facilities, preventing water loss and ensuring the quality of treated water.
- Power Generation: In power plants, flange gaskets play a crucial role in maintaining steam and fluid integrity, contributing to the overall efficiency of the power generation process.
Best Practices for Using Flange Gaskets
- Material Selection: Choose the right gasket material based on the application’s temperature, pressure, and the nature of the fluid being conveyed.
- Surface Preparation: Properly clean and prepare flange surfaces to ensure optimal gasket performance. Any irregularities on the flange surfaces can lead to leaks.
- Correct Installation: Follow manufacturer guidelines for proper gasket installation, including torque specifications and tightening sequences.
- Regular Inspection: Periodically inspect gaskets for signs of wear, damage, or degradation. Replace gaskets if necessary to prevent potential leaks.
- Environmental Considerations: Factors in the surrounding environment, such as temperature fluctuations and exposure to chemicals, when selecting gasket materials.
- Storage: Store spare gaskets in a cool, dry place away from direct sunlight and extreme temperatures to prevent premature degradation.
In summary, piping flange gaskets are generally static components that provide a seal between two flat surfaces, while seals are dynamic components that provide a seal around moving or rotating components. Piping Gaskets are usually made from compressible materials, while seals are made from materials that can withstand wear, abrasion, and chemicals. Flange gaskets might seem like small components, but their impact on industrial operations cannot be overstated. By choosing the right type of gasket, installing it correctly, and ensuring regular maintenance, industries can prevent costly leaks, ensure safety, and maintain operational efficiency.
Frequently Asked Questions (FAQs)
1. What is a gasket?
A gasket is a mechanical seal that fills the space between two mating surfaces to prevent the leakage of fluids or gases under compression. They are commonly used in industrial applications to ensure a tight and reliable seal.
2. Why are gaskets important in piping systems?
Gaskets play a crucial role in piping systems to prevent leaks and ensure the integrity of the system. They help maintain the pressure, temperature, and fluid containment within the pipes.
3. How do I choose the right type of gasket for my application?
The choice of gasket depends on several factors, including the type of fluid or gas being transported, temperature, pressure, and the materials of the mating flanges. Our article provides detailed information on various types of gaskets and their suitable applications.
4. What are the common materials used for gaskets?
Gaskets can be made from various materials, such as rubber, metal, graphite, and PTFE (Teflon). The choice of material depends on the specific requirements of the application.
5. Are piping flange gaskets reusable?
The reusability of a gasket depends on the material and condition. Some gaskets can be reused if they are in good condition after disassembly, while others may need replacement.
6. What are the different types of gaskets mentioned in the article?
Our article covers various types of gaskets, including spiral wound gaskets, ring-type joint (RTJ) gaskets, soft-cut gaskets (non-metallic gaskets), and metal gaskets. Each type has its unique characteristics and applications.
7. Can I use any piping flange gasket for high-temperature or high-pressure applications?
Not all gaskets are suitable for high-temperature or high-pressure environments. It’s essential to choose a gasket that is specifically designed to withstand the conditions of your application. The article provides guidance on gasket selection based on these factors.
8. How do I install a gasket correctly?
Proper installation of gaskets is crucial for their effectiveness. Our article offers guidance on the correct installation procedures, including torque values and alignment tips.
9. Are there any alternatives to traditional flange gaskets?
In some cases, alternatives like gasketless flange connections or sealants may be used instead of traditional gaskets. The choice depends on the application and specific requirements.
10. Where can I purchase gaskets for my piping system?
Gaskets can be sourced from various suppliers, including local hardware stores, specialized gasket manufacturers, and online retailers. It’s important to ensure that the gaskets you purchase meet the specifications required for your application.
11. How do I determine if a flange gasket needs replacement?
Flange Gaskets may need replacement if they show signs of wear, damage, or leakage. Regular inspection and maintenance are essential to identify when a gasket requires replacement.
Few more resources for you…
Piping Design and Layout
Piping Stress Analysis
Piping Materials
Piping Interface
The Teflon Seals, as the name suggest are back ups to prevent extrusion in rubber o-ring sealing systems. It is a common phenomenon for rubber o-rings to extrude especially with present day fluid systems that are a combination of high pressures and high temperatures.
Thanks a lot for the information..
Nice article,, thanks for sharing.
Very good article. Thank you for this information.
Great blog post – Speaking of which , people need to fill out a UK PSV 350 , my colleagues discovered a template document.
I liked the way you have described Gaskets and their Important properties. Thanks for sharing!!!
Thank you for the article and the suggested useful tips.
Very good article, thanks a lot for sharing!
Very good and useful article. Thanks a lot.
Very good. Important unformations. Congratulations.
Very important article
Anup, thank you very much for sharing these information, short but complete.
In Europe we use also the metallic lens gaskets, for both high pressure and temperature, according the standard
DIN 2696, and normally used with flanges ANSI 2500#.
Did you used somewhere during prior projects?
Many thanks again, stay healthy.
Thank you sir.
Thank you for your great information
Very informative article Anup.
So useful to enhanced knowledge.
Very good and informative article, thanks a lot for sharing.
thanks for lot of information
Thanks for good info. please share something about KAMOS gakets
I have come across Spiral wound gasket with Identification handle. I want to know the specific uses of this type of gasket have identification handle attached to it/