Pressure vessels play a crucial role in various industries. They help to process, store, or transport gases and liquids under high pressure. These vessels are designed to withstand internal or external pressure and are used in applications ranging from chemical plants and oil refineries to nuclear power plants and aerospace engineering. Heat exchangers, distillation towers, separators, reactors, reboilers, knock-out drums, scrubbers, dryers, coalescers, etc are some typical examples of pressure vessels. In this article, we will explore the different types of pressure vessels, their selection, and specific applications.
What is a Pressure Vessel?
A pressure vessel can be defined as a container designed to hold gases, vapors, liquids, or two-phase fluids at a pressure substantially different from the ambient pressure, and equipped with provisions for the introduction or removal of heat from the container. The pressure differential is dangerous, and there may be a risk of bursting if not properly designed, fabricated, installed, and maintained. Pressure vessels consist of some of the important parts like shell, head, nozzle, saddles, skirts, etc.
The ASME Boiler and Pressure Vessel Code provides rules and guidelines for the design, construction, inspection, testing, and certification of pressure vessels to ensure their safe operation under various pressure and temperature conditions. This code is widely recognized and followed by manufacturers, operators, and regulators worldwide to ensure the integrity and safety of pressure vessels used in various industries.
Types of Pressure Vessels
Pressure Vessels can be categorized based on various parameters as given below:
- Pressure Vessel Types Based on Shape
- Types of Pressure Vessels Based on Purpose
- Classification of Pressure Vessels Based on Construction
- Pressure Vessel Classification Based on Orientation/Positioning
- Types of Pressure Vessels Depending on Mounting
- Pressure Vessel Types Depending on the Material of Construction
- Types of Pressure Vessels based on Method of Heating
A. Classification based on Shape
Considering the shapes, there are four specific types of pressure vessels as mentioned below:
- Cylindrical Pressure Vessels
- Spherical Pressure Vessels, and
- Rectangular Pressure Vessels
- Conical Pressure Vessels
(a) Cylindrical Pressure Vessels:
Cylindrical pressure vessels are one of the most common types. They have a cylindrical shape with flat or dished ends, offering a simple and effective design for containing fluids under pressure. These vessels are used in applications such as storage tanks, air receivers, and hydraulic accumulators.
(b) Spherical Pressure Vessels:
Spherical pressure vessels have a spherical shape, offering excellent pressure distribution and strength. The uniform distribution of stresses allows them to handle higher pressures compared to other shapes. Spherical vessels are typically used in industries dealing with high-pressure gases like LPG storage, petrochemicals, and aerospace.
(c) Rectangular Pressure Vessels:
Rectangular pressure vessels are less common but find their use in specific applications, such as storing compressed gases or liquids in confined spaces. Their design allows for integration into limited spaces where cylindrical or spherical vessels would be impractical.
(d) Conical Pressure Vessels:
A conical pressure vessel is a type of pressure vessel that has a conical shape, with one end resembling a cone. These vessels are commonly used in industries such as food processing, pharmaceuticals, and chemical manufacturing. The conical shape allows for efficient mixing and blending of substances and is often used in processes where controlled agitation, heating, or cooling is required. The conical design promotes the circulation of materials inside the vessel, making it suitable for applications where homogenization and uniform temperature distribution are essential.
B. Classification based on Purpose:
Depending on the specific application purpose, there are four types of pressure vessels that are found to be widely used for industrial applications. They are:
- Storage Vessels
- Heat Exchangers
- Reactors, and
- Distillation Columns
(a) Storage Vessels:
These pressure vessels are primarily used for storing liquids or gases at a specified pressure. Storage vessels often serve as reservoirs for various industries, including petrochemicals, pharmaceuticals, and water treatment plants.
(b) Heat Exchangers:
Heat exchangers are pressure vessels designed to facilitate heat transfer between two fluids at different temperatures. They play a crucial role in applications like power generation, refrigeration, and chemical processing.
(c) Reactors:
Reactors are pressure vessels employed in chemical and petrochemical industries to facilitate chemical reactions under controlled conditions. They can be used for processes like polymerization, hydrogenation, and synthesis.
(d) Distillation Columns:
Distillation columns, a type of pressure vessel, are used for separating components in a liquid mixture based on their boiling points. They are essential in the production of petroleum products, alcoholic beverages, and other chemicals.
C. Classification based on Construction:
As per construction, three pressure vessel types are popular in industries. They are:
- Welded Pressure Vessels
- Forged Pressure Vessels, and
- Brazed Pressure Vessels
- Cast Pressure Vessels
- Riveted Pressure Vessels
(a) Welded Pressure Vessels:
Welded pressure vessels are constructed by welding together different sections of metal. They are commonly used in applications requiring low to medium pressure and are cost-effective for manufacturing.
(b) Forged Pressure Vessels:
Forged pressure vessels are made from a single piece of metal that is shaped and compressed under high pressure. This manufacturing process provides excellent strength and resistance, making them suitable for high-pressure applications.
(c) Brazed Pressure Vessels:
Brazed pressure vessels are assembled by joining metal parts using brazing techniques. They are often used for applications involving high temperatures and pressures, such as air conditioning and refrigeration.
(d) Cast Pressure Vessel
A cast pressure vessel is a pressure vessel that is manufactured by casting, a process where molten metal is poured into a mold to achieve the desired shape. Cast pressure vessels are typically made from materials like cast iron, cast steel, or other suitable alloys.
(e) Riveted Pressure Vessel
A riveted pressure vessel is a type of pressure vessel used to contain fluids or gases under pressure, and it is constructed by joining two or more metal plates or sections together using rivets. Rivets are mechanical fasteners that are inserted through holes in the plates and then deformed or headed on both ends to secure the plates tightly. Riveted pressure vessels were commonly used in the past but have largely been replaced by welded pressure vessels due to advancements in welding technology. These vessels are characterized by the visible rows of rivet heads on their exteriors.
D. Classification Based on Positioning/Orientation:
Pressure vessels come in various configurations, and one of the primary classifications is based on their positioning. Pressure vessels can be categorized as either horizontal or vertical, depending on the orientation of the vessel with respect to the ground. Each orientation offers distinct advantages and is chosen based on specific application requirements and space constraints.
Horizontal Pressure Vessels:
Horizontal pressure vessels are cylindrical tanks laid horizontally, with their length extending parallel to the ground. They typically have dished ends at both sides, providing structural stability and facilitating better stress distribution. The horizontal orientation allows for an even distribution of weight along the vessel’s length.
Typical Applications:
- Transportable Storage: Horizontal vessels are commonly used for transporting liquids or gases from one location to another. Examples include tanker trucks used for transporting liquefied gases or liquid chemicals.
- Compact Space Utilization: In applications where space is limited, such as onboard ships or in small processing plants, horizontal vessels prove advantageous as they can be placed under or alongside equipment efficiently.
- Vapor-Liquid Separators: Horizontal pressure vessels are also used as vapor-liquid separators to remove entrained liquid droplets from gas streams in various processes.
Horizontal vessels are preferred when:
- Space is limited, and a low-profile design is necessary.
- Transportability is essential for moving liquids or gases between locations.
- The vessel needs to function as a vapor-liquid separator in gas processing.
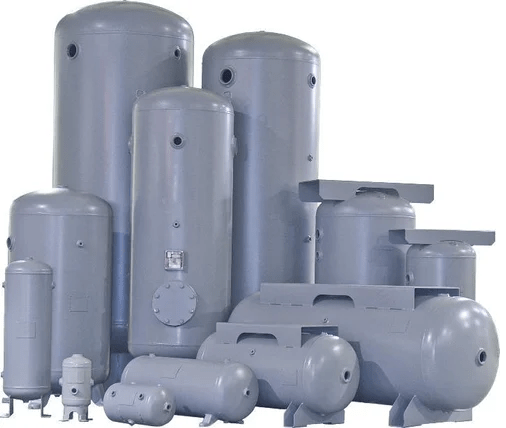
Vertical Pressure Vessels:
Vertical pressure vessels, as the name suggests, stand upright with their height perpendicular to the ground. They often have a cylindrical or spherical shape and can have either flat or dished ends. The vertical orientation allows for better utilization of vertical space, making them suitable for taller installations.
Typical Applications:
- Storage Vessels: Vertical pressure vessels are widely used as storage tanks in industries such as petrochemicals, oil and gas, and water treatment. Their upright design minimizes the footprint and optimizes storage capacity.
- Boiler Systems: Many industrial boiler systems utilize vertical pressure vessels to generate steam for power generation or heating applications.
- Compressed Air Receivers: In pneumatic systems, vertical pressure vessels are employed as compressed air receivers to store pressurized air, ensuring a steady supply during peak demand.
Vertical vessels are preferred when:
- Vertical space is available and needs to be optimized.
- Higher storage capacities are required while minimizing the horizontal footprint.
- The vessel will be utilized as a part of a taller system, such as in boiler installations.
E. Pressure Vessel Types Depending on Mounting/Supporting
Based on how the pressure vessel is mounted or supported there are three categories of pressure vessels.
- Skirt Mounted Pressure Vessels: These are mainly vertical pressure vessels and they are supported by a skirt at the bottom of the vessel.
- Saddle Mounted Pressure Vessel: Most horizontal pressure vessels are saddle-mounted. Typical examples are shell and tube heat exchangers.
- Leg-Supported Pressure Vessels: Some of the vertical pressure vessels are found to be leg-supported.
- Lug-Supported Pressure Vessels: These types of pressure vessels are mounted on lug supports which are basically plates with holes.
F. Pressure Vessel Types Depending on the Material of Construction
Based on the base material of construction, pressure vessels are classified as follows:
- Metallic Pressure Vessels
- Ferrous Pressure Vessels
- Carbon Steel Vessels
- Stainless Steel Vessels
- Alloy Steel Vessels
- Cast Iron Pressure Vessels
- Non-Ferrous Pressure Vessels
- Aluminum Pressure Vessels
- Ferrous Pressure Vessels
- Non-metallic Pressure Vessel
- Plastic Pressure Vessels
- Composite Metal Pressure Vessels
G. According to the Method of Heating
Depending on the type of heating, there are two types of pressure vessels as mentioned below:
- Fired Pressure Vessel, and
- Unfired Pressure Vessel
Again based on the location of pressure vessel fabrication, they are of two types:
- Shop Fabricated Pressure Vessels, and
- Site Fabricated Pressure Vessels
Sometimes, pressure vessels are also classified based on the shell thickness. They are:
- Thick-walled Pressure Vessel, and
- Thin-walled Pressure Vessels
Selection of Pressure Vessels
The selection of pressure vessel types depends on several factors, including the specific application requirements, operating conditions, material compatibility, and available space. Here are some key considerations to help guide the selection process:
- Application and Purpose: Identify the primary purpose of the pressure vessel. Is it for storage, transportation, heat exchange, chemical reaction, or another specialized function? Each type of pressure vessel is designed to fulfill specific roles, so understanding the application is essential.
- Pressure and Temperature: Determine the operating pressure and temperature requirements. Different pressure vessels are designed to withstand various pressure levels and temperature ranges. Choose a vessel that can safely handle the intended pressure and temperature conditions.
- Material of Construction: Consider the compatibility of the vessel’s material with the fluid or gas it will contain. Materials must be resistant to corrosion, stress, and fatigue. Common materials include carbon steel, stainless steel, aluminum, and various alloys.
- Space Constraints: Evaluate the available space for installation. Horizontal vessels may be suitable when space is limited, while vertical vessels can be more efficient in maximizing storage capacity within a restricted footprint.
- Transportability: If the vessel needs to be transported between locations, consider factors like weight, size, and the need for mobility. Horizontal vessels are often preferred for transportable applications.
- Codes and Standards: Adhere to relevant codes and standards, such as the ASME Boiler and Pressure Vessel Code or other international regulations, to ensure compliance with safety guidelines and legal requirements.
- Maintenance and Inspection: Consider ease of maintenance and inspection. Some vessel designs may facilitate easier access for inspection and repairs, which can contribute to the longevity and safe operation of the vessel.
- Cost and Life-Cycle Considerations: Evaluate the initial cost, ongoing maintenance expenses, and the expected service life of the pressure vessel. Choose a vessel that balances cost-effectiveness with long-term reliability.
Examples of Pressure Vessel Types for Different Applications:
- Storage Vessels: Vertical cylindrical pressure vessels are often used for bulk storage of liquids and gases, such as in oil refineries, petrochemical plants, and water treatment facilities.
- Heat Exchangers: Shell and tube heat exchangers are widely used for transferring heat between two fluids at different temperatures.
- Reactors: Depending on the process requirements, reactors can be cylindrical, spherical, or other specialized shapes designed for specific chemical reactions.
- Compressed Air Receivers: Vertical pressure vessels with dished ends are commonly used as compressed air receivers in industrial pneumatic systems.
- Transportable Tanks: For transporting liquefied gases or liquids, horizontal cylindrical pressure vessels are commonly used, often mounted on transport vehicles.
Video Tutorial on Pressure Vessel Fundamentals
The following video provides a very nice overview of the fundamentals of pressure vessels that one should know:
Online Course on Pressure Vessels
If you wish to learn more about Pressure Vessels, their design, fabrication, installation, etc in depth, then the following online courses will surely help you: