Fractional distillation is a fundamental separation technique widely used in various industries, including petrochemicals, pharmaceuticals, and food production. This blog post aims to provide an in-depth understanding of fractional distillation, covering its principles, equipment, applications, and advantages. By the end, you’ll have a thorough grasp of how this process works and why it’s essential in modern chemistry.
What is Fractional Distillation?
Fractional Distillation or Distillation or Fractionation is the process of separation of components from a product or mixture (Crude Oil) by heating the mixture to a temperature at which several fractions of the compound will vaporize. It is a physical process. Normally, when the mixture is heated, the component with the lowest boiling point will vaporize first and will separate out from the mixture. With further increases in temperature, other components will start to vaporize and separate.
Fractional Distillation is the most widely used form of separation technology and finds uses in petroleum refineries, petrochemical, and chemical plants, natural gas processing, and cryogenic air separation plants. It is one of the most important separation processes.
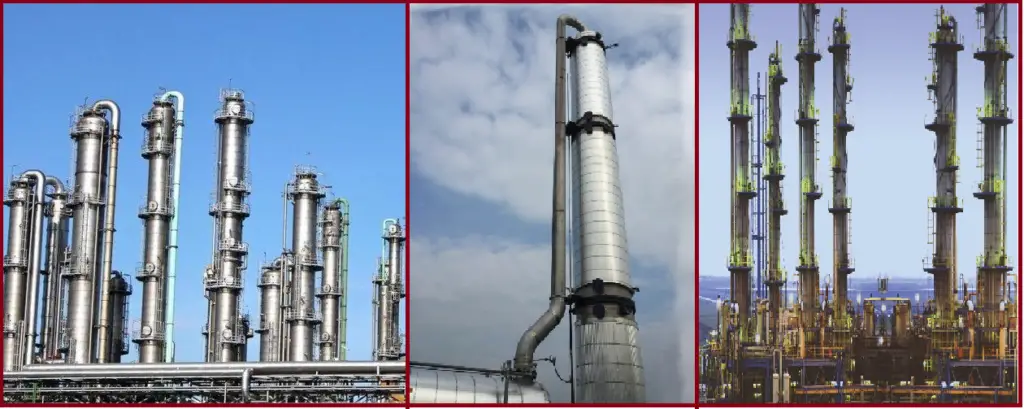
Principles of Fractional Distillation
Vapor-Liquid Equilibrium
At the heart of fractional distillation is the concept of vapor-liquid equilibrium. When a liquid mixture is heated, some components will vaporize before others, depending on their respective boiling points. When these vapors condense back into liquid form, the composition of the liquid phase changes, allowing for the separation of different components over repeated cycles.
Boiling Point
The boiling point of a substance is the temperature at which its vapor pressure equals the atmospheric pressure. In a mixture, each component has a unique boiling point. By carefully controlling the temperature during distillation, one can selectively vaporize the component with the lowest boiling point.
Raoult’s Law and Dalton’s Law
Raoult’s Law states that the partial vapor pressure of each component in a mixture is proportional to its mole fraction in the liquid phase. This principle is essential for understanding how components interact during distillation.
Dalton’s Law of partial pressures complements Raoult’s Law by stating that the total pressure exerted by a mixture of gases is equal to the sum of the partial pressures of each individual gas. These laws together provide a framework for predicting the behavior of mixtures during fractional distillation.
The Fractional Distillation Process
Step-by-Step Process
- Heating: The liquid mixture is heated in a distillation flask. As the temperature rises, components with lower boiling points start to vaporize.
- Vaporization: The vapor rises through the fractionating column, where it encounters a series of packing materials or trays that promote vapor-liquid contact.
- Condensation: As the vapor cools, it condenses back into liquid. The composition of this liquid will be richer in the component with the lower boiling point.
- Collection: The condensed liquid, or distillate, is collected in receiving flasks, and the process can be repeated to achieve higher purity.
What are the alternatives to the fractional distillation process?
There are a few alternatives to distillation as mentioned below but require higher investment costs. This is the main reason that distillation remains the main choice in the hydrocarbon industry, especially in large-scale applications.
- Liquid-Liquid Extraction or Solvent Extraction,
- Hydrophilic Pervaporation
- Multi-membrane Permeation Separation
- Adsorption process.
Types of Distillation Processes
There are various types of distillation processes that are popularly used in various industries for separating different products. Those are
- Fractional Distillation
- Extractive Distillation
- Reactive Distillation
- Simple distillation.
- Steam distillation.
- Vacuum distillation.
- Air-sensitive vacuum distillation.
- Short path distillation.
- Zone distillation
- Azeotropic Distillation
- Distillation under Reduced Pressure
- Destructive Distillation
- Industrial Distillation
When the physical properties (mainly boiling point) of the components in a mixture are very close to one another (For example an azeotropic mixture), the separation method becomes difficult.
Out of the above types, Fractional, Extractive, Reactive and Industrial distillation are the most frequently used ones.
Fractional Distillation
Fractional Distillation is the separation of key components from the product mixture by the difference in their relative volatility or boiling points by heating the product.
Extractive Distillation
In this type of distillation, an external solvent is introduced to the system that increases the separation. The external solvent changes the relative volatility between two close components by extracting one of the components, which forms a ternary mixture with different properties. Once, the extracted component is separated, the solvent is recycled into the system.
Reactive Distillation
In this method, a catalyst bed is used and the targeted component reacts when it is in contact with the catalyst. This separates the targeted component from the rest of the components in the mixture. The column where similar distillation is performed is termed a reactive distillation column.
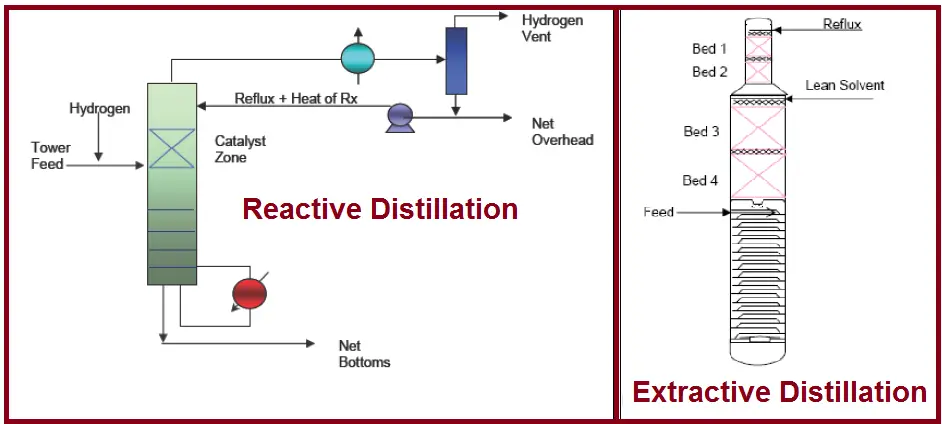
Industrial distillation
Industrial distillation is performed inside a large, vertical, tall cylindrical column. These columns are popularly known as “fractionation towers” or “distillation columns” or “Distillation Towers” and can be found in most process plants. The diameter of such Columns can range from about 65 centimeters to 6 meters and heights can range from about 6 meters to 60 meters or more.
Vacuum Distillation
Vacuum distillation reduces the pressure above the liquid mixture, lowering the boiling points of components. This technique is beneficial for thermally sensitive materials that might decompose at higher temperatures.
Steam Distillation
Steam distillation is a method used for extracting essential oils and volatile compounds from plants. By passing steam through the material, the desired components are vaporized and then condensed back into liquid form.
Role of the Fractionating Column
The fractionating column is critical in the fractional distillation process. It provides a large surface area for the vapor to interact with the liquid, promoting efficient mass transfer. The design and height of the column can significantly impact the separation efficiency, as a taller column generally allows for better separation due to increased theoretical plates.
Equipment Used in Fractional Distillation
Distillation Apparatus
The basic setup for fractional distillation consists of:
- Distillation Flask: Where the mixture is heated.
- Heat Source: Such as a heating mantle or a Bunsen burner.
- Thermometer: To monitor the temperature of the vapor.
Fractionating Column
The fractionating column can be packed with materials like glass beads, ceramic rings, or structured packing to enhance surface area and promote vapor-liquid interaction. The design varies based on the specific separation needs.
Reboiler and Condenser
- Reboiler: Heats the liquid mixture, converting it into vapor.
- Condenser: Cools the vapor, converting it back into liquid for collection.
Receiving Flasks
These flasks collect the separated components as they condense from the vapor phase.
Applications of Fractional Distillation
Petroleum Refining
Fractional distillation is a cornerstone of the petroleum industry. Crude oil is separated into various fractions, including gasoline, kerosene, diesel, and lubricating oils. Each fraction can then be further refined for specific applications.
Alcohol Production
In the production of alcoholic beverages, fractional distillation is employed to concentrate alcohol and separate different types of spirits. For instance, distilling fermented mash can yield vodka or whiskey, depending on the raw materials used.
Purification of Chemicals
Fractional distillation is used in laboratories and industries to purify solvents and chemicals. It enables chemists to isolate compounds for research or manufacturing processes.
Advantages and Disadvantages
Pros of Fractional Distillation
- High Purity: Capable of achieving high levels of separation, yielding pure components.
- Scalability: Can be scaled up for industrial applications or used in smaller laboratory settings.
- Versatility: Applicable to a wide range of mixtures and industries.
Limitations
- Energy Intensive: Requires significant energy input for heating and cooling.
- Complexity: The equipment can be complex and costly to operate.
- Sensitivity to Conditions: Performance can be affected by factors like pressure and temperature control.
In Conclusion, fractional distillation is an essential technique in both laboratory and industrial settings, enabling the effective separation of components in a mixture. Its principles are grounded in fundamental physical laws, making it a reliable and efficient process.
Few more Resources for you..
Process Basics..
Piping Design and Layout..
Piping Stress Analysis using Caesar II and Start-Prof..
Piping Materials..
Piping Interface Departments
It is very helpful for who looking jobs in piping or oil and gas industry.
Thank u so much for ur effort. And please continue the way… All the very best ☺️