ASME B31.3, the “process piping” code, provides guidelines for the pressure leak testing of piping systems. The primary goal of these tests is to ensure the integrity and safety of the piping system before it is put into service. As the name suggests, we just want to see if the piping we have designed and fabricated is not going to leak when put into operation. They basically serve two main purposes, as mentioned below:
- Determine the leak tightness of the welded and flanged joints of the piping system and
- Qualify joints that are not included in the UT or radiographic examination.
What are the methods of the Pressure Leak Test?
“Pressure Leak Test” is a general name. The more specific name depends on how you are going to execute the test. There are 6 types of methods stated in the code as below:
1. Hydrostatic Leak Test
Hydrostatic leak test, or simply Hydrotest, is the most common type of test that uses water as the test fluid. Tested at 1.5×Design Pressure×Ratio of Stress (that normally ends up as 1, unless operating at very high temperature). Only if a hydrostatic test could cause damage to the piping or is impractical, a pneumatic leak test be proposed as an alternative type of pressure leak test.
2. Pneumatic Leak Test
Using inert gas or air as the test fluid with 1.1×Design Pressure. This test must be carefully assessed as it presents hazards from the stored energy of compressed fluid during the test that could burst if a failure occurs.
3. Hydrostatic-Pneumatic Leak Test
Same as method 2, where a hydrostatic test may not be suitable; a combination of both hydrostatic & pneumatic tests could be proposed. However, I have never experienced such tests being conducted. If you have any insights about how it is done, please share them in the comment section.
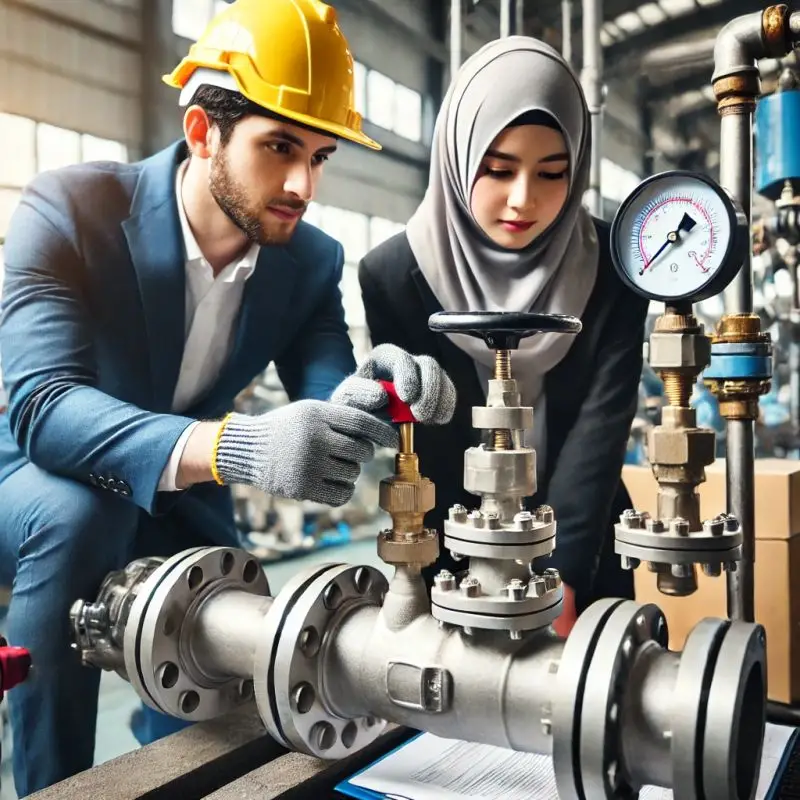
4. Initial Service Leak Test
With the owner’s approval, this test is only applicable to Category D fluid service. It is tested during the initial operation of the system with the service fluid itself. Pressure testing is the same as operating pressure.
5. Sensitive Leak Test
Sometimes, it is also known as a bubble test. The test pressure is only 105 kPa, or 25%×Design Pressure. This test is required for Category M fluid service as an additional pressure leak test on top of the hydrostatic or pneumatic test.
6. Alternative Leak Test
Where both hydrostatic and pneumatic tests are not feasible, an alternative leak test can be proposed. It consists of 3 procedures:
- Examination of all welds
- Flexibility analysis to be passed
- Performing a Sensitive Leak Test
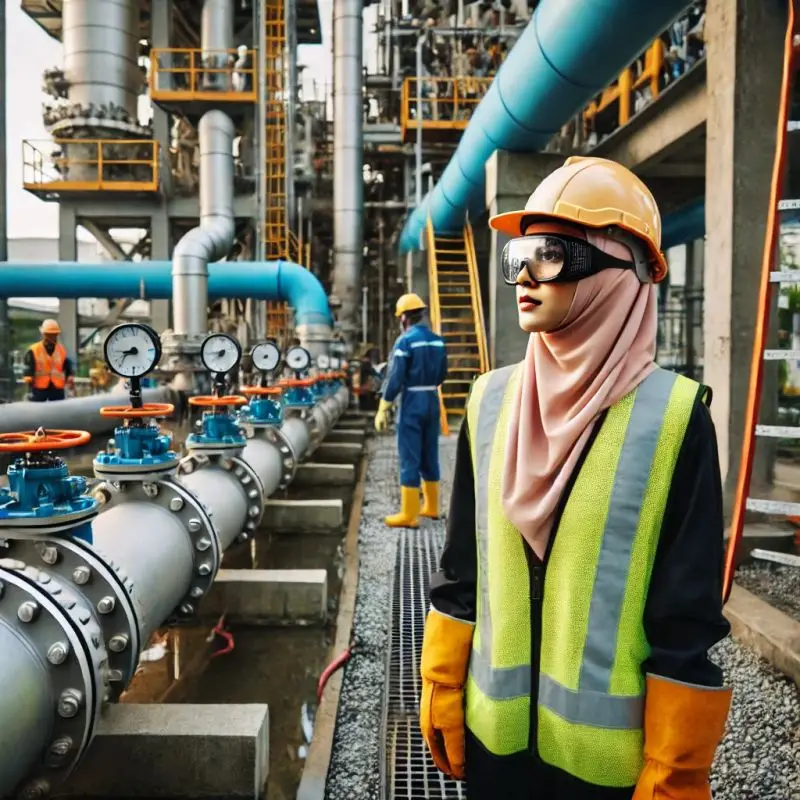
Requirements for Leak Pressure Tests
- Piping that is open to the atmosphere does not need to be leak tested, UNLESS, of course, specified by the owner or engineering design. The reason is that it is not an enclosed pressurized piping; the system has no pressure to retain.
- Category D piping systems can be tested using only the Initial Service Leak Test, PROVIDED; of course, it is approved by the Owner. So, if your projects face a setback schedule during testing, getting approval on this might make a difference in the overall progress.
- The pressure during the leak test only needs to be maintained for AT LEAST 10 minutes! The setup, fluid filling, and staggered pressurization are what take the most time. That is why if you could get Category D tested with only the Initial Service Leak Test, it would save lots of time!
- The pressure leak test shall be conducted after all required heat treatments have been completed. Yup, it’s kind of logic, isn’t it?
- Once a pressure leak test has been completed, if any repairs or modifications are made, the piping system shall be retested. Can this be waived if the changes are minor? Of course, with the Owner’s approval. The trick is, how minor is considered minor? You will need to justify that.
- All joints shall be exposed during the pressure leak test. Therefore, it is preferable that they are not painted beforehand. Paint may hinder any small leak point from being visible.
- If a pneumatic pressure test is specified, the hazard from stored energy shall be assessed. One way to do this is by using calculations in ASME PCC-2. The code provides guidelines for safe distance from the piping that is being pneumatically tested. Did you know the lowest distance is 50 m?