Diaphragm pumps are versatile and efficient devices that play a crucial role in various industries, from manufacturing and chemical processing to agriculture and healthcare. These pumps offer a unique pumping mechanism that sets them apart from traditional pumps, making them an essential tool for transferring fluids and handling challenging liquids. In this guide, we’ll delve into the mechanics, applications, advantages, and considerations of diaphragm pumps.
The Mechanics Behind Diaphragm Pumps
Diaphragm pumps, also known as membrane pumps, operate on a simple yet ingenious principle: they use the flexing of a diaphragm (a flexible barrier) to create a pressure differential that moves fluid through the pump. The diaphragm is typically made from materials such as rubber, thermoplastics, or elastomers, which can withstand the demands of the pumped fluid. As the diaphragm moves, it alternately creates a low-pressure area on one side and a high-pressure area on the other, causing fluid to flow into and out of the pump. Fig. 1 below shows the typical working of the pump in a diaphragm pump diagram.
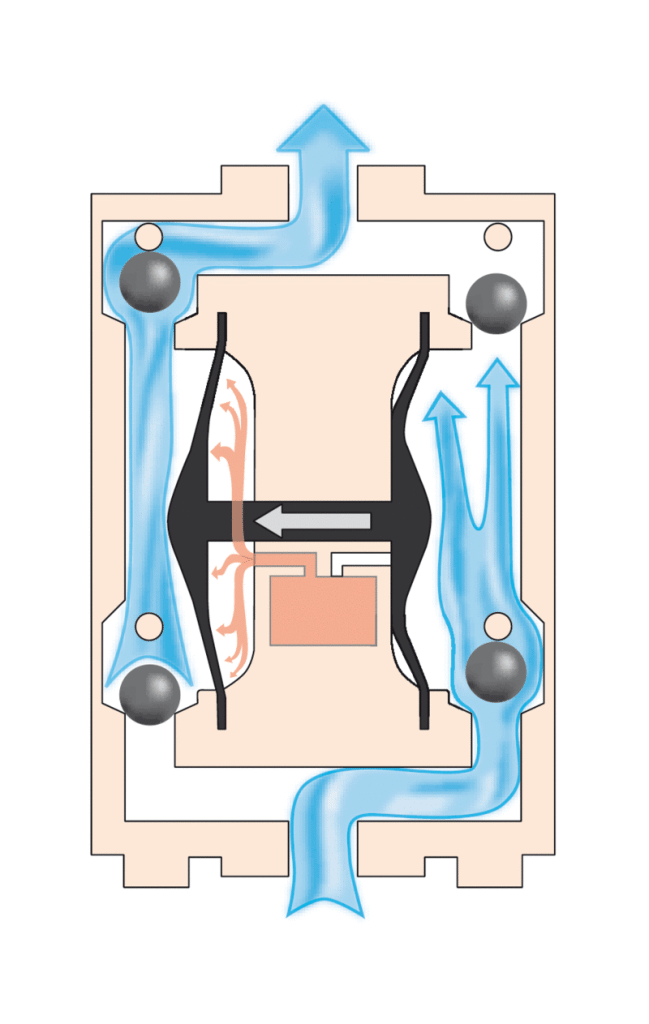
Key Components of a Diaphragm Pump
- Diaphragm: The diaphragm itself is the heart of the pump, responsible for fluid movement. Its flexibility and resilience are critical to its function.
- Check Valves: Diaphragm pumps feature inlet and outlet check valves that prevent the backflow of fluids and maintain the direction of flow.
- Drive Mechanism: Diaphragm pumps can be powered by various means, including electric motors, pneumatic air sources, and hydraulic systems.
Diaphragm Pump Types
There are several types of diaphragm pumps, each designed for specific applications:
Mechanically Actuated Diaphragm Pumps: These pumps use a mechanical linkage or cam to control the movement of the diaphragm.
Hydraulically Actuated Diaphragm Pumps: Here, hydraulic fluid or oil pressurizes the diaphragm, causing it to flex and create pressure differentials.
Air-Operated Double Diaphragm (AODD) Pumps:
An air diaphragm pump, also known as an air-operated double diaphragm (AODD) pump or pneumatic diaphragm pump, is a type of positive displacement pump that utilizes compressed air to move fluids. It’s a versatile and reliable pump commonly used for various fluid transfer and handling applications across industries. The distinctive feature of an air diaphragm pump is its use of air pressure to actuate the diaphragms, which creates alternating suction and discharge actions for fluid movement.
When compressed air is directed to one diaphragm, it flexes inward, creating a vacuum that draws fluid into the pump chamber from the inlet. At the same time, the other diaphragm is pushed outward, forcing fluid out through the outlet. When the air pressure is switched, the roles of the diaphragms reverse, causing the pump to cycle and the fluid to continue moving.
Characteristics of a Diaphragm Pump
Diaphragm pumps possess several distinctive characteristics that set them apart from other types of pumps. These features contribute to their versatility, efficiency, and suitability for various applications. Here are the key characteristics of a diaphragm pump:
Positive Displacement:
Diaphragm pumps are positive displacement pumps, meaning they move a fixed volume of fluid for each cycle of operation. This feature allows for precise and consistent fluid transfer, making them suitable for metering and dosing applications.
Dual-Action Mechanism:
Diaphragm pumps use a reciprocating motion of the diaphragm to create suction and discharge actions. The alternating flexing of the diaphragm creates pressure differentials that draw fluid into the pump and then expel it through the outlet.
Self-Priming:
Diaphragm pumps are inherently self-priming, capable of drawing fluid from a lower level without the need for external priming. This feature is advantageous when dealing with situations where a continuous flow of fluid might not be guaranteed.
Dry Running Capability:
Many diaphragm pumps can operate momentarily without liquid, making them more tolerant of unexpected fluid supply interruptions. This characteristic prevents damage to the pump and system components.
Versatility:
Diaphragm pumps can handle a wide range of fluids, including corrosive, abrasive, viscous, and shear-sensitive substances. The choice of diaphragm material and pump construction allows for compatibility with various liquids.
No Contamination:
The diaphragm acts as a barrier between the pumped fluid and the driving mechanism, ensuring that there is no contamination of the fluid by lubricants or other components.
Low Shear and Pulsation:
Diaphragm pumps provide gentle fluid handling with low shear forces, making them suitable for transferring delicate or shear-sensitive fluids. However, they can exhibit some degree of pulsation, which may need to be managed in certain applications.
Simple Maintenance:
Diaphragm pumps have relatively few moving parts, which simplifies maintenance and reduces downtime. Diaphragms are the primary wear components and can be replaced easily, extending the pump’s service life.
Multiple Drive Options:
Diaphragm pumps can be powered by various means, including electric motors, pneumatic air sources, and hydraulic systems, offering flexibility to adapt to different operational requirements.
Compact and Portable:
Diaphragm pumps are often compact in size and lightweight, making them portable and suitable for applications where space is limited or mobility is essential.
Suitable for Variable Flow Rates:
The flow rate of a diaphragm pump can be easily adjusted by changing the speed of the driving mechanism or altering the pressure on the diaphragm. This makes them adaptable to different process requirements.
Clog-Resistant Design:
Diaphragm pumps are less prone to clogging compared to some other pump types due to their smooth flow path and ability to handle solids and debris.
In summary, diaphragm pumps offer a unique combination of characteristics that make them a versatile and reliable choice for a wide range of industries and applications. Their positive displacement, self-priming ability, material compatibility, and ease of maintenance make them essential tools for fluid transfer and handling challenges.
Applications of Diaphragm Pumps
Diaphragm pumps find applications in a wide range of industries due to their versatility and ability to handle various fluids, including corrosive, abrasive, and viscous substances. Some common applications include:
- Chemical Processing: Diaphragm pumps handle aggressive chemicals and solvents safely and effectively.
- Pharmaceuticals and Biotechnology: These pumps are used in the production of pharmaceuticals, vaccines, and biotech products.
- Food and Beverage: Diaphragm pumps handle food products, beverages, and even dairy with care, maintaining product integrity.
- Oil and Gas: They are employed for metering and transferring fluids in oil and gas operations.
- Agriculture: Diaphragm pumps handle fertilizers, pesticides, and other agricultural chemicals.
Advantages of Diaphragm Pumps
- Versatility: Diaphragm pumps can handle a wide range of fluids, from thin and clear liquids to viscous and abrasive slurries.
- Self-Priming: They are self-priming, meaning they can draw fluid from a lower level without the need for external priming.
- Dry Running Capability: Diaphragm pumps can run dry without damage for short periods, which is beneficial in case of unexpected changes in fluid supply.
- Ease of Maintenance: These pumps have few moving parts, making maintenance relatively simple.
- No Contamination: The diaphragm isolates the pumped fluid from the driving mechanism, preventing contamination.
Considerations and Maintenance
While diaphragm pumps offer numerous benefits, there are some considerations to keep in mind:
- Material Compatibility: Ensure that the pump’s diaphragm material is compatible with the pumped fluid to prevent chemical reactions or degradation.
- Diaphragm Lifespan: Diaphragms may wear over time, especially when handling abrasive substances. Regular inspection and replacement are essential.
- Pulsation: Diaphragm pumps can exhibit pulsation in the flow, which may require additional measures to smooth out the output if necessary.
- Air Supply for AODD Pumps: If using air-operated double diaphragm pumps, a clean and consistent air supply is crucial for optimal performance.
Diaphragm Pump (Electric):
A diaphragm pump, when referred to as “electric,” indicates that it is powered by an electric motor. Electric diaphragm pumps use the energy from an electric motor to drive the movement of the diaphragm, which creates suction and discharge actions, allowing the pump to transfer fluids. These pumps are commonly used in a variety of applications across industries, and they offer the benefits of precise fluid transfer, ease of operation, and adjustable flow rates through the control of the motor speed.
Vacuum Diaphragm Pump:
A vacuum diaphragm pump is a type of diaphragm pump designed to create a vacuum by removing air or gas from a closed system. These pumps use the diaphragm’s reciprocating motion to expand and contract the pump chamber, creating a vacuum that draws air or gas out of the system. Vacuum diaphragm pumps are used in applications such as laboratory equipment, vacuum packaging, and processes requiring controlled or reduced pressure environments.
Water Diaphragm Pump:
A water diaphragm pump is a diaphragm pump specifically designed for handling water and other liquids. These pumps are often used in applications where water needs to be transferred, circulated, or pumped, such as in agriculture for irrigation, fluid transfer in water treatment plants, and water circulation in industrial processes. Water diaphragm pumps are chosen for their ability to handle different types of water, including clean water, wastewater, and slurries.
Pneumatic Diaphragm Pump:
A pneumatic diaphragm pump is a type of diaphragm pump that is powered by compressed air. It operates using the same basic principles as other diaphragm pumps, with the difference being that it uses compressed air to create the reciprocating motion of the diaphragm. Pneumatic diaphragm pumps are known for their durability, versatility, and ability to handle challenging fluids. They are commonly used in applications where electricity might not be available or where the pumped fluid is corrosive, abrasive, or hazardous.
Chemical Diaphragm Pump:
A chemical diaphragm pump is specifically designed to handle a wide range of aggressive and corrosive chemicals. These pumps are constructed using materials that are compatible with the chemicals being pumped, ensuring safe and efficient fluid transfer in industries such as chemical processing, petrochemicals, pharmaceuticals, and water treatment. They provide reliability and protection against chemical reactions or material degradation.
Diaphragm Pump High Pressure:
A high-pressure diaphragm pump is engineered to generate significant pressure levels while maintaining the positive displacement and self-priming characteristics of diaphragm pumps. These pumps are used in applications that require fluids to be transferred or pumped at elevated pressures, such as high-pressure cleaning, oil and gas operations, and industrial processes that demand precise pressure control.
Small and Micro Diaphragm Pump:
Small and micro diaphragm pumps are compact and lightweight versions of diaphragm pumps. They are ideal for applications where space is limited or where a smaller flow rate is required. These pumps find use in portable devices, medical equipment, laboratory instruments, and various other applications where precision and miniaturization are crucial.
Diaphragm Pump for Oil:
A diaphragm pump for oil is designed to handle the transfer of oil and other lubricating fluids. These pumps are commonly used in automotive, marine, and industrial applications for oil transfer, circulation, and lubrication.
Diaphragm Pump for Gas:
Diaphragm pumps for gas are utilized to transfer and handle gases, including both non-corrosive and mildly aggressive gases. They are employed in applications such as gas sampling, gas circulation, and gas evacuation in industries like laboratories, semiconductor manufacturing, and medical equipment.
Diaphragm Pump Troubleshooting:
Diaphragm pump troubleshooting involves identifying and addressing issues that may affect the pump’s performance. Common troubleshooting steps include checking for leaks, ensuring proper air supply (for pneumatic pumps), inspecting diaphragms for wear, and verifying proper suction and discharge connections. Addressing these issues promptly helps maintain pump efficiency and prevent downtime.
Diaphragm Pump Sprayer:
A diaphragm pump sprayer is an application-specific diaphragm pump used to create high-pressure fluid streams for spraying liquids, such as pesticides, herbicides, fertilizers, and cleaning solutions. These pumps are commonly used in agriculture, horticulture, pest control, and cleaning industries.
Metering Diaphragm Pump:
A metering diaphragm pump is designed for precise and controlled fluid dosing and metering. These pumps offer accurate volumetric output, making them suitable for applications where precise quantities of liquids or chemicals need to be delivered, such as in water treatment, chemical manufacturing, and pharmaceutical production.
Notable Diaphragm Pump Manufacturers
Here are some notable diaphragm pump manufacturers in the industry:
- Wilden (Dover Corporation): Wilden is a well-established manufacturer of air-operated double diaphragm (AODD) pumps, known for their reliability and versatility in various industries.
- ARO (Ingersoll Rand): ARO produces a wide range of air-operated diaphragm pumps used in diverse applications, including industrial, chemical, and mining sectors.
- Graco: Graco offers diaphragm pumps designed for fluid transfer, spray painting, and other applications in industries such as automotive, construction, and manufacturing.
- Yamada Corporation: Yamada specializes in diaphragm pumps for industries like chemicals, ceramics, mining, and wastewater treatment.
- Sandpiper (Warren Rupp, Inc.): Sandpiper is known for its rugged AODD pumps used in demanding environments such as oil and gas, mining, and water treatment.
- Versamatic: Versamatic produces AODD pumps for various industries, including chemicals, paints, and food processing.
- Iwaki Air: Iwaki Air manufactures AODD pumps for chemical, petrochemical, and other industrial applications.
- DEPA (Part of Dover Corporation): DEPA produces AODD pumps for the food and beverage, pharmaceutical, and chemical industries.
- Almatec (Dover Corporation): Almatec specializes in hygienic AODD pumps used in sensitive industries like food, pharmaceuticals, and biotechnology.
- Blagdon Pump (IDEX Corporation): Blagdon Pump offers AODD pumps for a wide range of applications, including mining, water treatment, and process industries.
- Finish Thompson Inc.: Finish Thompson manufactures diaphragm pumps used in chemical processing, electroplating, and other industrial processes.
- Viking Pump (Idex Corporation): Viking Pump produces AODD pumps for various industries, including chemicals, paints, and adhesives.
These manufacturers are recognized for producing high-quality diaphragm pumps that cater to a wide array of industries and applications. It’s important to note that the availability and prominence of manufacturers may vary by region and industry specialization.
Conclusion
Diaphragm pumps are an integral part of various industries, offering reliable fluid transfer and handling solutions for a wide range of applications. Their unique pumping mechanism, versatility, and ability to handle challenging fluids make them essential tools in modern manufacturing, chemical processing, healthcare, and beyond. By understanding the mechanics, types, and considerations associated with diaphragm pumps, businesses can harness their benefits and enhance their operational efficiency.