In the world of industry and manufacturing, precision and efficiency are paramount to success. Whether it’s in the oil and gas sector, water treatment facilities, or even pharmaceuticals, the need for accurate and controlled chemical dosing is crucial. Chemical injection, a method used to introduce specific substances into a system, has emerged as a powerful technique to achieve these objectives. This blog article explores the concept of chemical injection, its diverse applications, and the benefits it brings to various industries.
What is Chemical Injection?
Chemical injection, as the name suggests, involves the controlled introduction of chemicals or substances into a system or process. It is used to achieve a range of objectives, including water treatment, corrosion inhibition, pH control, sanitization, and various other chemical processes. The technique offers a precise and measured way to introduce chemicals into a system, ensuring optimal performance and avoiding wastage.
Applications Across Industries:
1. Oil and Gas Industry:
In the oil and gas sector, chemical injection plays a vital role in enhancing oil recovery from reservoirs. Chemicals such as polymers, surfactants, and alkaline agents are injected into the well to improve the flow of oil and separate it from the reservoir rock. Additionally, chemical injection is used to mitigate the formation of scale and prevent corrosion in pipelines, thus extending their lifespan and maintaining productivity.
2. Water Treatment:
One of the most critical applications of chemical injection is in water treatment facilities. Chemicals like chlorine, ozone, and coagulants are added to disinfect water, remove impurities, and ensure it meets safety and quality standards before distribution. This process is crucial for providing clean and safe drinking water to communities and industries alike.
3. Pharmaceuticals:
In pharmaceutical manufacturing, chemical injection is employed to control the precise dosing of active pharmaceutical ingredients (APIs) during drug production. This guarantees the consistency and potency of medications, ensuring they are safe and effective for patients.
4. Agriculture:
In agriculture, chemical injection is used for precise fertilization and pest control. It enables farmers to apply fertilizers, pesticides, and herbicides in accurate quantities, reducing environmental impact and maximizing crop yield.
5. Industrial Processes:
Many other industries, such as food and beverage, pulp and paper, and chemical manufacturing, rely on chemical injection to optimize their processes and maintain quality control.
The Advantages of Chemical Injection
Precision and Control:
Chemical injection systems are designed to deliver chemicals in exact quantities, eliminating the guesswork and human error associated with manual dosing. This precision ensures consistent results and prevents under or over-dosing.
Cost Efficiency:
With accurate chemical dosing, wastage is minimized, leading to cost savings in chemical procurement and disposal. Moreover, chemical injection helps extend the life of equipment by preventing corrosion and scale buildup, reducing maintenance and replacement costs.
Environmental Friendliness:
By using the right amount of chemicals, there is less risk of releasing excess substances into the environment. This promotes sustainable practices and minimizes the ecological impact.
Enhanced Safety:
Chemical injection systems are often automated and remotely controlled, reducing the need for manual handling of hazardous substances. This improves worker safety and reduces the potential for accidents.
Increased Efficiency:
By optimizing chemical usage and process conditions, chemical injection enhances overall system efficiency, leading to improved productivity and performance.
What is a Chemical Injection Skid?
A chemical injection skid, also known as a chemical injection package or chemical injection system, is a self-contained unit designed to accurately and safely inject chemicals or substances into a process or system. These skids are commonly used in industries such as oil and gas, water treatment, petrochemicals, and manufacturing, where precise dosing and controlled chemical delivery are essential. Fig. 1 shows an example of a typical chemical injection skid.
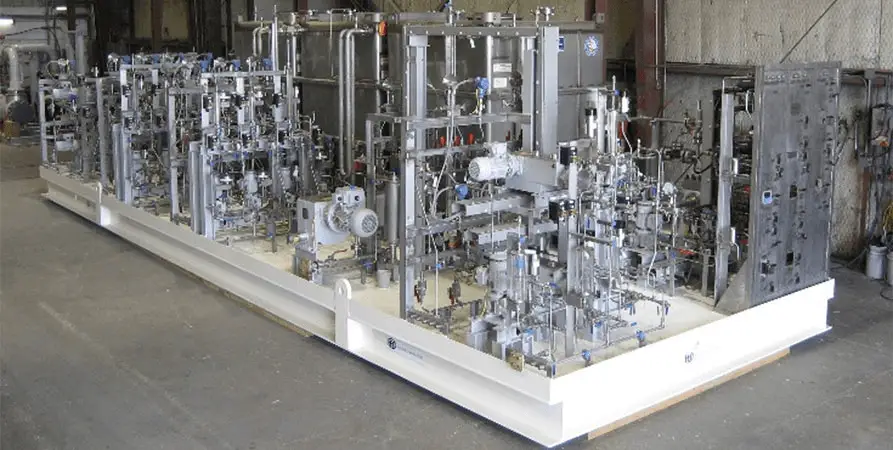
Components of a Chemical Injection Skid:
A typical chemical injection skid consists of several key components, each serving a specific function:
- Chemical Storage Tanks: These tanks hold the chemicals that need to be injected into the process. They come in various sizes and materials to accommodate different chemical requirements.
- Pumps: The pumps are responsible for moving the chemicals from the storage tanks to the injection point. They ensure a consistent and controlled flow rate of the chemicals into the system.
- Metering and Monitoring Devices: These devices measure and monitor the flow rate and pressure of the chemicals being injected. They provide real-time feedback and data to ensure accurate dosing and system performance.
- Valves and Control System: Valves control the flow of chemicals, and the entire system is operated and monitored through a control panel. This allows for remote and automated control, enhancing safety and efficiency.
- Safety Features: Chemical injection skids are equipped with safety features, such as pressure relief valves, leak detection systems, and emergency shutdown capabilities, to prevent accidents and ensure operator safety.
- Instrumentation: Various sensors and instruments are integrated into the skid to measure parameters like temperature, pressure, and chemical levels, providing valuable information for process control and optimization.
- Piping and Tubing: These components connect the chemical storage tanks, pumps, and metering devices to ensure the smooth flow of chemicals throughout the system.
- Frame and Housing: The skid is typically mounted on a sturdy frame and housed in a weather-resistant or climate-controlled enclosure, protecting it from environmental elements and facilitating easy transportation and installation.
Benefits of Using Chemical Injection Skids:
The use of chemical injection skids offers several advantages:
- Precision and Accuracy: Chemical injection skids provide precise and accurate dosing of chemicals, ensuring that the correct amount is delivered at the right time. This prevents under- or over-dosing, which can lead to process inefficiencies or safety risks.
- Efficiency: By automating the chemical injection process, skids eliminate the need for manual intervention, reducing the potential for human error and increasing overall process efficiency.
- Safety: Chemical injection skids are designed with safety features that prevent spills, leaks, and over-pressurization, protecting both the operators and the environment.
- Cost-Effectiveness: The controlled dosing and reduced wastage of chemicals lead to cost savings in chemical procurement and disposal.
- Flexibility: Chemical injection skids can be customized to suit specific process requirements and can handle a variety of chemicals and flow rates.
- Space-Saving: Since chemical injection skids are compact and self-contained, they require minimal space for installation and can be easily integrated into existing systems.
In summary, chemical injection skids are an essential tool in modern industries, offering precise and controlled chemical dosing, improving safety and efficiency, and contributing to cost savings and environmental sustainability.
What is a Chemical Injection Pump?
A chemical injection pump, also known as a metering pump or dosing pump, is a specialized device designed to accurately and precisely inject chemicals into a system or process. These pumps are widely used in various industries where controlled chemical dosing is essential to achieve specific objectives, such as water treatment, oil and gas production, pharmaceutical manufacturing, and many other applications.
How do Chemical Injection Pumps Work?
Chemical injection pumps work on the principle of displacing a specific volume of liquid with each stroke or cycle. They typically have a reciprocating or diaphragm-based design that allows them to deliver a consistent and controlled flow of chemicals.
Here’s a basic overview of how a chemical injection pump works:
- Suction Stroke: During the suction stroke, the pump draws the chemical from a storage tank or container through an inlet valve into the pump chamber.
- Discharge Stroke: During the discharge stroke, the pump pushes the chemical out through an outlet valve and into the process or system at the desired flow rate.
- Check Valves: Chemical injection pumps are equipped with check valves at the inlet and outlet to ensure a one-way flow of the chemical, preventing backflow and maintaining accuracy.
- Adjustment Mechanism: To control the flow rate, chemical injection pumps feature an adjustment mechanism, such as a stroke length adjustment or speed control, which allows the operator to set the desired dosing rate.
- Monitoring and Control: In modern chemical injection pumps, advanced electronic controls and sensors are often integrated, allowing for precise monitoring and feedback on flow rate, pressure, and other parameters. This enhances the accuracy and efficiency of chemical dosing.
Types of Chemical Injection Pumps:
There are several types of chemical injection pumps, each with its unique design and application:
- Diaphragm Pumps: These pumps use a flexible diaphragm to displace the chemical, creating suction and pressure. Diaphragm pumps are often used for low to medium flow rates and are well-suited for dosing corrosive or abrasive chemicals.
- Piston Pumps: Piston pumps use a reciprocating piston to draw and expel the chemical. They are ideal for high-pressure applications and can handle a wide range of chemicals.
- Peristaltic Pumps: Peristaltic pumps utilize a rotating roller or shoe that compresses a flexible tube, creating a squeezing action that moves the chemical through the tube. These pumps are gentle on the chemicals and are suitable for dosing sensitive substances.
- Solenoid Pumps: Solenoid pumps use an electromagnetic solenoid to actuate a diaphragm or piston, delivering precise and intermittent doses. They are often used in automated systems and where on/off dosing is required.
Benefits of Chemical Injection Pumps:
Chemical injection pumps offer several advantages in various industries:
- Accurate Dosing: Chemical injection pumps provide precise and consistent dosing, ensuring the correct amount of chemicals is delivered to the process.
- Efficiency: These pumps minimize chemical wastage, leading to cost savings and environmental benefits.
- Automation: Many chemical injection pumps can be integrated into automated control systems, reducing the need for manual intervention and enhancing process efficiency.
- Safety: Chemical injection pumps are designed with safety features to prevent leaks, spills, and over-pressurization, ensuring operator and environmental safety.
- Versatility: Chemical injection pumps can handle a wide range of chemicals, flow rates, and pressures, making them suitable for diverse applications.
In conclusion, chemical injection pumps play a vital role in achieving precise and controlled chemical dosing in various industrial processes. Their accuracy, efficiency, and safety features make them indispensable tools for maintaining optimal system performance and meeting industry standards.
Chemical Injection Quill
A chemical injection quill, also known as a chemical injection nozzle or chemical injection lance, is a specialized device used to introduce chemicals or other substances into a fluid stream within a process or pipeline system. The quill is designed to facilitate the controlled and uniform dispersion of the injected chemical, ensuring effective mixing and distribution throughout the fluid.
A typical chemical injection quill consists of a hollow tube or pipe with one end connected to the chemical injection system, such as a chemical injection pump or storage tank. The other end of the quill is positioned in the fluid stream where the chemical is to be introduced. The quill is designed to ensure that the injected chemical is evenly distributed within the fluid, avoiding localized concentrations or uneven mixing. More details about the chemical injection quill can be found here.
Chemical Injection Kit
A chemical injection kit is a packaged set of components and accessories designed to facilitate the safe and efficient introduction of chemicals or substances into a system or process. These kits are commonly used in various industries and applications where controlled chemical dosing is required. The kit typically includes all the necessary components for a complete chemical injection system, making it easy to install and use.
Components of a Chemical Injection Kit:
The specific components included in a chemical injection kit may vary depending on the manufacturer and the intended application. However, a typical chemical injection kit may consist of the following components:
- Chemical Injection Pump: The heart of the kit is a chemical injection pump or dosing pump. This pump is responsible for delivering a precise and controlled amount of chemicals into the system at the desired flow rate.
- Injection Quill: The kit may include an injection quill, which is a specialized device designed to introduce chemicals uniformly into the fluid stream. The quill ensures even dispersion and minimizes direct contact between the chemical and the pipe walls.
- Injection Valve: An injection valve is used to control the flow of chemicals from the injection pump to the quill. It allows for precise on/off control and adjustment of the injection rate.
- Tubing and Fittings: The kit will typically include the necessary tubing and fittings to connect the components together. These may include chemical-resistant tubing and various types of connectors and adapters.
- Check Valve: Some kits may include a check valve to prevent the backflow of fluid into the chemical injection line, ensuring that chemicals flow only in the desired direction.
- Mounting Hardware: Mounting brackets, clamps, or other hardware may be provided to secure and support the components in the desired location.
- Control System (Optional): In more advanced chemical injection kits, a control system or controller may be included to automate and monitor the chemical dosing process. This system can offer precise control and real-time monitoring of dosing rates and parameters.
- Instruction Manual: A detailed instruction manual or guide is typically included in the kit, providing information on the installation, setup, operation, and maintenance of the chemical injection system.
Chemical injection kits are versatile tools used in a wide range of industries, including water treatment, oil and gas, chemical manufacturing, and more. They provide a reliable and efficient solution for controlled chemical dosing, contributing to improved process performance and system integrity.
Conclusion
Chemical injection has become an indispensable tool in various industries, revolutionizing the way chemicals are incorporated into processes. Its precision, efficiency, and environmental benefits make it a go-to method for achieving optimal results in water treatment, oil recovery, pharmaceuticals, agriculture, and more. As technology continues to advance, we can expect even more sophisticated and automated chemical injection systems, further enhancing the way we harness the power of chemicals to drive progress and innovation across industries.
Dear Anup Kumar
thank you very much of the useful paper ,