In the world of mechanical engineering, software tools have become indispensable for designing, analyzing, simulating, and optimizing various aspects of mechanical systems. These tools not only enhance efficiency but also allow engineers to tackle complex challenges with precision and creativity. In this blog post, we will explore the top 10 mechanical engineering software tools that every aspiring and seasoned mechanical engineer should consider using.
To attain elevated levels of performance in mechanical products, computer technology plays a vital role in aiding design processes and performing system analysis within the realm of mechanical design. The following is a compilation of the ten most extensively employed mechanical engineering design software on a global scale. As an expert in mechanical engineering, are you using these engineering software packages?
Here are the top 10 mechanical engineering software tools for 2023.
- AutoCAD
- SolidWorks
- ANSYS
- MATLAB
- Pro-Engineer
- Unigraphics
- CATIA
- Cimatron
- Mastercam
- LabVIEW
1. AutoCAD:
AutoCAD, developed by Autodesk, revolutionized the field of mechanical engineering by introducing computer-aided design (CAD) technology. Since its inception in 1982, AutoCAD has become the backbone of countless design projects across industries.
Functions and Applications of AutoCAD:
AutoCAD serves as a versatile platform for creating accurate 2D and 3D models of mechanical components, structures, and assemblies. Its drafting and modeling tools empower engineers to translate concepts into detailed designs, facilitating visualization, analysis, and communication. The software’s functionality extends beyond mechanical engineering, finding utility in architecture, construction, and manufacturing. With its extensive library of symbols, blocks, and templates, AutoCAD streamlines the design process while adhering to industry standards.
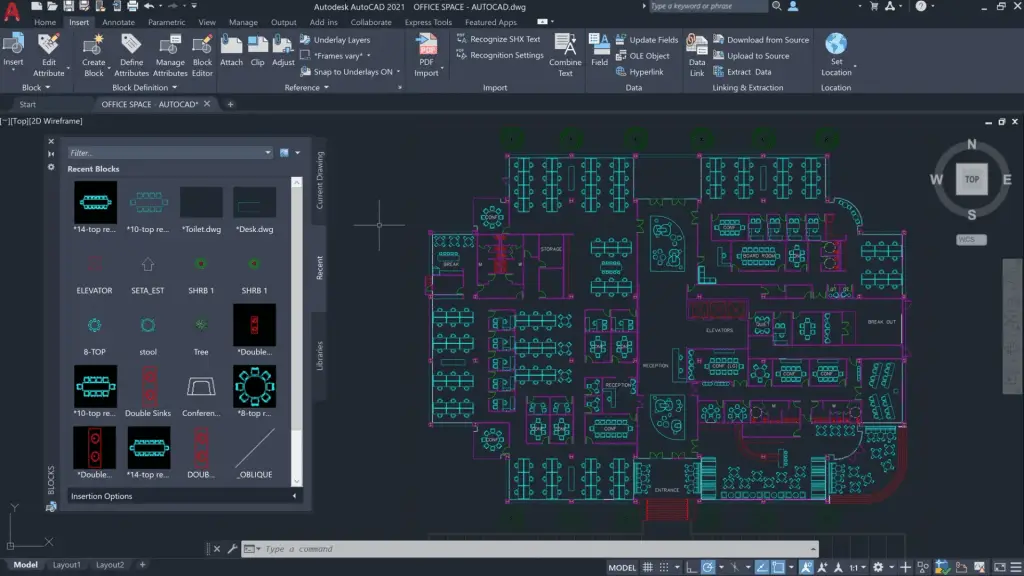
Features and Impacts:
AutoCAD offers a user-friendly interface, parametric design capabilities, and compatibility with third-party plugins. Its 3D modeling tools enable engineers to create intricate and realistic representations of complex mechanical systems. AutoCAD’s parametric constraints allow for easy modification and adaptation, ensuring efficient design iteration. Over the years, AutoCAD has evolved to include cloud collaboration, mobile access, and advanced rendering, bolstering its usefulness in modern engineering workflows.
2. SolidWorks:
SolidWorks, introduced by Dassault Systèmes in 1995, is a pioneering 3D CAD software that has become a cornerstone of mechanical engineering design.
Functions and Applications of SolidWorks:
SolidWorks empowers engineers to create comprehensive 3D models of mechanical components and assemblies, enabling visualization and simulation. Its parametric modeling capabilities facilitate efficient design changes and updates, while integrated tools for simulation and analysis allow engineers to predict and optimize performance. SolidWorks’ influence spans industries like aerospace, automotive, consumer goods, and more, fostering innovation and efficient product development.
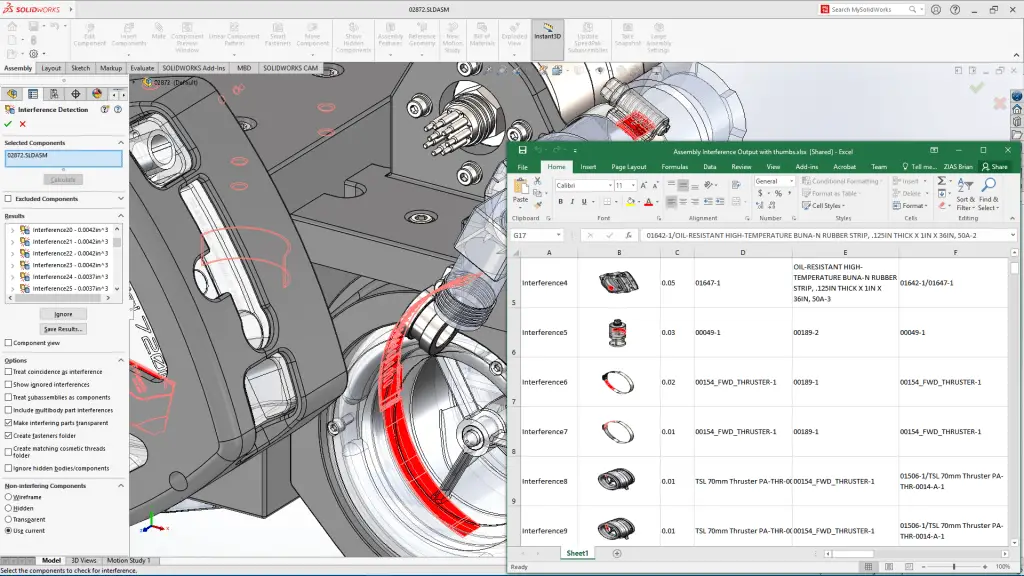
Features and Impact:
The software’s feature-rich toolbox includes advanced surfacing, sheet metal design, and rendering options, enhancing the level of detail in designs. SolidWorks’ simulation tools enable engineers to perform stress, thermal, and fluid flow analyses, ensuring the structural integrity and reliability of designs. Collaboration is simplified through SolidWorks’ integration with other design and PLM (Product Lifecycle Management) tools, aiding interdisciplinary teamwork and streamlining the design-to-manufacturing process.
3. ANSYS:
ANSYS, developed by ANSYS Inc., emerged as a pioneering simulation software in 1970, revolutionizing the field of mechanical engineering analysis and virtual testing.
Functions and Applications of ANSYS:
ANSYS serves as a comprehensive simulation platform, offering a wide range of capabilities including finite element analysis (FEA), computational fluid dynamics (CFD), and electromagnetic simulations. Engineers utilize ANSYS to study how mechanical designs behave under various conditions, predicting factors such as stress, thermal effects, and fluid flow. The software enables virtual testing and optimization, reducing the need for physical prototypes and minimizing development time and costs.
Features and Impact:
ANSYS provides intricate modeling and meshing tools for complex geometries, and its solver capabilities deliver accurate simulations of real-world scenarios. The software’s multiphysics capabilities enable engineers to analyze interactions between different physical phenomena, leading to holistic design insights. ANSYS’ impact on industries such as aerospace, automotive, energy, and electronics is profound, driving innovation and advancing engineering practices.
4. MATLAB:
MATLAB, developed by MathWorks, emerged in the late 20th century as a computational powerhouse, transforming the landscape of numerical analysis and algorithm development.
Functions and Applications of MATLAB:
MATLAB is a high-level programming language and environment that plays a crucial role in mechanical engineering. Engineers harness MATLAB’s capabilities for modeling dynamic systems, control system design, signal processing, and data analysis. Its extensive library of functions and toolboxes allows for efficient problem-solving in diverse engineering domains. MATLAB serves as a versatile platform for prototyping and simulating mechanical systems, aiding in research, design, and analysis.
Features and Impact:
MATLAB’s interactive and user-friendly interface encourages rapid development and testing of algorithms, making it an invaluable tool for engineers. The software’s graphical capabilities facilitate data visualization, aiding in the interpretation of results. Its compatibility with external hardware and software further extends its utility, enabling seamless integration into complex experimental setups. MATLAB’s influence extends beyond academia, finding applications in industries such as automotive, aerospace, and robotics.
5. Pro-Engineer (now Creo):
Pro-Engineer, later rebranded as Creo, was developed by PTC and introduced in 1987, revolutionizing parametric 3D modeling.
Functions and Applications of Creo:
Creo offers a robust set of tools for product design, simulation, and analysis. Its parametric modeling capabilities enable engineers to create associative models that update automatically as design changes occur. Creo’s application spans various industries, from consumer products to industrial equipment, where intricate designs and seamless collaboration are paramount.
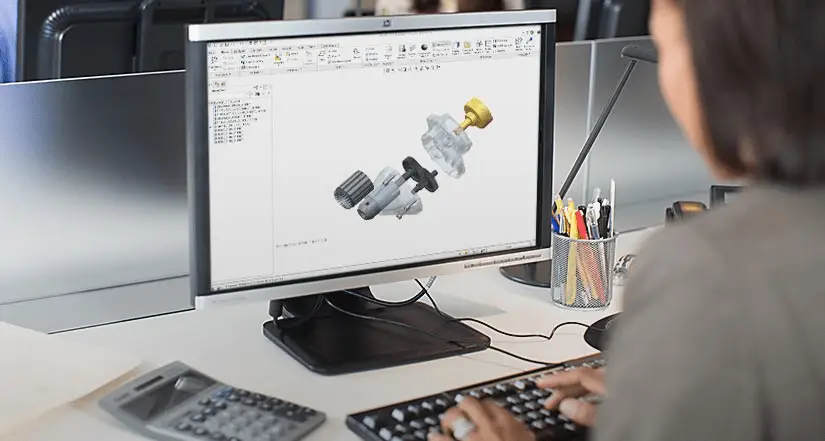
Features and Impact:
Creo’s feature-rich toolbox includes advanced surfacing, sheet metal design, and direct modeling capabilities. The software facilitates multi-disciplinary collaboration, allowing mechanical, electrical, and software engineers to work in harmony. Creo’s integration with product data management (PDM) and PLM systems ensures efficient data management throughout the product lifecycle, contributing to streamlined design and manufacturing processes.
6. Unigraphics (now Siemens NX):
Unigraphics, now known as Siemens NX, was developed by Siemens PLM Software and made its mark in the 1980s as a comprehensive solution for product design and engineering.
Functions and Applications of Siemens NX:
Siemens NX offers a suite of tools for product design, engineering analysis, and manufacturing. Its parametric modeling, surface modeling, and advanced simulation capabilities empower engineers to create complex mechanical systems. The software’s application extends to industries such as aerospace, automotive, and consumer goods, where precision and innovation are vital.
Features and Impact:
Siemens NX’s capabilities span the entire product lifecycle, from concept to manufacturing. Its integrated simulation tools enable engineers to conduct detailed analyses and optimization, resulting in improved product performance. The software’s digital twin concept allows engineers to create virtual representations of physical products, facilitating real-time monitoring and maintenance.
7. CATIA:
The full form of CATIA is Computer-Aided Three-Dimensional Interactive Application. It is developed by Dassault Systèmes and emerged in the 1980s as a revolutionary software suite for designing complex mechanical and engineering systems.
Function and Applications of CATIA:
CATIA provides a comprehensive suite of tools for 3D modeling, surface design, simulation, and multi-disciplinary collaboration. Its application spans industries like aerospace, automotive, and industrial design, where intricate and innovative designs are crucial.
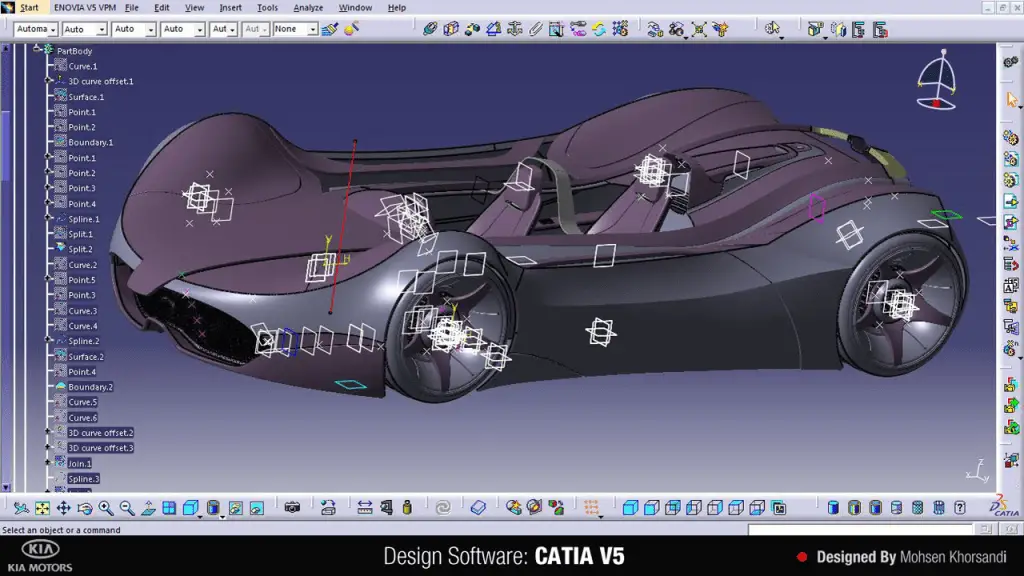
Features and Impact:
CATIA’s parametric and feature-based modeling capabilities allow engineers to create highly detailed and intricate designs. Its integrated simulation tools enable engineers to analyze and optimize mechanical systems, ensuring performance and reliability. CATIA’s collaborative features facilitate teamwork across various disciplines, promoting efficient product development and innovation.
8. Cimatron:
Cimatron, developed by 3D Systems, emerged as a specialized CAD/CAM software solution, addressing the unique challenges of toolmaking and mold design.
Functions and Applications of Cimatron:
Cimatron focuses on creating intricate geometries, designing molds, and generating tool paths for CNC machining. Its specialized capabilities are indispensable in industries where precision, accuracy, and complex shapes are paramount, such as automotive, electronics, and consumer goods.
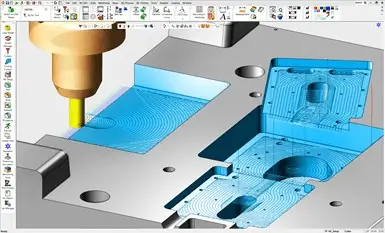
Features and Impact:
Cimatron offers tools for parametric design, mold design, and electrode design. Its integration with CAM capabilities allows engineers to seamlessly transition from design to manufacturing, optimizing the entire production process. Cimatron’s high degree of automation streamlines the creation of complex molds and tooling, reducing errors and production lead times.
9. Mastercam:
Mastercam, developed by CNC Software Inc., emerged as a leading CAM software, revolutionizing computer-aided manufacturing and machining processes.
Functions and Applications of Mastercam:
Mastercam focuses on generating precise tool paths for CNC machines, translating design models into tangible components. Its application spans industries like aerospace, automotive, and industrial manufacturing, where precision and efficiency in machining are vital.
Features and Impact:
Mastercam provides a range of machining strategies, from milling and turning to multi-axis machining. Its optimization tools ensure efficient tool paths, minimizing machining time and maximizing tool life. Mastercam’s compatibility with a wide range of CNC machines and its post-processing capabilities streamline the manufacturing process, allowing engineers to turn designs into high-quality products.
10. LabVIEW:
LabVIEW (Laboratory Virtual Instrument Engineering Workbench), developed by National Instruments, emerged as a powerful software platform for testing, measurement, and control systems.
Functions and Applications of LabVIEW:
LabVIEW enables mechanical engineers to develop applications for real-time data acquisition, analysis, and control. Its application extends to various industries, including research, automation, and experimental setups.
Features and Impact:
LabVIEW’s graphical programming approach allows engineers to create custom user interfaces and automate complex measurement systems without traditional coding. Its compatibility with a wide range of hardware devices facilitates seamless integration into experimental setups, enabling engineers to conduct real-time monitoring, data analysis, and control. LabVIEW’s impact spans academia, research institutions, and industries where precise measurement and control are essential.
These software tools, each with its unique capabilities and applications, have become integral to the practice of mechanical engineering. From design and analysis to simulation and manufacturing, these tools empower engineers to push the boundaries of innovation and create advanced mechanical systems that shape the world around us.
Why Use Engineering Software Tools: Benefits of Using Mechanical Software
Using mechanical software offers a multitude of benefits that significantly enhance the efficiency, accuracy, and creativity of the entire mechanical engineering process. Whether you’re designing complex components, analyzing structural integrity, or optimizing manufacturing processes, these software tools can revolutionize the way you work. Here are some of the key benefits:
Precision and Accuracy:
Mechanical software allows engineers to create precise and accurate designs with intricate detailing. Computer-aided design (CAD) tools enable exact measurements, tolerances, and geometric relationships, reducing the risk of errors and ensuring consistent quality in the final product.
Time and Cost Efficiency:
Designing, prototyping, and testing physical prototypes can be time-consuming and expensive. Mechanical software enables virtual prototyping, eliminating the need for multiple physical iterations. This leads to reduced development time, cost savings, and quicker time-to-market.
Visualization and Communication:
Advanced 3D visualization capabilities in these software tools help engineers better understand the design, making it easier to communicate ideas to stakeholders, clients, and team members. Visual representations enhance collaboration, reduce misunderstandings, and facilitate decision-making.
Simulation and Analysis:
Mechanical software offers simulation and analysis tools that allow engineers to predict how designs will behave under different conditions. This enables optimization, testing for factors like stress, strain, fluid flow, and heat transfer, leading to safer, more reliable products.
Innovation and Creativity:
Software tools provide a platform for experimentation and innovation. Engineers can explore multiple design variations, test unconventional ideas, and simulate scenarios that may not be feasible in physical prototypes.
Design Iteration and Modification:
Parametric modeling in many software tools enables quick and seamless design changes. Engineers can easily modify dimensions, features, or parameters and instantly observe the impact on the design, facilitating rapid iteration and refinement.
Multi-Disciplinary Collaboration:
Many software tools support collaborative workflows, allowing mechanical engineers to work alongside professionals from other disciplines like electrical and software engineering. This interdisciplinary approach ensures seamless integration of different systems and components.
Data Management and Documentation:
Mechanical software offers tools for organizing and managing design data, including version control, revision history, and annotations. This enhances data integrity, simplifies documentation, and aids in complying with industry standards and regulations.
Automation and Customization:
Software tools can automate repetitive tasks, reducing manual effort and minimizing human errors. Additionally, engineers can customize workflows and develop scripts to suit specific needs, boosting productivity and streamlining processes.
Global Accessibility and Remote Work:
Cloud-based solutions enable access to designs and projects from anywhere with an internet connection. This facilitates remote work, collaboration with international teams, and real-time updates on project progress.
Training and Skill Enhancement:
Using mechanical software enhances the technical skills of engineers, making them more proficient in modern engineering practices. Regular use of these tools encourages continuous learning and keeps professionals up-to-date with the latest industry trends.
In summary, mechanical software tools are indispensable assets for modern mechanical engineers, offering a wide range of benefits that contribute to improved design quality, reduced costs, faster development cycles, and enhanced collaboration. As technology continues to evolve, these software tools will play an increasingly critical role in shaping the future of mechanical engineering.
Selecting the Right Mechanical Engineering Software
Selecting the right mechanical software for your needs is a crucial decision that can significantly impact your efficiency, productivity, and the quality of your work. With a wide array of options available, it’s important to consider several factors before making your choice. Here’s a step-by-step guide to help you select the most suitable mechanical software:
1. Define Your Requirements:
Start by identifying your specific needs and goals. What tasks do you need the software to perform? Do you require 3D modeling, simulation, analysis, or a combination of these? Clarify your objectives to ensure you choose software that aligns with your priorities.
2. Evaluate Features:
Compare the features and capabilities of different software options. Look for tools that offer the functionalities you require, such as parametric modeling, simulation, rendering, CAM, etc. Consider the software’s user interface, ease of use, and the extent to which it meets your workflow demands.
3. Consider Industry and Applications:
Different software tools are tailored to specific industries and applications. Some may excel in automotive design, while others may be better suited for aerospace or consumer goods. Choose software that is relevant to your industry and the type of projects you work on.
4. Scalability and Integration:
Consider whether the software can scale as your projects become more complex. Look for options that integrate well with other software tools you use, such as CAD/CAM systems, data management solutions, or analysis platforms.
5. Learning Curve and Training:
Evaluate the learning curve associated with the software. Will you or your team require extensive training to use it effectively? Choose software that offers resources such as tutorials, documentation, and customer support to help you get up to speed quickly.
6. Compatibility and Interoperability:
Ensure that the software is compatible with your hardware and operating system. Additionally, check whether it supports common file formats to ensure smooth collaboration with clients, partners, and other team members.
7. Performance and Simulation Accuracy:
If simulation and analysis are critical for your work, assess the accuracy and reliability of the software’s simulation capabilities. Look for software with a proven track record in providing accurate results.
8. Budget and Cost:
Consider your budget constraints and the cost of the software, including any subscription fees, licensing costs, and potential add-ons. Evaluate whether the software’s benefits justify its price.
9. User Community and Support:
Research the software’s user community and support options. Online forums, user groups, and communities can be valuable resources for troubleshooting and sharing knowledge. Check if the software vendor provides timely customer support and updates.
10. Trial Period and Demos:
Whenever possible, take advantage of trial periods or demos offered by software vendors. This hands-on experience will give you a feel for the software’s interface, features, and how well it suits your needs.
11. Long-Term Considerations:
Think about the long-term implications of your choice. Will the software continue to meet your needs as your projects evolve? Is the software regularly updated with new features and improvements?
Remember that selecting the right mechanical software is a personalized process that depends on your specific requirements and preferences. Take your time to research, evaluate, and test different options to make an informed decision that aligns with your engineering goals.
Future Trends in Engineering Software
The field of mechanical engineering software is rapidly evolving, driven by advancements in technology, industry demands, and emerging trends. As we look ahead, several key trends are expected to shape the future of mechanical software:
1. Integration of Artificial Intelligence (AI) and Machine Learning (ML):
AI and ML are poised to revolutionize mechanical engineering software by enabling predictive analytics, optimization, and automation. These technologies can assist in generating design alternatives, conducting simulations, and identifying optimal solutions based on vast datasets. AI-driven tools can accelerate the design process and help engineers make more informed decisions.
2. Generative Design and Topology Optimization:
Generative design techniques, often fueled by AI, will become more prevalent. These tools can create innovative designs by exploring a wide range of possibilities and optimizing for various parameters like weight, strength, and cost. Topology optimization, a subset of generative design, focuses on determining the optimal material distribution within a design to achieve desired performance characteristics.
3. Cloud-Based Collaboration and Computing:
Cloud computing will continue to gain prominence, allowing engineers to collaborate on designs and simulations seamlessly, irrespective of their physical location. Cloud-based solutions provide scalable computing resources for resource-intensive tasks like complex simulations and analyses, making them accessible to a broader range of users.
4. Augmented and Virtual Reality (AR/VR) Integration:
AR and VR technologies will find increased use in mechanical engineering software for design visualization, simulation, and training. Engineers can immerse themselves in virtual environments to assess designs, perform maintenance procedures, and simulate real-world scenarios before physical implementation.
5. Digital Twins and IoT Integration:
Digital twins, virtual replicas of physical systems, will become more sophisticated and interconnected with the Internet of Things (IoT). Mechanical software will allow engineers to create, monitor, and analyze digital twins in real time, enabling predictive maintenance, performance optimization, and data-driven decision-making.
6. Simulation-Driven Design Optimization:
Software tools will place greater emphasis on simulation-driven design optimization. Engineers can conduct iterative simulations to refine designs, assess performance under different conditions, and rapidly iterate to find the most optimal solution.
7. Sustainable Design and Analysis:
With a growing emphasis on sustainability, mechanical software will integrate tools for assessing the environmental impact of designs. This includes evaluating factors like energy consumption, carbon emissions, and material efficiency to support the creation of environmentally friendly products.
8. Additive Manufacturing (3D Printing) Integration:
As additive manufacturing gains traction, mechanical software will evolve to provide specialized tools for designing and optimizing components for 3D printing. This includes capabilities for lattice structures, lightweight, and ensuring printability.
9. Real-Time Data Analytics and Visualization:
Mechanical software will increasingly provide real-time data analytics and visualization capabilities, enabling engineers to monitor and analyze operational data from physical systems. This can lead to better insights into product performance, maintenance needs, and potential improvements.
10. Cross-Disciplinary Integration:
Software tools will continue to break down silos between different engineering disciplines. Integrated platforms will facilitate seamless collaboration between mechanical, electrical, and software engineering teams, enabling the development of holistic and interconnected systems.
As technology advances and industries evolve, these trends are expected to shape the future landscape of mechanical engineering software, empowering engineers to design, simulate, and innovate with even greater efficiency and precision.
As a hobbyist, I highly recommend CADHOBBY IntelliCAD to anyone looking for a CAD software that’s easy to use, yet powerful enough to create complex 3D designs.
Thank you so much for your wonderful articles.
could you please provide me with Top 10 welding and NDT Software Tools for 2024 for workshop and construction site work