What is an Ejector?
An Ejector is a piece of equipment often used to eject gases and vapors or non-condensable from a system to generate a vacuum. Ejectors are used in several industries in numerous ways including chemicals, pharmaceuticals, FMCG, petrochemicals & refineries, etc.
Working Principle of an Ejector
An ejector follows Bernoulli’s Principle i.e. when the kinetic energy of a fluid increases its pressure energy decreases to maintain total energy constant & vice versa. Equation 1 clearly indicates that if velocity increases pressure energy decreases.
P+(1/2)ρV2+ρgh=Constant……….(1)
Where,
- P= Pressure energy
- (ρV2)/2 = Kinetic energy per unit volume
- ρgh = Potential energy per unit volume
- ρ = Density
- V = Velocity
The ejector has a converging section in which velocity increases to convert pressure energy into kinetic energy. This transformation results in a low-pressure region that provides the motive force to draw the process fluid. Then both the fluid is mixed & flows through the diverging section consisting of a diverging nozzle. As it propagates through the diverging section the kinetic energy converts into pressure energy by decreasing its velocity and increasing the pressure. Finally, by re-compressing the mixed fluid it meets the destination pressure.
How vacuum is created in an Ejector?
In the ejector, the velocity of the motive fluid becomes very high as it expands across the converging and diverging nozzles from motive pressure to the operating pressure of process fluid. The expansion of the motive fluid through the motive nozzle causes supersonic velocities at the exit of the nozzle. Velocity coming out from a motive nozzle is 3 to 4 times the Mach number. In the actual scenario, the motive fluid expands to a pressure lower than the suction process fluid pressure. This causes the driving force to draw the suction fluid into the ejector. High-velocity motive steam entrains and mixes with the suction fluid.
Main Parts of an Ejector
There are five main parts of an ejector which are as follows,
STEAM CHEST: This is the part of the ejector where the high-pressure motive fluid is entered into the ejector.
SUCTION CHAMBER: It is a chamber that has proper connections for the process inlet, diffuser section, and motive nozzle.
INLET DIFFUSER: It is a properly shaped introductory section and converging diffuser zone that handles the high velocity of the fluids. In this section, entrainment and mixing of the motive and process fluids occur, and the energy of supersonic velocity is converted to pressure energy.
THROAT SECTION: This section is the transition section where the converging section ends and the diverging section begins. Basically, it is located at the junction of the converging supersonic inlet diffuser and the diverging subsonic outlet diffuser.
OUTLET DIFFUSER: It is a properly shaped diffuser section for accomplishing the conversion of velocity head to pressure head. After passing the fluid through the throat of the diffuser, the velocity becomes essentially subsonic. The outlet of the diffuser section further decreases the fluid velocity to a significant level so as to convert the kinetic energy to pressure energy.
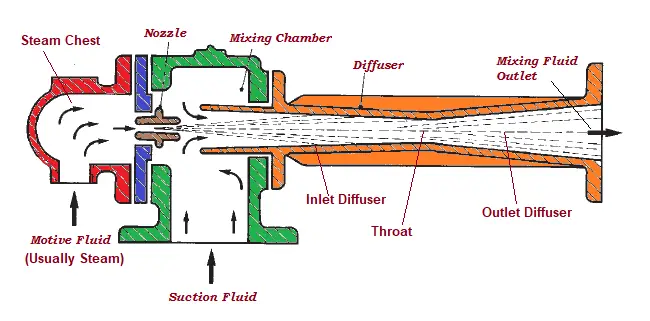
Types of Ejectors
Ejectors are mainly categorized into two types which are as follows,
- Single-Stage ejector
- Multi-Stage ejector
Single-Stage Ejector
Single-stage ejectors are the simplest and most frequently used in industries. They are generally recommended to use for pressures from atmospheric to 80 torrs or for compression ratio <10. A single-stage ejector discharges at or near atmospheric pressure.
Multi-Stage Ejector
A multi-stage ejector is normally used when a generation of high vacuum is required that is normally from the atmosphere to in the range of 30 torrs to 0.05 torr. For the generation of such low pressure, up to six stages of the ejector can be used.
What is Motive Fluid?
Motive fluid is the fluid that motivates the process fluid to draw into the ejector. Normally, high-pressure steam is used as a motive fluid, but compressed air or gas can also be used as the motive fluid. The choice depends on the availability of the utility, operational feasibility, etc. A minimum pressure of the motive fluid is required to maintain a stable operation & thereby to design a stable ejector system. If the pressure of the motive fluid falls below the design pressure, then the nozzle will pass less steam than required. If it happens, the ejector is not provided with sufficient energy to compress the process fluid to the design discharge pressure. A similar problem occurs when the supply temperature of motive fluid rises above its design value, which results in increased specific volume, and consequently, less steam passes through the motive nozzle.
What is a Gas Ejector?
A gas ejector is an ejector which utilizes high-pressure gas as a motive fluid. The motive gas can be compressed natural gas, nitrogen, air, etc. Normally gas ejector has three connecting points high-pressure gas, low-pressure gas & discharge. This type of ejector is used to draw flare gas & routed it to flare.
What is a Steam Ejector?
Steam ejector is the ejector which utilizes high-pressure steam as the motive fluid. It has a converging and diverging nozzle across which pressurized motive fluid is passed. In the diffuser section, the velocity of the mixed fluid is recovered to pressure energy greater than suction pressure but it is lower than the inlet pressure of the motive steam. This pressure should be greater or equal to the backing pressure for smooth operation. For low vacuum, multiple-stage ejectors are used. Table 1 shows the probable suction pressure vs total steam consumption in an ejector.
No. of stage | Operating suction pressure (Torr) | Total Steam consumption per kg of air pumped (kg) |
1 | 200-100 | 4-8 |
2 | 60-400 | 15-20 |
3 | 20-5 | 18-25 |
4 | 3-0.5 | 20-100 |
The steam jet ejector capacity is directly proportional to the weight of the motive fluid. Motive gas to process gas pumped is high, especially under low vacuum, and results in the huge requirement of steam in multi-stage systems. Operating parameter of motive steam such as inlet steam pressure, and discharge pressure has a significant impact on overall ejector performance.
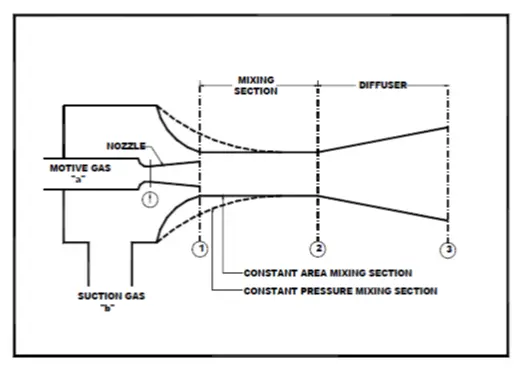
Purpose of Inter-condenser
Inter-stage condensers & ejectors are staged in series with each other. The purpose of the inter-condenser is to condense hydrocarbon & steam as much as possible. The load of the downstream ejector can be reduced by condensing steam & hydrocarbon. So for proper maintaining of motive steam consumption condenser is highly recommended.
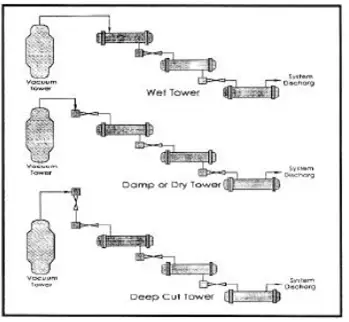
Factors affecting the performance of the steam ejector
The following factors have a significant impact on the performance of the ejector’s performance
- Motive steam
- Cooling water
- Dry & saturated air
- Gas & vapor densities
Motive steam:
A steam ejector is normally designed for a motive steam pressure of 15 to 600 PSIG. Motive steam pressure must be above a minimum pressure for stable operation. This minimum pressure is called motive steam pick-up pressure. So it is very much essential to maintain motive steam pressure; otherwise, the ejector cannot give the desired performance. On the other side, excess motive steam pressure can lead to the wastage of costly steam. Steam ejectors are operated normally with saturated dry steam or superheated steam. 5–15 °C superheating is recommended, but its effect should be considered during ejector design. The use of wet steam is not at all desirable, as it erodes the ejector nozzle and interferes with the ejector performance by clogging the nozzle with droplets of water. The design pressure of the motive steam should be selected as the lowest expected pressure at the steam nozzle of the ejector. The recommended design pressure of the steam is the expected minimum pressure at the motive nozzle: 10 psi.
Cooling Water:
In the inter-condenser, the temperature of the cooling water has a significant impact on the efficiency of the ejector. If the temperature of cooling water rises more than the design condition available LMTD of the condenser decreases. In this situation, the condenser will not condense properly and vapor & non-condensable gases are carried out as saturated fluids.
On the other hand, if the flow rate of the cooling water decreases below the design condition, a huge temperature rise across the condenser occurs. Even if cooling water is at its designed inlet temperature, an increase in temperature rise reduces available LMTD across condensers. Thus the efficiency of condensation is greatly reduced, and additional load is passed on to the downstream stage of the ejector.
Dry and saturated air
If an ejector is used for maintaining a vacuum in the condenser, the air that is extracted by the ejector is saturated with water vapor. The entrained water vapor by the dry air that leaks into the condenser depends upon the temperature of the mixture and the vacuum at the ejector suction.
Gas and vapor densities
When an ejector handles chemical gases or vapors, it is necessary that the density of the gas be known. The compression of a given weight of heavy gas requires less operating steam than the same weight of light gas e.g., one pound of air is more easily handled by an ejector than one pound of water vapor.
What is the maximum discharge pressure of an ejector?
The maximum discharge pressure (MDP) is the highest discharge pressure that an ejector can achieve with the given amount of motive steam fluid passing through the motive nozzle. If the discharge pressure of an ejector exceeds the MDP, it will become unstable and break the operation. If this occurs, an abrupt increase in suction pressure happens. Since increasing the discharge pressure more than the MDP causes a loss of performance, it seems rational that reducing the discharge pressure below the MDP should have the opposite impact. If the compression ratio (discharge pressure to suction pressure) of the ejector is higher than 2:1 then it is called a critical ejector.
Calculation of flow rate of motive steam requirement:
The flow rate of motive fluid is a very crucial parameter for the ejector operation. It can be calculated by the following method. Other than this, it can be calculated in ASPEN Hysys software as well as by graphical method.
The following equation has been developed by the Heat Exchanger Institute,
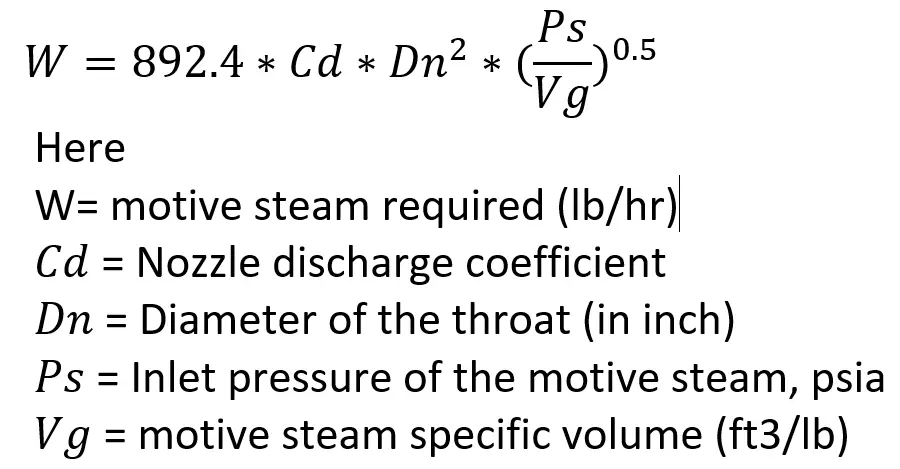
Ejector Datasheet
The below figure (Fig. 5) shows a sample datasheet of an ejector.
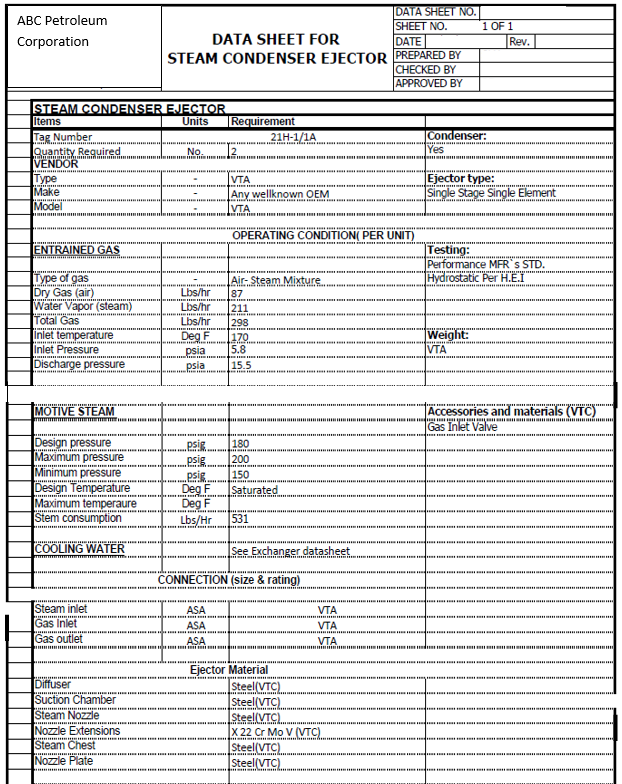
Eductor vs Ejector: Differences between an Eductor and an Ejector
The terms educator and ejector are used interchangeably. Their working philosophy is similar, and both of them work based on Bernoulli’s principle. However, some engineers believe there is a slight difference between the eductor and the ejector. The difference between eductor and ejector is mentioned in the table (Table-2) below:
Eductor | Ejector |
The main objective of an eductor is to take the volume of any fluid out of the system by maintaining a system pressure upstream. | The main objective of an ejector is to maintain a system vacuum upstream. |
Eductors usually have a high compression ratio as compared to ejectors. | Ejectors simply suck the excess volume of fluid to maintain system pressure. The compression ratio is low. |
The diameter of the eductor throat is larger than that of ejectors. | The ejector throat diameter is smaller. |
The main function of the eductor is compression. | The main function of the ejector is vacuum creation. |
In general, the motive fluid of the eductor is liquid. | The motive fluid of ejectors is usually gas (Steam or Air). |
The operation of eductor is generally silent. | Noisy operation. |
Eductors operate at lower velocities. | Ejectors operate at higher velocities. |
The motive fluid nozzle for eductors is a converging type. | The motive fluid nozzle for ejectors is a converging-diverging type. |
I need excelsheet for ejector design.
Can u give us real example for ejector design ?
Can you give us excel sample of ejector design
How to download as pdf
Excellent Article, Excellent Blog , Excellent Site ✅✅✅