Check valves are essential components in fluid control systems. They play a crucial role in preventing the reverse flow of fluids within pipelines or piping systems. Check valves are popular as non-return valves or one-way valves. This comprehensive guide aims to provide a deep understanding of check valves, covering their types, working principles, applications, design considerations, maintenance, and common questions related to these vital components.
What is a Check Valve?
A Check valve is a mechanical device used in piping and pipeline systems to prevent back-flow. Check valves allow fluid flow only in the forward direction that’s why it is called a one-way valve or non-return valve. They work on the principle of differential pressure. It means the check valve will only open if the upstream pressure is more than the downstream pressure. In situations, where downstream pressure is more, the valve will close preventing reverse flow. Closure can also be accomplished by the weight of the check mechanism, by a spring, or by a combination of all these means. Check valves are commonly used in a wide range of industries and applications to ensure the safety, efficiency, and integrity of fluid systems. One of the main applications of check valves is at the pump outlet piping to protect the equipment from flow reversal.
Check valves are automatic valves and unlike other valves, human intervention or external control is not required for their opening or closing. The only purpose of the check valve is to prevent flow reversal or back-flow and they are available in various sizes, designs, and materials.
Working Principle of Check Valves
As already stated, a check valve operates on the principle of differential pressure. For a check valve to open, it must attain a minimum upstream pressure known as cracking pressure. Depending on the check valve design and size, the cracking pressure changes. When the upstream pressure reaches the cracking pressure, the valve opens allowing the fluid to enter. When the upstream pressure falls below the cracking pressure, back pressure is generated, and the flow attempts to move from the outlet to the inlet. At this point, the check valve closes, and the flow halts. The closing mechanism of a check valve varies depending on the design and type of the valve. Spring or Gravity pressure normally assists the closing process.
As the check valve works only in one direction, manufacturers provide an arrow on the valve body indicating the flow direction.
Types of Check Valves
Depending on the movement of the closure member, various types of check valves are available.
- Swing Check Valve
- Wafer Check Valve
- Spring Loaded Check Valves
- Spring Loaded Inline Valves
- Spring Loaded Y
- Ball Check Valves
- Diaphragm check valves
- Lift check valve
- Stop check valve
- Foot Valve
- Duckbill Valve
- Dual Plate Check Valve
Swing Check Valve
A swing check valve is the most common and widely used check valve. The closing member or the disc swings on a hinge or shaft. To allow the flow, the disc swings off the seat and swings back onto the seat to block the reverse flow. In an open position, a swing check valve offers very little resistance to the flow. To achieve optimum performance, often a lever and weight or a lever and spring are mounted. The disc weight and the return flow have an impact on the shut-off characteristics of the valve.
An improved version of swing check valves is known as Tilting Disc Check Valves. It uses a disc that tilts on a hinge to allow or block flow. This design offers improved sealing performance compared to swing check valves and is often used in high-pressure or high-velocity applications.
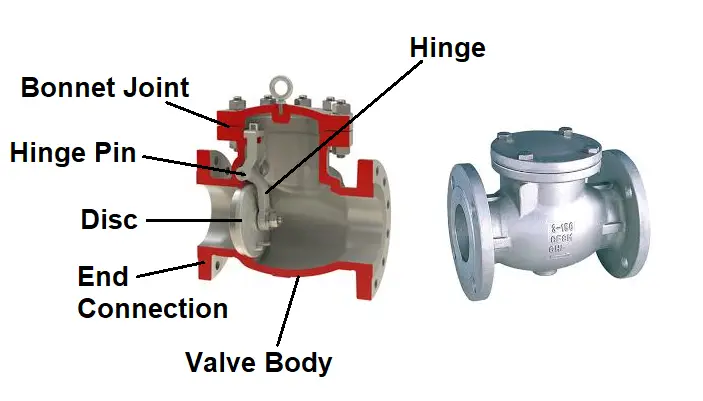
The swing check valve allows full, unobstructed flow and automatically closes once pressure decreases. The following animation video explains the main parts and working methodology of a typical Swing Check Valve
Wafer Check Valve
Wafer check valves are very slim and compact in design and use a swinging disc to allow or block flow. They are lightweight and suitable for various applications. They are economical and are available in various sizes. The following figure shows the typical working of a Wafer Check Valve.
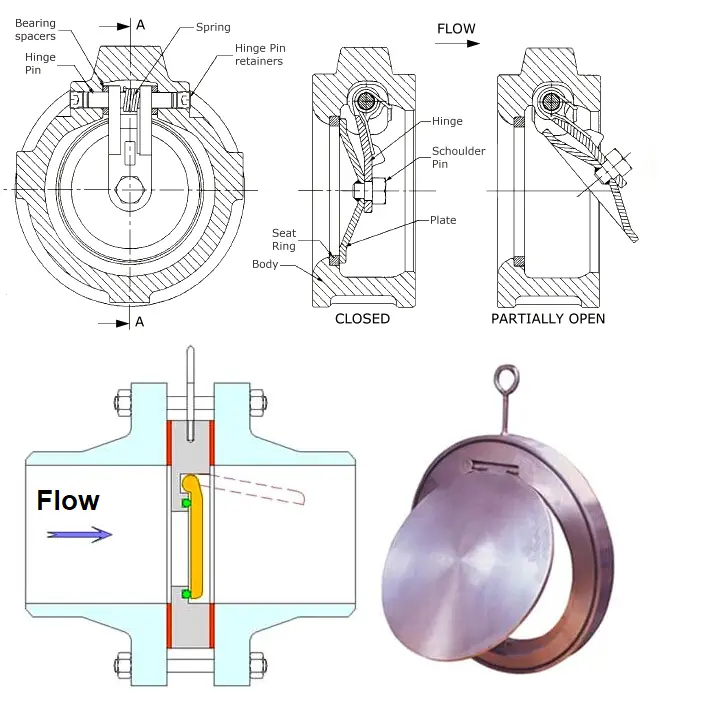
Wafer check valves are ideal for services requiring low-pressure loss as the valve operation takes place at a very low-pressure difference.
Spring Loaded Check Valves
There are two types of Spring spring-loaded check Valves; Spring-Loaded in-line valves and spring-loaded Y-valves.
In-line valves are also known as Nozzle Check Valves or Silent Check Valves. These valves employ a centrally guided stem-disc assembly along with a compression spring. To open the valve, the flow pressure must be more than the spring force and cracking pressure. In that case, the flow pushes the disc allowing the flow. When the inlet pressure reduces, the spring pushes the disc against the orifice and shuts the valve.
The operating principle of Spring-loaded y-check valves is similar to in-line check valves. The only difference is that the spring and movable disc are located at an angle to form a ‘y’ shape. The main advantage of Y-type check valves is that they can be inspected and serviced while the valve is still connected to the system.
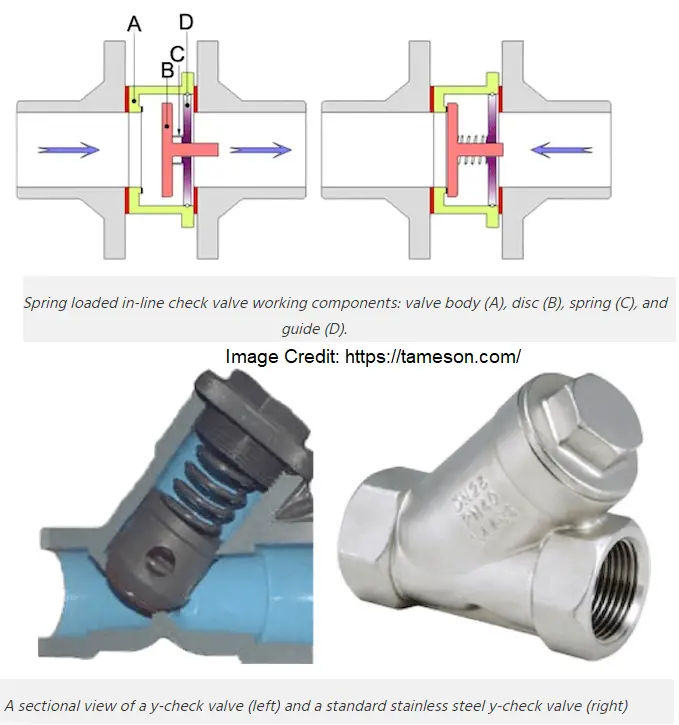
Ball Check Valves
Ball check valves are simple in operation and commonly used on small pumps and in low-head systems. Ball check valves involve a spring-loaded or free-floating spherical ball clapper to shut at pressures below the cracking pressure. In order to guide the ball into the seat and create a positive seal, the sealing seat is conically tapered. However, these valves can easily wear due to prolonged use and require frequent maintenance. Ball check valves are widely used for their simplicity and low pressure drop.
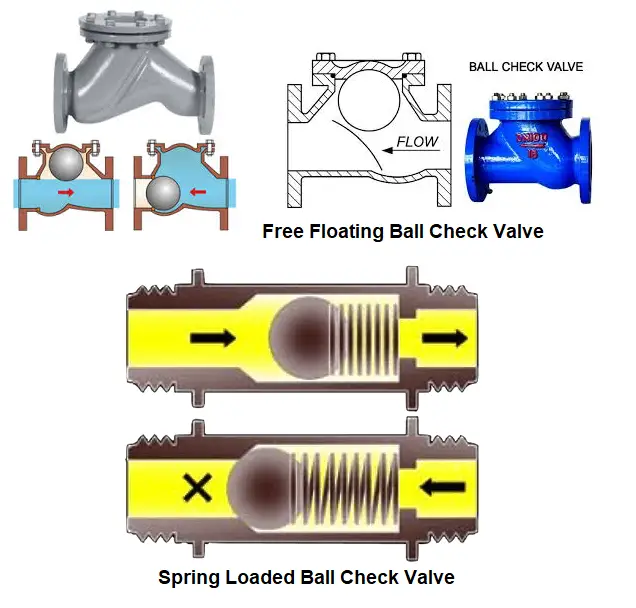
Diaphragm check valves
Diaphragm check valves consist of rubber flexing diaphragms or self-centering discs for preventing backflow. When the inlet pressure is increased, the diaphragm flexes open, and flow starts. There are two types of diaphragm check valves;
- Free-floating Normally Open Valve and
- Fixed Flexing Normally closed Valve.
In the case of normally open diaphragm valves, no cracking pressure is required as the self-centering elastomeric diaphragm is free-floating. However, they need back pressure to close the valve. On the other hand, normally closed valves need a certain inlet pressure to overcome the elasticity of the fixed diaphragm.
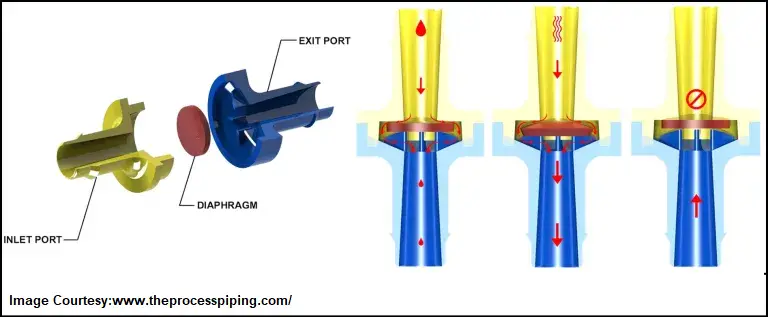
Due to very low cracking pressure, Diaphragm check valves find their use in low-pressure and vacuum applications.
Lift check valve
A lift check valve is also known as a piston check valve. It consists of a guided disc that raises (lifts) up from the valve seat and creates space for media to flow. The inlet pressure must be more than the cracking pressure to overcome gravity and/or a spring force. The valve will close when the inlet pressure decreases below the cracking pressure or there is back pressure.
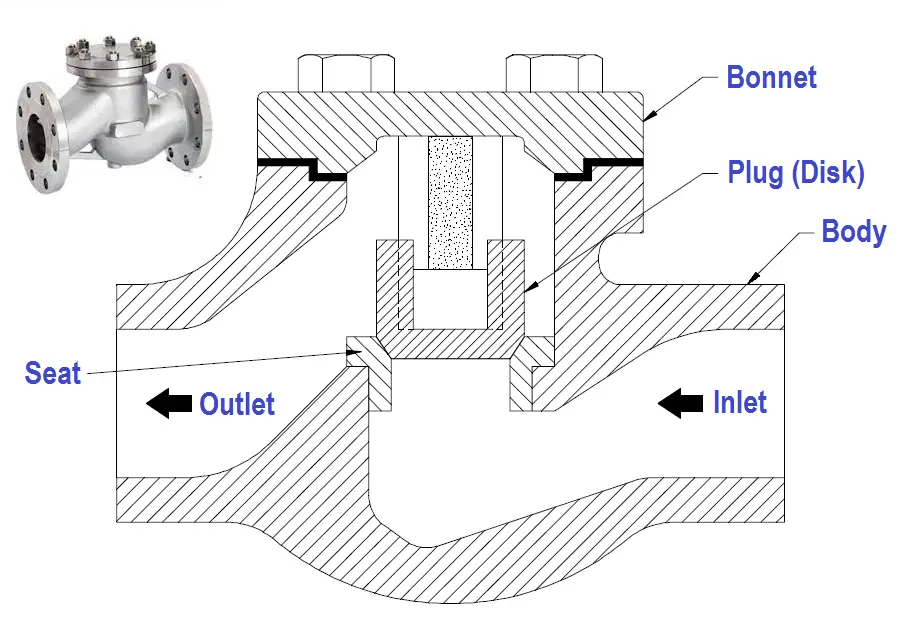
Stop check valve
A stop-check valve is basically, two valves built into one body. It can act as a globe valve for isolation or regulation purposes. Again, It can act as a check valve to prevent backflow. Contrary to other check valves, the Stop check valve has an additional external control mechanism in a perpendicular or angular direction. Stop Check valves are popular in steam services like power plants, boiler circulation, steam generators, turbine cooling, and safety systems.
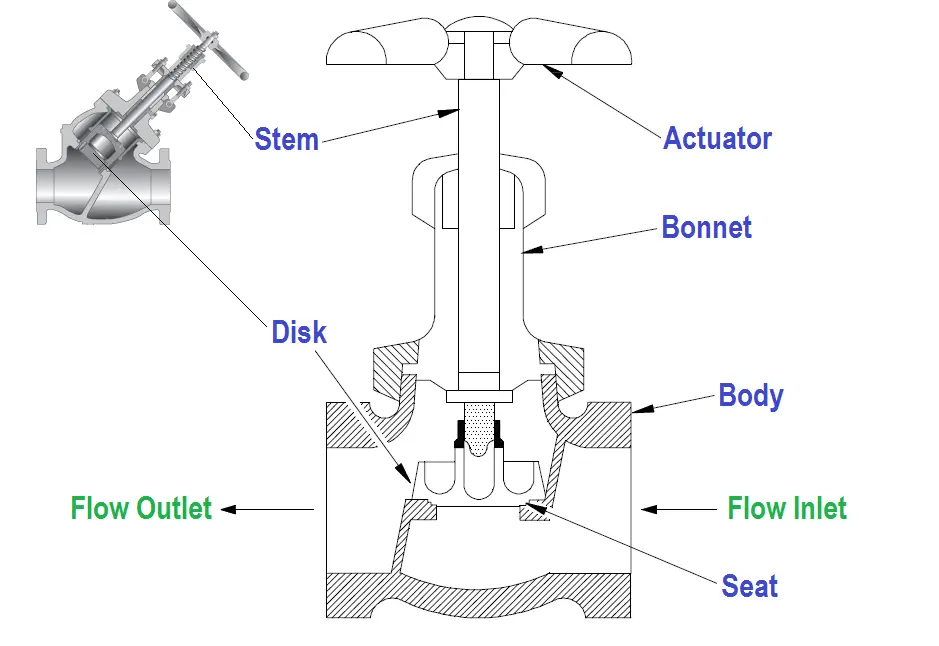
Foot Valve
A foot valve is a check valve that has a strainer installed on the inlet side to prevent debris from entering the valve.
Duckbill Valve
Duckbill Check Valves are unique, one-piece, elastomeric components that enable flow to proceed through a soft tube that feeds into the downstream side of the valve wherein back pressure collapses the tube and cuts off the flow.
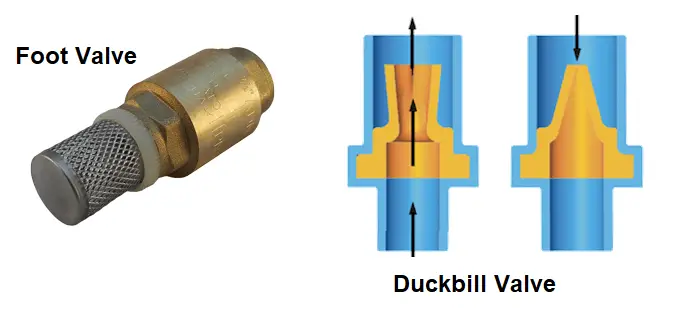
Dual Plate Check Valve
Dual-plate check valves are wafer-type compact valves with a small overall length. They provide excellent hydrodynamic properties that result in very low-pressure losses and they are technically efficient. Their low weight provides advantages during installation, transport, and storage. Dual-plate check valves are suitable for liquid, gas, steam, condensate, water supply, and oil and natural gas services. They are designed as non-slam types. With suitable springs, they can be installed in any position.
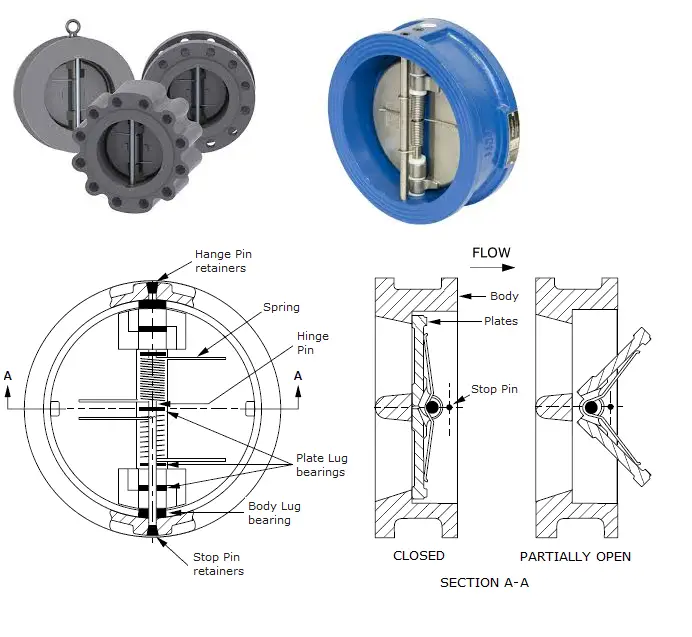
What is Check Valve Slam?
The check valve slamming phenomenon can be described as follows:
- The ideal check valve is one that closes at the moment the fluid being transported reaches “zero” velocity prior to flow reversal.
- But, No check valve is closed at the point of “zero” flow.
- Closure of the valve occurs after flow reversal has taken place.
- The mean velocity of the fluid is backward at the instant of closure.
- The magnitude of the reverse velocity, Vr, causes the phenomenon of “check valve slam”
- Check valves have “dynamic behavior”, ie “speed of response”. Different check valves behave differently.
- Check valves have “Dynamic Characteristics”, ie different speeds of response, which determines the maximum reverse velocity, Vr max, and, hence, the degree of “check valve slam”.
- The quick slamming creates a pressure spike that is a probable cause of the water hammer.
Non-Slam Check Valve
Non-slam check valves are specifically designed valves where the closing member closes without
slamming preventing excess pressure spikes. The disc of a non-slam check valve includes an internal spring opposing the opening fluid flow pressure. When the flow media is strong enough, the spring compresses and the valve opens. Again when the flow decreases, the disc is smoothly pushed back toward the valve seating surface by the spring force and stops. For vertical piping runs or complex applications requiring constant and controllable pressure levels, Non-slam check valves are an ideal solution.
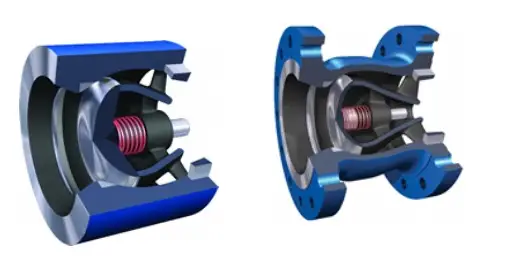
The main advantage of non-slam check valves is their ability to effectively prevent water hammer. Hence, pressure swings, vibrations, and component damages are ideally eliminated. As Non-slam valves have a short
stroke, they facilitate quick soft closing of the disc to prevent water hammer. As they consist of only one moving part, the disc itself, non-slam check valves experience minimal wear over time. However, the non-slam check valves are not piggable.
Desirable Design Characteristics of a check valve
For a check valve to work smoothly the following design characteristics are desirable:
- Moving parts of the valve are of low inertia
- The distance/angle through which the moving element(s) have to travel is minimal and
- Mechanical assistance of closure motion of moving element(s), e.g. spring.
- Tight seal leakage
- Lower pressure loss
Check Valve Symbols | Symbols for Check Valves
Check valve symbols are visual representations used in schematic diagrams to denote the presence and type of check valve. Standardized by organizations like the International Organization for Standardization (ISO) and the American National Standards Institute (ANSI), these symbols ensure consistency and clarity. Below are some common check valve symbols:
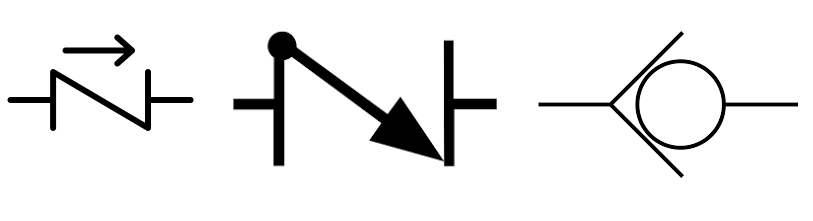
The following figure also shows certain non-return valve symbols that are used in different organizations for different types of check valves.
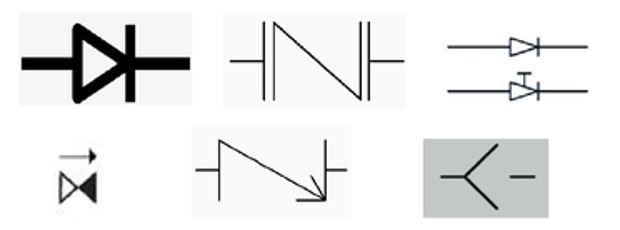
Comparison of Check Valve Symbols for Different Types of Check Valves
Different types of check valves have unique symbols to show how they work. Each symbol highlights the valve’s specific mechanism:
- Swing Check Valves: The symbol has an arc or semicircle to show the swinging motion of the valve disc.
- Lift Check Valves: The symbol includes a perpendicular line or dot to indicate the lifting mechanism that controls the flow.
- Ball Check Valves: The symbol features a ball inside the valve body outline to represent the ball’s movement.
- Diaphragm Check Valves: The symbol has a curved line or diaphragm to show the flexible diaphragm controlling the flow.
- Wafer Check Valves: The compact symbol between two parallel lines shows the valve is placed between flanges.
These symbols help engineers and technicians quickly identify and understand the type of check valve in a system.
Engineering Drawings Where Check Valve Symbols used
All the above check valve symbols are used specifically in the following drawings to represent a specific type of check valve application in the piping system:
- P&ID
- Flow Diagram
- Piping GA Drawings
- Isometric Drawings, etc
Materials of Check Valve
Industrial check valves are available in various materials like
- Carbon Steels
- Stainless Steels
- Duplex Stainless Steel
- High Nickel Alloys
- Titanium
Check valve Standards
The following are the various check valve standards followed during piping design
- API Standards: API Spec 6D, API Std 594
- ASME Standards: ASME B16.34
- AWWA Standards: AWWA C508, AWWA C510
- BSI Standards: BS 1868, BS 1873, BS 2080, BS 5152, BS 5153, BS 5154, BS 5160, BS 5352
- MSS Standards: MSS SP-42, MSS SP-61, MSS SP-71, MSS SP-80, MSS SP-84
Design Considerations for Check Valves
Designing and Selecting the right check valve for a specific application requires careful consideration of various factors:
Material Selection
The choice of materials for check valves is critical to ensure compatibility with the fluid or gas being handled. Common materials include stainless steel, brass, bronze, cast iron, PVC, and various elastomers. The material should also resist corrosion, erosion, and chemical attack.
Sizing and Flow Rate
Proper sizing of check valves is essential to ensure they can handle the required flow rate while maintaining a reasonable pressure drop. Manufacturers provide flow coefficient (Cv) values to help determine the valve’s capacity. Calculating the Cv and understanding the system’s flow requirements are crucial for proper sizing.
Installation Orientation
Check valves typically have a preferred orientation for installation. Installing a check valve in the wrong direction can result in improper functioning and increased wear. Manufacturers provide guidelines on proper installation orientation.
Pressure Ratings
Check valves have pressure ratings that indicate the maximum pressure they can handle safely. It’s essential to choose a valve with a pressure rating suitable for the system’s operating conditions to prevent valve failure.
Maintenance Factors
Consider the maintenance requirements of the chosen check valve type. Some valves may require periodic inspection, cleaning, or replacement of seals and seats. Understanding these maintenance needs can help ensure the longevity of the valve and the reliability of the system.
Applications of Check valves
Check valves are used in various industries like Offshore Oil and gas Production, Onshore Oil and gas Production, Gas Plant, LNG, Liquid Gases, Refineries, Petrochemical, Chemical, Fertilizer, Terminals, Pipelines, Power, Desalination, Water, marine, HVAC, Pharmaceutical, Food Industries, etc. They are widely used in Pump and Compressor discharge, Heat Exchangers, Reactors, Vessels, and Separators to prevent flow reversal. A few typical applications are shown below:
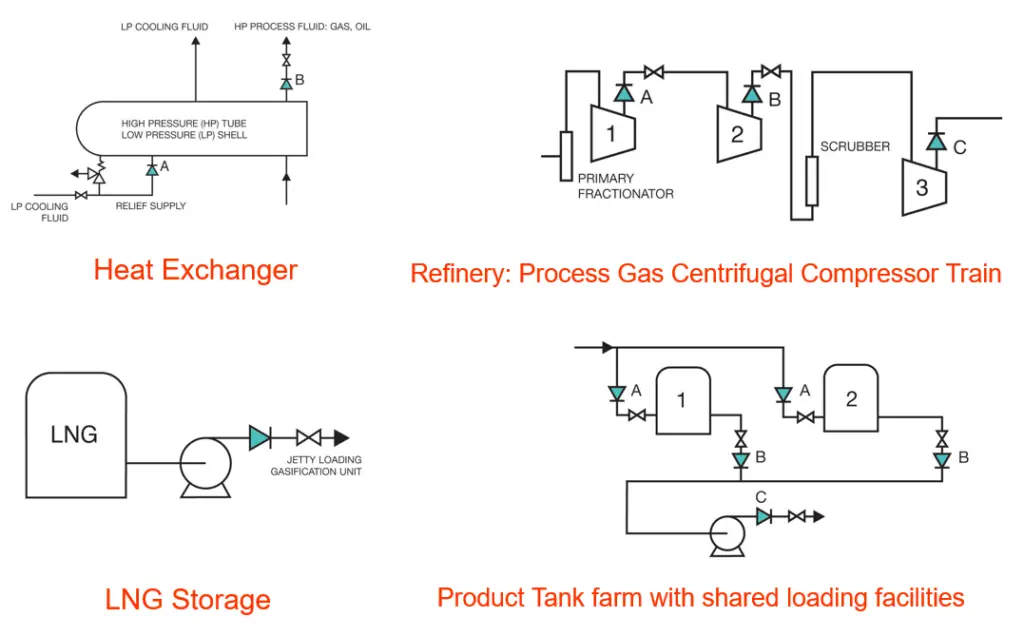
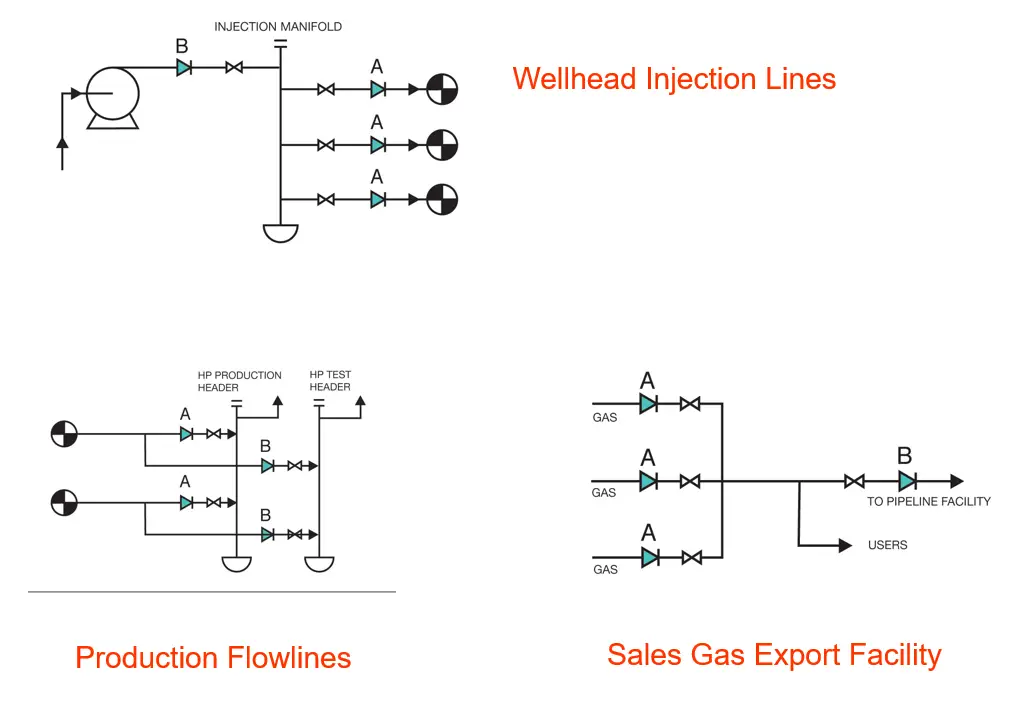
Spring Check Valves vs Swing Check Valves
Swing check valves are highly effective low-cost check valves in the industry. However, there are some basic differences between the swing check valves and the spring check valves.
Spring Check Valves vs Swing Check Valves: Working
In a swing check valve, the flapper ‘swings’ off the seat to allow forward flow. It again swings back onto the seat to stop the flow. On the other hand, a spring-loaded check valve uses a spring to aid in the valve closing.
Swing Check Valves vs Spring Check Valves: Installation Limitation
Swing check valves are only suitable for horizontal flow applications, which greatly limits the orientation of installation. Even though swing check valves provide a larger flow capacity, sometimes they do not fit in existing piping configurations.
On the contrary, spring-loaded check valves are suitable for any flow orientation. So, spring check valves provide more flexibility in difficult spaces with challenging dimensions as compared to swing check valves.
Spring Check Valves vs Swing Check Valves: Minimizing Water Hammer
A spring-loaded check valve has to ability to minimize the damaging effects of a water hammer. In contrast, a swing check valve can amplify the issue.
Let’s understand the concept of a water hammer with an example: Assume in a water line, there is a check valve. Downstream of that check valve, there is a quarter-turn ball valve. Now, during operation, if someone shuts the quarter turn ball valve abruptly, a pressure wave will be generated which will flow through the piping. This phenomenon is known as a water hammer. If the check valve is a swing check valve, the flapper will remain open until that pressure wave returns back to the swing check. The pressure wave causes the flapper to slam shut making an audible sound and causing excessive wear within the swing check valve and other piping system components. However, if a spring-loaded check valve is installed, the spring will close the valve before the pressure wave gets there. So, a spring check valve can effectively reduce the effects of a water hammer. Spring check valves are also known as “silent check valves”. A spring is utilized in the spring check valve to assist the poppet in the silent closing of the check valve prior to fluid flow reversal.
Swing Check Valves vs Spring Check Valves: Cost
As mentioned earlier, Swing check valves are cheaper as compared to Spring check valves.
Click here to learn about various types of Valves
Frequently Asked Questions
1. What is the purpose of a check valve?
The primary purpose of a check valve is to prevent the reverse flow of fluids or gases within a pipeline or system. It ensures that media flows in only one direction, preventing contamination, damage, and inefficiency.
2. How does a swing check valve work?
A swing check valve uses a hinged disc or flap to control flow. When fluid or gas flows in the forward direction, the disc swings open, allowing flow. Reverse flow causes the disc to swing closed, blocking further passage.
3. What are the advantages and disadvantages of ball check valves?
Advantages of ball check valves include their simplicity, low-pressure drop, and suitability for various applications. However, they may not provide a perfect seal and can be sensitive to debris or particulate matter in the fluid.
4. How do you calculate the cracking pressure of a check valve?
The cracking pressure of a check valve is determined by the valve’s design, spring tension (if applicable), and the force required to overcome friction. It can be calculated using the manufacturer’s specifications or testing equipment.
5. Can check valves be used for backflow prevention in a sewage system?
Yes, check valves are commonly used in sewage systems to prevent the reverse flow of wastewater, which can lead to contamination and system damage.
6. What materials are commonly used for check valve construction?
Materials commonly used for check valve construction include stainless steel, brass, bronze, cast iron, PVC, and various elastomers. The choice of material depends on the fluid or gas being handled and the operating conditions.
7. How can I prevent check valve failures in my system?
To prevent check valve failures, ensure proper material selection, sizing, installation orientation, and maintenance. Regular inspection, cleaning, and replacement of worn components can also extend the lifespan of check valves.
I need the documents
Greeting of the day
I am Instrumentation and Automation engineer.
Working with paper industry.
Really wonderful material. Good technical information. Thanks a lot for your technical service.
B. Guru rajan
ISRO
Hello, kindly forward quotations technical specification shipment for each of your valves, look forward for your kind response. Best regards, Lewis Michael
Sir can you provide guidance for mechanical engineer who wants to switch job and come into this industry.
Means exactly what skills should one learn in order to join this industry.
So the question – can you install check valves vertically?
spring-loaded check valves are suitable for any flow orientation.
What is the recommended check valve for a cistern?
How to avoid back flow in the city water line when city water pressure is lower than in the cistern line feeding the house?