A Motor Operated Valve (MOV) is a type of valve that is controlled by an electric motor. The motor rotates a shaft that is connected to the valve, which allows the valve to open or close based on the position of the motor. MOVs are commonly used in industrial and commercial applications to control the flow of fluids, such as water, air, and steam. They can be used to regulate pressure, temperature, and flow rate, and are often used in HVAC systems, power plants, chemical plants, petrochemical plants, and other industrial settings. It is popularly known as MOV valve.
A motor-operated valve (MOV) consists of two different devices; a valve assembly and an electric actuator. This motorized actuator allows for the remote or automated operation of the valve, enabling it to be adjusted to various positions as required by the process. They are sometimes called On-Off valves as the motor serves the purpose of opening and closing. The main applications of motor-operated valves are for flow control and flow isolation purposes.
Working of a Motor Operated Valve
A motor-operated valve (MOV) uses an electric motor to open and close a valve. The motor is connected to the valve stem, which moves the valve’s closure element (such as a ball or gate) to change the flow of fluid through the valve when the motor is activated. The electric motor is controlled by a signal from a controller, which can be a simple switch, a programmable logic controller (PLC), or a more complex process control system. The controller sends a signal to the motor to open or close the valve based on the desired flow rate and the feedback from sensors monitoring the system’s pressure, temperature, and flow rate. Refer to Fig. 1 below which shows the components of an MOV in a motor-operated valve diagram.
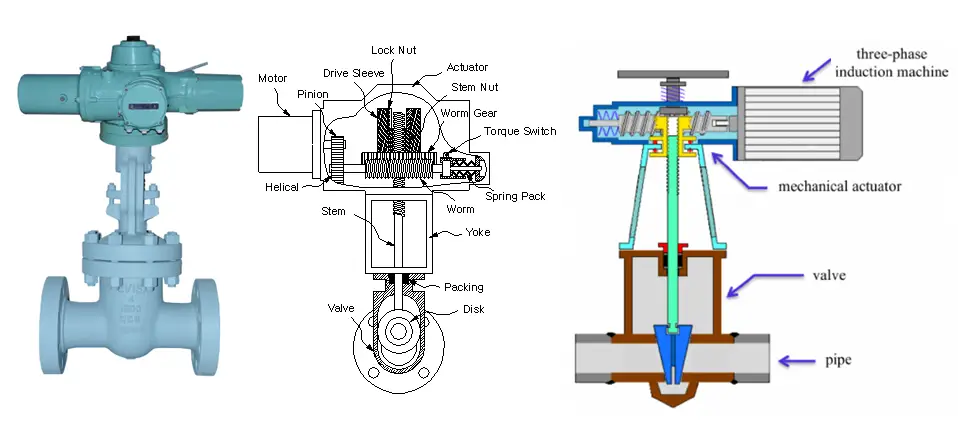
Types of Motor-Operated Valves
Depending on what kind of flow control is achieved by these MOVs, motor-operated valves are classified into three categories:
- Open/Close Valves for normal on-off services
- Inching Valves to have some degree of control, and
- Precision Flow Valves to have precise control
Again, there are several different types of motor-operated valves, including:
- Quarter-turn valves: These valves use a quarter-turn of the valve stem to open and close the valve. Examples include ball valves and butterfly valves.
- Multi-turn valves: These valves use multiple turns of the valve stem to open and close the valve. Examples include globe valves and gate valves.
- Linear valves: These valves use linear motion to open and close the valve. Examples include diaphragm valves and pinch valves.
- Electric valves: These valves are operated by an electric motor and are commonly used in HVAC and other industries.
- Smart valves: These valves are equipped with additional features such as sensors, communication capabilities, and self-diagnostic capabilities.
The type of motor-operated valve used depends on the specific application and the fluid being controlled.
Why is the MOV Valve Used?
A motor-operated valve or MOV is commonly used in piping applications for several reasons:
- Remote Operation: MOVs can be operated remotely, which is particularly useful in situations where valves are located in hard-to-reach or hazardous areas. This allows for convenient control from a central location.
- Automation: MOVs are essential for automated systems where valves need to be controlled automatically based on process conditions or schedules. They integrate with control systems and process automation systems to regulate flow, pressure, and temperature without manual intervention.
- Precision Control: Motorized valves provide precise control over flow rates and pressure. They can be adjusted to specific positions with accuracy, which is important for maintaining optimal operating conditions in many industrial processes.
- Safety: In critical applications, such as in chemical or nuclear plants, MOVs help ensure safety by allowing for quick and reliable shutdowns or adjustments in response to alarms or process changes.
- Reduced Labor: By automating valve operations, MOVs reduce the need for manual valve adjustments, thereby saving time and reducing labor costs. This also minimizes the potential for human error.
- Integration with SCADA Systems: MOVs can be integrated with Supervisory Control and Data Acquisition (SCADA) systems or other monitoring systems, allowing for real-time monitoring and control of valve positions and the overall process.
- Consistent Performance: Motor-operated valves provide consistent performance compared to manual valves, as they are not subject to the variability of human operation and can maintain precise settings over time.
So basically, MOVs enhance efficiency, control, safety, and automation in piping systems, making them a valuable component in many industrial and commercial applications.
Applications of Motor Operated Valves
Motor-operated valves (MOVs) are used in a wide variety of industrial and commercial applications, including:
- HVAC systems: MOVs are used to control the flow of air, water, and steam in heating, ventilation, and air conditioning systems.
- Power plants: MOVs are used to control the flow of water and steam in power generation systems.
- Process control: MOVs are used in various industrial processes to control the flow of liquids and gases, such as in the oil and gas, chemical, and food and beverage industries.
- Water treatment: MOVs are used to control the flow of water in municipal and industrial water treatment systems.
- Fire protection: MOVs are used to control the flow of water in fire suppression systems.
- Mining: MOVs are used to control the flow of liquids and gases in mining operations.
- Pharmaceuticals: MOVs are used to control the flow of liquids and gases in the production of pharmaceuticals.
- Automation: MOVs are used in automation systems to control the movement of machine parts and other equipment.
In general, MOVs are used wherever flow control is required and where manual operation is not practical or feasible.
Difference between Air Operated Valve and Motor Operated Valve
Air-operated valves (AOVs) and motor-operated valves (MOVs) are both types of actuated valves, which means they are controlled by an external power source rather than a manual operator. However, there are some key differences between the two:
- Power source: AOVs are powered by compressed air, while MOVs are powered by electricity.
- Speed of operation: AOVs can open and close more quickly than MOVs because compressed air is more responsive than an electric motor.
- Size and weight: AOVs tend to be smaller and lighter than MOVs because they don’t require an electric motor.
- Cost: AOVs are generally less expensive than MOVs because they don’t require the additional components, such as the electric motor and control system, that MOVs do.
- Maintenance: AOVs require regular maintenance to ensure that the compressed air supply is clean and dry. MOVs require less maintenance, but the electric motor and control system may need to be serviced.
- Safety: AOVs are generally considered safer as they don’t require electricity, while MOVs require a power supply, and electrical safety precautions need to be taken.
The choice between AOVs and MOVs will depend on the specific application, the environment, the cost, and the safety requirements.
Typical Datasheet for a Motor-Operated Valve
A typical datasheet for a motor-operated valve (MOV) will contain the following information:
- Valve type and size: The type of valve (e.g. ball valve, butterfly valve, globe valve) and the size of the valve (e.g. 3″ NPT) will be specified.
- Valve body material: The material of the valve body, trim, seat, sealing, etc. will be listed.
- Pressure and temperature ratings: The maximum pressure and temperature that the valve can handle will be specified.
- Flow characteristics: The valve’s flow characteristics, such as Cv (flow coefficient) or Kv (flow factor), will be provided.
- Actuator type and size: The type of electric actuator (e.g. rotary, linear) and the size of the actuator (e.g. 24V DC, 110V AC) will be specified.
- Control signal: The type of control signal required to operate the valve, such as 4-20mA, 0-10V, or 24V DC will be specified.
- Power consumption: The power consumption of the valve will be specified.
- Ambient and fluid temperature range: The range of temperatures within which the valve can be used will be specified.
- Enclosure protection level: The level of protection provided by the valve’s enclosure against external elements such as dust, moisture, etc.
- Certifications: Any relevant certifications such as UL, CE, ATEX, etc. will be listed.
- Dimensions and weight: The overall dimensions and weight of the valve will be provided.
- Valve End Connections: Valve end connections like ASME B16.5 (FF, RF, RTJ, Threaded), ASME B16.47 Series A or B, MSS SP-44, and ASME B16.25 (BW, SW, WE) shall be mentioned.
- Other information: Additional information such as recommended spare parts, recommended maintenance schedule, and warranty information may also be included.
The exact information provided in a datasheet may vary depending on the manufacturer and the specific valve model. Fig. 2 below presents a typical process datasheet for motor-operated valves.
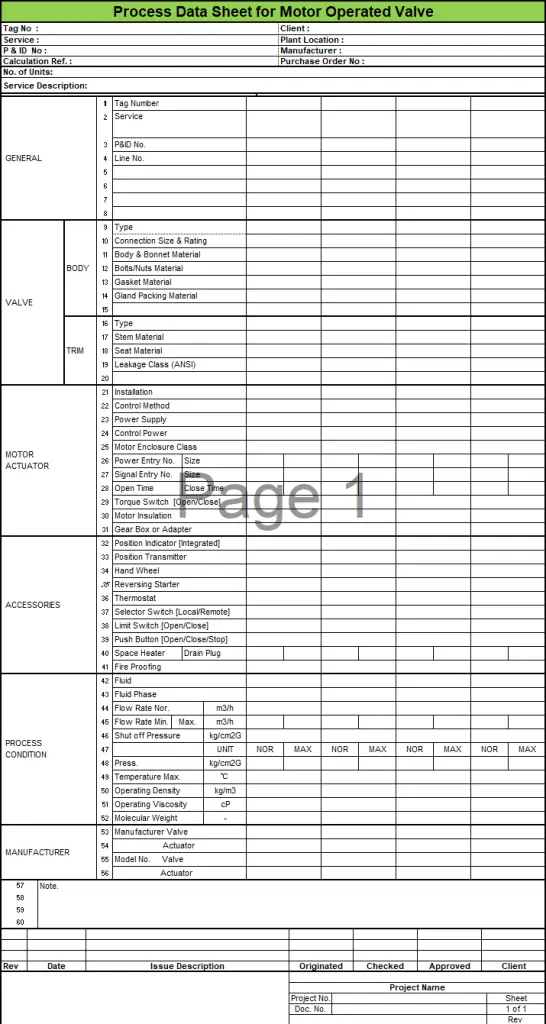
Motor Operated Valve (MOV) Symbols
In a P&ID (Piping and Instrumentation Diagram), MOV stands for “Motor Operated Valve.” It is a symbol used to represent a valve that is controlled by an electric motor. The symbol typically consists of a circle with an “M” inside, and an arrow pointing in the direction of flow. The arrow shows the direction of flow when the valve is open. The circle with an “M” inside represents the electric motor that controls the valve.
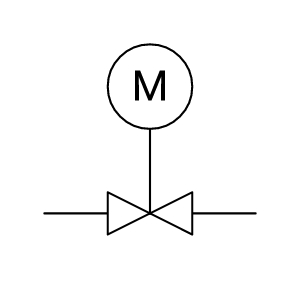
MOVs are used in a variety of industrial processes to control the flow of liquids and gases and are commonly used in HVAC systems, power plants, and other industrial settings. They are used to regulate pressure, temperature, and flow rate. P&ID is a diagrammatic representation of the process, in which all the instruments and components of the process are represented by standard symbols. The P&ID is a fundamental tool used by engineers to understand the process and design the control system.
Difference between a Control Valve and a Motor Operated Valve
A control valve and a motor-operated valve (MOV) are similar in that they both are used to control the flow of fluids in a system. However, there are some key differences between the two.
- Actuation: A control valve typically provides better control than motor-operated valves. Control valves are normally not used for simple on-off services. A MOV, on the other hand, uses an electric motor to open and close the valve.
- Control Response: Control valves usually have a faster response as compared to MOVs.
- Control Elements: The control elements in control valves are usually analog types, whereas MOVs use digital control elements.
- Control valves are used for precision control in closed loops, whereas motorized valves are predominantly used in open loops.
- Type of Control: Control valves can be used for any type of control like pressure control, flow control, temperature control, etc whereas a motorized valve is generally used for flow control.
Overall, control valves are more suited for simple on/off control systems and MOVs are used for more precise flow control in more complex systems. The following table provides the major differences between the two:
Feature | Motor Operated Valve (MOV) | Control Valve |
---|---|---|
Actuation Mechanism | The electric motor drives the valve open or closed | Can be actuated by electric, pneumatic, or hydraulic means |
Control Function | Typically used for open/close or simple on/off control | Used for precise control of flow, pressure, or temperature |
Control Type | On/Off or position control, depending on motor and system | Continuous or modulating control with variable positions |
Applications | Simple applications where precise control is less critical | Applications requiring fine control of process variables |
Integration | Often integrated with simple automation or remote control systems | Integrated with advanced control systems (e.g., SCADA, DCS) for process control |
Feedback Mechanism | May or may not include feedback on the position | Often includes feedback devices like positioners for accurate control |
Valve Types | Available in various types (e.g., ball, butterfly) | Commonly globe valves, butterfly valves, or other types designed for precise control |
Complexity | Generally simpler in design and operation | Typically more complex due to the need for precise control and integration |
Cost | Generally lower, due to simpler operation and control | Generally higher, due to complexity and advanced control capabilities |
Performance | Suitable for applications needing binary (open/close) operations | Designed for applications needing variable control and performance optimization |
Wiring Diagram of a Motor Operated Valve
A wiring diagram for a Motor Operated Valve (MOV) shows how the electrical connections are made between the valve’s motor, control system, and other components. Here’s a simplified overview of a typical MOV wiring diagram:
Basic Components in the Wiring Diagram:
- MOV Motor: The actuator that drives the valve open or closed.
- Power Supply: Provides electrical power to the MOV motor.
- Control Switch: Allows manual or automated control of the MOV.
- Control System: Includes components like PLCs (Programmable Logic Controllers), SCADA systems, or other process control systems.
- Limit Switches: Sensors that detect the valve’s open or closed position and provide feedback.
- Feedback Signals: Electrical signals that provide real-time data on the valve’s position to the control system.
Fig. 4 below shows a typical example of a MOV wiring diagram:
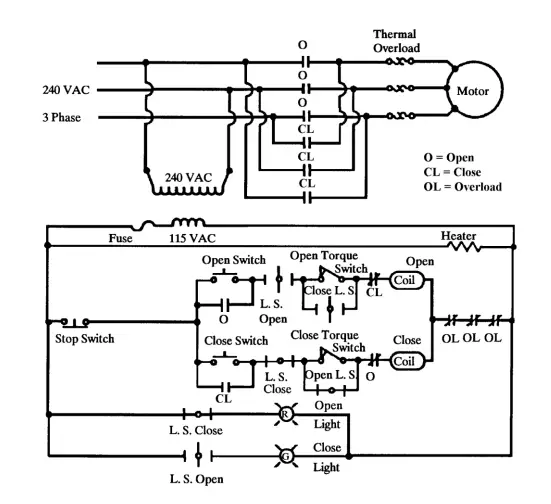
For further learning about the MOV wiring diagram, you can visit the MOV wiring diagram course by clicking here.
Motor Operated Valve Manufacturers
There are many manufacturers of motor-operated valves (MOVs) around the world. Some of the more well-known manufacturers include:
- Emerson: A global technology and engineering company that offers a wide range of MOVs for various industries and applications.
- Flowserve: A provider of flow control products and services that offer a variety of MOVs for the oil and gas, chemical, and power generation industries.
- Rotork: A UK-based company that designs and manufactures MOVs for a variety of industries and applications.
- Auma: A German manufacturer of electric actuators and MOVs for a wide range of industrial applications.
- Honeywell: A multinational conglomerate that offers a range of MOVs for various industries and applications.
- Biffi: An Italian company that designs and manufactures MOVs for a wide range of industrial applications.
- Festo: A German manufacturer that offers a range of pneumatic and electric actuators and MOVs for various industries and applications.
- Neles: a global provider of flow control solutions for the oil and gas, chemical, and other process industries.
These are some of the major manufacturers, but there are many other companies that also produce MOVs for various industries and applications.
Differences between ROV and MOV
ROVs (Remote Operated Valves) and MOVs (Motor Operated Valves) are both types of valves used in industrial applications, but they serve different functions and have distinct features. Here are the key differences between them:
Feature | Remote Operated Valve (ROV) | Motor Operated Valve (MOV) |
---|---|---|
Actuation Mechanism | ROVs can use hydraulic, pneumatic, or electric actuators | MOVs use an electric motor to drive the valve |
Control Method | ROVs are operated remotely via control panels or systems | MOVs are controlled by electric signals integrated into automation systems |
Integration | Remote control capability, less sophisticated automation | Often integrated into advanced automation and control systems (e.g., SCADA, DCS) |
Applications | Offshore platforms, underwater installations, hazardous environments | Water treatment, chemical processing, HVAC systems, and other industrial applications |
Feedback and Monitoring | Feedback mechanisms may be less advanced or optional | Often includes real-time feedback and monitoring systems for precise control |
Automation | Can be manually controlled remotely; automation varies | Typically used in automated systems with precise, programmable control |
Safety | Designed for remote operation in hazardous or difficult-to-access areas | Provides consistent control and can include safety features for automated systems |
Valve Types | Various valve types depending on the actuator used | Available in both quarter-turn (e.g., ball, butterfly) and linear (e.g., gate, globe) configurations |
Operational Complexity | The operation of ROVs may involve simpler or more complex control systems depending on the application | The operation of MOVs is often more complex, with integration into broader process control systems |
This table highlights the key differences between ROVs and MOVs, focusing on their mechanisms, control methods, applications, and other relevant features.
Great article. Loved it.
thank you fot the great info
in my plant, we have an MOV (process is gas) there a 1 incg line like a bypass (no valves or blinds) for the MOV.
What is the purpose?
thanks in advanced
Very nice article