Control valves are control devices that are used to manage and control fluid flow, pressure, temperature, or liquid level by varying the flow passage size. In process systems of production wells, oil and gas plants, Chemical and Petrochemical industries, refineries, and power plants, Control valves are frequently used to control or manage any of the process parameters.
The piping systems of industrial, commercial, residential, and other civic facilities carry the lifeblood of modern civilization, like arteries and veins. And the valves in those piping systems serve the functions of allowing, stopping, regulating, and controlling the flow, to fulfill the intended objectives of the system.
Valves are an essential part of any piping system that conveys liquids, gases, vapors, slurries, and mixtures of liquid and gaseous phases of various flow media.
Some valves are self-actuated while others are manually operated or have actuators that are powered with electric motors, pneumatic or hydraulic, or a combination to operate the valve. Valves are manufactured with metals and non-metals.
What is a Control Valve?
The control valve is an automated valve that can make precise adjustments to regulate and monitor any commodity flowing through a piping system. The function of a control valve is to provide throttling control in response to signals from a control system, using an actuator and a positioner. They are considered the ‘‘final control element’’ in an automated and usually very sophisticated ‘‘control loop.’’
A control valve receives the information from various sensors and transmitters in a control loop and processes that data to manage the control of the fluid parameter. The following figure shows a typical control loop for a control valve
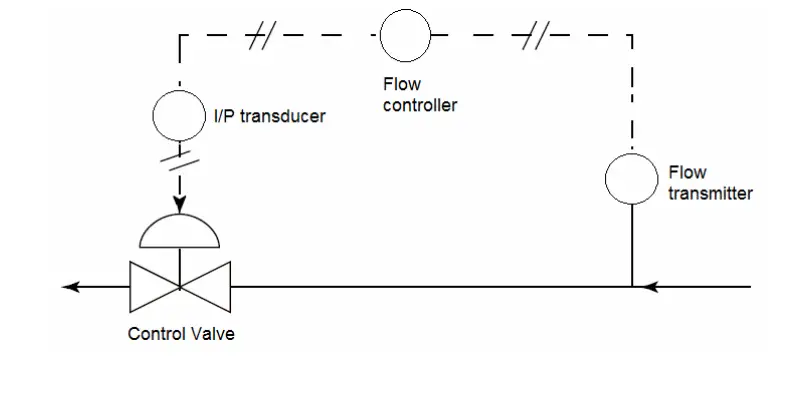
Components of Control Valve
Control valves have basically three interactive components:
- a valve body subassembly (either with a reciprocating or rotating stem),
- an actuating device (usually a spring diaphragm type),
- a valve positioner (an instrument that converts an electronic control signal from a controller, or computer, into an air signal to control the position of the control valve stem), and
- an air set or regulator to supply air pressure to the positioner.
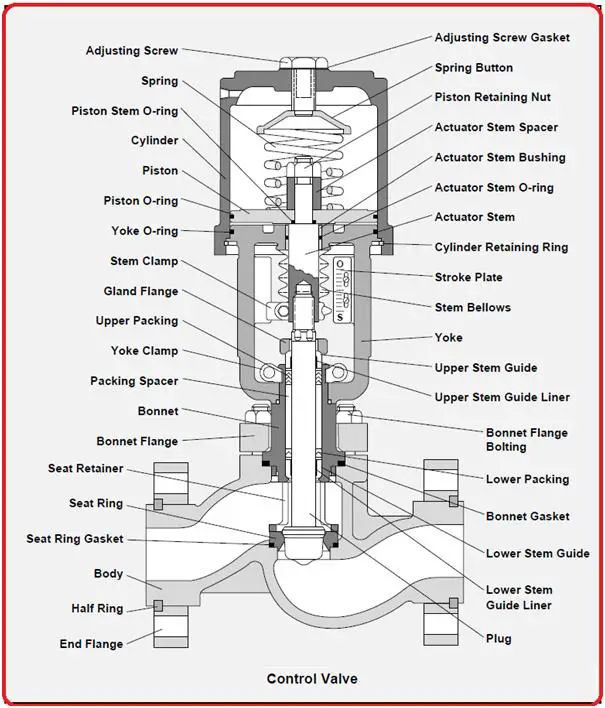
Control Valve Features
The most common valve body style used as a control valve is the globe valve. Although many other body styles such as angle valves, Three-way valves, Eccentric rotary plug valves, semispherical ball valves, Ball Valves, Butterfly valves, etc are used, the globe valve provides the most effective means to regulate and control flow.
Control valves use signals received from instruments positioned throughout the piping system to automatically make adjustments that regulate the commodity within the pipe. Though control valves can perform many functions, they are typically used to control the flow of a commodity within a pipe or to limit its pressure.
Control valves must be arranged within a run of the pipe so that they can be easily operated. To achieve this, control valve manifolds are configured. Control valve manifolds make control valves readily accessible to plant workers.
Control Valve Actuators
The actuator of a control valve is the assembly that provides power for moving the control valve mechanisms. In a control valve loop, actuators move the plug, ball, or vane upon receipt of a signal from the control system to allow or disallow full or partial flow. There are three types of actuators in a Control Valve. They are
- Pneumatic Actuators
- Electric Actuators and
- Hydraulic Actuators
Pneumatic Actuators:
Pneumatic Actuators are the most basic and widely used control valve actuators that use an air or gas signal from an external source to produce a modulating control action. The top port sends the pneumatic signal to the actuator that exerts pressure on the diaphragm plate to move the valve stem. On loss of driver power, pneumatic actuators provide a fail-safe response.
Electric Actuators:
Electric Actuators of a control valve are motor-driven devices. A motor rotates when an electrical signal is received. A gear reduction drive converts this rotating motion into a linear motion to drive the control valve stem for flow modulation. They are used for On-OFF applications in isolation services and for continuous positioning control.
Hydraulic Actuators:
Control Valve Hydraulic actuators use hydraulic oil as the signal fluid. When the force required to move the valve stem is high, hydraulic actuators are used. Due to the non-compressibility of the liquid they exhibit stable positioning.
Specifying Control Valve
The first step in specifying a control valve is to define its function in the given application. In some, it will operate as an on-off valve that opens or closes following the commands of a programmable controller on, say, a batch process. In others, it will be used to remotely set a flow rate in a process—that is, it will be used as a manually controlled variable orifice in a pipe (an open-loop application).
Finally, in more sophisticated applications, the control valve will serve as the final control element in a process control loop and respond to the sometimes infinitely small variations of a signal coming from a controller (typically a computer). The signal will be generated in response to a deviation in the desired temperature, pressure, or level of a process fluid as measured by a transmitter.
More than 90 percent of all control valves use pneumatic actuating devices—either spring-opposed diaphragm types or piston-actuated.
Materials for Control Valves
For noncorrosive use, the material of choice is carbon steel (ASTM A216 Grade WCB, if cast; and A105 when forged). For mild, corrosive applications, valve housings are made from type CF8M (316 stainless steel). However, Teflon-lined housings and exotic alloys, such as Hastelloy, Monel, or Titanium are available for highly corrosive fluids.
Characteristics of different valves to serve as Control Valve
Control Valves play a major role in the everyday effort to increase process plant profitability and conserve energy. Proper selection of these valves can have a significant financial impact on the overall cost of a project and how well the process can be controlled. To narrow down the choices, the engineer must understand how the general characteristics of each type of valve match up with the design requirements. Refer to table 1 for the general characteristics of a few valve types.
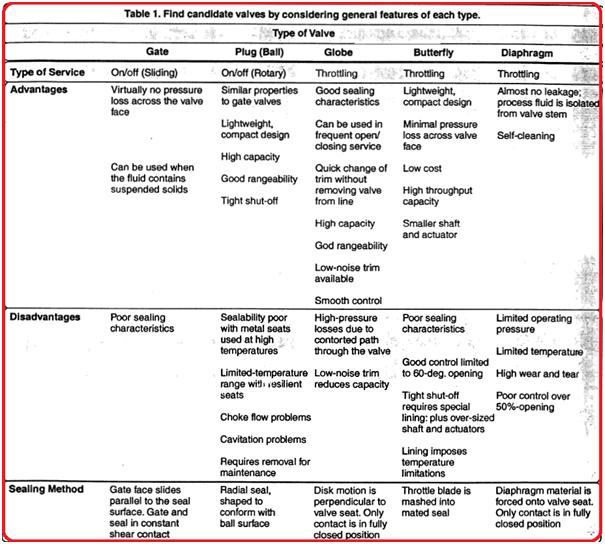
Control Valve Characteristics
Each control valve has a flow characteristic, which describes the relationship between the flow rate and the control valve travel. As a valve opens, the flow characteristic, which is inherent to the design of the selected valve, allows a certain amount of flow through the valve at a particular percentage of the stroke. This enables flow regulation through the control valve in a predictable manner. The three most common types of control valve flow characteristics are:
- Linear
- Equal percentage
- Quick opening
Control Valve Selection
There are two major parameters on which the control valve selection is dependent-
- Service condition and
- Load characteristics
Other parameters that determine the control valve selection are
- Ability to control the flow rate;
- Lack of turbulence or resistance to flow when fully open – turbulence reduces head pressure;
- Quick opening and closing mechanism – rapid response is many times needed in an emergency or for safety;
- Tight shut-off – prevents leaks against high pressure;
- Ability to allow flow in one direction only – prevents return;
- Opening at a pre-set pressure – procedure control to prevent equipment damage; and
- Ability to handle abrasive fluids – hardened material prevents rapid wear.
Control Valve Types
Depending on various parameters control valves are classified as follows:
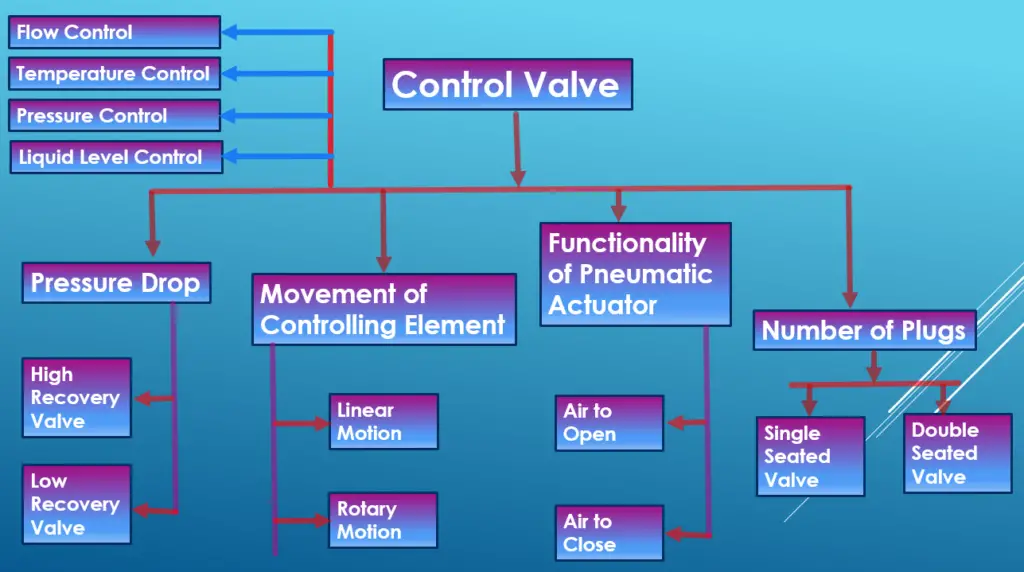
Pressure Control Valve
Pressure Control valves help in controlling system pressure within a limit. They are installed in all systems where pressure fluctuations can occur and can cause a hazard if not controlled. Pressure control valves are basically closed valves with a restriction for pressure control. There are two mechanisms on which pressure control valves operate:
- Direct-Acting Valve and
- Pilot Operated valve.
Relief valves, reducing valves, etc are examples of pressure control valves.
Control Valve Symbols
The symbols used for different types of control valves in P&ID are as given below:
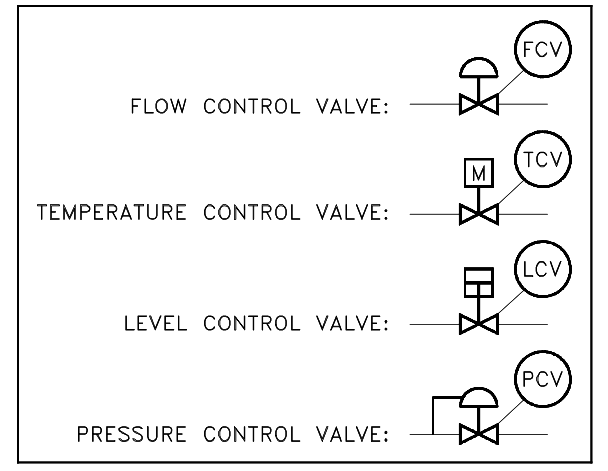
How to install a Control Valve?
Control valves are normally installed in a horizontal orientation in a straight pipe run preferably away from elbows. The actuator is kept in a vertical position. A bypass valve is installed for continuous operation during control valve inspection and maintenance. Upstream and downstream isolation valves and drains are added to the piping system to isolate the control valve for maintenance. The following figure shows a typical control valve installed in a piping system.
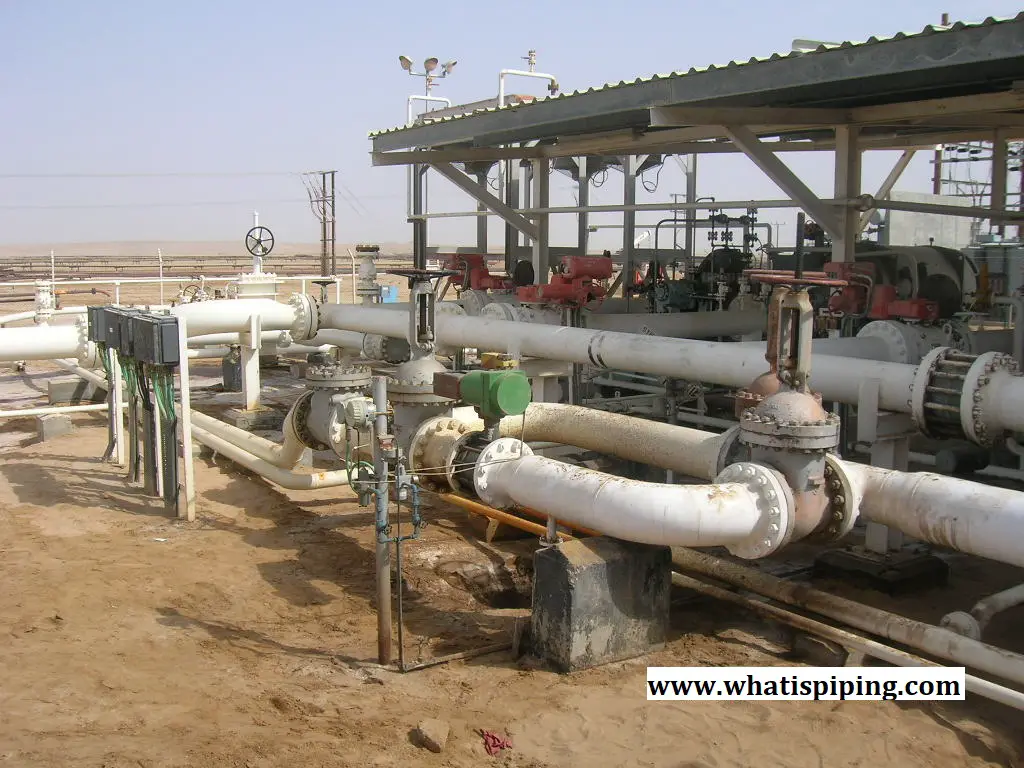
Control valve sealing classification
The sealing quality of a metal seated control valve is very important. Normally, The higher the pressure class of the valve, the lower the allowable leakage rate in a closed position.
Control Valve Assembly
The control valve assembly is used for controlling process parameters in piping systems. The following figures show typical different arrangements of control valve assemblies
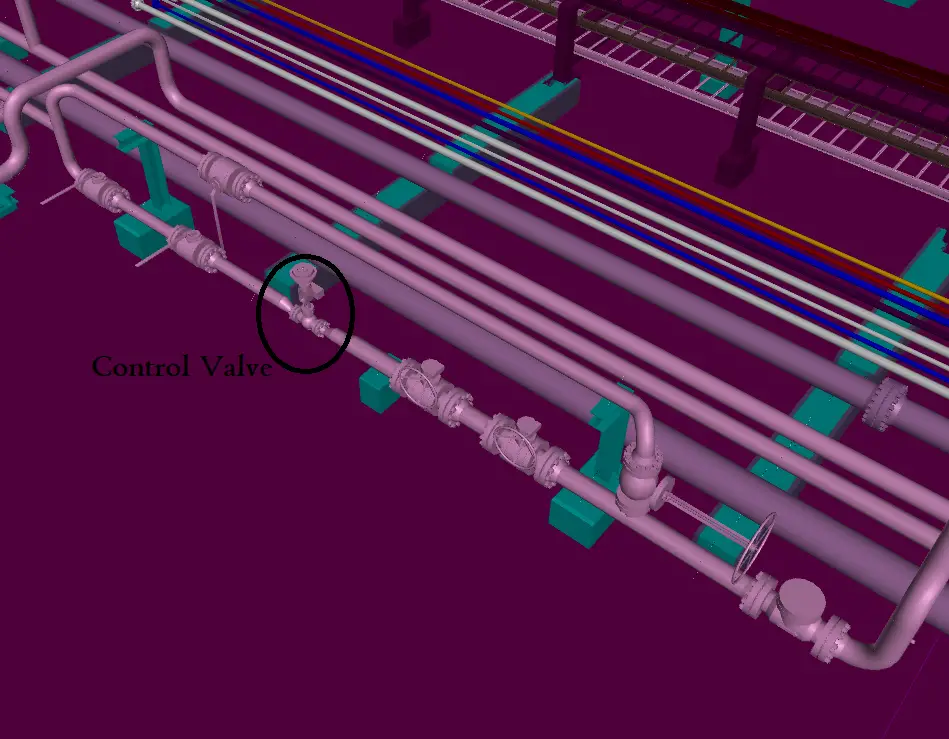
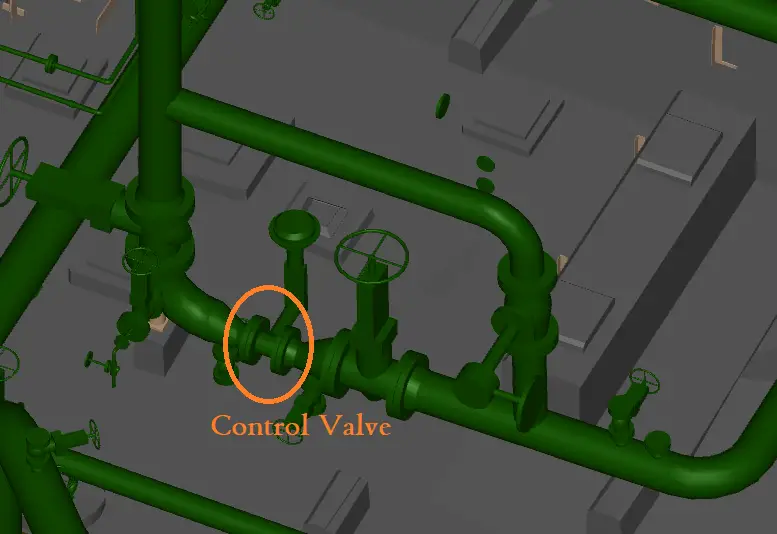
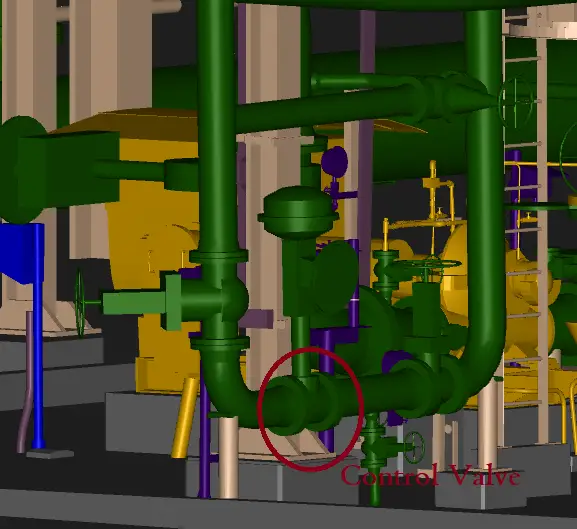
The following videos will explain more details about control valves and their working methodology:
Control Valve Basics
The following video briefly describes the basics of Industrial Control Valves.
Flow control valves
Flow control valves are devices that manage the rate of fluid flow in part of a hydraulic circuit. The following video tutorial explains the basics of flow control valves
Few more Resources for you…
Details about control valves
Ball Valve Design Features: A Literature
A brief article on Valve Inspection & Testing
An article on ROTARY SELECTOR VALVE (RSV) and MULTIPHASE FLOW METER (MPFM)
Selection of Valves: A Few Guidelines
Great information
I am a start up instrumentation engineer this information is more useful to me
Nice information, keep it up.
great information
Good content for learning.
Thanks. Please continue to post such learning items.
Thanks a lot for posting such informative article. Please continue.
Hi Anup Sir,
For power projects why control valve are of butt welded ends instead of flanged face end. and also there is no bypass valve given in my previous power project, in this case how the maintenance of control valve will be done?
And also please make a blog page dedicated to butt weld end valves use and control valve philosophy without provided by pass line with valve.
Thanks
Thanks for your fine information
Very Significant details of Control valve explained in simple language.
Great Information.
Significant details explained about control valve.
great info.
valuable information, thank you.
Fantastic article…Thanks for sharing such an amazing content with us.Good job.Keep it up.