Liquefied Natural Gas (LNG) is a natural gas that has been cooled to a temperature of -162°C (-260°F) at atmospheric pressure, which results in the gas transforming into a liquid state. This process, called liquefaction, reduces the volume of natural gas by about 600 times, making it easier and more economical to transport and store.
LNG is primarily composed of methane, which is the main component of natural gas. It is produced by cooling natural gas to its boiling point, which causes it to condense into a liquid. The resulting LNG is clear, odorless, non-corrosive, and non-toxic.
LNG is typically stored in insulated tanks and transported in special carriers, such as LNG ships or tanker trucks. It can be used as a fuel for power generation, heating, and transportation, or as a feedstock for producing chemicals and other products.
Due to its high energy density and low environmental impact, LNG is becoming an increasingly popular alternative to other fossil fuels, such as coal and oil. It is also considered a bridge fuel toward a low-carbon future, as it can help reduce greenhouse gas emissions compared to other fossil fuels.
Liquefied Natural Gas or LNG is natural gas with the primary element as methane. The Liquefied Natural Gas is converted to liquid form for ease of transport and storage. While in liquid form, Liquified Natural Gas takes up around 1/600th of the volume of its gaseous form. So, LNG can easily be transported in liquid form in locations where natural gas transportation through pipelines is not feasible. Special tankers carry this liquefied natural gas to the terminals where the LNG is returned to the gaseous phase and distributed through pipelines.
Characteristics of Liquefied Natural Gas
Liquefied natural gas or LNG is colorless, odorless, non-toxic, and non-corrosive. The main characteristics of liquefied natural gas are
- It is a cryogenic liquid so must be handled using special materials and technologies.
- LNG is stored in special containers.
- It is a fossil fuel created by organic deposited materials.
- The boiling point of LNG is typically -162 Deg. C
- The density of liquefied natural gas varies between 430 Kg/m3 to 470 Kg/m3.
- At ambient conditions, LNG will convert to vapor form.
- LNG is non-flammable.
- Liquefied Natural Gas has a very hot flame temperature means it rapidly burns and creates huge heat because its heat of combustion is 50.2 MJ/kg.
- It is hazardous if not contained properly.
- LNG is a very good source of energy.
Uses of Liquefied Natural Gas
LNG or liquefied natural gas is used widely for the following applications.
- To generate electricity or power.
- Used as fuel for industrial and commercial boilers.
- for heating water and buildings, to cook in residential applications.
- For Road transport as LNG vehicles
- For sea transport in ships, ferries, etc
- Used as fuels for furnaces, fluid bed dryers
- As marine fuel
Origin of Natural Gas
Natural gas exists in nature under pressure in rock reservoirs in the Earth’s crust, either in conjunction with and dissolved in heavier hydrocarbons and water or by itself. It is produced from the reservoir similarly to or in conjunction with crude oil.
Natural gas has been formed by the degradation of organic matter accumulated in the past millions of years. Two main mechanisms (biogenic and thermogenic) are responsible for this degradation. Natural gas produced from geological formations comes in a wide array of compositions. The varieties of gas compositions can be broadly categorized into three distinct groups:
- Non-associated gas – it occurs in conventional gas fields
- Associated gas – it occurs in conventional oil fields, and
- Unconventional natural gas.
Unconventional gas
It occurs outside of the former two. The most common types of unconventional gas are:
- Tight gas – natural gas produced from reservoir rocks with such low permeability that massive hydraulic fracturing is necessary to produce the well at economic rates;
- Coalbed methane – methane adsorbed into the solid matrix of the coal;
- Natural gas from geo-pressurized aquifers;
- Gas hydrates – methane clathrate is a solid clathrate compound in which a large amount of methane is trapped within a crystal structure of water, forming a solid similar to ice;
- Deep gas
Composition of Natural Gas
Natural gas is a complex mixture of hydrocarbon and non-hydrocarbon constituents and exists as a gas under atmospheric conditions.
Raw natural gas typically consists primarily of methane (CH4), the shortest and lightest hydrocarbon molecule. It also contains varying amounts of:
- Heavier gaseous hydrocarbons: ethane (C2H6), propane (C3H8), normal butane (n-C4H10), iso-butane (i-C4H10), pentanes, and even higher molecular weight hydrocarbons.
- Acid gases: carbon dioxide (CO2), hydrogen sulfide (H2S), and mercaptans such as methanethiol (CH3SH) and ethanethiol (C2H5SH).
- Other gases: nitrogen (N2) and helium(He).
- Water: water vapor and liquid.
- Liquid hydrocarbons: crude oil and/or gas condensates.
- Mercury: only trace amounts.
Refer to the table in Figure 1 for a typical composition of Natural gas.
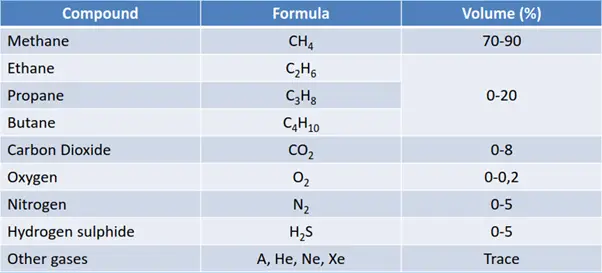
LNG Process
Naturally, liquefaction is advantageous as it can be transported or stored in a greater quantity. The LNG Process is the process of liquefaction. The process of cooling the gaseous LNG to -259°F or -162°C for transforming it into liquid is known as the LNG Process. The process is actually a chain of methods, hence popularly known as LNG Process Chain.
Natural Gas – Exploration to End-User
Fig. 2 below shows the flow chart for Liquefied natural gas exploration.
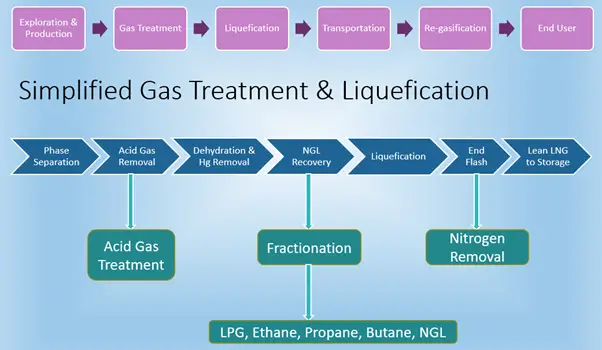
LNG Plant
An LNG plant refines the crude natural gas received from deep within the earth and condenses it into a pure, concentrated, efficient, liquid form of energy. Three basic processing steps are performed in the LNG plant. These are:
- Purification of the extracted natural gas by removing dust, acid gases (CO2), helium, water, and heavy hydrocarbons.
- Liquefaction by condensing and cooling it to approximately −162 °C.
- Transportation of the liquefied natural gas to the consumer by sea or road transport.
Typical processes of a 2-train LNG plant are shown in Fig. 3.
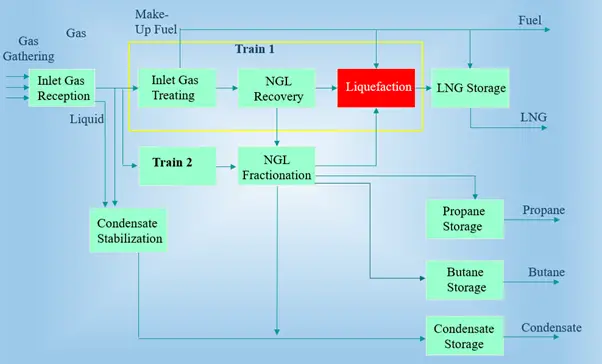
Liquefaction Temperatures of LNG
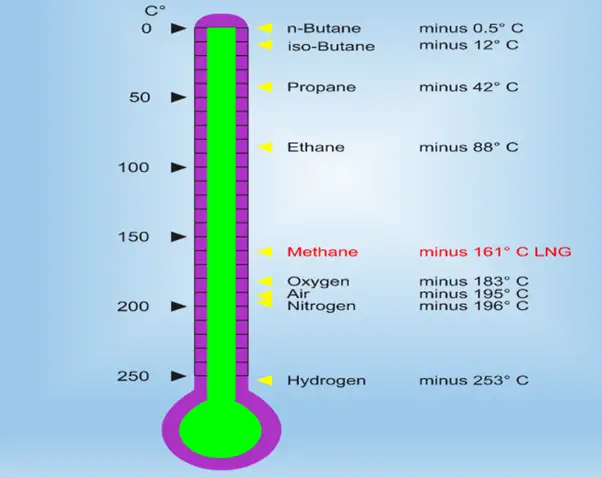
LNG Process Flow
Fig. 5 shows a Schematic of a Simple Refrigeration Cycle (LNG Process Flow)
Natural Gas Liquefaction Techniques
Different LNG Process liquefaction techniques include:
- Single Refrigeration cycle
- Multiple Refrigeration cycles
- Self Refrigerated cycles
- Cascade Processes
- The cooling of natural gas involves the use of refrigerants which could either be pure component refrigerants or mixed component refrigerants.
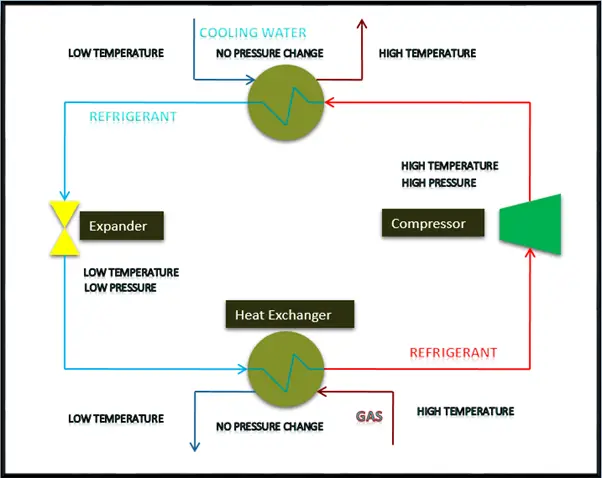
LNG Process Liquefaction Technologies
LNG process liquefaction is performed using various technologies mentioned below:
- CASCADE PROCESS by ConocoPhillips
- C3MR or AP-X by Air Products
- DMR by Shell
- Mixed Fluid Cascade – MFC by Linde
- Liquefin by Axens / Air Liquide
Liquefied Natural Gas by CASCADE Process
- Most Straight Forward of All Processes
- Kenai Plant Continuous Operation 1969
- CoP License, Plant Build by Bechtel.
- The raw gas is first treated to remove typical contaminants.
- Next, the treated gas is chilled, cooled, and condensed to -162 ˚C in succession using propane, ethylene, and methane.
- The last stage is pumping LNG to storage tanks and awaiting shipment.
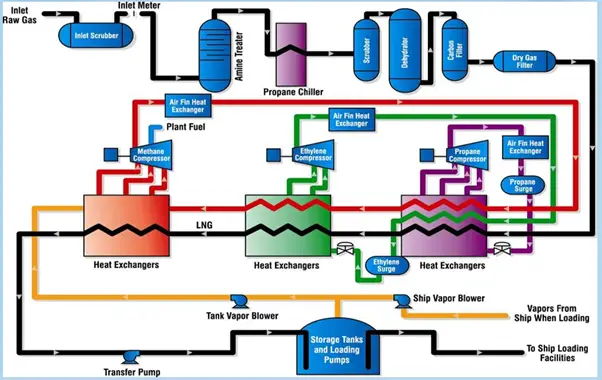
- Pure component Refrigerants
- Specific operating ranges for each component
- Mixed Refrigerants
- Modified to meet specific cooling demands.
- Helps improve the process efficiency
- Mixed refrigerants are mainly composed of hydrocarbons ranging from methane to pentane, Nitrogen, and CO2. Typically, Methane – 25-30%, Ethane – 45-55%, Propane – 15-20%, Nitrogen – 1-5%, and Butane – 1-2%.
Liquefied Natural Gas by Single MR Process
- Significant improvement from Cascade Process
- The use of Coil wound Heat Exchangers & MR refrigerant simplified the process.
- Mixed Refrigerant offered a way to provide the required refrigeration over the temperature range required.
C3MR process of Liquefaction of LNG Process
- Introduction of Propane as Pre-cooling to liquefication
- Improved Efficiency, increased single train capacity
- Reduction in MR refrigerant volumetric flow due to pre-cooling by Propane
- Train size continued to grow with larger drivers & larger compressors
- Liquefication capacity up to 5 MMTPA.
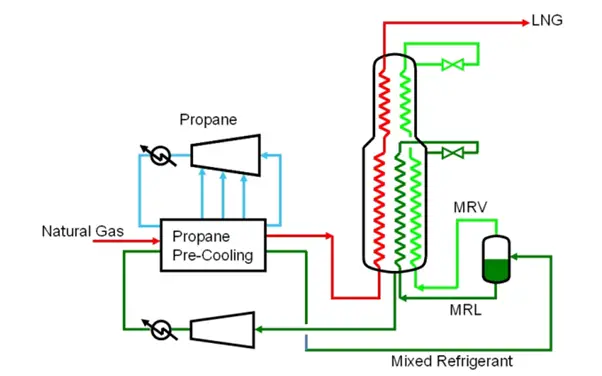
Liquefied Natural Gas by AP-X Hybrid LNG Process
- Improved C3-MR process – pre-cooling by Propane, liquefaction using MR, and sub-cooling using Nitrogen Cycle.
- Nitrogen Cycle has a simple & efficient expander loop.
- Increased capacity by a reduction in volume flow of MR (40%of C3MR) & Propane (20% of C3MR).
- Liquefication capacity up to 8.0 MMTPA.
- Nitrogen Cycle is a simplified version of the cycle employed by Air Products in Air Separation plants.
Why Nitrogen:
- Higher vapor pressure at the required liquefication temperature of Natural Gas
- The relatively smaller volumetric flow rate in low-pressure Nitrogen circuits.
- Improved efficiency by reducing pressure losses
DMR LNG Liquefaction Process
- DMR – Dual Mixed Refrigerant is very similar to C3MR
- The difference is in the utilization of a second pre-cooling refrigerant component.
- The use of two mixed refrigerant cycles allows full utilization of power in a design with two mechanically driven compressors.
- It allows keeping the compressors at their best efficiency point over a very wide range of ambient temperature variations and changes in feed gas composition.
- The natural gas stream is cooled via two stages. The first stage cools natural gas to -50°C while the second column cools natural gas to LNG at -160°C.
Liquefied Natural Gas using Liquefin by Axens (Air Liquide)
- Developed by IFPEN and AXENS, now owned by Air Liquide.
- a highly efficient process and provides the most cost-competitive LNG product per ton.
- is optimized best with the Brazed Aluminium Heat Exchanger, leading to further cost reductions and scalable output.
- Compact and modular design
- Balanced refrigeration power allows for identical refrigerant compressor drivers
- Very cost-effective solution
Codes and Standards for Liquefied Natural Gas
Stringent code and standard guidelines are followed at every step of the LNG process to ensure safety. The primary LNG codes and standards are
- NFPA 59A
- EN1473
- EN 1160
- EN 14620
- EN 1474
- EN 1532
- EN 13645
- 33 CFR Part 127
- API 620
- JGA-107-RPIS
- JGA-108-RPAS
- JGA-102
- JGA-103
- OISD 194
- NFPA 30.
Types of Liquefied Natural Gases
There are two main types of liquefied natural gas (LNG), which are based on the processes used to produce them:
- Associated Gas LNG: This type of LNG is produced as a by-product of oil extraction from oil fields that contain natural gas. When the oil is extracted, the natural gas is separated and liquefied. Associated Gas LNG typically has a higher content of hydrocarbons other than methane, such as ethane and propane, which makes it suitable for use as a feedstock for producing petrochemicals.
- Non-Associated Gas LNG: This type of LNG is produced from natural gas fields that do not have any associated oil. The natural gas is extracted from the fields and processed to remove impurities before being liquefied. Non-Associated Gas LNG typically has a higher methane content than Associated Gas LNG, which makes it suitable for use as a fuel for power generation, heating, and transportation.
Both types of LNG have similar properties and can be used interchangeably, although their specific applications may differ depending on their composition and quality.
LNG pricing
The pricing of Liquefied Natural Gas is not straightforward. In the current LNG contracts, three major pricing systems are prevalent as mentioned below:
- Oil-indexed contract. Primary user countries are Japan, Korea, Taiwan, and China.
- Oil, oil products, and other energy carriers indexed contracts. Specifically used in Continental Europe; and
- Market-indexed contracts. Used mostly in the US and the UK.;
- The equation used for the calculation of an indexed price is as follows:
CP = BP + β X
Here,
- BP: constant part or base price
- β: gradient
- X: indexation
The above-mentioned formula finds its wide use in Asian LNG SPAs. The base price is represented by various non-oil factors but is usually a constant determined by negotiation at a level that can prevent LNG prices from falling below a certain level. It thus varies regardless of oil price fluctuation.
Quality of Liquefied Natural Gas
In the LNG Business, the quality of LNG is one of the most important issues. During trading, any natural gas that does not meet the agreed specifications is termed as “off-specification” or “off-quality” LNG. That’s why the LNG Quality must be regulated. Such regulations serve the following purposes:
- Ensures the distributed gas is non-corrosive and non-toxic.
- Guards against liquid or hydrate formation in the networks.
- Allow interchangeability of the distributed gases by limiting the parameter variation ranges. Such parameters are the content of inert gases, calorific value, Incomplete Combustion Factor, Wobbe index, Soot Index, Yellow Tip Index, etc.
The quality of liquefied natural gas is measured at the delivery point by instruments like gas chromatograph.
Amount of the sulfur and mercury content and the calorific value are the most important gas quality concerns. To ensure the lowest concentration of sulfur and mercury in LNG, the liquefaction process must be accurately refined and tested.
The other concern for LNG is the heating value. In terms of heating value, the natural gas markets can be grouped into three markets as follows:
- Asia (Japan, Korea, Taiwan) with a gross calorific value (GCV) higher than 43 MJ/m3(n), i.e. 1,090 Btu/SCF, known as rich gas distribution.
- the UK and the US, with a GCV usually lower than 42 MJ/m3(n), i.e. 1,065 Btu/SCF, known as lean gas distribution
- Continental Europe with the acceptable GCV range is quite wide: approx. 39 to 46 MJ/m3(n), i.e. 990 to 1,160 Btu/scf.
Sometimes to increase the heating value of liquefied natural gas, propane and butane are injected. In general, the price of lean LNG in terms of energy value is lower as compared to the rich LNG.
LNG Safety
Natural gas is the most environmentally friendly fossil fuel with the lowest CO2 emissions per unit of energy. But, Natural gas, being fuel and a combustible substance, must be handled with care. For the design, construction, and operation of liquefied natural gas facilities, proper measures must be taken to ensure safe and reliable operation.
However, LNG in its liquid form can not ignite and is not explosive. For LNG to burn, it must vaporize first and mix with air in the proper proportions. During leakage, LNG rapidly vaporizes and turns into a gas that easily mixes with the air. In such a case, there is a risk of ignition causing fire and thermal radiation hazards.
What is Floating Liquefied Natural Gas or FLNG?
Floating Liquefied Natural Gas (FLNG) is a technology used to produce, liquefy, store, and transfer LNG at sea. It involves using a specialized vessel that is equipped with liquefaction facilities and can be moored at a natural gas field to produce and process gas in situ.
FLNG technology enables the production of LNG from offshore natural gas fields that are too small or too remote to justify the cost of building onshore liquefaction facilities. It also allows for greater flexibility in LNG production, as the vessel can be moved from one location to another depending on the demand for LNG.
The FLNG vessel typically includes a processing plant, storage tanks, and a liquefaction plant that cools the natural gas to its liquid state. The LNG is then stored in onboard tanks until it can be transferred to LNG carriers for transportation to markets around the world.
The main advantage of FLNG technology is its ability to produce LNG at the source of natural gas, which reduces the need for long-distance pipelines and onshore liquefaction plants. This can result in significant cost savings and reduced environmental impact compared to traditional LNG production methods. However, FLNG technology also has some challenges, including the need for specialized vessels and the potential for safety and environmental risks associated with offshore operations.
Liquefied Natural Gas vs Propane
Liquefied Natural Gas (LNG) and propane are both forms of liquefied gases that can be used as fuels. However, there are some differences between the two:
- Composition: LNG is primarily composed of methane, while propane is a hydrocarbon gas composed of propane molecules.
- Production: LNG is produced by cooling natural gas to its boiling point, while propane is produced as a by-product of natural gas processing and crude oil refining.
- Energy content: LNG has a lower energy content per unit volume than propane, which means that a larger volume of LNG is required to provide the same amount of energy as propane.
- Storage and transportation: LNG is typically stored and transported in insulated tanks at cryogenic temperatures of around -162°C (-260°F), while propane is stored and transported as a liquid under pressure at room temperature.
- Applications: LNG is primarily used as a fuel for power generation, heating, and transportation, while propane is commonly used for heating, cooking, and as a fuel for vehicles and industrial processes.
Both LNG and propane are considered cleaner-burning fuels compared to other fossil fuels like coal and oil, as they produce fewer emissions of pollutants and greenhouse gases. However, the choice of which fuel to use depends on the specific application and availability of the fuel.
Differences Between LPG and LNG
LPG (liquefied petroleum gas) and LNG (liquefied natural gas) are two types of liquefied gases that are commonly used as fuels. Here are some of the key differences between LPG and LNG:
- Composition: LPG is a mixture of propane and butane gases, while LNG is primarily composed of methane.
- Production: LPG is produced as a by-product of natural gas processing and crude oil refining, while LNG is produced by cooling natural gas to its boiling point.
- Energy content: LNG has a lower energy content per unit volume than LPG, which means that a larger volume of LNG is required to provide the same amount of energy as LPG.
- Storage and transportation: LPG is typically stored and transported as a liquid under pressure at room temperature, while LNG is stored and transported in insulated tanks at cryogenic temperatures of around -162°C (-260°F).
- Applications: LPG is commonly used for heating, cooking, and as a fuel for vehicles and industrial processes, while LNG is primarily used as a fuel for power generation, heating, and transportation.
- Availability: LPG is generally more widely available than LNG, as it is produced as a by-product of oil and natural gas extraction and processing. LNG production requires specialized facilities and transportation infrastructure.
Both LPG and LNG are considered cleaner-burning fuels compared to other fossil fuels like coal and oil, as they produce fewer emissions of pollutants and greenhouse gases. The choice of which fuel to use depends on the specific application, availability, and cost of the fuel.
Liquefied Natural Gas Companies
There are many companies involved in the production, transportation, and marketing of liquefied natural gas (LNG). Here are some of the largest and most well-known companies in the LNG industry:
- Royal Dutch Shell: Shell is one of the world’s largest energy companies and is involved in all aspects of the LNG business, from production to transportation and marketing.
- ExxonMobil: ExxonMobil is a global energy company that is involved in LNG production and marketing, as well as the development of LNG infrastructure.
- Chevron: Chevron is a major player in the LNG industry, with interests in LNG production, transportation, and marketing.
- Total: Total is a French multinational energy company that is involved in all aspects of the LNG business, from production to transportation and marketing.
- BP: BP is a global energy company with interests in LNG production and marketing, as well as the development of LNG infrastructure.
- Qatargas: Qatargas is a joint venture between Qatar Petroleum and several major international oil and gas companies, and is one of the largest producers of LNG in the world.
- Cheniere Energy: Cheniere is a US-based energy company that specializes in LNG production and export, and is one of the largest LNG exporters in the world.
- Woodside Energy: Woodside is an Australian energy company that is involved in LNG production and marketing, with a particular focus on the Asia-Pacific region.
- Novatek: Novatek is a Russian energy company that is one of the largest producers of LNG in Russia and is expanding its LNG export capabilities.
This is the best website ever
This is a really great article that explains a lot about LPG&LNG in a simple way, thanks for that.
Can I have a PDF copy if you do not mind? on my email:
hakki.n63@gmail.com
regards