When it comes to the intricate world of industrial systems and processes, piping valves play a pivotal role. These devices regulate the flow of liquids, gases, and even solids, ensuring the smooth operation of countless industries ranging from manufacturing to energy production. In this detailed guide, we will discuss everything that a piping engineer needs to know about piping valves; ranging from valve definition, types, materials, applications, standards, selection, etc.
What is a Piping Valve?
A valve is a mechanical element used in piping systems to start, stop, mix, control, or regulate the flow or pressure of the fluid by modifying the passage through the pipe. Valves are an essential part of any piping system conveying liquids, vapors, slurries, gases, mixtures of liquid, and gaseous phases of various flow media. Valves are the most costly rigid piping components in a plant. They can account for up to 20% to 30% of overall piping item costs for a process plant. The size of a valve is decided by the size of its ends connected to the piping system.
Their primary function is to start, stop, or control the flow rate to maintain desired conditions in various processes. Valves achieve this by opening, closing, or partially obstructing the passage of fluid, which in turn affects pressure, flow rate, and direction.
Common types of valves can be self-actuated or manually operated or have actuators. Actuators of valves can be electric, pneumatic, or hydraulic powered, or a combination to operate the valve. Valves are made of metals and non-metals depending on the application.
Applications of Piping Valves
Piping valves find applications in a wide array of industries, including:
- Oil and Gas: Valves control the flow of crude oil, natural gas, and refined products throughout the extraction, refining, and distribution processes.
- Chemical Processing: Valves regulate the movement of various chemicals and substances in chemical manufacturing.
- Water Treatment: Valves manage the flow of water in treatment plants, distribution networks, and wastewater systems.
- Power Generation: Valves control the flow of steam, water, and other fluids in power plants to generate electricity.
- Pharmaceuticals: Valves play a role in the precise control of fluids in pharmaceutical manufacturing and research.
- Food and Beverage: Valves are used to handle liquids and gases in the production and packaging of food and beverages.
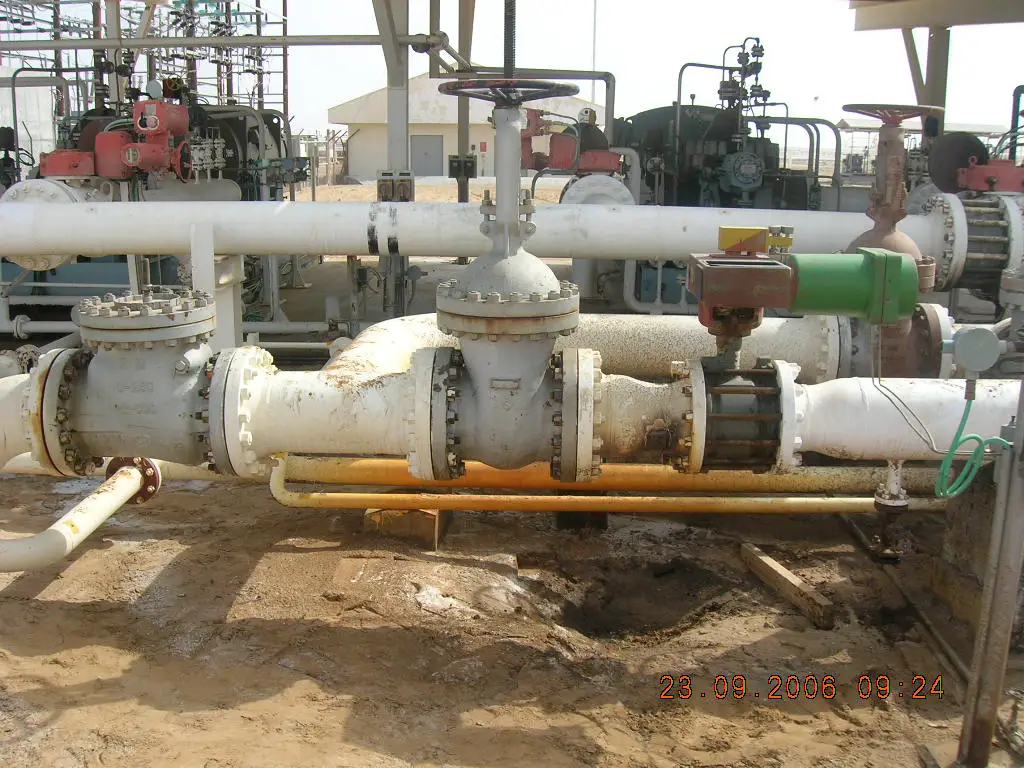
Types of Valves / Valve types
Common types of valves used in piping systems can be classified based on various parameters like
- valve types based on functions
- type of valves based on end connections
- valves based on construction material
- valve types based on actuator operation
- valve types based on the mechanical motion of the closing member
- valves based on pressure-temperature ratings
- types of valves as per port size.
Valve Types Based on Functions
The valve type classification based on functions is shown in Fig. 2.
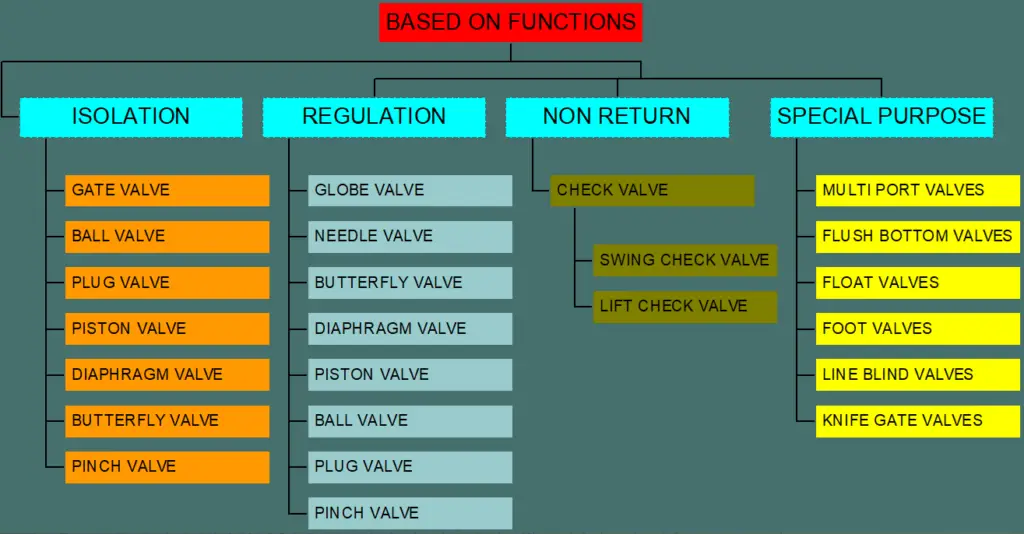
The main function of a valve is
- To start or stop a flow.
- To increase or reduce a flow.
- To control the flow.
- To prevent backflow.
- To relieve a pipe system at a certain pressure to safeguard the system.
- To throttle.
Types of Valves Based on End Connection
Based on the end connection to piping or equipment nozzles, the valves can be classified as follows:
Flanged ends (Normally 2″ and larger valves):
Flanged connections involve using flanges at the ends of the valve and the adjoining piping. Flanges are flat, rimmed disks with holes that are bolted together to create a tight seal. These connections are widely used in industrial applications and are suitable for high-pressure and high-temperature systems. Flanged connections provide easy installation and maintenance but can be bulkier compared to other types.
Butt-welded ends (Class 900 and higher):
Welded connections involve permanently joining the valve to the piping system using welding techniques. This ensures a strong, leak-proof connection and is often used for critical applications where security and integrity are paramount. Welding, however, requires skilled labor and can complicate maintenance and repairs.
Screwed ends (1.5 inch and smaller sizes):
Threaded connections involve screwing the valve onto threaded pipe ends. This connection type is commonly used for smaller valves and low-pressure applications. Threaded connections are relatively simple to assemble, but they might not be as robust for high-pressure systems due to potential leakage issues.
Socket welded ends (2″ and smaller sizes):
Socket weld connections are similar to threaded connections, but instead of threading, the pipe end is inserted into the socket of the valve end. The joint is then welded for a strong, leak-resistant connection. Socket weld connections are used in high-pressure and smaller-sized applications.
Wafer type:
A wafer-type valve connection is a specific type of end connection used for certain types of valves, especially in applications where space and weight considerations are important. Wafer-type connections are commonly used for butterfly valves, check valves, and some other types of valves.
Valve Types Based on the Material of Construction
Based on the construction material, the available valve types are
- Carbon Steel
- Alloy Steel
- Cast Iron
- Bronze
- Stainless Steel
- Ductile Iron
- Nickel Plated Ductile Iron
- Aluminum
- Copper
- Brass
- Silicon Bronze
- Aluminum Bronze
- Lined valves
- Monel
- Stellite
- Hastelloy
- Gunmetal
- Glass
- Special steels
- Non-metals like PP, PVC
Valve Types Depending on the Actuator Operation
Based on operator types, industrial valves are classified as shown in Fig. 3
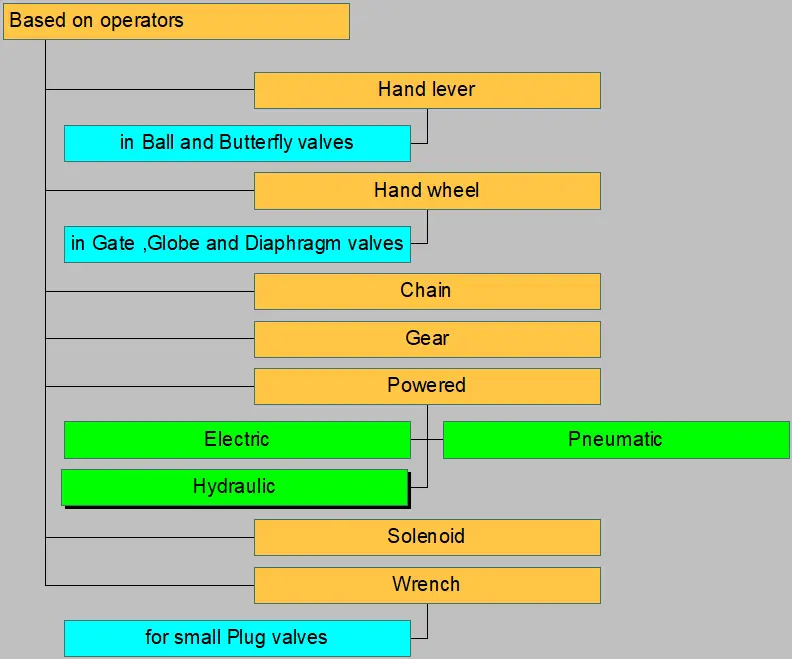
The operator is a device that aids in opening or closing a valve. Various operators available in industrial valves are
Hand lever:
It is used to actuate the stems of a small butterfly, ball, and plug valves. Wrench operation is used for small plug valves.
Hand Wheel:
For the majority of popular smaller valves, Handwheel (Fig. 5) is the most common means of rotating the stem. Normal handwheels can be substituted using a hammer blow or impact handwheels when an easier operation is needed.
Chain-Operated Valves:
It is used where a handwheel would be out of reach. The stem is fitted with a chain wheel or wrench (for lever-operated valves) and the loop of the chain is brought within one meter of the working floor level.
Gear-operated valves:
Gear operators are used for reducing the operating torque. It consists of a hand wheel-operated gear train actuating the valve stem in the case of a manual operator. A thumb rule for gear operator’s consideration is
- valves of 350 mm NB and larger up to 300#,
- valves of 200 mm NB, and larger up to 600#,
- valves of 150 mm NB, and larger up to 1500# and
- valves of 100 mm NB and larger for higher ratings.
Pneumatic and Hydraulic:
In situations where the possibility of flammable vapor is likely, a pneumatic or hydraulic operator is used. They are of the following forms:
- Cylinder with a double-acting piston driven by air, water, oil, or other liquid, which usually actuates the stem directly.
- Air motor, which actuates the stem through gearing. These motors are commonly piston and cylinder radial types.
- A double-acting vane with limited rotary movement in a sector casing, actuating the stem directly.
Electric Geared Motor:
For large valves in remote locations, Electric Geared Motor is used to move the valve stem.
Solenoids:
These can be used for fast-acting check valves, and with on/off valves in light-duty instrumentation applications.
Types of Valves Based on the Mechanical Motion of the Closing Member
The closure members of the valve exhibit various kinds of mechanical motion during operation. Accordingly, valves are grouped as follows:
Linear Motion Valves:
The valves in which the closure member moves in a straight line to allow, control, regulate, stop, or throttle the flow are known as linear motion valves. Gate, globe, diaphragm, pinch, and lift check valves are linear motion valves. Linear valves are of two types: rising stem (multi-turn) and axial. In both valve types, the flow obstructer moves linearly but there are wide differences in construction and operation.
In the case of multi-turn rising stem valves, the obstructer is moved by the rotation of a threaded rod (stem) attached to the obstructer. Typical examples of multi-turn valves are globe valves, gate valves, pinch valves, needle valves, and diaphragm valves which are commonly used for flow control applications.
On the other hand, Axial valves use electromagnetic or pneumatic force to move the flow obstructer along an axis. Coaxial valves, angle seat valves, etc are examples of these types of valves which are typically fast-acting and only used for on/off process applications.
Rotary Motion Valves:
In butterfly, ball, plug, eccentric, and swing check valves, the valve-closure member travels along an angular or circular path. These types of valves are known as rotary motion valves as these valves rely on the rotary motion of the flow obstructer. The rotation is usually limited to one-quarter turn or 90 degrees.
Quarter Turn Valves:
Some rotary motion valves on the other hand require approximately a quarter turn i.e., 00 through 900 of motion of the stem to travel from fully open to a fully closed position or vice versa. Such valves are called quarter-turn valves.
Fig. 4 below shows the common types of valves possessing various kinds of mechanical motion.
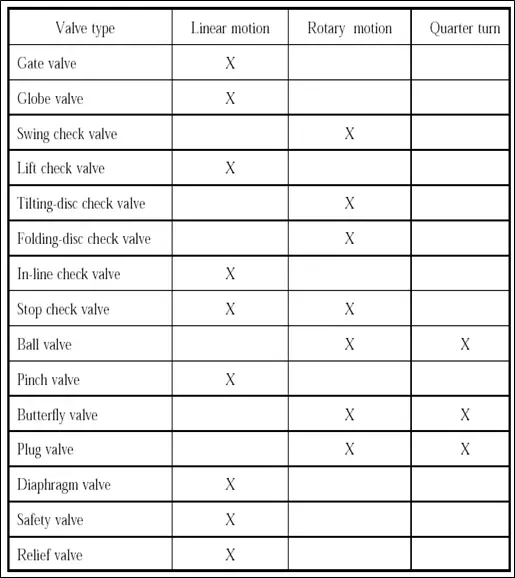
Valves Based on Pressure-Temperature Ratings
Based on pressure-temperature ratings, the following types of valves are available in the market.
- Class 150 (Allowable Pressure=16 bar)
- Class 300 (Allowable Pressure=40 bar)
- Class 400
- Class 600 (Allowable Pressure=100 bar)
- Class 900 (Allowable Pressure=160 bar)
- Class 1500 Allowable Pressure=250 bar) and
- Class 2500 valves (Allowable Pressure=400 bar)
However, the Class 400 valve is used occasionally in the piping industry. So less common.
Types of Valves as per Port Size
The port is the maximum internal valve opening for the flow. As per port size, there are two types of valves
- Full Port Valves: Available area almost equal to the full bore of the pipe
- Reduced Port Valves: They have less port area that produces a venturi effect to restore a large percentage of velocity head loss through the valve and produce a resultant total pressure drop of relatively low order.
Here is a brief description of some of the common types of valves. For further details on each valve type click on the name of the valve.
Gate Valves:
These valves control flow by raising or lowering a gate-like obstruction. They are well-suited for full open or full closed positions and are commonly used in applications where a straight-line flow with minimal pressure drop is required.
Ball Valves:
Ball valves use a rotating ball with a hole through it to control flow. They are versatile, durable, and suitable for on/off control as well as throttling applications.
Butterfly Valves:
These valves feature a circular disc that pivots on a central axis. They are ideal for large-scale applications due to their cost-effectiveness and ability to handle high flow rates.
Check Valves:
Also known as non-return valves, check valves allow flow in only one direction, preventing backflow. They are crucial for maintaining the integrity of a system and preventing damage.
Globe Valves:
Globe valves offer precise flow control through a disk element that moves perpendicular to the flow direction. They are commonly used for throttling applications where fine control is necessary.
Needle Valves:
Needle valves provide fine control over flow rates and are often used in situations where precise adjustments are needed, such as in laboratory settings.
Plug Valves:
Plug valves use a cylindrical or conical plug with a hole to control flow. They are durable and suitable for applications involving slurries and abrasive fluids.
Pressure Relief Valves:
These valves automatically release excess pressure from a system to prevent equipment damage. They are vital for ensuring safety in high-pressure environments.
Pinch Valves:
A pinch valve is a type of valve designed to control the flow of fluids by pinching or compressing a flexible tube or sleeve that serves as the valve’s main closure element. This unique mechanism allows for a simple yet effective way to start, stop, or regulate the flow of various liquids, gases, or slurries within a pipeline or system.
Major Valve Components /Valve Parts
There are two kinds of components in a valve
- Pressure Retaining Parts (Body, Bonnet, Cover Bolting, Disc, Valve Trim, etc) and
- Non-Pressure Retaining Parts (Valve Seats, Stem, Packing, Bushings, Yoke, Handwheel, Actuators, Gland Bolting, etc)
Valve Body:
The valve body is the house of the valve’s internal parts and the path for fluid passage. The valve body is manufactured by casting, forging, fabricating, or a combination of two or more methods. A variety of metals or nonmetals can be used to produce Valve bodies based on size and pressure-temperature rating and service requirements. The valve body (Fig. 5) ends are designed to connect with the pipe or equipment nozzles. Some Valve bodies are lined with corrosion-resistant materials.
Bonnet or Cover of the valve:
The valve body is fastened to the bonnet or cover, another pressure-retaining shell. It normally provides an opening for the valve stem to pass through. The bonnet (Fig. 5) contains a stuffing box. Valve internals is accessed through the bonnet or cover. It serves as the base for the valve top works like the yoke, hand wheel, etc. The Bonnet is classified based on the type of attachment as Bolted, Bellow, Sealed, Screwed-on, Welded, Union, Pressure Sealed, etc.
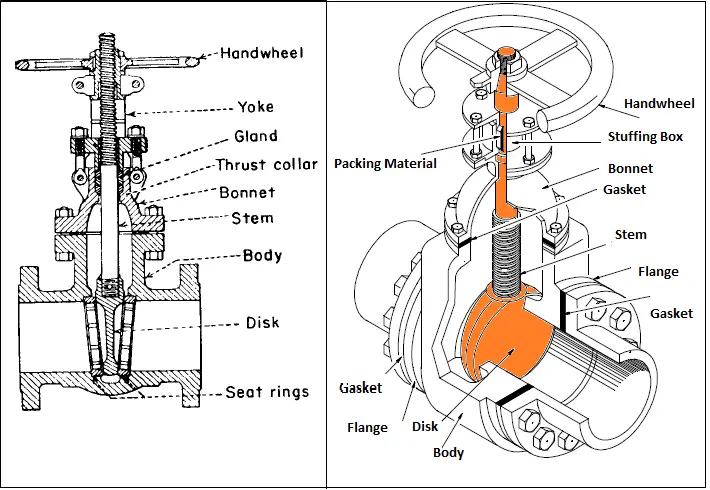
Cover Bolting:
Bolts, nuts, and washers are combinedly called Bolting. The bolting material is selected based on the application conforming to the applicable codes and standards.
Valve Disc:
The valve disc is one of the major components of the valve that allows, throttles, or stops the flow depending on its position. So, the disk directly affects the flow. In various valves, it is known by different names. For example, the disc is known as a plug in a plug valve, a ball in a ball valve, or a gate in a gate valve. A disc is made from casting, forging, or fabrication. When the valve is in a closed position, the disc is seated against the stationary valve seat. Using the motion of the valve stem, the disc (Fig. 5) can be controlled to open or close the valve.
Valve Trim:
Valve trims are the removable and replaceable internal parts of the valve. These parts come in contact with the flow medium and are collectively known as valve trim. Examples of such parts are valve seat(s), glands, discs, spacers, guides, bushings, and internal springs.
Note that, The valve body, bonnet, packing, etc even though comes in contact with the flow medium are not considered valve trim.
Valve Seat:
The non-moving part that the body bears is termed a valve seat. There may be one or more seats in a valve. Globe or swing-check valves have one seat while a gate valve has two seats; one each on the upstream and downstream side. The valve disc along with the seats form a seal that stops the flow.
Valve Stem:
The valve stem imparts the required motion to the disc to open or close the valve. One side of the stem (Fig. 5) is connected to the valve handwheel, actuator, or lever; while the other ends with the valve disc. In gate or globe valves, linear motion of the disc is needed to open or close the valve, while in plug, ball, and butterfly valves, the valve disc is rotated to open or close the valve. However, check valves (exception: stop-check valves) do not have valve stems. There are four categories of valve stem.
- Rising Stem: Handwheel can either rise with the stem, or the stem can rise through the stationary handwheel.
- Non-Rising Stem: The Hand Wheel and the stem are in the same position whether the valve is opened or closed. In such a case, the screw is inside the Bonnet and comes in contact with the fluid.
- Sliding Stem: In this variation, the valve stem slides in and out of the valve for opening or closing the valve.
- Rotary Stem: In ball, plug, and Butterfly valves, Rotary type valve stem is frequently used. To open or close such a valve, a quarter-turn motion of the stem is sufficient.
Valve Stem Packing:
Depending on the application; the Stem packing performs one or both of the following two functions,
● Preventing leakage of flow medium to the environment
● Preventing outside air from entering the valve in vacuum applications
Stem packing is contained in the stuffing box. Packing rings are packed and compressed by tightening a packing nut or packing gland bolts. Compression must be adequate to achieve a good seal.
Sealing between Valve Stem and Bonnet
The proper sealing between the bonnet and the valve stem is achieved by
- Using Gaskets in between a bolted bonnet and valve body.
- Using Metal Bellows where high vacuum or corrosive, flammable fluids are to be handled.
- Using gaskets in Flanged Valves to seal against the line flanges.
- Using a resilient seat serves as line gaskets for Butterfly Valves.
Valve Yoke and Yoke Nut
Using a Valve Yoke the valve body or bonnet is connected to the actuating mechanism. A Yoke must be designed strong enough as it will be subjected to forces, moments, and torque developed by the actuator.
A Yoke nut is an internally threaded nut and is placed on the top of a Yoke by which the stem passes.
Working of a Valve
The working of a valve involves the manipulation of its components to control the flow of fluids through a pipeline or system. Valves operate by opening, closing, or partially obstructing the pathway through which fluids pass. The specific operation of a valve depends on its type and design. In general, the valve works as follows:
- Opening the Valve: In the closed position of the valve, the disc makes contact with the seat, preventing fluid from passing through the pipeline. To open the valve, the actuator applies force to the stem, causing the disc to move away from the seat. This opening allows fluid to flow through the valve, following the pathway defined by the design of the valve.
- Partial Flow Control: Many valves offer the ability to control the flow rate by partially obstructing the pathway. By adjusting the position of the disc using the actuator, the effective opening can be modified, allowing more or less fluid to pass through. This is particularly useful for applications where precise flow control is required.
- Closing the Valve: To close the valve, the actuator reverses its operation and moves the disc back into contact with the seat. The sealing action stops the flow completely, preventing any further passage of fluids.
For the specific operation of each type of valve, you can refer to the specific type of valve by searching on this website.
Valve Standards:
Valve standards provide a set of guidelines, specifications, and regulations established by various organizations to ensure the safety, reliability, and consistency of valves used in industrial applications. These codes and standards provide manufacturers, engineers, and users with a common framework for designing, manufacturing, testing, installing, and maintaining valves. They cover various aspects of valve design, materials, performance, and testing to ensure that valves meet the required quality and safety standards.
Here are some notable valve standards:
American Petroleum Institute (API) Valve Standards:
- API 600: Covers design and manufacturing requirements for bolted bonnet steel gate valves.
- API 602: Specifies requirements for forged steel gate, globe, and check valves.
- API 603: Corrosion-resistant, Bolted Bonnet Gate Valves-Flanged and Butt-welding Ends
- API 594: Check Valves: Flanged, Lug, Wafer, and Butt-welding
- API 607: Fire test for Quarter-turn Valves and Valves with Non-metallic Seats
- API 609: Focuses on butterfly valves used for isolating and controlling flow in various industries.
- API 598: Valve Inspection and Testing
- API 6D: Addresses pipeline valves, including gate, plug, ball, and check valves, for petroleum and natural gas industries.
- API 6FA: Standard for Fire Test of Valves
- API RP 574: Provides guidelines for the inspection of valves, which includes requirements for visual, magnetic particle, liquid penetrant, and ultrasonic testing.
American Society of Mechanical Engineers (ASME) Valve Standards:
- ASME B16.34: Provides requirements for valve design, materials, pressure-temperature ratings, and testing.
- ASME B16.10: Specifies face-to-face dimensions of various industrial valves.
- ASME B16.5: Covers pipe flanges and flanged fittings, including flange dimensions and materials.
- ASME B16.25: Addresses butt-welding ends for piping components like valves.
- ASME B16.47: Large Diameter Steel Flanges
- ASME B16.20: Metallic Gaskets for Pipe Flanges
- ASME B16.48: Line Blanks
International Organization for Standardization (ISO) Valve Standards:
- ISO 5208: Specifies the test procedures for pressure testing of valves.
- ISO 14313: Focuses on valves for pipeline transportation systems within the petroleum, petrochemical, and natural gas industries.
- ISO 10497: Testing of valves-Fire Type-Testing requirements
- ISO 17292: Metal ball valves for petroleum, petrochemical, and allied industries
- ISO 15848: Industrial valves – Measurement, test, and qualification procedures for fugitive emissions
MSS (Manufacturers Standardization Society) Valve Standards:
- MSS SP-25: Covers standard marking system for valves, fittings, flanges, and unions.
- MSS SP-61: Specifies pressure testing of steel valves.
European Valve Manufacturers Association (FSAE):
- EN 12516: Addresses industrial valves for petroleum, petrochemical, and natural gas industries.
European Committee for Standardization (CEN):
- EN 593: Focuses on butterfly valves for general purposes.
- EN 12569: Specifies requirements for ball valves for pressure applications.
British Valve Standards
- BS 1873: Specification for Steel Globe and Globe Stop and Check Valves (Flanged and Butt-Welding Ends) for the Petroleum, Petrochemical, and Allied Industries
- BS 1868: Specification for Steel check valves (flanged and buttwelding ends) for the petroleum, petrochemical, and allied industries
Selecting the Right Valve
Choosing the appropriate valve for a specific application requires careful consideration of factors such as fluid type, pressure, temperature, flow rate, and operational environment. The process engineers in discussion with instrumentation engineers usually decide the type of valve required for a specific fluid and function. Sometimes, It’s important to consult valve manufacturers or experts to ensure you make an informed decision. The steps of the valve selection procedure are covered here in detail.
In conclusion, piping valves are essential components in a myriad of industries, enabling the precise control and regulation of fluid flow. Their various types and applications underscore their importance in maintaining the efficiency, safety, and reliability of industrial processes. Whether you’re managing a power plant, chemical processing facility, or simply using water at home, piping valves silently work to keep things running smoothly.
Superb presentation/notes/description/research/illustrations on valve sir. Thank you so much
Helpful your knowlge share topic.
Could you also add a table that highlights the duration time for fabrication and delivery times for various types of valves?
Regarding Reduced Port Valves, venturi effect increases total lost due to increase in speed in comparison to a full port. Let’s just considering a a full port valve as a pipe with the same bore of the upstream and downstream pipe and a reduced port valve as two reducers; which one has less pressure drop?
Reduced port is used where the increased velocity is used functionally, e.g. any type of swing check valves to ensure full opening of the obdurator.