Duplex Stainless Steel is a specific group of engineering stainless steel materials consisting of the austenitic and ferritic phases in roughly equal proportions in the microstructure. They are widely popular because of their good corrosion resistance, high strength, and ease of fabrication. They are also popular by their acronym DSS. Compared to traditional austenitic stainless steel and ferritic stainless steel grades; Duplex Stainless Steels provide a range of benefits:
- Improved Strength: Roughly two times stronger than normal stainless steel grades.
- High Toughness and Ductility
- High Corrosion Resistance
- Cost-Effectiveness: High strength of DSS material required less pipe thickness reducing pipe weight. Also, lower levels of nickel reduce cost.
Applications of Duplex Stainless Steel
Excellent corrosion resistance with increased strength and affordable pricing makes duplex stainless steel (DSS) a popular choice for a variety of industries. Their wide uses are found in:
- Chemical and liquid processing
- Offshore (flowlines, risers) and other industrial operations
- Naval parts and components
- Pulp and paper production
- Pollution control equipment
- Water Treatment/Desalination plants
- Construction, Infrastructure, Architecture
- Hot water and brewing tanks
- Food and Drink Storage
- Boilers, Heat exchangers, pressure vessels
- Marine Tanks
- Renewable Energy
- Nuclear Industry
Duplex Stainless Steel Grades
Duplex stainless steels have a higher chromium content, 20–28%; higher molybdenum, up to 5%; lower nickel, up to 9%, and 0.05–0.50% nitrogen as compared to austenitic stainless steels. For resistance against pitting corrosion, DSS material is an ideal selection. The resistance against pitting corrosion is characterized by the pitting resistance equivalence number, or PREN Number defined as follows:
PREN = %Cr + 3.3 %Mo + 16 %N
Depending on the PREN Number values, Duplex Stainless Steel is categorized into four grades.
- Lean duplex grades (PREN range: 22–27): No deliberate Molybdenum addition. mainly used in the building and construction industry for bridges, pressure vessels, or tie bars. Example: S32001, S32101, S32304, S32202.
- Standard duplex (PREN range: 28–38): The most widely used (More than 80%) duplex stainless steel material with mid-range properties. Example: S32003, S31803, S32205
- Super duplex (PREN range: 38-45): Higher contents of Cr, Ni, Mo, N, and even W. Specifically designed for highly corrosive oil & gas and chemical industries. Example, S32750, S32760, S32950, S32808.
- Hyper duplex (PREN >45): These are highly alloyed duplex stainless steel. Example S32707, S33207
Naming Convention for Duplex Stainless Steels
Various naming conventions are followed for duplex stainless steels such as:
- Composition-based Names: For DSS 2205 or 2305; 22 or 23 denotes %Cr and 5 denotes %Ni in that specific DSS material.
- UNS Designation: The Unified Numbering System or UNS designation of DSS materials is the most popular and listed on ASTM specifications.
- AISI Designation: Only one DSS material type 329 has an AISI designation.
Duplex Stainless Steel Properties
As informed earlier the duplex name has arrived from the co-existence of both austenitic (FCC Structure) and ferritic (BCC Structure) in approximately equal proportions (Fig. 1). The major alloying elements are Chromium, Silicon, Molybdenum, Carbon, Nickel, Nitrogen, Manganese, Copper, Tungsten.
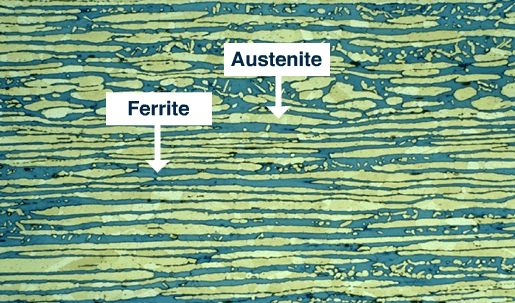
Typical duplex stainless steel exhibits a higher strength value as compared to stainless steel. But, the working temperature range of DSS is normally narrow as at around 300oC undesirable intermetallic phases (α’ -alpha prime phase) start to precipitate which decreases the mechanical properties and corrosion resistance by embrittlement phenomenon. The following table provides some selected properties of common duplex stainless steel grades.
DSS Grades | ASTM A789 Grade S32520 Heat-Treated | ASTM A790 Grade S31803 Heat-Treated | ASTM A790 Grade S32304 Heat-Treated | ASTM A815 Grade S32550 Heat-Treated | ASTM A815 Grade S32205 Heat-Treated |
Elastic Modulus | 200 GPa | 200 GPa | 200 GPa | 200 GPa | 200 GPa |
Elongation | 25 % | 25 % | 25 % | 15 % | 20 % |
Tensile Strength | 770 MPa | 620 MPa | 600 MPa | 800 MPa | 655 MPa |
Brinell hardness | 310 | 290 | 290 | 302 | 290 |
Yield Strength | 550 MPa | 450 MPa | 400 MPa | 550 MPa | 450 MPa |
Thermal expansion coefficient | 1E-5 1/K | 1E-5 1/K | 1E-5 1/K | 1E-5 1/K | 1E-5 1/K |
Specific Heat capacity | 440 – 502 J/(kg·K) | 440 – 502 J/(kg·K) | 440 – 502 J/(kg·K) | 440 – 502 J/(kg·K) | 440 – 502 J/(kg·K) |
Thermal Conductivity | 13 – 30 W/(m·K) | 13 – 30 W/(m·K) | 13 – 30 W/(m·K) | 13 – 30 W/(m·K) | 13 – 30 W/(m·K) |
The stress-strain curve of austenitic, ferritic, and duplex stainless steels are plotted in the following curve for reference:
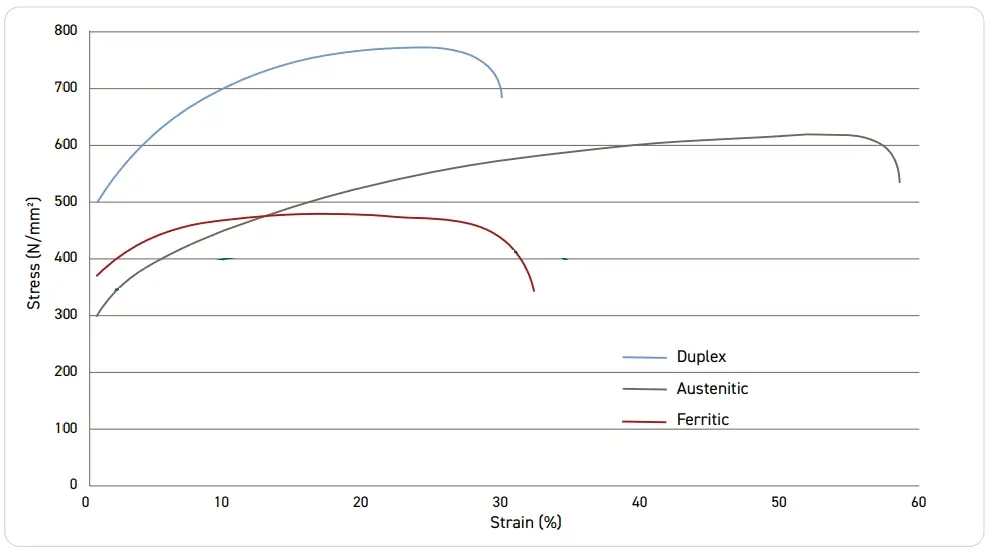
Composition of Duplex Stainless Steel
The following table in Fig. 3 and Fig. 4 provides the chemical compositions in %wt for common DSS and SDSS materials.
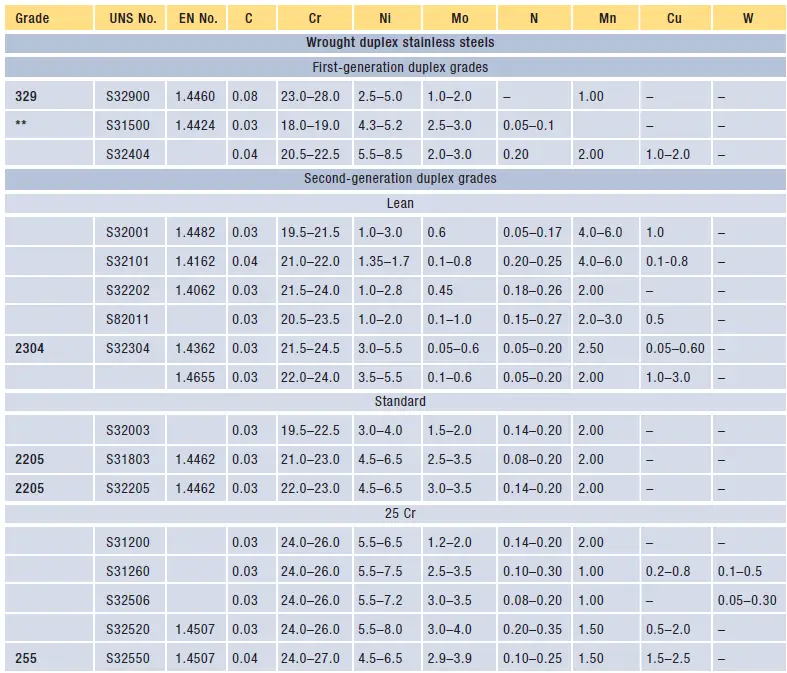
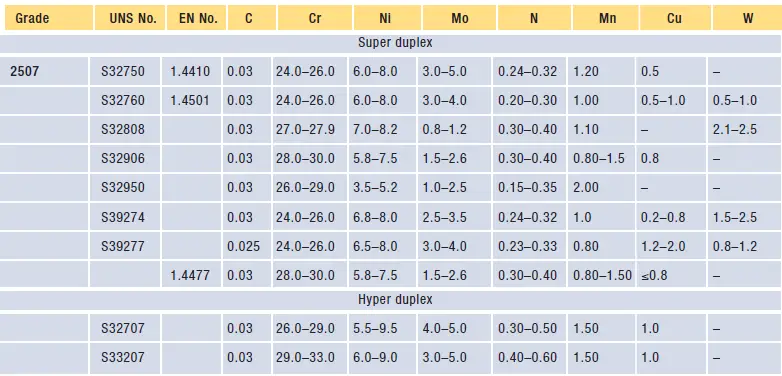
Corrosion Resistance of Duplex Stainless Steel
Due to the presence of a relatively high % of chromium, molybdenum, and nitrogen, Duplex Stainless Steels exhibit a high level of corrosion resistance capability in a variety of environments. DSS materials are specifically selected for oxidizing, acidic, and hot alkaline environments. To fight against pitting corrosion, DSS is the ideal material choice. The PREN Number defined above describes the resistance of DSS against localized pitting corrosion. An increase in PREN Number increases the resistance against pitting corrosion that is quantified using Critical Pitting Temperature. Materials with higher CPT are more resistant to pitting corrosion.
Duplex stainless steels possess better Stress Corrosion Cracking resistance than austenitic stainless steel.
Fabrication of Duplex Stainless Steel
Duplex Stainless steel is supplied in a pipe, plate, sheet, tube, fittings, or bar form. Depending on the requirement they must be fabricated. Special tools are required for the fabrication of duplex stainless steel materials. They have very good weldability and hot-forming capability. However, DSS materials are normally difficult for machining purposes.
Difference Between SS, DSS, and SDSS
Some of the important differences between SS, DSS, and SDSS are provided here: What is SS, DSS, and SDSS in Piping for Oil and Gas Applications
Differences between DSS and SDSS?
Duplex Stainless Steel (DSS) and Super Duplex Stainless Steel (SDSS) are both types of stainless steel that combine the properties of austenitic and ferritic stainless steel. However, the key differences between them are:
- Composition: SDSS has higher chromium (25-27%), molybdenum (3-5%), and nitrogen content compared to DSS, which typically has 22-25% chromium, 3-4% molybdenum, and lower nitrogen content.
- Strength: SDSS offers higher yield strength than DSS, making it suitable for more demanding applications.
- Corrosion Resistance: SDSS has superior resistance to pitting, crevice corrosion, and stress corrosion cracking, particularly in aggressive environments like seawater, sour gas, and chloride-rich conditions.
- Applications: SDSS is often used in more extreme environments, such as subsea equipment and high-pressure pipelines, where the material’s superior performance is critical.
Fig. 5 below provides a nice image showing some of the applications of DSS and SDSS material in Onshore Oil & Gas:
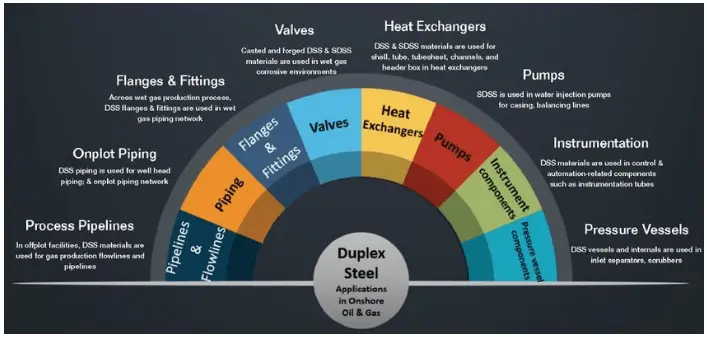
Relationship between SDSS and DSS
SDSS (Super Duplex Stainless Steel) is an enhanced version of DSS (Duplex Stainless Steel). While both materials share a similar duplex microstructure (a roughly equal mix of austenite and ferrite phases), SDSS is designed for even higher performance. The relationship is that SDSS builds on the foundation of DSS by offering increased strength and better corrosion resistance, making it suitable for more demanding environments. Essentially, SDSS is a more advanced form of DSS with higher alloy content and improved properties.
Differences between SS and DSS
Stainless Steel (SS) and Duplex Stainless Steel (DSS) differ primarily in their microstructure, composition, and performance:
- Microstructure: SS can be austenitic, ferritic, or martensitic, while DSS has a mixed microstructure of approximately 50% austenite and 50% ferrite.
- Corrosion Resistance: DSS generally offers better resistance to pitting, crevice corrosion, and stress corrosion cracking, particularly in chloride-containing environments, compared to SS.
- Strength: DSS has nearly twice the yield strength of austenitic SS, allowing for thinner sections and potential cost savings in certain applications.
- Applications: SS is widely used in a variety of applications, while DSS is favored in more demanding environments, such as offshore platforms, subsea pipelines, and chemical processing plants.
DSS Pipe Material Specification
The DSS Pipe Material Specification defines the chemical composition, mechanical properties, and acceptable testing methods for Duplex Stainless Steel piping. A common specification is ASTM A790/A790M, which covers seamless and welded duplex stainless steel pipes for high-temperature and general corrosive service. The specification outlines requirements such as:
- Chemical Composition: Specific ranges for elements like chromium, nickel, molybdenum, and nitrogen.
- Mechanical Properties: Minimum yield strength, tensile strength, and elongation requirements.
- Testing Methods: Includes hydrostatic testing, nondestructive testing (NDT), and intergranular corrosion testing.
Frequently Asked Questions of DSS with Answers
- What is meant by duplex stainless steel?
- The word duplex in stainless steel refers to the two-phase microstructure of DSS material. Duplex stainless steel is a family of stainless steel having ferritic and austenitic phase microstructure in approximately equal proportions.
- Is 304 stainless steel a Duplex?
- No, 304 stainless steel is austenitic stainless steel. It is not a duplex.
- Is 316 stainless steel a Duplex?
- Stainless steel 316 is not a duplex SS. 316 SS is austenitic in nature.
- What is the purpose of duplex stainless steel?
- Duplex stainless steels have roughly twice the strength of austenitic stainless steels and higher resistance to pitting corrosion, crevice corrosion, and stress corrosion cracking.
- Does duplex stainless steel rust?
- Duplex Stainless steel has a very high chromium content that prevents the DSS material from rusting. So, in general, duplex stainless steel does not rust. However, under a suitable corrosive environment, DSS may corrode or rust.
- Is 2205 duplex stainless steel magnetic?
- As duplex stainless steels are ferritic as well as austenitic, it does have magnetic properties. 2205 super duplex is also magnetic. All DSS materials are magnetic.
- Does duplex 2205 rust?
- 2205 stainless steel being a DSS usually does not rust. But when exposed to severe conditions, it may corrode.
- What is the difference between a duplex and a super duplex stainless steel?
- Super duplex stainless steel is an improved duplex stainless steel. It possesses additional characteristics as compared to DSS. DSS has 25% chromium, 7% nickel, and 4% molybdenum content which makes the material have higher corrosion resistance and . strength than duplex stainless steel.
- How strong is duplex stainless steel?
- Duplex stainless has more strength as compared to other groups of stainless steel. Roughly, duplex stainless steel is around twice as strong as either ferritic or austenitic stainless steel.
- Who invented the super Duplex?
- Super Duplex stainless steel was developed by Langley Alloys in the mid-1960s and was launched in 1969.
- What grade is a super duplex?
- DSS grades UNS S32760, S32750, F55, 1.4501, etc are super duplex.
- What is the DSS Material Code?
- The material code for Duplex Stainless Steel (DSS) typically refers to a standardized designation used in engineering and procurement to specify the type of material. One common code system is the Unified Numbering System (UNS), where DSS is often designated by codes such as:
- UNS S31803: Standard grade of DSS, also known as 2205.
- UNS S32205: An improved version of S31803 with slightly higher nitrogen content, offering enhanced corrosion resistance.
- The material code for Duplex Stainless Steel (DSS) typically refers to a standardized designation used in engineering and procurement to specify the type of material. One common code system is the Unified Numbering System (UNS), where DSS is often designated by codes such as:
- Which is cheaper: DSS or SDSS?
- Duplex Stainless Steel (DSS) is generally cheaper than Super Duplex Stainless Steel (SDSS). The lower cost of DSS is primarily due to its lower alloy content, particularly the reduced levels of chromium, molybdenum, and nickel compared to SDSS. While SDSS offers superior strength and corrosion resistance, its higher material cost reflects these enhanced properties. However, the choice between DSS and SDSS should be based on the specific application requirements, as SDSS may provide cost savings in the long term by reducing maintenance and extending service life in harsh environments.
Click here to learn cathodic protection design for DSS pipes
Dear Anup,
When considering manufactured items in either Cast or Forged Duplex Materials it’s worth mentioning the type of quality requirements that are typically required. Vendors should be conformity assessed and qualified by an appropriate Notified body against ISO 17782:2018 or Norsok M650 for the size / weight of the product they are making. MDS such as those contained in IOGP S563 / M630 should be used to ensure the product is manufactured correctly.
If DSS are competitive material then why it is not used in extensively?
What is the difference between austenitic SS and DSS?
If we generally use 18-8 that is SS304 material for High Temp. then what is the equivalent DSS to ASTM A304, 310 ?
Hi Anup, very well explained in depth. Really appreciate your efforts for junior / senior level piping engineers.
In my view Duplex is known as 22% crome and Super Duplex is known as 25% crome. Most of the UK and Norwegian continental shelf uses this material for hydrocarbon due to low temp condition. In gulf region this material is replaced by Inconel 625 for offshore piping.
Hello Anup,
Appreciate your efforts to aware the industry about DSS materials.
We are aggressively promoting Duplex steels and super Duplex steels in last few years. In fact we have convinced many of our clients to use DSS instead of 316L in process industry.
Good site Anup
I have had a supplier quote the use of a C26 Duplex Stainless Steel for the wet end of an acid water pump, unfortunately I am unable to find a spec sheet or for that matter any technical data at all on C26 Duplex, are you familiar with this material?
Hi Kumar,
We are required to send test samples made of DSS pipe weld joint for G48A testing.
How can I ensure that the weldment is ok for getting satisfactory result from G48A test?
Is there any satisfactory and instant testing for this purpose?
G48A is very expensive and time consuming so we need to make sure it is ok for it…
Hi Anup,
thanks for sharing,
My concern is joining DSS to Al alloy by Brazing using Al-Si12 filler metals and the Control Atmosphere Brazing process (CAB),
can you provide your kind recommendation and comments regarding to the using process and thermal cycle parameters, etc.
I’ll be highly appreciated for your help,
Regards
Ihsan
Hi Kumar,
Need your urgent advice regarding the safest way to offload coated DSS pipes ? using Hooks ?…
please advise ASAP
Kind regards
KM