Choke valves or choker valves are a type of severe service control valve that is widely used in oil and gas production wells. They control the flow of well fluid. Additionally, Choke valves act to kill the reservoir pressure and regulate the downstream flowline pressures. A choke valve consists of a plug or stems that move up and down inside a slotted cylinder to control the flow.
Choke valves are very robust in design to handle severe extreme conditions of high corrosion, erosion, high fluid velocity, wide ranges of flow rates, marine environmental conditions, etc. It has the ability to handle extreme pressure drops in the range of 500 bars. Choke valves are usually designed based on API codes (API 6A/6D). Refer to Fig. 1 below that provides a typical cross-section of a choke valve.
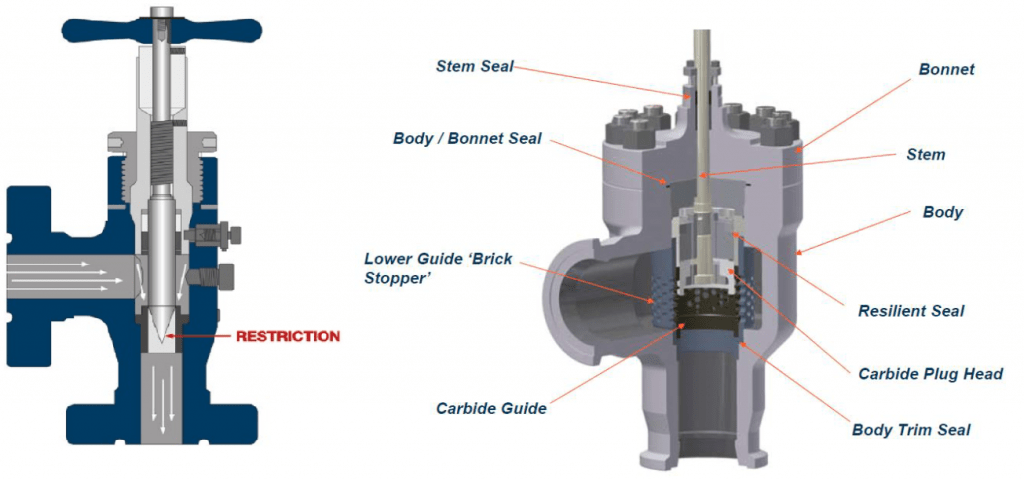
Applications of Choke Valves
Choke valves are found in a variety of applications. Some of the common uses of choke valves are:
- Production well heads
- For gas reinjection in the Christmas tree
- In surface and sub-sea manifolds to handle mixtures of crude, gas, water, and sand in various chemical industries.
- To handle Steam and CO2 in various petrochemical plants.
- In drilling mud and hydraulic fracturing applications for oil and gas industries.
- Oil and gas reserves.
- Flowlines with very high operating pressure requirements.
- Cementing and acidizing lines.
- Oil and gas production platforms.
- FPSO loading vessels.
Types of Choke Valves
Depending on the function of the choke valves they are classified into two groups. They are:
- Regulating choke valves and
- Non-regulating choke valves.
Regulating Choke Valves
This type of choke valve acts as a flow control valve. These valves are capable of maintaining steady production levels in production headers and flowlines. It is an automatic valve where an electric signal from the panel controls the opening of the valve.
Non-regulating Choke Valves
Non-regulating choke valves act as an On-Off valves. The opening of these types of choke valves is designed in such a way that it can remove pressure when in fully open condition. As the name suggests, they do not regulate or control the flow.
Depending on the orifice size, there are two types of choke valves.
- Positive Choke valve having a fixed orifice size, and
- Adjustable choke valves with a variable orifice size with an external adjustment device to vary the orifice size.
Depending on the design and construction of the choke valves they are grouped into the following types:
- Needle and Seat Choke valve: simple design of positive choke with a cone-shaped plug, rising stem, and handwheel.
- Plug and Cage choke valve: complex design with ported cages arranged to provide a great combination of flow and control capability.
The Port cage of the choked valve can be of various types like:
- 4-port cage: Used for well-site separators and line heaters.
- Multi-ported cage: for high-pressure drop critical applications.
- Plug and cage design: for high-capacity applications.
Choke Design
To make better use of the gas for natural gas lift and to control the bottom hole pressure for recovery reasons, chokes hold back pressure on a flowing well. With decreasing hydrostatic head, the gas expands rapidly in vertical pipe flow, and the liquid moves in slugs through the tubing. This causes the potential gas lift energy to be rapidly lost. In turn, the liquids fall back and begin to accumulate over the perforations. These accumulating liquids hold back pressure on the formation. When enough liquids accumulate, the well may “die” and quit flowing.
The choke holds this backpressure by restricting the flow opening at the wellhead. The uncontrolled expansion and rise of the gas are restricted by the back pressure. It thus helps keep the gas dispersed in the liquids on the way up the tubing.
Chokes may have a variable or a set opening. The set openings, known as “beans,” are short flow tubes. They graduated in 1/64ths of an inch. Common flow sizes are about 8 through more than 20 (in 64ths) for small to moderate-rate gas wells.
Depending on the reservoir pressure, tubing size, amount of gas, and the amount and density of liquids, the size of the choke varies. To allow quick resetting, variable chokes may use an increasing width slot design. They are useful on well-cleanups following stimulation where choke size can vary over the course of a single day. They can also be used for periodic liquid unloading that necessitates frequent choke size changes.
Choke valve Symbols
Chokes valves are usually denoted by the following symbol in P&IDs.
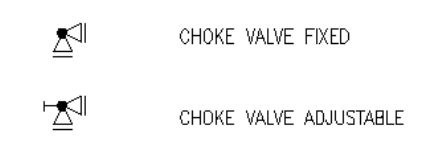
Functions of a Choke Valve
A choke valve mainly performs the following three main functions:
- Changing the flow rate by controlling the choke cross-section.
- Loading resistance, and
- Pressure buffering by hindering the fluid flow to a certain extent.
Working Principle of a Choke Valve
The main purpose of a choke valve is to restrict the flow through the valve to have the desired flow rate. This is achieved by reducing the flow area through the valve body. The adjustable choke valves control the flow rate by adjusting the stem and seat combination. The handwheel can be turned to set the orifice size and flow coefficient which in turn produces the required flow rate. In the case of positive choke valves, a fixed flow rate is achieved through the use of a choke bean.
Selection of Choke Valves
Choke valves are carefully selected based on applications and various factors like size, material, trim design, etc. The parameters that influence the selection of choke valves are:
- Inlet and outlet velocities
- Cavitation index
- Pressure drop limitation
- Sound pressure level
- Required flow rate
- Process operating conditions
- Start-up conditions
- Size and Schedule of connecting pipework.
- Physical properties of fluid handled
Advantages of Choke Valves
Choke valves are widely used in oil and gas production facilities because of their reliability and safe handling of high operating pressures. The main advantages of choke valves are:
- High reliability
- High rangeability
- Controlled erosion
- Low noise
- The ability of pressure balancing
- Accurate flow rate adjustment
- Long service life
Further Studies
More details about the choke valves can be accessed by clicking here.
Useful information,
Thank you very much!
Very well clearly expalined.
Thanks for this information. Very good.
Beautiful