In recent times, FEA or Finite Element analysis is the most widely used method for solving engineering and mathematical models. Using Finite Element Analysis or FEA, a physical phenomenon is simulated to find close to real behavior. FEA is developed using a numerical mathematic technique known as the Finite Element Method, or FEM. Finite Element Analysis is a computer-aided numerical analysis program that solves complex problems in many engineering fields. The complex problems might be
- thermal analysis such as steady-state and transient,
- structural analysis such as stress, vibration, and deflection, and
- fluid dynamic analysis such as turbulent and laminar flow.
Basically, with the help of this method, one can find stress distribution in complex geometries. It provides solutions to problems that are anyway difficult to obtain. In other words, the finite element analysis method is a faster way to get solutions to problems that are difficult to solve.
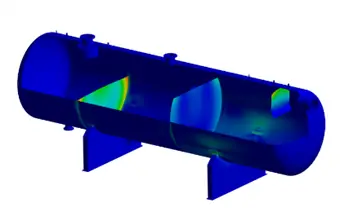
FEA Meaning
In simple language, finite element analysis or FEA is the right approach to problems like when a force is applied on a solid, what could be the values of the displacements, strains, and stresses at each material point? The most logical answer is that FEA tells us where a particular object can break or strain to make it unusable. The most common problems solved by FEA involve determining stress intensity factors of a load on an object. This can be in any form such as solid mechanic analysis, thermal analysis, structure analysis, dynamics, and electrical analysis.
How Does Finite Element Analysis Work?
Finite element analysis software creates a mesh of millions of smaller elements to create the complete structural shape. The effect of the parameter for example internal pressure force is assessed on each element and then combined to arrive at the final result for the full equipment or structure.
Importance of Finite Element Analysis or FEA
Finite Element Analysis is the basis of modern software simulation with the results shown on a computer-generated color scale. There are some theories that state that finite element analysis has its roots in the 16th-century work of Euler, which is the earliest mathematical paper describing the technique dating back to Shellback’s work of 1851. This method was then developed by engineers from various industries around the world thereby helping the user to solve a large number of structural mechanic problems, basically in civil engineering and aerospace. The very first development of finite element analysis for real applications began in the 1950s.
Finite element analysis is important as it plays a major role in the product design and development process. It has the capability to identify where a problem can occur in a product or an object. This method uses mathematical calculations to solve the problem areas of an object, thereby saving engineers the time and effort required to build a physical prototype. On the other hand, prototype tests as compared to FEA do not provide numerical calculations which makes the product development process quite long. Finite element analysis software saves both time and effort for the engineers. The importance of this software lies in its ability to take a complex design and highlight the efficiency and robustness of the design. With the help of FEA, engineers can quickly understand early information on system failures and their improper design techniques.
The finite element analysis method is used in almost all engineering disciplines. It is known to be the alternative to the experimental test method being set in many standards. It works in such a way that a user can reach an approximate solution to any complex problem by dividing the component into smaller or finite elements.
Advantages of FEA
There are numerous advantages of FEA:
- It is used in many engineering disciplines for the estimation of structural behavior and strength, design optimization, modeling, and simulation.
- It is used in piping design where rigidity is a governing factor instead of flexibility.
- There are a few limitations of beam element software like CAESAR II that experienced engineers and designers are aware of. CAESAR II may indicate stress or sometimes loading issues that may not exist and sometimes fail to point out the issues.
- The application of FEA software is created to address problems related to piping and pressure vessel that CAESAR II and code limitations cannot resolve.
- It helps in solving problems related to buckling and plasticity.
- Buckling is a concern where Piping and pressure vessel geometries have a large D/t ratio or external pressure. In this case, FEA analysis of pressure vessels helps to analyze buckling and elastic-plastic collapse study.
- Thermal gradients through the wall often result in significant stresses. In this case, it also, FEA helps in analyzing steady-state transient thermal stresses.
- Optimal use of a model.
- It gives comprehensive result sets by generating a physical response of the system at any location which might have been neglected in the analytical approach.
- It provides rapid calculation time and low investment for most applications.
- It provides engineers with simultaneous calculation and visual representation of a number of physical parameters like stress, and temperature and helps the designer to quickly analyze performance and necessary modifications.
- It helps to gain a thorough understanding of the behavior of the product and the nature of the application.
- An FEA tool improves the quality of user analysis for critical service lines.
- FEA tool automatically includes coverage of B31J2017 ASME B31 code in the analysis and hence gives more accurate flexibility and SIF factors for necessary components.
Finite Element Analysis software
There is numerous finite element analysis software available in the market and it’s really difficult to choose. Widely used engineering finite element analysis software are:
- ANSYS: US-based full CAE software package.
- AutoDesk CFD: Finite Element Analysis software of Autodesk.
- Nozzle-Pro: By PRG
- ROHR2fesu: Finite Element Analysis of substructures in ROHR2.
- PASS/EQUIP Nozzle-FEM: By PASS
- Abaqus: Advanced Franco-USA software from SIMULIA, owned by Dassault Systemes
- MATLAB: MATLAB Toolbox for solving structural, thermal, electromagnetics, and other general PDEs
- Solidworks FEA Simulation
- RFEM: 3D finite element analysis software
- Advance Design: BIM software for FEM structural analysis, including international design eurocodes.
- OpenFOAM: By the OpenFOAM Foundation
- Simscale: German 100% web-based CAE platform
- VisualFEA: FEA software for structural, geotechnical, heat transfer, and seepage analysis.
- RoboLogix: By Logic Design Inc.
- COMSOL Multiphysics: COMSOL Multiphysics Finite Element Analysis Software (formerly FEMLAB)
- IVRESS: By Advanced Science & Automation Corporation
- Altair HyperWorks Suite: By Altair Engineering
- Advanced Simulation Library: By Avtech Scientific
- SU2: By Stanford University
- PRO/II Process Engineering: By AVEVA
- Ingrid Cloud: By Adaptive Simulations
- Nastran: Originally developed for NASA, now available commercially from several software companies
Out of the above ANSYS is the most widely used FEA software. For Nozzle load checking Piping and Mechanical Engineers use the NozzlePRO or PASS/EQUIP Nozzle-FEM package.
When to use the CAESAR II FEA module
Caesar II FEA module can be used during the following circumstances:
- To check nozzle loads where WRC 107/297 are often inaccurate and not comprehensive.
- When the d/D ratio is greater than 0.5, that is, to examine large branch intersections.
- For piping having D/t ratios of more than 100.
- To calculate accurate operating bolt load while performing flange analysis.
- To accurately estimate SIF and flexibility for piping analysis.
- Piping systems that use thin-walled welding tees.
- To determine external loads on saddle-supported vessels.
- When a piping system requires a more accurate spring hanger design.
- Piping systems that are connected to sensitive or rotating equipment.
- Piping Systems are anticipated to have operating cycles of more than 7000.
- When there is short or stiff piping in a system where k factors have a large impact.
- When a piping system has questionably high calculated stresses.
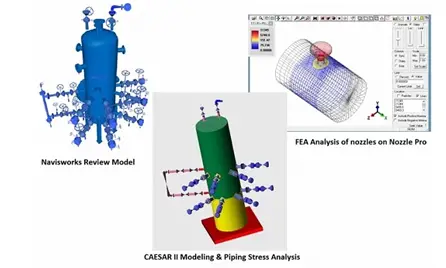
Examples of Finite Element Analysis
We will explain the results by taking an example of a piping system as shown below in Fig. 3:
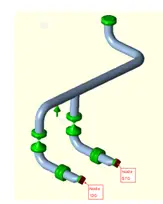
There are two pumps. Both of these pumps combined to a common header as shown in Fig.3 Here we have used FEATools to reduce the loads on the nozzles of pumps A and B at odes 120 and 570. The load on the nozzle having node no.120 is FX=1140lb and for node no. 570, FX= 3626lb. The question here is whether will FEA Tools help in Caesar II analysis.
SIF and flexibilities can be refined to new factors at the tee location with the help of FEA Tools, hence we will see if this results in reducing the loads at the pump nozzles.
Table 1 in Fig. 4 shows the global element forces for pumps A and B before using FEA Tools and Table 2 shows the global element forces after using FEA Tools respectively.
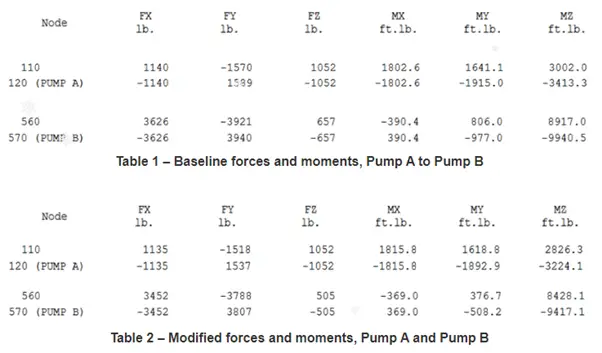
Conclusion: SIF and Flexibility are updated based on ASME 07-02, with suitable changes to appendix D of the B31 codes. Also, it is quite clear that there is a lot of incorrect SIF from ASME B31J that has been shown and provide the user with incomplete guidance. Further to be noted, for branch connections, the omission of k-factors allows for ASME 07-02 to correct these errors. Basically, the use of FEA Tools does not really mean that it can reduce the nozzle loads until the stresses reach the allowable stress.
Fig.5 shows the added restraints and spring at the branch connection as per the guidelines in 07-02 of FEA Tools.
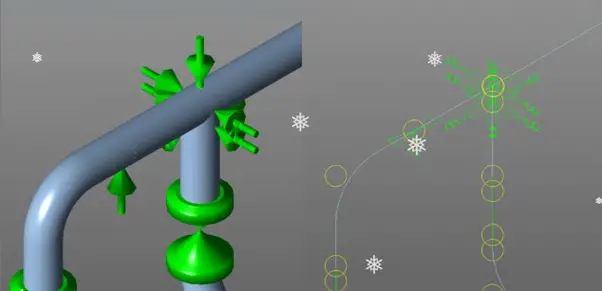
To the center point of the tee, each branch is connected by a series of connecting nodes with k factors as per the allowable in ASME 07-02. The purpose of the added spring would be to reduce the stress caused due to thermal strain in a piping system. Such types of piping systems are best applicable with expansion joints or expansion loops when no other solutions are successful or not ideal in Caesar II analysis. Hence an analyst can conclude that FEA Tools itself cannot reduce the loads significantly enough to create that much difference in the equipment’s overall loads. One must think of other options to reduce the loads in the pump nozzles.
ASME B31J the engineer should use stress intensification factor and flexibility factor data from the code in the absence of applicable data. In order to supply this applicable data to CAESAR II, FEA-Tools uses the results of the latest research, analysis, and testing.
FEA vs FEM
Are FEA and FEM the same or are there any differences!!
FEA (Finite Element Analysis) | FEM (Finite Element Method) |
FEA is the application of FEM | FEM is the cause or reason. It is the background theory behind FEA software. |
This is the same as FEM. Engineers involve FEM to predict the performance of their designs in different conditions. | A numerical technique that is used to get approximate solutions of the partial differential equations. |
It is related to solids and can be used for anything. | Here the analysis could be solid, fluid, thermal, or electromagnetic. |
It is most popular in industries. | It is popular in universities. |
It covers a wide area of problems related to heat transfer, the strength of materials, vibrations, and acoustics. | It includes the Galerkin method, numerical integration methods, and weighted residual method to solve problems. |
It is learning basic FEM concepts, and solid mechanics and using them in FEA software like ANSYS. | It is totally solid mechanics and finite elements and solving problems using coding or numerical methods. |
Is Finite Element Analysis Difficult?
Knowing the full background theory and equations for performing the FEA analysis is really a difficult and time-consuming job. However, the application of FEA software is quite simple. All the required algorithms and equations are already fed into the software. So, FEA software is also similar to other stress analysis software.
Online Courses on Finite Element Analysis
To develop your strength in finite element analysis you can opt for the following online courses
I can see how a business could really benefit from getting the right kind of consulting in order to be safer. Getting some help from a professional would allow them to be more effective with their data. It was interesting to learn about how the two pumps are combined with the right kind of flexibility.