What is Hot Sustained Stress?
In Layman’s terms, Sustained means always present. So sustained stresses are the stresses which are present in the system throughout its operating cycle. The weight of the piping system and Pressure inside the pipe are examples of sustained loads that generate sustained stresses in the system. So what is a hot sustained case?
While analyzing a piping system, many times you will come across some supports which will take a load in sustained cases but are not taking a load in operating and design temperature cases (Refer to Attached Fig. 1 and Fig. 2 for one such typical example). The support is lifting at that point in temperature case i.e. supports are not contributing to load and stress distribution while in operating condition. Still in that situation, the weight of the pipe and pressure inside the system will induce sustained stresses. So in my opinion, hot sustained stress is the sustained stress in pipe operating situations. And we must ensure that the system stress will not fail because those supports not sharing any load. That is why many organizations make it mandatory to check sustained stresses.
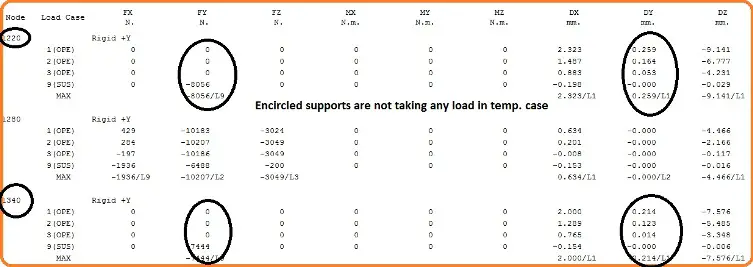
Methods of Hot Sustained stress checking
I have come across two different methods of hot sustained stress checks in the various organization based on old philosophy:
1. Conventional Method of Hot-Sustained Check
- In the first method, the analyst has to run the static analysis as per the conventional method.
- Now go to the restraint summary and note down the support nodes which are lifting or not taking any vertical load (Sometimes small positive value may be there due to guide and line stop frictions, in that case, check the vertical displacement if it shows positive value consider the same as lifting).
- Make a separate Caesar file with the name FILE NAME_HOT SUSTAINED.
- Open the input screen and delete all lifting supports from the nodes you noted down. Delete only +Y support, Guide and line stops will be there.
- Run the analysis and check sustained stress.
- If sustained stress is within allowable limit accept the file as it is else change the support location or routing to make the system safe.
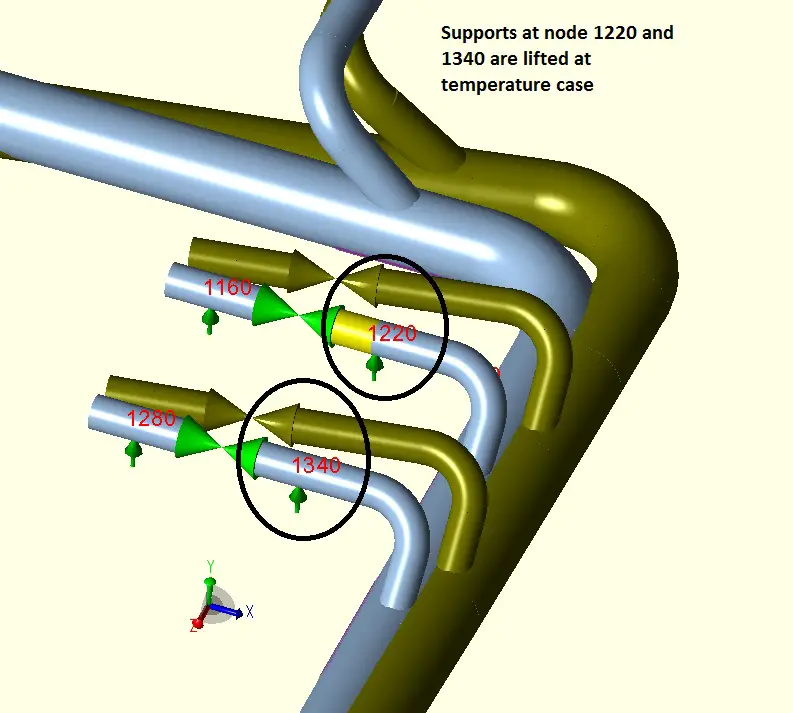
2. Second method of Hot Sustained Checking
- In this method, the analyst will check the hot sustained stress in the same main file (No need to create a separate file). Some additional load cases are required. Let’s assume we will check hot sustained stress in design temperature, T1 condition (means we will check which supports are lifting in design temp case). So the below-mentioned cases are required for hot sustained stress checking
L1: W+T1+P1 OPE
L2: T1 OPE/EXP
L3: L1-L2 SUS
- Check the stresses for load case L3, if the same is within the allowable limit then accept the file else make the system safe.
3. Hot Sustained Check Philosophy from Caesar II 2018 version onwards:
From Caesar II version 2016 onwards, based on code requirements they have created a load case type known as ALT-SUS. So, in the single file, by adding ALT-SUS load cases, Caesar II automatically calculates hot-sustained stresses for each operating condition. Refer to Fig. 3 below to understand the load cases which has been introduced from ASME B 31.3-2014 onwards as Alternate sustained stress checking.
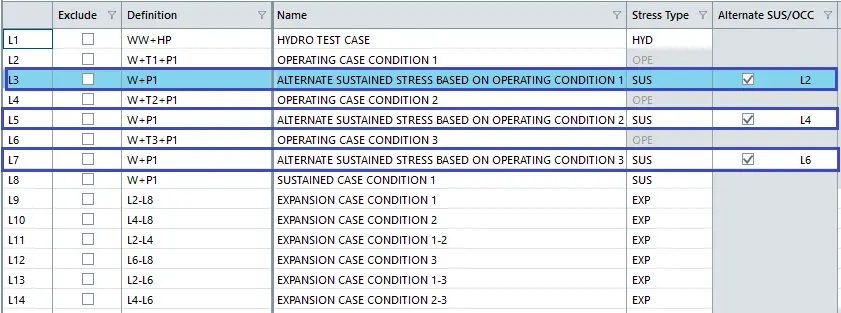
So, the above stresses are sufficient for hot-sustained stress checking. Load case L3 is checking sustained stress for temperature T1; which means in load case L3 all supports which are lifting or not taking load will be removed by the software automatically and sustained stress will be calculated after that. A similar situation will arise for load cases L5 and L7 as shown above and they are the hot sustained cases with respect to temperature cases T2 and T3 respectively.
Notes:
- Now you may be thinking about whether to mark deleted supports in isometric or not. You must mark those supports. As we have not deleted the supports in actual practice. Supports will be there at site, We simply ensured that without those supports also the system will be safe. However, if you want to delete those supports that can be done if all other stress criteria can be met.
- Whether we need to check expansion stresses in a hot sustained file too? In my opinion, if we are using liberal stress for expansion stress range checking then it is better to check expansion stress (along with sustained stress) in the hot sustained file. Otherwise, it is not required as the system won’t fail in an expansion cases even after removing those supports.
Neither the “traditional” approach nor the “new method” are valid from a mathematical or engineering standpoint. The traditional approach overlooks a very obvious and important aspect of load distribution in a nonlinear analysis, and that is the fact that piping loads can redistribute significantly without completely lifting off. A pipe support which supports 4,000 lbs in ambient condition may support only 500 lbs under W+T1. It didn’t “lift off”, but the weight redistribution was significant, and traditional approach ignores this.
The new method is similarly flawed. Linear algebraic subtraction between nonlinear load cases is invalid.
I agree with Mikey. In my opinion, if the pipe is lifting off support by less than 3 mm, ignore displacement it, And if the lift is more than 3 mm, either adjust support location or use spring.
I agree that the approach may not be (structurally) valid but that’s not the point. There are piping codes that have the engineer review stress due to sustained loads for every support configuration that may occur (e.g., B31.3). This article reviews two methods addressing this code requirement.
I like Prasad’s 3mm check but that number could be argued.
We have always considered a change in restraint configuration and stress redistribution to be associated with the thermal component in such evaluation; “L1-L2” is the way to go.
A good engineer should be able to determine when these extra analyses are actually necessary.
One note on method two – this method is incomplete where friction is considered.
How about
L1 W+P1+T1
L2 W+P1
L3 L1-L2
L4 L1-L3
Which will take care of non linearity issue.
I tried to set load cases as Raghavendra explained
L1 W+P1+T1 (OPE)
L2 W+P1 (SUS)
L3 L1-L2 (algebric) (EXP)
L4 L1-L3 (algebric) (SUS)
but I obtain the same result when I use the tradional load cases
L1 W+P1+T1 (OPE)
L2 W+P1 (SUS)
L3 L1-L2 (EXP)
In both cases +Y support are not removed.
Could you tell me where I’m wrong?
What is the limit on hot sustained stresses in piping system?
the stresses shall be less than Sh.
When there is a lift up at a support location due to expansion load and you need to relocate the support. Does one have to reduce the support span by moving the support closer or increase the support span by moving the support away. Please advise what is the best practice.
We can just create an alternate sustained load case as W+P5 if t5 is the design temperature.
Better make a video on this example
Hi,
Thank you for your post. As you mentioned code has a method to check piping stresses for the support lifting case, however you didn’t address equipment nozzle loads failure in case of support lifting. i.e, for the supports near a vertical vessel where heavy valves are supported , once the equipment expands with the operating temperature in vertical direction, it lifts the piping/valves from the adjacent support , so the weight will impose excessive moment to the nozzle of the equipment. Can you elaborate the best way to deal with it. Unless we don’t model the vessel with the operating temperature, this support lifting happens during operation.
Dear Anup,
I have one question about the normale SUS case.
Usually: SUS=W+P.
As we can see no temperature here.
My question at which temperature CAESAR will consider the pipe stress? at 20°C?
Thank you in advance.
Munif JOURIEH
0033620855722
ambient temperature
How do we calculate hot sustained stresses?
Thanks for explanation. I do not understand an issue: if we have an uplift of pipe at +Y support in operating case W+P1+T1 and obtain a calculated Y restrain load zero at that support, I do not think Caesar II calculates stress and deformation keeping the presence of that support. So I think to remove the support is useless. Where I am wrong?
Can anyone challenge below?
1. Why just one case W+P1+T1 (checked in SUS) does not address issue of hot sus stress? (I believe it accurately simulates hot displaced condition with dead load distribution in hot condition)
I believe if the system does not have hold down support(which is seeing positive load) then above case is accurate enough.
On the other hand, if there’s a hold down (which sees positive load), then we have dead load distribution with hold down reaction loads. in both the cases we see accurate simulation of load distribution as long as system is in elastic range. Please share your views.