When thinking of materials for high performance in rigorous applications, the name of Inconel material automatically comes to mind. As the Inconel material is very expensive, the use is of limited nature. Because of this Inconel material is generally less familiar as compared to Steel or Aluminum. In this article, we will explore some basics of this unique nickel alloy.
What is Inconel?
Inconel materials are nickel-chrome-based superalloys. Inconel has high corrosion resistance, oxidation resistance, strength at high temperatures, and creep resistance. Inconel is able to withstand elevated temperatures and extremely corrosive environments.
The term “Inconel” is a registered trademark of Special Metals Corporation, USA. In 1932, the first Inconel alloy was formulated.
Composition of Inconel Alloy
The chemical composition of Inconel material varies with grade. As this is a nickel alloy, the Nickel percentage is more. Other elements present in Inconel alloy material are:
- Chromium
- Iron
- Cobalt
- Molybdenum
- Titanium
- Niobium
Refer to table 1 below which provides the chemical composition of some of the common Inconel material grades (Reference: https://en.wikipedia.org/wiki/Inconel). All values of elements are provided in mass %.Inconel Grade Nickel (Ni) Chromium (Cr) Iron (Fe) Molybdenum (Mo) Niobium (Nb) & Tantalum(Ta) Cobalt (Co) Manganese (Mn) Copper (Cu) Aluminum (Al) Titanium (Ti) Silicon (Si) Carbon (C) Sulphur (S) Phosphorous (P) Boron (B) 600 ≥72 14-17 6-10 – – – ≤1.0 ≤0.5 – – ≤0.5 ≤0.15 ≤0.015 – – 617 44.2–61 20-24 ≤3 8-10 – 10-15 ≤0.5 ≤0.5 0.8-1.5 ≤0.6 ≤0.5 0.05-0.15 ≤0.015 ≤0.015 ≤0.006 625 ≥58 20-23 ≤5 8-10 3.15-4.15 ≤1 ≤0.5 – ≤0.4 ≤0.4 ≤0.5 ≤0.1 ≤0.015 ≤0.015 – 690 ≥58 27-31 7-11 – – – ≤0.5 ≤0.5 – – ≤0.5 ≤0.05 ≤0.015 – – Nuclear grade 690 ≥58 28-31 7-11 – – ≤0.1 ≤0.5 ≤0.5 – – ≤0.5 ≤0.04 ≤0.015 – – 718 50–55 17-21 Balance 2.8-3.3 4.75-5.5 ≤1.0 ≤0.35 ≤0.3 0.2-0.8 0.65-1.15 ≤0.35 ≤0.08 ≤0.015 ≤0.015 ≤0.006 X-750 ≥70 14-17 5-9 – 0.7-1.2 ≤1.0 ≤1.0 ≤0.5 0.4-1.0 2.25-2.75 ≤0.5 ≤0.08 ≤0.01 – –
Properties of Inconel Material
Inconel is characterized by its ability to withstand very high temperatures. Inconel alloy maintains excellent strength even at elevated temperatures. A thick and stable protective oxide layer is formed when heated which provides excellent corrosion resistance even at high temperatures. For very high-temperature applications when steel material succumbs to creep, Inconel material is an ideal choice.
The main reason for Inconel’s very high-temperature resistance is due to the formation of an intermetallic compound Ni3Nb in the gamma double prime (ɣ’’) phase. This intermetallic phase acting as a ‘glue’ on the grain boundaries, prevents the grains from increasing in size when heated to high temperatures. Gamma prime forms small cubic crystals that inhibit slip and creep effectively at elevated temperatures.
The Mechanical and Physical properties of Inconel alloy 625 are provided below in Fig. 1:
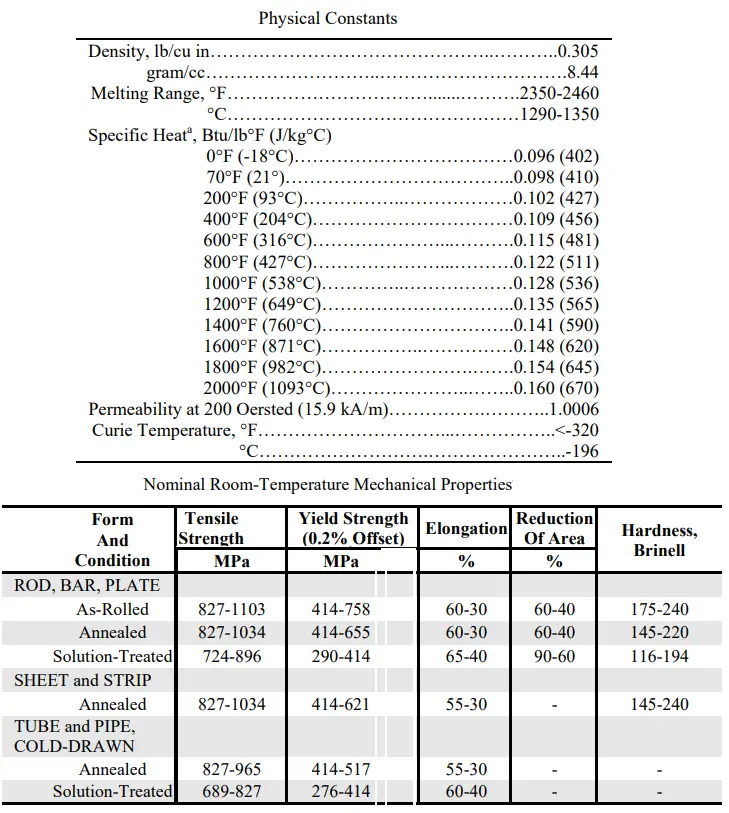
Inconel Alloy Material Grades
Inconel material has a variety of grades varying in composition and properties developed for specific applications. The common Inconel grades are as follows:
- Inconel 188: Used widely for commercial gas turbine and aerospace applications.
- Inconel 230: Used mainly by the power, aerospace, chemical processing, and industrial heating industries.
- Inconel 600: Solid solution strengthened.
- Inconel 601
- Inconel 617: Used in ASME Boiler and Pressure Vessel Code for high-temperature nuclear applications such as molten salt reactors.
- Inconel 625: Acid resistant, good weldability.
- Inconel 690: For nuclear applications, and low resistivity
- Inconel 706
- Inconel 713C: It is a precipitation hardenable nickel-chromium base cast alloy.
- Inconel 718: This alloy is a gamma double prime strengthened with good weldability.
- Inconel X-750: Widely used for gas turbine components, blades, seals, and rotors.
- Inconel 751: Increased aluminum content for improved rupture strength in the 1600 °F range.
- Inconel 792: Added with increased aluminum content for improved high-temperature corrosion-resistant properties, used especially in gas turbines.
- Alloy 825
- Inconel 907
- Inconel 909
- Inconel 925: Inconel 925 is a nonstabilized austenitic stainless steel with low carbon content.
- Inconel 939: Gamma prime strengthened to increase weldability.
Applications of Inconel Material
INCONEL alloy is designated as UNS N06625, Werkstoff Number 2.4856, and ISO NW6625. The NACE MR-01-75 standards list Inconel material. The Inconel material products are manufactured in all standard mill forms including rod, bar, wire, wire rod, plate, sheet, strip, shapes, pipes, tubular products, and forging stock.
The most widespread application of Inconel alloys is found in the aerospace industry. The space shuttle, Rocket engines, 3D printing technology, etc use Inconel. The nuclear industry also uses a lot of various Inconel grades. Other uses of Inconel alloys include:
- Jet Engines
- Fuel Nozzles
- Engine Components
- Afterburner Rings
- Saltwater marine applications
- Oil and Gas extraction
- Industrial Processing
- Pharmaceutical Industry
Inconel vs Monel
Both Inconel and Monel have Nickel as their primary element. However, there are many differences between the two nickel alloys. The main differences between Inconel and Monel are provided in Table 2 below:Parameter Inconel Monel Definition Inconel is a nickel-chromium based superalloy Monel is Nickel-copper based alloy Maximum Nickel Content Inconel roughly has 72% nickel in the base material. Monel has around 67% nickel in the composition. Price Inconel is more expensive than Monel. Monel is relatively cheaper than Inconel. Elevated temperature corrosion resistance properties Inconel has superior corrosion resistance properties at elevated temperatures. At lower temperatures, the corrosion resistance of Monel is preferred because of its low cost. Melting Point Range 2500 to 2600 Deg F 2372 to 2462 Deg F Density 8.8 gm per cubic cm 8.22 gm per cubic cm Hardness Harder Relatively softer. Temperature range The maximum temperature range is 2200 Deg F The maximum temperature range is 1000 Deg F Strength The strength of Inconel is higher than Monel. Lower
Why Alloy 825 (UNS N08825) not listed. It is also a Inconel Material.
is an austenitic nickel-iron-chromium alloy with additions of molybdenum, copper and titanium.
Added
Hi,
I believe monel has better performance than inconel in see water ( salt water )
Are you agree?
Would you please have a compare between incinel and hestalloy too?
Fhanks