Magnetic Particle Inspection (MPI) is one of the most widely used non-destructive inspection methods for locating surface or near-surface defects or flaws in ferromagnetic materials. MPI is basically a combination of two NDT methods: Visual inspection and magnetic flux leakage testing. Developed in the USA, magnetic particle inspection is extensively used to detect defects in the casting, forging, and welding industries.
MPI is simple, easy, fast, and very effective. This is the reason the Magnetic particle test is used in a variety of industries like automotive, oil & gas construction, chemical, and petrochemical plant construction, structural steel, aerospace, offshore structures, power generation industries, and pipeline industries. This is also known as the magnetic particle test or magnetic particle examination in NDT.
Basic Principle of Magnetic Particle Inspection
MPI uses magnetic fields and magnetic particles for detecting defects in ferromagnetic components. The basic principle of this inspection method is that the component specimen is magnetized to generate magnetic flux in the material which travels from the north pole to the south pole (magnetic flux exits at the north pole and enters at the south pole). Now if there is any discontinuity or flaws in the component, secondary magnetic poles are produced in the cracked faces. In this location, the magnetic field spreads out due to the air gap in the defect causing a magnetic flux leakage field. Such regions can be detected easily by using magnetic particles (iron powder), or a liquid suspension on the surface. Due to the magnetic effect, such particles are attracted to the flux leakage and make a cluster around the flaw making it visible. Refer to Fig. 1 showing the basic principle of magnetic particle inspection.
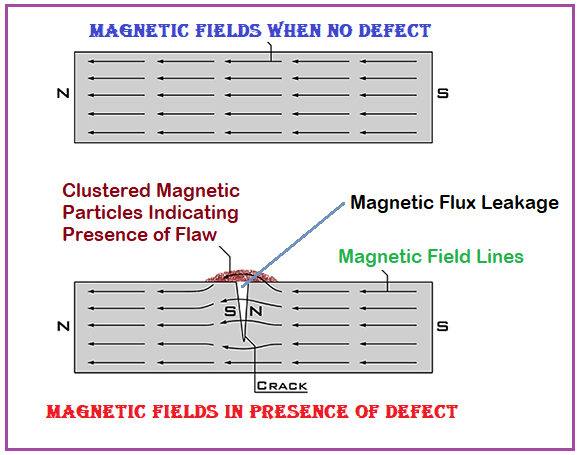
The magnetic particles can be dry or wet. Normally, dry particles can be used up to a temperature of 316 Deg C wet particles can be used up to a temperature of 50 Deg C.
Steps for Magnetic Particle Inspection
The magnetic particle inspection (MPI) is performed in the below-mentioned six steps.
1. Surface Preparation:
All surfaces and adjacent areas (within 1 inch) that will be examined must be free from rust, scale, sand, grease, paint, slag, oily films, or other interfering conditions. Unusually rough or non-uniform surfaces may interfere with magnetic particle cluster formation making interpretations of the magnetic particle inspection method’s indications difficult.
2. Inducing a Magnetic Field:
This is the most important step in the magnetic particle inspection procedure. In this step, place the equipment on the area to be tested and induce a magnetic field. Various types of magnetic particle inspection equipment are available. Widely used industrial equipment are Permanent magnets, Electromagnetic Yokes, Current flow probes, Magnetic Flow, Flexible coils, Threading bars, Adjacent cables, etc. The magnetization technique can be Longitudinal, Circular, or Multidirectional Magnetization. Equipment spacing in the inspection area is normally kept in between 3 inches to 8 inches. An ASME Pie Gauge or Burmag Castrol strip can be used to verify adequate magnetization of the part.
3. Applying Magnetic Particles on the Test Surface:
Both dry and wet magnetic particles can be either fluorescent or non-fluorescent (visible, color contrast) and are available in a variety of colors to contrast with the tested material. So accordingly choose the required particles for the magnetic particle inspection and apply them on the surfaces when the specimen is in magnetized condition.
4. Examine the component surface for defects
Remove the excess particles using light airflow and inspect the component for defects as per acceptable standards.
5. Repeat the test by changing the magnetic field
Two separate examinations are carried out on each area to be tested. The second examination is performed with the lines of flux perpendicular to those used for the first examination in that area.
Refer to Fig. 2 which shows the above 5 steps. An electromagnetic Yoke is used in the test to inspect the welding of two plates.
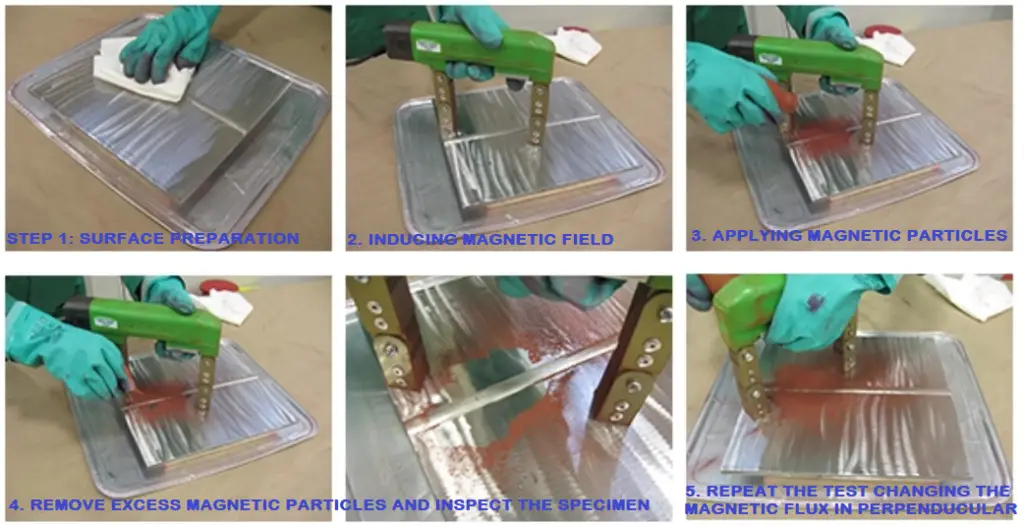
6. Demagnetization and Cleaning:
The presence of Residual magnetism in the component may interfere with the subsequent usage. Hence, the demagnetization shall always be performed on the parts once the magnetic particle inspection is over. The presence of residual magnetism can be verified using a calibrated Gaussmeter, Magnetic Field Meter, or a hall Probe Gauss meter. Residual magnetism must not exceed (+/-) 2 gausses.
After that, the parts shall be cleaned to remove all residual magnetic particle materials. If wet fluorescent MPI was performed, the part shall be scanned with the backlight to assure that the cleaning is adequate.
Advantages of Magnetic Particle Inspection/Test
The main advantages of magnetic particle inspection/testing are
- Find flaws on the surface and near surfaces
- Fast examination method with an immediate result
- This is an easy method as compared to other NDT methods
- Portable and low-cost equipment.
- Defects are visible directly on the surface.
- Relatively safe method.
- Hot testing can be performed using dry particles.
- The shape and size of the cracks are indicated.
- Less training requirements.
Disadvantages of Magnetic Particle Inspection
The major drawbacks of magnetic particle inspection/examination are
- MPI is limited only to ferromagnetic materials like steel, cast irons, etc. Non-ferrous materials, cannot be inspected.
- The inspection is limited to small sections only. The examination of large parts may require the use of special equipment.
- Equipment must be calibrated, with no permanent record of the result.
- Before inspection thick paints (>0.005″) shall be removed.
- Post-cleaning and demagnetization are normally required.
- Magnetic flux and indications must be aligned for proper results.
- Access may be a problem for the magnetizing equipment.
- Testing in two perpendicular directions is required.
Codes and Standards for Magnetic Particle Inspection
Normally ASME Section V: Nondestructive Examination governs the magnetic particle inspection/examination methods for most organizations. However, there are various other codes and standards that provide guidance rules for magnetic particle test procedures as listed below
ISO (International Organization for Standardization) Standards for MPI
The following ISO standards govern the inspection by MPI.
- ISO 3059, Non-destructive testing – Penetrant testing and magnetic particle testing – Viewing conditions
- ISO 9934, Part 1, Part 2, and Part 3– Non-destructive testing – Magnetic particle testing – Part 1: General principles, Part 2: Detection media, Part 3: Equipment
- ISO 10893-5-Non-destructive testing of steel tubes. Magnetic particle inspection of seamless and welded ferromagnetic steel tubes for the detection of surface imperfections
- ISO 17638, Non-destructive testing of welds – Magnetic particle testing
- ISO 23278, Non-destructive testing of welds – Magnetic particle testing of welds – Acceptance levels
European Committee for Standardization (CEN) Standards for MPI
- EN 1330-7, Non-destructive testing – Terminology – Part 7: Terms used in magnetic particle testing
- EN 10246-12, Non-destructive testing of steel tubes – Part 12: Magnetic particle inspection of seamless and welded ferromagnetic steel tubes for the detection of surface imperfections
- EN 1290, Surface Crack Testing
- EN 1369, Founding – Magnetic particle inspection
- EN 10228-1, Non-destructive testing of steel forgings – Part 1: Magnetic particle inspection
- EN 10246-18, Non-destructive testing of steel tubes – Part 18: Magnetic particle inspection of the tube ends of seamless and welded ferromagnetic steel tubes for the detection of laminar imperfections
ASTM (American Society of Testing and Materials) Standards for magnetic particle inspection
- ASTM E1444/E1444M Standard Practice for Magnetic Particle Testing
- ASTM E 1316 Terminology for Nondestructive Examinations
- ASTM A 275/A 275M Test Method for Magnetic Particle Examination of Steel Forgings
- ASTM E543 Practice Standard Specification for Evaluating Agencies that Performing Nondestructive Testing
- ASTM E 709 Guide for Magnetic Particle Testing Examination
- ASTM A456 Specification for Magnetic Particle Inspection of Large Crankshaft Forgings
- ASTM E 2297 Standard Guide for Use of UV-A and Visible Light Sources and Meters used in the Liquid Penetrant and Magnetic Particle Methods
The United States Military Standard: A-A-59230 Fluid, Magnetic Particle Inspection, Suspension
CSA (Canadian Standards Association) Standards: CSA W59 Welded steel construction
MPI Standards of Society of Automotive Engineers (SAE)
widely used MPI standards from the society of Automotive Engineers are listed below:
- AMS 3040 Magnetic Particles, Nonfluorescent, Dry Method
- AMS 2641 Magnetic Particle Inspection Vehicle
- AMS 3045 Magnetic Particles, Fluorescent, Wet Method, Oil Vehicle, Ready-To-Use
- AMS 5355 Investment Castings
- AMS 3041 Magnetic Particles, Nonfluorescent, Wet Method, Oil Vehicle, Ready-To-Use
- AMS 3043 Magnetic Particles, Nonfluorescent, Wet Method, Oil Vehicle, Aerosol Packaged
- AMS 3042 Magnetic Particles, Nonfluorescent, Wet Method, Dry Powder
- AMS 3044 Magnetic Particles, Fluorescent, Wet Method, Dry Powder
Magnetic Particle Inspection Equipment
During magnetic particle examination, various kinds of equipment are required as listed below:
- Electromagnetic Yokes
- Magnetic Benches
- Power Packs & Mobile Test Units
- Demagnetising Units
These magnetic particle inspection equipment should be designed to be durable, fast, and reliable. Refer to Fig. 3 which shows a few of the magnetic particle test equipment.
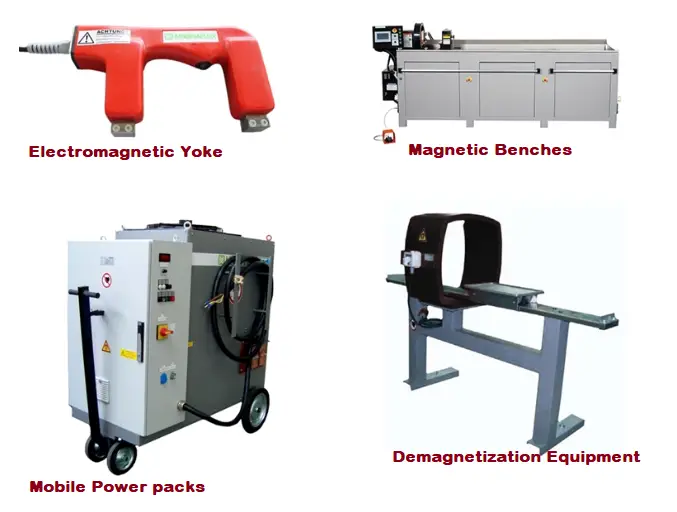
Code Acceptance Criteria for Magnetic Particle Inspection
As per ASME Sec VIII Div 1 and Div 2, all surfaces examined by magnetic particle inspection shall be free from
- Linear indication
- Rounded indication with size greater than 3/16 inches.
- Four or more rounded indications in a line separated by 1/16 inch or less.
- Crack-like indications, irrespective of surface condition.
As per ASME B31.3, any cracks or linear indications are unacceptable.
Magnetic Particle Inspection/Testing Questions
The following pdf link provides a few sample questions for examinations for level 1 and level 2. Go to page no 46 directly to prepare answers for magnetic particle testing questions. Click here to open the pdf and start preparing.
I really love to study this site…. I got clearly answer for every questions.. Thank you
THANKS,
Simple & clear.
Hello Good day, what is due date for next inspection date for MPI.Is it mention in any code like one year or two year.
good really wonderfull
Hello,
Having a new and different problem, in all my years I have never given this enough thought.
Does the case for a 5 turn coil need to be electrically conductive, non-conductive or does it matter. I have always made sure that the cable itself was insulated but not the case.
Thanks,
We are doing Magnetic Particle Test by Black Light Method.
anybody can suggest the particular coverall or suit to wear the operator for protector their body?
Hi,
Should MPI be on full lot size quantity or sample of of lots?
below 2 inche can do mpi ?
how many inches can do mpi ?