A welding position is a technique by which a welder joins the metals in positions or angles. The welding position is very important as it affects the flow of molten filler material. It’s desirable that the welding operator understands the types of welding positions to smoothly accomplish the task. Also, at a certain position of the welder different welding processes are performed. In this article, we will learn about the common welding positions used in the industrial application of welding.
The guidelines and limitations regarding welding positions in WPS are covered in Section IX of the ASME Boiler and Pressure Vessel Code.
Types of Welding Positions
Some welding processes can be performed at all positions; while some are possible in one or two positions only. According to the positions of the welding joint on sections, the American Welding Society (AWS) and ASME define four types of welding positions. They are
- Flat welding position
- Horizontal welding position
- Vertical welding position, and
- Overhead welding position
The welding position is defined by a number (1 to 6) followed by one letter from F, G, or S. Here, the letter “F” stands for fillet welding, “G” denotes Groove welding, and “S” refers to Stud welding.
The numbers denote welding positions as follows:
- “1” indicates a flat position. For example, 1F, 1G or 1S
- “2” refers to a horizontal welding position; Example 2F, 2G or 2S
- “3” denotes a vertical position; for Example 3F or 3G
- “4” denotes an overhead position; for Example, 4F, 4G, or 4S.
- Letters “5” and “6” are specifically used for piping welding positions in a horizontal fixed position and inclined position respectively. Pipe welding positions will be discussed toward the end of the article.
The following table shows the various welding symbols for welding positions used for different types of welding methods
Welding Position Symbol | Welding Position | Weld Type |
1 F | Flat position | Fillet weld |
1 G | Flat position | Groove weld |
1S | Flat position | Stud Weld |
2 F | Horizontal position | Fillet weld |
2 G | Horizontal position | Groove weld |
2S | Horizontal position | Stud Weld |
3 F | Vertical position | Fillet weld |
3 G | Vertical position | Groove weld |
4 F | Overhead position | Fillet weld |
4 G | Overhead position | Groove weld |
4S | Overhead position | Stud Weld |
Welding Positions 1G or 1F (Flat welding positions)
In Flat Welding position 1G or 1F, the welding is done from the top side of the joint. The head of the welder remains above the test coupon and the weld face is approximately horizontal. The flat welding position is easier and faster and the molten metal is drawn downward. A flat welding position is also known as a down-hand welding position.
The following image in Fig. 1 shows the welding positions used during welding.
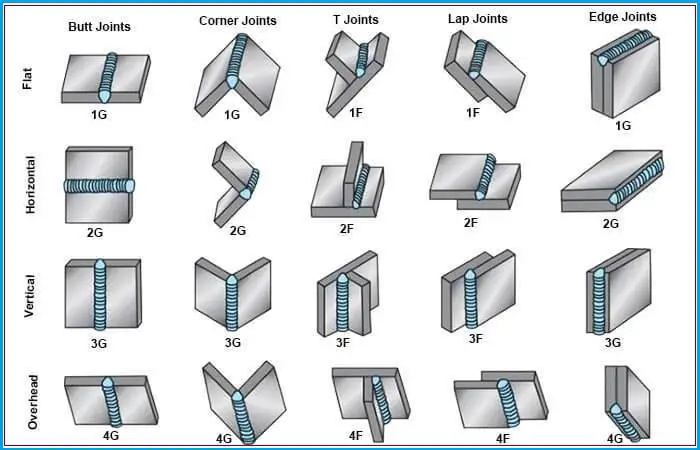
Welding Positions 2G or 2F (Horizontal welding positions)
In the horizontal welding position, the weld axis is almost horizontal. Compared to a flat welding position, this is a more difficult position for welding.
Welding position 2F is for a fillet weld where the welding is performed on the upper side of a horizontal surface and against an approximately vertical surface keeping to welding torch at a 45-degree angle.
Welding position 2G is for a groove weld when the welding face lies in an approximately vertical plane with the weld axis in a horizontal plane.
Welding Position 3G or 3F (Vertical welding positions)
In vertical position welding, the weld axis is almost vertical. Both the weld and the plate will lie vertically. For welding vertical surfaces, the molten metal runs downward by gravity and piles up. Welding in an upward or downhill vertical position can resolve this problem. Also, by pointing the flame upward at around a 45-degree angle to the plate, the metal flow can be controlled. Welding position 3G is used for groove welding and 3F is used for fillet welding.
Welding Position 4G or 4F (Overhead weld position)
When the welding is done from the underside of the joint, it is known as the overhead welding position. It’s the most difficult position for a welder to work and the most complicated one. Welding Position 4G refers to groove welding and 4F indicates fillet welding.
In overhead welding positions, the metal deposited tends to drop or sag on the plate which results in a bead with a high crown. To get rid of this difficulty, the molten puddle should be kept small. When the puddle becomes too large, one can remove the flame momentarily for the molten metal to cool.
Pipe Welding Positions
The above-mentioned welding positions, i.e, flat, horizontal, vertical, and overhead are the most basic types of welding positions used for plate welding. However, these do not completely describe pipe welding positions. As far as pipe welding is concerned, there are four types of piping welding positions. They are:
- Horizontal Rolled Pipe Weld Position 1G
- Vertical Position 2G
- Horizontal Fixed Position 5G, and
- Inclined Weld Position 6G
Pipe Welding Positions 1G
Welding Position 1G is the easiest pipe welding position as the pipe is in a horizontal position. In a 1G pipe welding position, the pipe can be rotated against its horizontal axis (X-axis). The welder performs pipe welding from the top without changing his position while the pipe is slowly rotated manually or by equipment. Pipe Weld Position 1G is the most basic pipe welding.
The image in Fig. 2 below explains all the pipe welding positions.
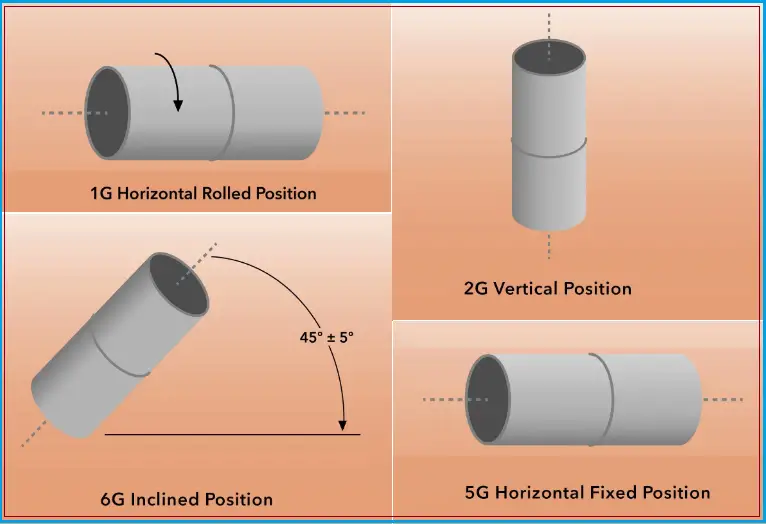
Pipe Welding Positions 2G
In pipe welding position 2G, the pipe will be in the vertical position (Pipe axis in the Y direction) and the weld axis in the horizontal direction. The welder performs the welding from the side by remaining stationary or moving around the pipe. The welding method is easy in the case of a 2G pipe welding position and is most frequently welded by the backhand method.
Welding Positions 5G
Pipe welding position 5G is a weld position where the pipe axis is fixed in a horizontal position and the operator weld vertically either downward or upward. In this welding position, the pipe is kept fixed and can not be rotated, unlike 1G welding. 5G welding position is difficult as the pipe can not be rotated.
Welding Positions 6G
In pipe welding position 6G, welding is performed in a sloping pipe. The pipe slope is normally 45 degrees from a horizontal or vertical axis. 6G welding positions, being the most difficult pipe welding positions, require certified and highly experienced welders. The pipe remains fixed and the operator needs to move around the pipe for welding. This is the most challenging and complex pipe welding position for welders.
There is another form known as 6GR where welding is done in a ring mode by placing a steel plate below the weld with a 1-inch gap. This requirement comes while welding pipes near impediments like walls, brackets, or other structures.
Comparisons of welding positions between ISO standard and ASME / AWS standard
Sometimes, the weld positions by professional organization ISO are found in industries. The weld position nomenclature in the ISO system is a bit different. The following table provides a comparison between ISO and AWS standard welding position symbols.
AWS Welding Position | ISO Welding Position |
1G / 1F | PA |
2F | PB |
2G | PC |
4F | PD |
4G | PE |
3G Uphill | PF |
3G Downhill | PG |
5G Uphill | PH |
5G Downhill | PJ |
6G Uphill | H-L045 |
6G Downhill | J-L045 |
Why care about Pipe Welding Positions?
Welding position is one of the most important variables that determine weld quality. For each pipe weld position, welders need to undergo certification processes. If a welder is qualified to weld in a 1G position, he is not allowed to weld hard positions like the 6G position. But on the other hand, if the welder is certified for the hardest 6G position then he can work in the 1G position. So, expertise in each weld position levels up a welder’s skills and qualifications.
Frequently Asked Questions related to Welding Positions
- What are the 5 welding positions?
As described above, the 5 major welding positions widely used in the welding industry are flat weld, horizontal weld, overhead weld, vertical weld, and piping weld. These welding positions are designated by a number and followed by a letter. - What are 5G and 6G welding?
Weld positions 5G and 6G are pipe welding positions. The 5G is welding in a horizontal fixed position whereas the 6G is welding in an inclined fixed position that is about 45 degrees. Refer to Fig. 2 above for a proper understanding of the 5G and 6G welding positions. - How much does a 6G welder make in the United States?
The salary of welders depends on various factors like the experience of the welder, demand and supply, etc. However, in general, the salary of a 6G welder in the United States varies between $30, 000 to $67,000 per year. - Which position is advantageous for easy welding?
The horizontal welding position is the easiest, safest, and most ergonomic for a welder. - How hard is 6G welding?
The 6G pipe welding is one of the most difficult weldings as the pipe is at a 45-degree angle and immovable. So, only experienced and certified 6G welders can perform these jobs efficiently at the construction site.
Few more welding articles for you.
Welding Galvanized Steel
Overview of Pipeline Welding
Welding Positions: Pipe Welding Positions
Welding Defects: Defects in Welding: Types of Welding Defects
Welding Inspector: CSWIP and AWS-CWI
General requirements for Field Welding
Underwater Welding & Inspection Overview
Methods for Welding Stainless Steel
Video Courses in Welding
To learn more about welding the following video courses you can refer to:
does 2G & 3G qualified welder can be considered for 5f Position?
Your knowledge is superior.
Please add 6GR Position.