Pipelines are used to transport gas, water, oils, and other liquids from one point to the other. And as all pipes are produced at a fixed length, there is a requirement of welding to join pipes and make kilometers of pipelines. So, pipeline welding is a very important activity in pipeline construction and is always a demanding profession. Pipe and Pipeline welders are required in construction industries, oil and gas fields, water industries, fabrication shops, nuclear energy industries, etc to lay new pipelines or repair an old pipe.
Pipeline welding is popular as girth welding which is performed along the circumference of the pipes to be connected. As compared to pipe welding in usual plants, pipeline welding poses various additional challenges. Pipeline welding should conform to the relevant ASME codes like B31.4, B31.8, ASME BPVC, etc.
Note that there is a specific difference between pipe welding and pipeline welding. Pipe welding normally refers to the welding of pipes inside chemical plants and oil refineries. Inside the plant a varying range of pipe sizes and materials require welding. On the contrary, pipeline welding concentrates on welding pipes of uniform size and material spread over hundreds of kilometers.
Widely used Pipeline Welding Processes
Usually, the following types of welding processes are widely used for pipeline welding:
- Shielded Metal Arc Welding
- Gas Metal Arc Welding
- Flux-Cored Arc Welding
- Submerged Arc Welding
- Gas Tungsten Arc welding
Pipeline Welding by Shielded Metal Arc Welding (SMAW)
Shielded Metal Arc Welding of pipelines is also known as Stovepipe welding. In SMAW the pipelines are welded by melting the electrodes with the heat generated by an electric arc. The number of passes required usually varies with the pipe thickness, electrode size, welding position, and the current used for pipeline welding. The usual thumb rule for pipeline welding by SMAW is to consider one pass for each 1/8 inch(3.2 mm) of pipe thickness. Electrode diameters for SMAW pipeline welding normally vary from 1/8 inch to 3.16 inches (3.2 mm to 4.8 mm).
The main advantage of pipeline welding by SMAW is that the welding equipment is simple and portable. Also, no flux or shielding gases are required during welding. However, the productivity of this method is less due to lower travel speed.
Pipeline Welding by Gas Metal Arc welding (GMAW)
Pipeline welding by gas metal arc welding provides high productivity as compared to the SMAW method But this method required better control of welding variables for efficient quality work. High deposition efficiency (90 to 97%) with low fume generation are advantages of GMAW. This is generally performed using semi-automatic/ automatic equipment and the welding cost is increased.
Pipeline Welding by Flux-cored Arc Welding
Gas Shielded Flux-cored arc welding is performed using semi-automatic machines. Along with high productivity and excellent welding capabilities, pipeline welding by this method provides a broader operating range compared to GMAW. However, the wind usually causes disturbance for the shielding gas which in turn may cause porosity defects.
In the case of self-shielded flux-cored arc welding, external shielding gas is not required. However, this has lower deposition rates as compared to the gas-shielded arc welding process.
Welding of Pipelines by Submerged Arc Welding
In the semi-automatic Submerged arc welding process, the arc is not visible and it provides the highest deposition efficiencies as compared to all other pipeline welding methods. Such welding provides sound, defect-free welding surfaces but tracing is very difficult due to the invisible arc.
Pipeline Welding by Gas Tungsten Arc welding of Tungsten Inert Gas welding
TIG welding is used for welding critical joints requiring precision welds as this method produces high-quality pipeline welding utilizing tungsten electrodes. But, welding of pipelines by gas tungsten arc welding has lower deposition rates and higher equipment costs.
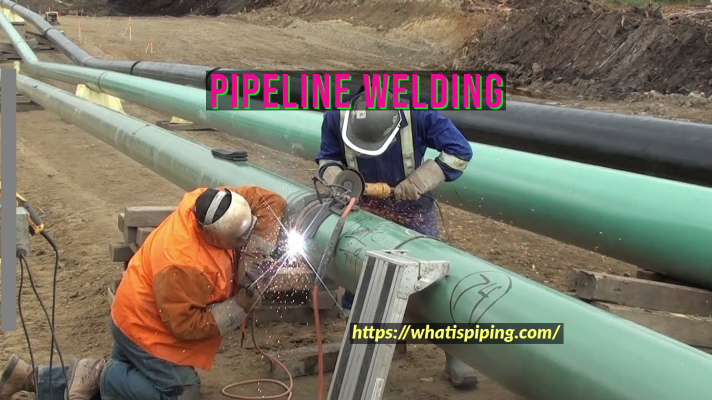
Steps for Pipeline Welding
Usually, the following steps are performed for welding a pipeline:
- Joint Preparation: Usually, guidelines provided in API 1104 are used for joint preparation.
- Pipe End Cleaning: Undesirable moisture, paint, primer, rust, oil, varnish, and other coatings must be removed by cleaning the pipeline ends. Note that, proper cleanliness prevents defect generation leading to rejected welds and costly repair.
- Follow the Welding Process specific to the pipes and pipeline materials (Electrode selection, Preheat requirement, etc). All these details are available in the Project welding specifications.
- Welding the Root Pass
- Welding the Hot Passes
- Welding Fill and Cap Passes
- Repairs in cases of unacceptable defects arise.
Pipeline Welding Process Selection
Pipeline welding is the backbone of pipeline construction. Hence, the pipeline welding process selection must be done, considering various factors as mentioned below:
- Pipeline material
- Pipe Diameter and Wall thickness
- Welding location
- Weldment properties
- Welding Direction (Uphill or downhill)
- Welding quality
- Economic Consideration
- HSE Consideration
Pipeline Welding Machine
Appropriate equipment for welding pipelines is a must for maintaining weld quality and production efficiency. Various parameters must be checked prior to selecting a proper pipeline welding machine such as
- Output power
- Duty cycle
- Portability
- Versatility
- Safety
Pipeline Welding Jobs
Pipeline welding jobs are very demanding with long working hours. A daily review of the pipeline welders’ work is carried out. As the commissioning of the pipelines depends on the pipeline weld completion, pipeline welders always remain under high work pressure. At the same time, the job is unsafe, there are huge chances of accidents happening at any moment. However, all these come with good salaries for pipeline welders. Depending on the experience and skills of pipeline welders they make in the range of $2,000 to $11,000 per month in the USA.
To get into the pipeline welding jobs, a person must have
- High school diploma
- Welding school certificate or completed apprenticeship
- Welding certificate (AWS/CSWIP)
- Prior welding experience (pipeline welding preferred)
- Knowledge of AWS, ANSI, ASME, and API standards
- Experience and working knowledge of using all welding tools and equipment,
- Excellent technical and communication skills
- Ability to interpret schematics
In pipeline welding jobs, a pipeline welder typically is responsible for
- Reading and understanding blueprints, and schematics
- Determining required tools, materials, and welding methods
- Assembling pipe components and systems
- Preparing the materials
- Installing and repairing these systems
- Inspecting and maintaining supplies, materials, tools, and equipment
- Ensuring produced welds are up to specifications
- Following safety procedures and guidelines
Few more welding articles for you.
Welding Galvanized Steel
Overview of Pipeline Welding
Welding Positions: Pipe Welding Positions
Welding Defects: Defects in Welding: Types of Welding Defects
Welding Inspector: CSWIP and AWS-CWI
General requirements for Field Welding
Underwater Welding & Inspection Overview
Methods for Welding Stainless Steel
Video Courses in Welding
To learn more about welding the following video courses you can refer to:
Very good information you shared here
It’s interesting to know about pipeline welding and how their jobs include the inspection and maintenance of materials and equipment. I would understand how equipment upgrades such as using automatic welders can really speed up the production process. Updating equipment should always be in a company’s consideration.
Hello
Thanks for sharing the great information. I read this blog and must say the information that you shared in this blog is really very useful. Please post more such blogs.
Thank You.
This is great information for those looking to learn about pipeline welding! I have been a pipeline welder for 20 years and love how easy your information is to understand. One question I am always asked is what the difference is between pipeline welding and process pipe welding. Mainly in terms of welding vertical down (pipeline) vs welding vertical up (process pipe). People want to know why they can’t weld downhill for process piping. Any clarification would be great!
Thank you and keep up the good work!
Pipeline मे हमेशा downhill welding ही क्यों किया जाता है इसमे root, hot pass, filler camping किस electrode या filler wire से किया जाता है ?
जबाब दे ?
Hi sir,
What is the welding requirement for pipeline??