Piping Elbows are very important pipe fitting which is used very frequently for changing direction in the piping, pipeline, and plumbing systems. They are essential pieces of fittings for routing pipes around obstacles or for creating a more efficient and organized pipe layout. Even though the terms “piping bends” and “piping elbows” are often used synonymously, they are not the same. In this article, we will discuss about:
- Definition of Pipe Elbow
- Types of Pipe Elbows
- Features of Piping Elbow
- Calculating Pipe Elbow Angle
- Significance of Elbow Radius
- Pipe Elbow Minimum Thickness Requirement
- Piping Elbow End Connections
- Pipe Elbow Material Specification
- And many more…
What is a Piping Elbow?
A Pipe Elbow or Piping Elbow is a specific, standard, engineered bend pre-fabricated as a spool piece (based on ASME B16.9) and designed to either be screwed, flanged, or welded to the piping it is associated with. It is a type of pipe fittings. Pipe elbows are usually manufactured to provide a 45-degree or 90-degree direction change from the main pipe direction. There can also be custom-designed piping elbows, although most are categorized as either “short radius” or long radius”.
Types of Piping Elbows
Depending on various piping parameters, pipe elbows can be classified as follows:
Piping elbow types based on direction angle
- 45-degree elbow
- 90-degree elbow
- 180-degree elbow
45-Degree Pipe Elbow:
A 45-degree elbow creates a 45-degree change in direction, providing a slightly less sharp turn than a 90-degree elbow. These types of pipe elbows are preferred when there is space limitation for pipe routing or there is a requirement for a more gradual change in direction to result in less turbulence and pressure drop.
90-Degree Elbow:
This type of elbow creates a 90-degree change in direction, either turning the flow of fluid from horizontal to vertical or vice versa. The majority of piping elbows used in piping or plumbing systems are 90-degree elbows.
180-Degree Elbow:
A 180-degree elbow, also known as a U-bend or return bend, is used to change the direction of a pipe/pipeline by a complete reversal of direction, resulting in a 180-degree turn. Unlike 45-degree and 90-degree elbows, which provide gradual changes in direction, a 180-degree elbow completely flips the direction of flow back on itself. In situations where a complete u-turn of pipe routing is required 180-degree pipe elbows can be used to eliminate the requirement of two 90-degree elbows. In general, they are frequently used in piping/plumbing systems.
Refer to Fig. 1 shows various types of piping elbows
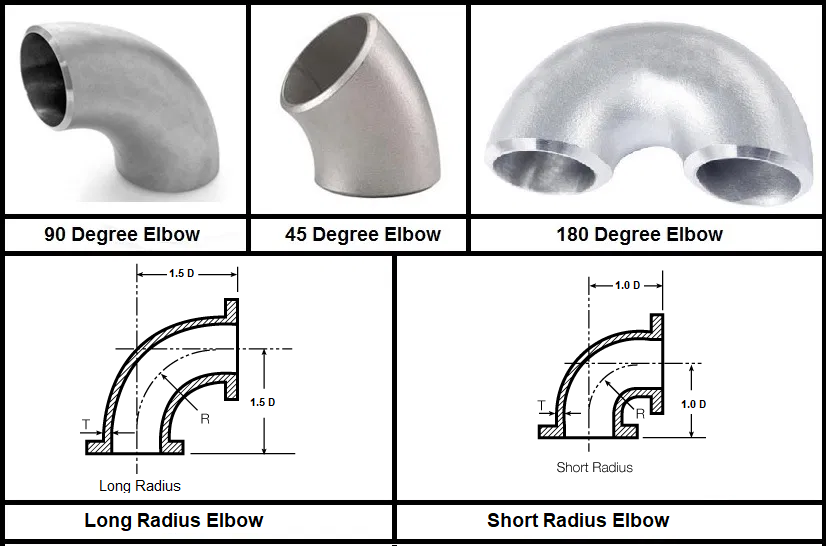
Types of piping elbows depending on bend radius
- Long radius elbow
- Short radius elbow
Long-radius and short-radius pipe elbows differ in terms of their curvature and the radius of the bend.
Long Radius Elbow:
A long-radius pipe elbow has a larger radius of curvature compared to short-radius elbows. The radius of a long-radius elbow is typically 1.5 times the nominal pipe diameter. They provide a more gradual change in direction, resulting in less resistance to fluid flow and reduced pressure drop. Long-radius elbows are often preferred in situations where minimizing flow resistance and maintaining a smooth flow path are important. They are the most widely used piping elbows and are found in applications with higher flow rates, such as in large industrial piping systems or when handling viscous fluids. These elbows are also suitable for applications where space is not a major constraint, as they require more room to accommodate their larger curvature.
Short Radius Elbow:
Short-radius elbows, on the other hand, have a smaller radius of curvature, typically equal to 1.0 times the nominal pipe diameter. They create a sharper change in direction, which can lead to higher resistance to fluid flow and increased pressure drop compared to long-radius elbows. Short-radius elbows are often used in situations where space is limited, and a tighter turn is required to navigate around obstacles or fit within confined spaces. They are usually not preferred by pipe layout engineers or pipe designers but are used when there is limited room for pipe layout routing adjustments. These elbows are commonly found in applications like shipbuilding, process equipment, and tight mechanical rooms.
Piping elbow types considering pipe end connections
- Butt welded piping elbow
- Socket welded piping elbow
- Threaded piping elbow
- Flanged elbow
Butt Welded Piping Elbow:
A butt-welded piping elbow is a type of pipe elbow that is joined to the pipeline through a butt-welding process. Butt welding involves welding the elbow directly to the pipe by aligning the ends of the pipe and the elbow and then fusing them together using heat and pressure. Butt welded elbows are known for their strength and integrity as the weld provides a continuous, leak-resistant joint. They are commonly used in high-pressure and high-temperature piping systems, especially in industrial piping applications. Refer to Fig. 2 below
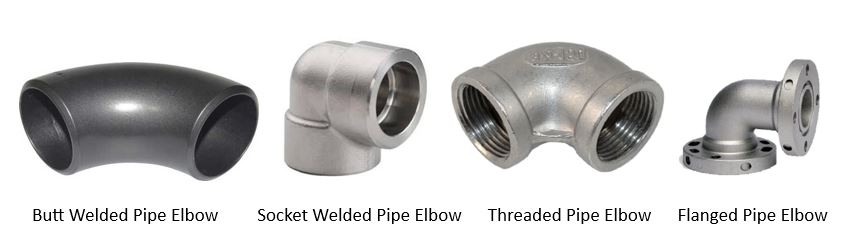
Socket Welded Piping Elbow:
A socket-welded piping elbow is a type of pipe elbow designed to be joined to the pipeline using socket weld connections. In this process, the pipe is inserted into the socket of the elbow, and then fillet welds are applied to secure the joint. Socket welded elbows are suitable for smaller-diameter pipes and are often used in applications where a strong and reliable connection is needed but without the need for complex welding procedures. They are commonly used in low- to medium-pressure piping systems.
Threaded Piping Elbow:
A threaded piping elbow is a pipe elbow with female threads on both ends, allowing it to be screwed onto threaded pipes or fittings with male threads. The connection is made by threading the elbow onto the pipe threads. Threaded elbows are convenient for assembly and disassembly, making them suitable for applications where frequent maintenance or changes to the piping system may be required. They are commonly used in plumbing and lower-pressure industrial piping systems.
Flanged Elbow:
A flanged elbow is a type of pipe elbow with flanges on both ends. These flanges have holes for bolting the elbow to the matching flanges on pipes or equipment. The joint is sealed using gaskets between the flange faces. Flanged elbows are often used in applications where easy assembly and disassembly are necessary, and they are particularly prevalent in large-diameter pipes and systems with higher pressure and temperature requirements. The flange connection allows for a secure and leak-proof joint.
Other Pipe Elbow Types
Reducing Elbow
A reducing elbow is a type of pipe elbow used in piping systems to change the direction of flow while also reducing the pipe diameter or size in the process. It combines the functions of a standard elbow, which redirects the flow, with that of a reducing coupling or adapter, which reduces the pipe size. Reducing elbows are designed to accommodate situations where two pipes of different sizes need to be connected while maintaining the required change in direction. Reducing pipe elbows are in various end connection types, including butt weld, socket weld, threaded, or flanged, depending on the specific requirements of the piping system.
Features of Piping Elbow
Whenever the term piping elbow is used, it must also carry the qualifiers of type (45 or 90 degrees) and radius (short or long) – besides the nominal size.
Elbows can change direction to any angle as per requirement. An elbow angle can be defined as the angle by which the flow direction deviates from its original flowing direction (See Fig. 3 below). Even though An elbow angle can be anything greater than 0 but less or equal to 90° But still a change in direction greater than 90° at a single point is not desirable. Normally, a 45° and a 90° elbow combinedly are used while making piping layouts for such situations.
Calculating Elbow Angle
Elbow angle can be easily calculated using a simple geometrical technique of mathematics. Let’s give an example to you.
Refer to Fig. 4. Pipe direction changes at point A with the help of an elbow and again the direction changes at point G using another elbow.
In order to find out the elbow angle at A, it is necessary to consider a plane that contains the arms of the elbow. If there had been no change in direction at point A, the pipe would have moved along line AD but the pipe is moving along line AG. Plane AFGD contains lines AD and AG and the elbow angle (phi) is marked which denotes the angle by which the flow is deviating from its original direction. Considering right angle triangle AGD, tan(phi) = √( x2 + z2)/y Similarly elbow angle at G is given by: tan (phi1)=√ (y2 +z2)/x
Elbow Radius | Bend Radius
Elbows or bends are available in various radii for a smooth change in direction which is expressed in terms of pipe nominal size expressed in inches. Elbows or bends are available in three radii,
a. Long radius elbows (Radius = 1.5D): used most frequently where there is a need to keep the frictional fluid pressure loss down to a minimum, there is ample space and volume to allow for a wider turn and generate less pressure drop.
b. Long radius elbows (Radius > 1.5D): Used sometimes for specific applications for transporting high viscous fluids like slurry, low polymer, etc. For radius, more than 1.5D pipe bends are usually used and these can be made to any radius. However, 3D & 5D pipe bends are the most commonly used. In the pipeline industry, a piping bend of up to 60D is quite common.
c. Short radius elbows (Radius = 1.0D): to be used only in locations where space does not permit the use of long radius elbows and there is a need to reduce the cost of elbows. In jacketed piping, the short radius elbow is used for the core pipe.
Here, D is the nominal pipe size in inches.
There are three major parameters that dictate the radius selection for the elbow. Space availability, cost, and pressure drop Pipe bends are preferred where pressure drop is of major consideration. The use of short-radius elbows should be avoided as far as possible due to abrupt changes in a direction causing the high-pressure drop.
Pipe Elbow Minimum Thickness Requirement
Whether a pipe elbow or bend is used the minimum thickness requirement from the code must be met. Code ASME B31.3 provides an equation for calculating the minimum thickness required (t) in finished form for a given internal design pressure (P) as shown below:
Here,
- R1 = bend radius of welding elbow or pipe bend
- D = outside diameter of the pipe
- W = weld joint strength reduction factor
- Y = coefficient from Code Table 304.1.1
- S = stress value for material from Table A-1 at the maximum temperature
- E = quality factor from Table A-1A or A-1B Add any corrosion, erosion, or mechanical allowances with this calculated value to get the thickness required.
Pipe Elbow Material Specifications
The material specifications for pipe elbows can vary widely depending on the specific requirements of the piping system, the type of fluid being transported, and the environmental conditions. Different materials offer varying levels of corrosion resistance, strength, and temperature tolerance. Below are some common ASTM material specifications used for pipe elbows:
Carbon Steel Piping Elbows:
- ASTM A234/A234M Standard Specification for Piping Fittings of Wrought Carbon Steel and Alloy Steel for Moderate and High-Temperature Service.
- ASTM A420/A420M Standard Specification for Piping Fittings of Wrought Carbon Steel and Alloy Steel for Low-Temperature Service.
Stainless Steel Pipe Elbows:
- ASTM A403/A403M Standard Specification for Wrought Austenitic Stainless Steel Piping Fittings.
- ASTM A815/A815M Standard Specification for Wrought Ferritic, Ferritic/Austenitic, and Martensitic Stainless Steel Piping Fittings.
Copper and Copper Alloys Pipe Elbows:
- ASTM B16/B16M Standard Specification for Free-Cutting Brass Rod, Bar, and Shapes for Use in Screw Machines.
- ASTM B75/B75M Standard Specification for Seamless Copper Tube.
PVC (Polyvinyl Chloride) Pipe Elbows:
- ASTM D2466 Standard Specification for Poly(Vinyl Chloride) (PVC) Plastic Pipe Fittings, Schedule 40.
- ASTM D2467 Standard Specification for Poly(Vinyl Chloride) (PVC) Plastic Pipe Fittings, Schedule 80.
CPVC (Chlorinated Polyvinyl Chloride) Pipe Elbows:
- ASTM D2846 Standard Specification for Chlorinated Poly(Vinyl Chloride) (CPVC) Plastic Hot-and-Cold-Water Distribution Systems.
Ductile Iron Piping Elbows:
- ASTM A536 Standard Specification for Ductile Iron Castings.
- ISO 2531 Ductile iron pipes, fittings, accessories, and their joints for water applications.
Brass Elbows:
- ASTM B62 Standard Specification for Composition Bronze or Ounce Metal Castings.
- ASTM B124/B124M Standard Specification for Copper and Copper Alloy Forging Rod, Bar, and Shapes.
Aluminum Pipe Elbows:
- ASTM B361 Standard Specification for Factory-Made Wrought Aluminum and Aluminum-Alloy Welding Fittings.
Titanium Elbows:
- ASTM B363 Standard Specification for Seamless and Welded Unalloyed Titanium and Titanium Alloy Welding Fittings.
Nickel Alloys:
ASTM B366 Standard Specification for Factory-Made Wrought Nickel and Nickel Alloy Fittings.
Butt-Welded Pipe Elbows
- Butt-welded piping elbows are the most widely used pipe connections for high-temperature and pressure lines. They are normally used for pipe sizes with a size of NPS 2 or more. The pipe is connected to butt welded elbow as shown in Fig. 6 by having a butt-welding joint.
- Butt-welded fittings are supplied with bevel ends suitable for welding to the pipe. It is important to indicate the connected pipe thickness /schedule while ordering. All edge preparations for butt welding should conform to ASME B16.25.
- Dimensions of butt welded elbows are as per ASME B16.9. This standard is applicable for carbon steel & alloy steel butt weld fittings of NPS 1/2” through 48”.
Dimensions of stainless steel butt welded fittings are as per MSS-SP-43. Physical dimensions for fittings are identical under ASME B16.9 and MSS-SP-43. It is implied that the scope of ASME B16.9 deals primarily with the wall thicknesses which are common to carbon and low alloy steel piping, whereas MSS-SP-43 deals specifically with schedule 5S & 10S in stainless steel piping.
Dimensions for short radius elbows are as per ASME B16.28 in the case of carbon steel & low alloy steel and MSS-SP-59 for stainless steel.
Butt-welded fittings are usually used for sizes 2” & above. However, for smaller sizes up to 1-1/2” on critical lines where the use of socket welded joints is prohibited, pipe bends are normally used. These bends are usually of a 5D radius and made at the site by cold bending of the pipe.
Alternatively, butt welded elbows can be used in lieu of pipe bends but usually smaller dia lines are field routed and it is not possible to have the requirement known at the initial stage of the project for procurement purposes. So pipe bends are preferred. However, pipe bends do occupy more space and particularly in pharmaceutical plants where a major portion of piping is of small diameter and the layout is congested, butt welded elbows are preferred.
Butt-welded joints can be radiographed and hence preferred for all critical services.
ASME B31.3 allows the application of miter bends subject to meeting its pressure requirements.
Material standards as applicable to butt welded fittings are as follows:
ASTM A234
This specification covers wrought carbon steel & alloy steel fittings of seamless and welded construction. Unless seamless or welded construction is specified in the order, either may be furnished at the option of the supplier. All welded construction fittings as per this standard are supplied with 100% radiography. Under ASTM A234, several grades are available depending on chemical composition. Selection would depend upon the pipe material connected to these fittings. Some of the grades available under this specification and corresponding connected pipe material specifications are listed below:
ASTM A403
This specification covers two general classes, WP & CR, of wrought austenitic stainless steel fittings of seamless and welded construction. Class WP fittings are manufactured to the requirements of ASME B16.9 & ASME B16.28 and are subdivided into three subclasses as follows:
- WP-S-Manufactured from a seamless product by a seamless method of manufacture.
- WP – W These fittings contain welds and all welds made by the fitting manufacturer including starting pipe weld if the pipe was welded with the addition of filler material are radiographed. However, no radiography is done for the starting pipe weld if the pipe was welded without the addition of filler material.
- WP-WX These fittings contain welds and all welds whether made by the fitting manufacturer or by the starting material manufacturer are radiographed.
Class CR fittings are manufactured to the requirements of MSS-SP-43 and do not require non-destructive examination. Under ASTM A403 several grades are available depending on chemical composition. Selection would depend upon the pipe material connected to these fittings. Some of the grades available under this specification and corresponding connected pipe material specifications are listed below:
ASTM A420
- This specification covers wrought carbon steel and alloy steel fittings of seamless & welded construction intended for use at low temperatures. It covers four grades WPL6, WPL9, WPL3 & WPL8 depending upon chemical composition. Fittings WPL6 are impact tested at temp – 50° C, WPL9 at -75° C, WPL3 at -100° C and WPL8 at -195° C temperature.
- The allowable pressure ratings for fittings may be calculated for straight seamless pipe in accordance with the rules established in the applicable section of ASME B31.3.
- The pipe wall thickness and material type shall be that with which the fittings have been ordered to be used, their identity on the fittings is in lieu of pressure rating markings.
Piping Elbow vs. Piping Bend
A PIPING BEND is simply a generic term in piping for an “offset” – a change in the direction of the piping. It signifies that there is a “bend” i.e., a change in direction of the piping (usually for some specific reason) – but it lacks a specific, engineering definition as to direction and degree. Bends are usually made by using a bending machine (hot bending and cold bending) on-site and suited for a specific need. The use of bends is economical as it reduces the number of expensive pipe fittings. The major differences between a pipe elbow and a pipe bend are provided in Table 1 below:
Pipe Bend | Pipe Elbow |
---|---|
A pipe bend is a generic term for a curved section of a pipe used to change the direction of the pipeline. | A pipe elbow is a specific type of pipe fitting designed to change the direction of flow at a particular angle, typically 90 degrees or 45 degrees. |
Pipe bends can come in various angles, including 90 degrees, 45 degrees, or other custom angles. | Pipe elbows are primarily available in two common angles: 90 degrees and 45 degrees, although other angles are possible. |
Pipe bends may have a varying radius of curvature depending on the design and application. | Pipe elbows can be categorized as either long radius or short radius, each with its own specific radius of curvature. |
Pipe bends can be fabricated by bending a straight section of pipe to the desired angle using heat and mechanical force or by welding together straight pipe segments. | Pipe elbows are manufactured as dedicated fittings, and their shape is consistent with their specified angle and radius of curvature. |
Pipe bends are often used in custom or field-fabricated applications where specific bending requirements exist, or when standard elbows are not readily available. | Pipe elbows are standard fittings commonly used in piping systems to achieve predetermined angles for changing direction. |
The curvature and angle of a pipe bend may vary depending on the fabrication method and skill of the welder, potentially leading to inconsistencies. | Pipe elbows are manufactured with precise angles and radii, ensuring consistency and reliability in pipe routing. |
Pipe bends can be compatible with various materials and sizes, depending on how they are fabricated. | Pipe elbows are designed to be compatible with specific pipe sizes and materials, conforming to industry standards. |
Pipe bends are not standardized fittings and may require custom fabrication for each application. | Pipe elbows are standardized pipe fittings available in various materials and sizes, conforming to industry standards. |
Pipe bends are used in specialized or custom situations where a standard elbow may not fit or when specific bending requirements exist. | Pipe elbows are used as standard fittings in most piping systems to facilitate changes in direction while maintaining flow efficiency. |
Pipe bends may require custom fabrication for replacements, making maintenance more complex and time-consuming. | Pipe elbows are readily available as standard fittings, simplifying maintenance and replacement tasks. |
In short “All pipe elbows are bends as they change direction but all pipe bends are not elbows as they are not pipe fittings”
Pipe elbows are used in a wide range of industries, including plumbing, HVAC (heating, ventilation, and air conditioning), oil and gas, chemical and petrochemical processing, shipbuilding, marine, food processing, power plants, and many more.
Few more Resources for you…
Piping Elbow or Bend SIF (Stress Intensification Factor)
Consideration of Flanged Bend while modeling in Caesar II
Piping Design and Layout Basics
Piping Materials Basics
Piping Stress Analysis Basics
Piping Interface Basics
In short “All bends are elbows but all elbows are not bend”… following the previous description maybe it s exactly the opposite? “All elbows are bend, but all bends are not elbows”.
Ciao! and congrats for your job well done anyway 🙂
Hi
May i know the exact meaning of the WPB and WPC
Dear,
WPB means Wrought Product Grade B and WPC means Wrought Product Grade C. Wrought Products are those which are drawn from Pipe.
My question is the “D” in 5D bend. I that the od of “pipe” or the id of the pipe???
I really appreciate you giving insights to the difference and similarities to a pipe bend and elbow. It’s interesting to the see the process that are behind the bending of pipes in these different ways. I guess it really all depends on what they are being used for and what the engineer is trying to do.
Hi
May i know how can i indpect a bended pipe or elbow?i mean it needs some special test like pt or mt?pleae lintriduce some standard document about it thanks alot
Hallo, Thank you so much for your Helpful Information.
how I can calculate the Radius of Bending In Pipies :R1 from Asme Code B31.3
Is there a Table or a general Formula to calculate this value ?
Thanks In Advance
Can we use SS elbows with cs pipeline ? would it be better in terms of corrosion ?
This is a great read. I really like how you have explained some important points.
Wow! A lot of information about piping elbows and bands is provided on your site and outdoor compressor units are most accurately mentioned. Your site provides very useful information. Thanks for giving this info!
Dear Mr. DEY,
please tell your experience with welding a bypass loop line into elbow of the main line and impacts of erosion corrosion on weld?
Subrahmanya Bhat
Freelance Consultant
Thanks for great suggestion.
how much is tolerance in S bend
Good morning Mr. Dey,
We have several piping spools to fabricate. One calls for two 90 deg. bends with a 15″ center to center dimension. Nominal pipe size is 6″. We would prefer long radius however given the c-c dimension, the only thing I can think of is to use one long radius and one short radius elbow. If my math is correct, one of each radius would come out to the right dimension. If we were to do this, in which orientation should the long and short elbows be? I do not believe pressure drop will be an issue as this is a transfer line between two tanks. Thanks for your insight.
Regards, Mark
I’m glad there are dimensions for short radius elbows with carbon steel and low allow steel. I need a part similar to this to fit perfectly in the prototype design of my project. If it works like I think it should, I’ll end up getting a bunch more of them.
i appreciate the author for sharing such a amazing content with such a rich information
We are doing a a High pressure vessel as per B31.3 and have the following clarification,
1. Can we use the Elbow thickness same as branch connection without calculating tmin as per the elbow equation.
2. How to do weld strength calculation for branch nozzles fillet and groove welds.
No , tmin certainly in any case has to apply
Whats the angle of roll???