The idea of modular design is as follows: The complex piping system is divided into several modules that are mounted on a frame structure. Modules can be transported to the site and joined to each other into the entire piping system. One of the modules is shown in the picture below. At the points, “1” external piping or other module piping is connected.
Stress analysis of separate modules for temperature expansion and other loads acting on a whole system is impossible. Only the whole system can be analyzed. Exception: when anchors are added at all connection points between modules. But in this case design for temperature expansion will become extremely hard.
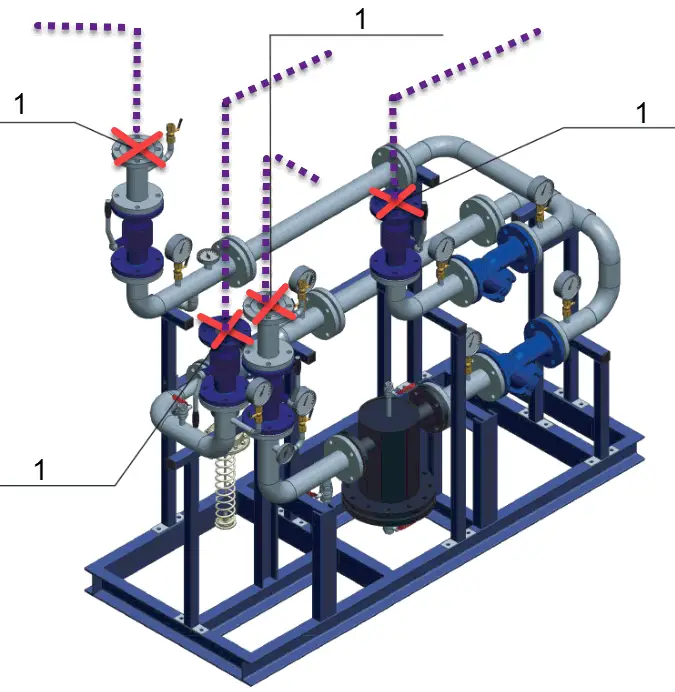
The practical solution to this problem is the following:
Option 1. Module manufacturer performs its stress analysis using of several, the most unfavorable variants of external piping design. Stress analysis should be successful for all variants. After that manufacturer passes the START-PROF module piping model to the customer. The customer adds the module model to own the piping model and performs an analysis of the whole system.
Option 2. The customer adds anchors or hinged anchors at the points, where his piping model is connected to the module. Performs stress analysis and optimize the design. After that, he passes the START-PROF piping model to the module manufacturer, who joins this model to the module piping model and preforms whole system stress analysis.
Option 1 & 2 can be simplified if you use the overlapping models when one part is included 100% and the second part included just partially.
There’s also Option 3. Too complex and hard. Module manufacturer offers 6 stiffnesses (Kx, Ky, Kz, KRx, KRy, KRz) for each connection point and temperature expansions (point movements). Also, the stiffness matrix 6×6 can be offered. The customer adds these stiffnesses and add support movements. But after analysis, he must pass new movements of connection points back to the manufacturer.
Also, piping systems usually are nonlinear. Some restraints may switch off, friction behavior may be different, therefore the manufacturer should perform new analysis and generate new stiffnesses and new movements. The design process will become iterative. If the piping system has several operation modes with various temperatures, this work becomes almost impossible. Much more easy to offer the whole piping model to counterpart. This option can only be used if the manufacturer wants to keep the design secret, but doesn’t want to use Option 2 for some reason.
Transportation Stage
The transportation stage should be calculated for both options described above. The system should have transportation configuration (locked springs, added temporary supports, detached flanges, etc.) and analyzed for inertial loads and vehicle body deformations during transportation. Added ice, show, wind, impact, and other possible loads.
Thank you very much for this informative article. In an ongoing project, to which I am assigned, we are going to have to do “modular” stress analysis.
Keep doing and excellent job
Thank you