A centrifugal pump is a mechanical turbomachine that converts mechanical energy into hydraulic energy through centrifugal activity and is used for transporting liquids. The fluid enters through the centrifugal pump suction, and the centrifugal force of the rotating impeller increases the pressure and velocity of the liquid. Centrifugal pumps are the most widely used pumps in the industry as they are suitable to handle both viscous and non-viscous liquids with high efficiency.
Use of Centrifugal Pumps
Centrifugal pumps are found in various industries for liquid transfer like
- Power Plants
- Refineries, Chemical, and Petrochemical Plants.
- Oil and Gas Industries.
- Chemical and Mining Industry.
- Pharmaceutical Industries.
- Agricultural
- Water Treatment Plants
- Fire Protection Industries, etc.
Components of a Centrifugal Pump
A centrifugal pump consists of the following major parts.
- Impeller,
- Casing,
- Suction and Discharge Nozzles,
- Shaft
- Bearings
Centrifugal Pump Impeller
An impeller is a wheel or rotor with a series of backward curved blades or vanes. It is the key component of a centrifugal pump and is mounted on the shaft. An external energy source (motor) forces the impeller to rotate at high speed. Liquid enters at the eye of the impeller and the rotational motion accelerates it through the impeller vanes into the pump casing.
There are three types of Pump Impellers;
- Open Impeller
- Semi-enclosed Impeller (One Side open and the other side backed by a single disc)
- Enclosed Impeller (Impeller is sandwiched between two discs)
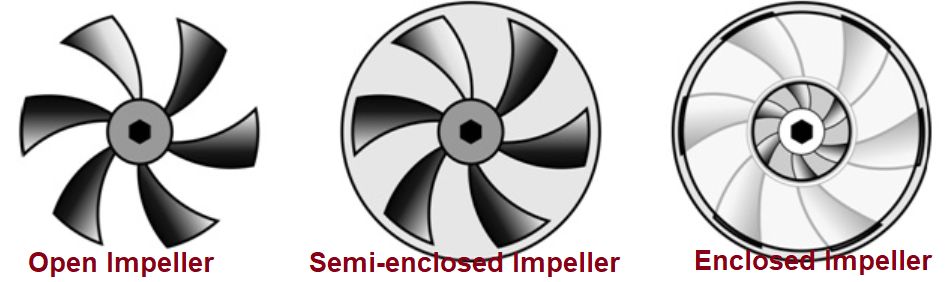
Centrifugal Pump Casing
The centrifugal pump casing seals the pump inside the atmosphere. It is an air-tight boundary that retains the pressure and converts the impeller velocity into a stable flow. In centrifugal pumps, the casing surrounds the pump rotor. The casing converts the velocity head into the pressure head. It guides the flow to the discharge nozzle. Industrial Centrifugal Pumps use three types of pump-casing. They are
- Volute Casing or Spiral Casing
- Vortex Casing and
- Casing with Guide Blades or Diffuser Casing
The diffuser casing is a highly efficient casing in centrifugal pumps.
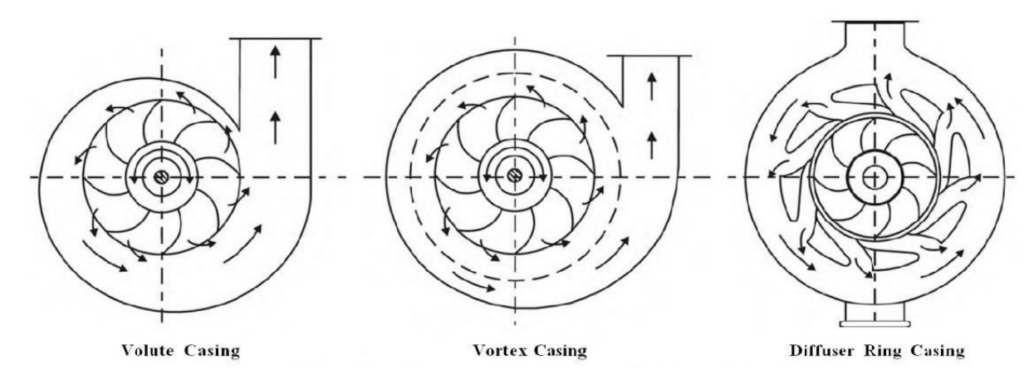
Suction and Discharge Nozzles of Centrifugal Pump
Suction and Discharge Nozzles are provided in a centrifugal pump for fluid intake and pumping outside respectively. The suction nozzle has an axis corresponding to the impeller’s rotational axis. The discharge nozzle has a normal axis to the impeller axis.
Centrifugal Pump Shaft
The pump shaft is the central component and it transmits the driving torque to the impellers. The shaft connects the impeller to the motor. It carries the impellers, the shaft sleeves, and the bearings. It is designed to center the rotating components within the pump casing.
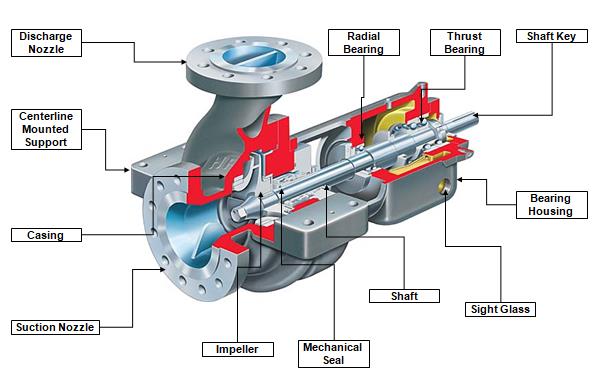
Bearings
Bearings in centrifugal pumps support all the loads imposed on the pump. Through pump bearings, the loads are transmitted to the foundation. Bearings keep the shaft deflections within acceptable limits.
Types of Centrifugal Pumps
Depending on Various parameters, centrifugal pumps can be grouped into the following types:
- Centrifugal Pump Types based on the number of impellers in the pump
- Single-stage pump (Fig. 4)
- Double-stage pump, and
- Multi-stage pump
- Types of Centrifugal Pumps Based on the orientation of case-split
- Axial split Pump and
- Radial split Pump
- Centrifugal Pump types based on the type of impeller design
- Single suction Pump and
- Double suction Pump
- Based on the basis of compliance with industry codes and standards
- ANSI pump – (American National Standards Institute)
- API pump – (American Petroleum Institute)
- DIN pump – DIN 24256 specifications
- ISO pump – ISO 2858, 5199 specifications and
- Nuclear pumps
- Based on the type of volute
- Single volute Pump
- Double volute Pump
- Based on where the pump bearing support
- Overhung Pumps
- Between-bearing Pumps
- Based on the orientation of the pump shaft
- Horizontal Pump and
- Vertical Pump
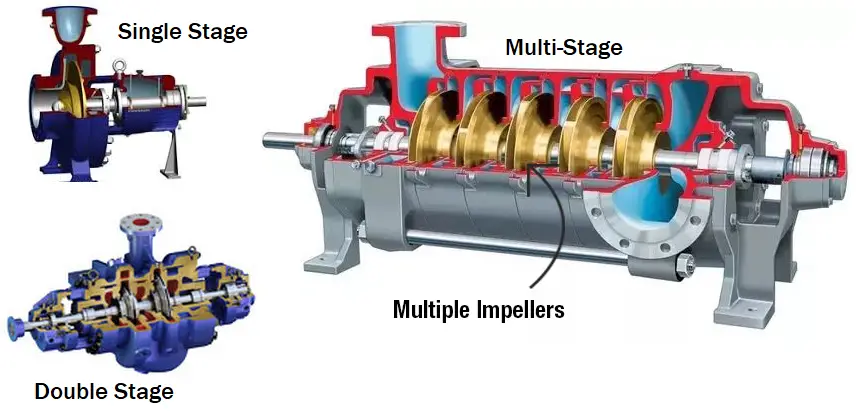
Centrifugal Pump Working
The fluid enters through the pump suction nozzle (Fig. 5) at the center of the impeller. Rotating Impeller imparts energy and the fluid gets accelerated till the impeller edge. Finally, it drains into the pump casing where the liquid is slowed down due to the gradually increasing section. The kinetic energy of the fluid is converted into pressure energy.
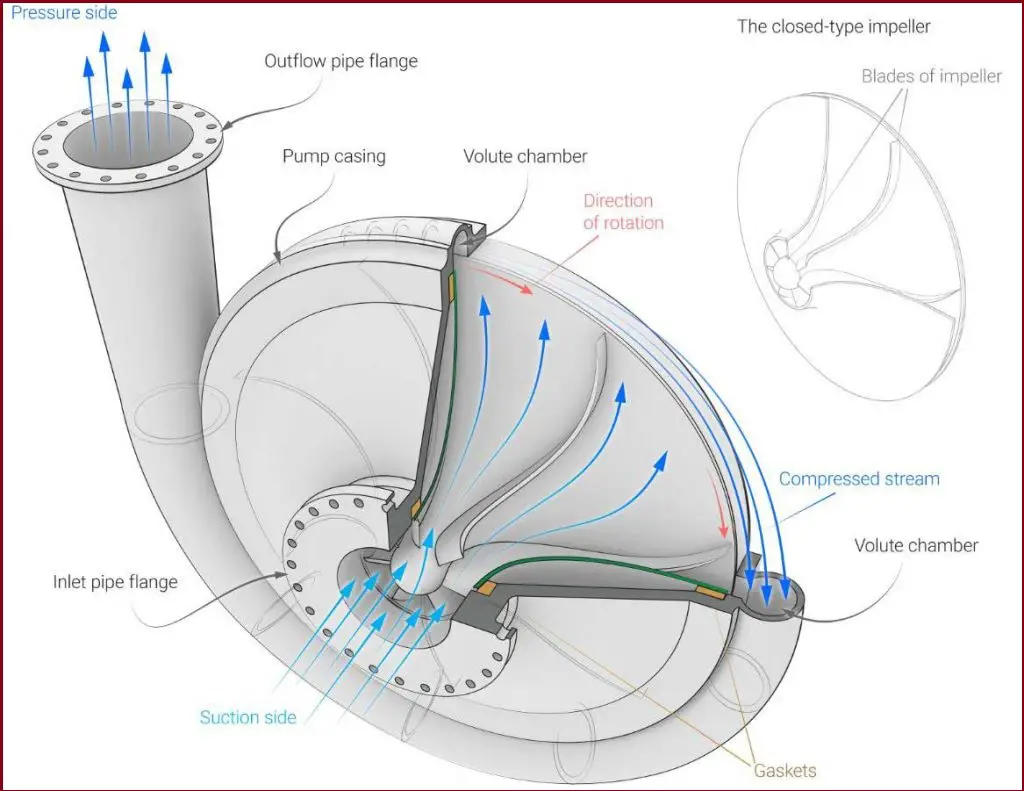
Normally, There are four stages of a centrifugal pump operation.
- Priming of the Pump, and
- Switching the motor for rotating the impeller
- Liquid enters through the suction nozzle.
- Impeller Rotates and the centrifugal force acts on the liquid to increase the velocity and pressure
A video tutorial explaining more details of the centrifugal pump operating principle is provided at the end of this article.
Advantages of Centrifugal Pump
A centrifugal pump offers the following advantages
- Handle viscous and non-viscous fluids
- Fewer Parts
- Simple construction and mechanism
- Less frictional Loss
- Highly Efficient
- Economical, Less Maintenance Cost
- Uniform pressure, no shock, or pulsation.
- Compact size, comparatively low space requirement
- Uniform torque.
- Easy Installation.
- Less Noisy
- Separate pump and motor causing negligible heat transfer
Disadvantages of Centrifugal Pump
Below mentioned are a few of the limitations of a centrifugal pump
- Less suction power is less as impeller rotation drives the liquid suction. Hence, priming is necessary.
- Magnetic resistance can be generated in the coupling causing energy losses.
- With an increase in fluid viscosity, efficiency reduces.
- Centrifugal Pump failure can happen during low-flow conditions due to overheating of the pump.
- Not suitable for high-head applications.
- Cavitation occurs if not properly designed and selected.
Centrifugal Pump Standards
Some widely used centrifugal pump standards are:
- API 610
- ISO 5199 and ISO 2858
- ASME B73.1 and B 73.2
- BS 5257
Out of the above, API 610 is the most widely used centrifugal pump standard and it governs the design of centrifugal pumps for general refinery services. Their design is robust and their performance is highly satisfactory. They are also known as API Pumps.
Difference between Centrifugal Pump and Centrifugal Compressor
- The Basic Difference between a centrifugal pump and a centrifugal compressor is that pumps handle mainly liquids but compressors compress gases.
- There is no fluid volume change in a pump but in a compressor the gas volume reduces.
Video Tutorial for Centrifugal Pump Working Principle
The following video tutorial by the Learn Engineering group explains the working of centrifugal pumps with animation.
Thank you for explaining that a centrifugal pump is a turbomachine that converts mechanical energy into hydraulic power to move liquids. Are centrifugal pumps used in the irrigation industry to move water around? It seems like you could probably find this kind of pump in the irrigation industry because water has to be moved from its source to where it is going to be distributed over crops.
According to Value Market Research, the latest technology trends and global market opportunity analysis in the Centrifugal Pumps Market industry growing with a high CAGR in the upcoming year. Our report has categorized the market based on technology, service, development, vertical and region.
Very good