A pressure switch is an electronic or mechanical device that informs that a certain set pressure is reached. It is installed in systems where monitoring pressures are required. When a preset fluid pressure is reached, the pressure switch activates an electrical contact. A wide range of industrial and residential applications are found for pressure switches. Some typical applications where pressure switches are used are Furnaces, HVAC systems, Well pumps, etc. In this article, we will discuss the working, types, selection, and applications of pressure switches.
What is a Pressure Switch?
Pressure switches are devices that are used to monitor the pressure level of a process. The device informs a pressure rise or fall and thus helps in controlling systems of pressurized fluids. Based on the current pressure situation of the system the device becomes On or OFF. A range of process control systems uses pressure switches. The device usually consists of the below-mentioned components:
- A pliable and sensitive diaphragm for detecting pressure.
- A spring to adjust preset points or cut-out points.
- A lever to activate or deactivate the pressure switch.
- Electrical contact from an external power source.
- Terminals for connecting the external power source to the contacts.
Types of Pressure Switches
Depending on their working there are two major types of pressure switches; Mechanical Pressure Switches and Electronic Pressure Switches.
Mechanical Pressure Switches
Mechanical pressure switches are robust and simple. They use a spring and a diaphragm or piston to control the pressure for triggering the switch. The spring force opposes the inlet pressure. A set screw or knob adjusts the spring’s pretension. This spring pretension directly correlates to the set pressure at which the switch makes an electric contact and the device activates. When the pressure drops, the pressure switch resets to its original state.
There is a difference between the switch point and reset point known as hysteresis which is expressed as a percentage of the switch point value, for example, 15%. For most mechanical pressure switches, the hysteresis is defined by the manufacturer and it is not user-configurable.
Mechanical pressure switches are preferred to handle high voltages and amperages as compared to electronic pressure switches. A contract change can help in increasing or decreasing the pressure.
These pressure switches generally work using three different types of contacts. They are NO or normally open, NC or normally closed, and changeover (SPDT) contacts. The Changeover contacts are for both NC and NO operations.
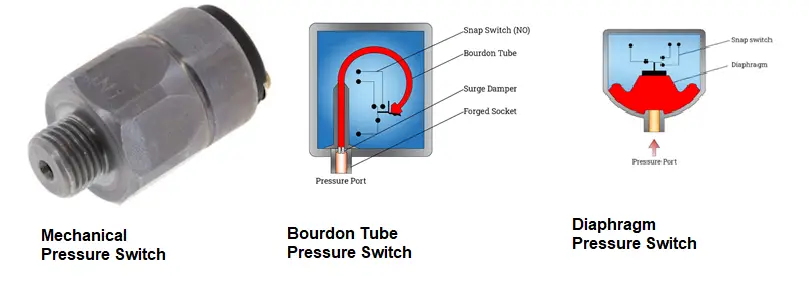
Types of Mechanical Pressure Switches
Mechanical switches are basically electromechanical pressure switches. Depending on the type of pressure-sensing element, mechanical pressure switches can be categorized as follows:
- Bourdon tube pressure switch that uses a flexible tube.
- Diaphragm pressure switch that uses a diaphragm
- Piston pressure switch that uses a piston mechanism
- Differential pressure switch that uses differential pressure between two points, and
- Snap disc pressure switch that uses two metal discs.
Electronic Pressure Switch
In an electronic pressure switch, an electrical pressure sensor (pressure transducer) measures the pressure change. The switching function is digitally displayed in such pressure switches. The set pressure can be adjusted by the electronic pressure switch manufacturer or on-site programming. This type of pressure switch is flexible as depending on the application requirement, the switch point, delay time, hysteresis, and output signals can be adjusted. Electronic pressure switches are solid-state switches that are suitable for automated and controlled equipment. They work using electrical parameters like resistance, capacitance, etc.
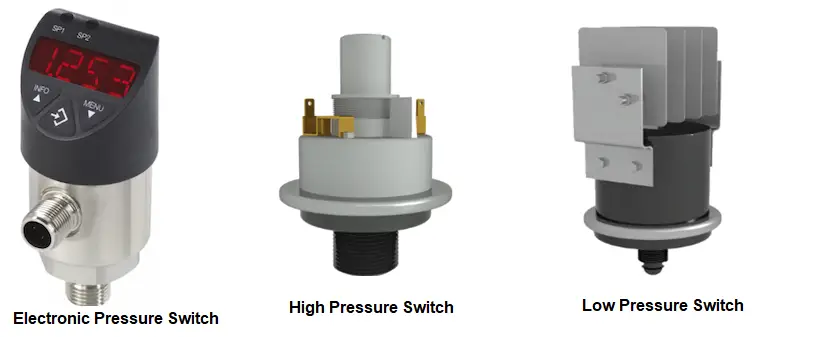
Again, depending on the pressure handling capability, there are two types of pressure switches; High-pressure switches and Low-pressure switches. High-pressure switches are designed to operate from 1 PSIG to 10, 000 PSIG whereas low-pressure switches can respond to small pressure fluctuations.
Working of a Pressure Switch
As already informed the pressure switches work either by mechanical or electronic action. In the mechanical operation principle, the inlet fluid pressure pushes a piston against a spring of known resistance force. The spring constant is selected such that the piston only moves when a certain predetermined pressure is attained. The piston then triggers the micro-switch which moves from NC to NO position using an operating pin and trip button.
Selection Criteria for Pressure Switches
The selection of pressure switches is dependent on various parameters as listed below:
Process Fluid Type:
The process fluid must be compatible with the materials of wetted parts like ports, seals, pressure sensing components, etc. Common process media used with pressure switches are Hydraulic oil, Water, Heating oil, Air, Turpentine, gasoline, etc.
The material for pressure switches must be resistant to chemical and physical attacks like corrosion, erosion, oxidation, etc. In general, steel, stainless steel, PTFE, brass, etc are used for rigid parts of the pressure switch while the sensing parts are usually made of Nitrile butadiene rubber, Ethylene propylene diene monomer rubber, FKM, etc.
Working Pressure Range:
The pressure switch must withstand the complete working pressure range. A diaphragm-type design is selected for vacuum and low-pressure applications while a piston design is used for high-pressure applications. Additionally, the type of pressure (positive or vacuum pressure) is also to be considered.
Temperature:
The working temperature range influences the pressure switch material selection. Sometimes, the effectiveness of the pressure switch varies with temperature change. Therefore, some pressure switches need to be readjusted if the working temperature is much higher than the room temperature.
Repeatability:
Repeatability or accuracy is a very important consideration for pressure switch selection. The device must produce accurate results in every repetition. In general, diaphragm-type pressure switches provide more accuracy than the piston design.
Switching Function:
Pressure switches are characterized by the number of poles or throws that a switch can control. Various different types of switching functions are available like single pole single throw (SPST), single pole double throw (SPDT), double pole single throw (DPST), double pole double throw (DPDT), etc.
Hysteresis:
The difference between the switch point and the reset point is known as Hysteresis. The switching pressure stays active for a longer duration when the reset point is large. On the other hand, the switch will flip between the on/off state frequently if the reset point is small. So, depending on the application the required hysteresis must be predecided.
Service Life:
The service life of a pressure switch can be defined as the number of times the switch can activate or deactivate before failure. Electronic pressure switches have more service life as compared to mechanical pressure switches as there are no moving parts.
End Connection Fittings:
The pressure switch end connection must be compatible with the process port connection. In general, male and female threaded connections are widely used for mounting pressure switches.
Certification and Approval Requirements:
National and International certifications and approvals improve the quality of pressure switches. UL, CSA, FM, CE, etc are some of the certifications available for pressure switches.
I love this post, it is very informative. I have enjoyed your site very much! These types of switches can be used in pneumatic systems
Hi, thank you for such a brilliant post. I have been reading some blogs that give me more knowledge about What is a Pressure Switch. I must say this is one of the best among them. You have done great research I feel, thanks for sharing.
The article on whatispiping.com about pressure switches is an excellent resource for anyone looking to understand how pressure switches work and how to select the right type for a specific application. The article covers the basic principles of pressure switches, including how they convert pressure changes into electrical signals. It also provides a detailed explanation of the different types of pressure switches, such as electromechanical, solid-state, and differential pressure switches, along with their respective advantages and disadvantages.
Thank you for your expert engineering advice. I’m a newbie at pressure switches, specifically for a deep water well, and I surely am being challenged to figure out problems that I knew nothing about. I comprehend the principles you’ve discussed, but so far everything I’ve attempted to get the switch to cut in at a certain pressure has not been successful. I hope some of your information helps me once I assimilate it further.
Can I use pressure switch to fresh water pump, if yes explain
Can I use pressure switch pump for fresh water, if yes to kindly explain