A stud bolt is an externally threaded mechanical fastener. An assembly of stud bolt connections is usually formed by two nuts and the stud. Sometimes, washers and additional nuts may be used. In high-pressure piping and pipeline flange connections, stud bolts are widely used. In this article, we will learn about the types, standards, materials, selection, and sizes of stud bolts.
What is a Stud Bolt?
A stud bolt is a mechanical fastener having external threads without a head. The external thread is either for the full length of the stud or partially threaded from each end. It uses at least two nuts, one on each side for assembly connection. Stud bolts are available in various sizes, types, and threading patterns.
Types of Stud Bolts
Depending on the threading pattern and design, various types of stud bolts are available as listed below:
- Fully threaded stud bolt or continuous threaded stud bolt having uniform thread throughout its length.
- Tap end stud bolts having unequal threads from each end and non-threaded center.
- Double-end stud bolts having both ends threaded of equal lengths and a non-threaded center.
- Flange Stud bolts: Fully threaded stud bolts with chamfered ends specifically used for flanged connections.
- Double-end stud bolt with reduced shank: the non-threaded center part is of a reduced diameter than the actual diameter.
Depending on the Stud bolt material strength they are divided into three groups;
- High-Strength stud bolt
- Intermediate-strength stud bolt, and
- Low-strength stud bolt.
Types of Stud Bolt Threads
Stud bolts use a variety of screw thread profiles depending on the application. Some of the most common thread profiles are:
- ISO metric thread
- ACME thread
- UNC thread
- UNF thread
- UN thread
- WHITWORTH thread
Stud Bolt Standards
The design and manufacturing of stud bolts are governed by a range of ASME standards as listed below:
- ASME B16.5 & ASME B16.47 cover the diameter and length.
- ASME B1.1 covers coarse and fine thread series.
- ASME B18.2.1 is used for Square and Hex Bolts and Screws
- ASME B18.2.2 provides details for Square and Hex Nuts
- ASME B18.21.1 provides Lock Washer details
- ASME B18.22.1 is used for Plain Washers
Various other international standards like DIN, ISO, BS, SAE, IS, etc also provide details of stud bolts.
Stud Bolt Materials
For high-temperature and pressure services, ASTM A193 is the most widely used flange material. Grade B7 and B7M are the most frequently used A193 material grades. For low-temperature services, ASTM A320 Gr L7, L7A, and L7B are used. Other stud bolt materials include the following:
- ASTM A354 Gr BC, BD
- ASTM A540 Gr B21 to B24
- ASTM A193 Gr B5, B6, B8, B16, B8M, B8A, B8T, L7, B17B.
- ASTM A453 Gr 660A/B/C/D
- ASTM A913 Inconel 718
- ASTM A320 Gr L7M, L43, B8, B8A, B8T, B8MA, B8C
- ASTM A182 Gr S31803, S32205.
The nut and washer material must be compatible with the selected stud-bolt material to avoid galvanic corrosion. Sometimes stud bolts are coated to increase corrosion resistance. The common coating materials are:
- Electro zinc plating
- Electro cadmium plating
- PTFE Coating
- Hot-dip galvanizing
- Phosphate coating
- Electroless nickel plating
- Silver coating
- Zinc/Nickel by electrodeposition
- Zinc-nickel coating
- Aluminum coating
- Dacromet
- Geomet
- XYLAN and
- Xylar
Selection of Stud Bolt Materials
The material of the stud bolt mainly depends on the process design temperature and flange materials. however, there are many other parameters that must be considered. The following image from blog.projectmaterials.com provides rough guidance on the stud bolt material selection based on design temperature and flange material:
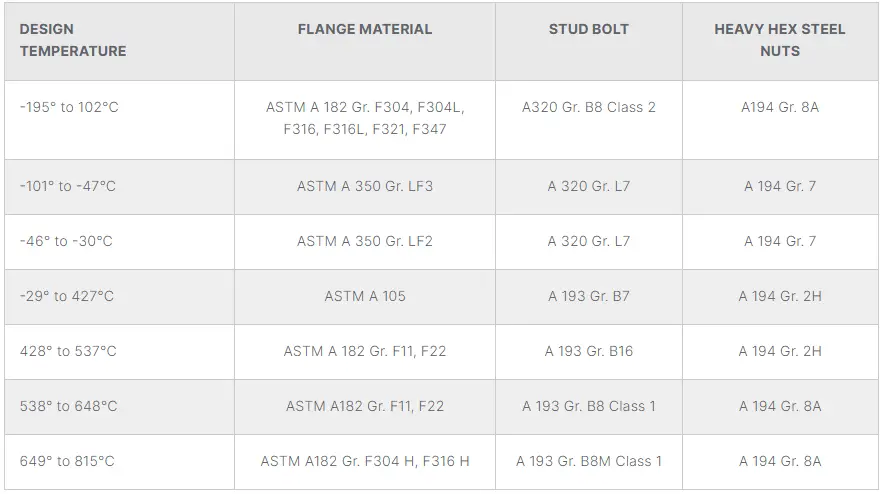
Stud Bolt Ends and Lengths
The ends of stud bolts are usually rounded, sheared, saw cut, flat, or chamfered. The length of a stud bolt is measured parallel to the axis from one end to the other. They are available in 1/4″ length increments.
Stud Bolt Size/Dimension
The size and dimension of the stud bolt are decided by the governing standard. ASME B16.5 and ASME B16.47 provide stud bolt charts that provide the bolt diameter and the number of bolts required depending on the pressure class, flange type, and pipe size.
In general, with an increase in pressure class and NPS, the bolt area increases. There are two parameters that decide the bolt area; bolt diameter and the number of bolts. So, any of the two or both parameters can increase to get an increase in bolt area. Refer to Fig. 2 below for a typical Stud-bolt chart for pressure class 150, 300, and 600 based on ASME B16.5 standard.
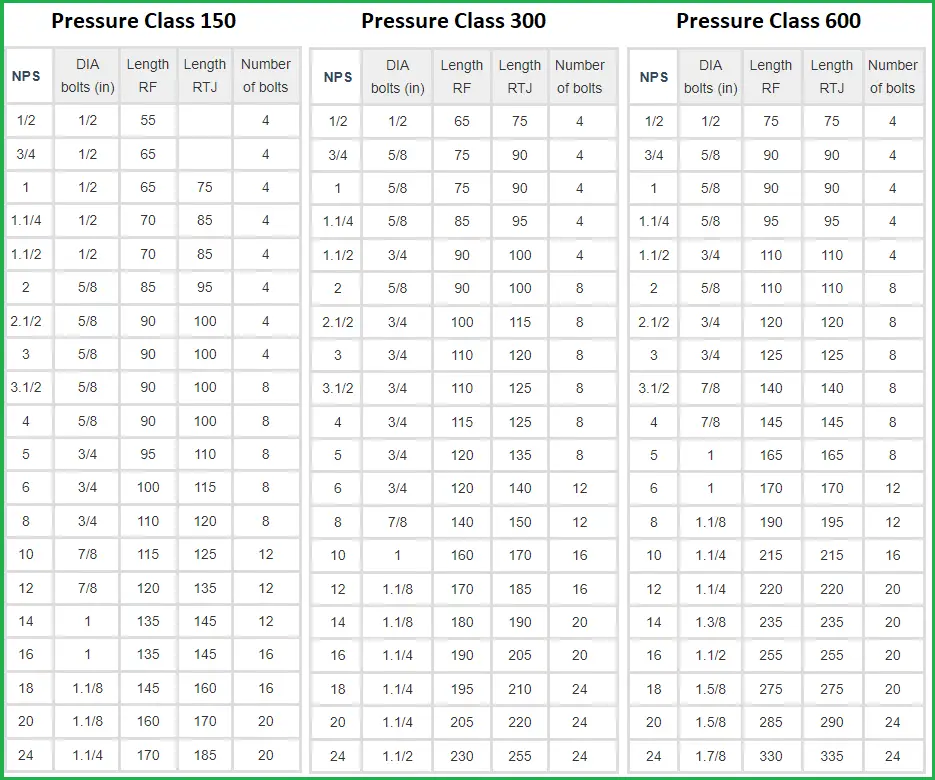
Is there a particular technical advantage in using a stud vs a bolt? The only practical advantage I see is that if there is not enough room behind the flange you can insert the stud from the opposite end. But I always wonder if the stud provides any other advantage, for example more tensile strength than a bolt.
Studs provide optimal torque specs. A standard bolt stretches horizontally (twists) and stretches vertically, where a stud only stretches vertically as it’s free floating between the two nuts. You can picture the studs as springs working together in a bolting pattern to achieve uniform pressure on the sealing surface. Regardless of flange and gasket thickness the nuts can be adjusted evenly to facilitate uniform tensile stretching. Torque should be staged progressively higher, and then checked at intervals as the metal relaxes over time.
Difference between b7&b7m why b7m used in h2s services
Guys, do you have any formula or calculation to stretching or tension of double-end stud bolt ??
Thanks