Turnbuckles are essential components in various industries, providing tension and support in structures, rigging, and mechanical assemblies. They play a crucial role in ensuring safety and functionality in applications ranging from construction to sailing. While using spring hanger supports in the piping industry, you must have seen the application of this specialized device known as a turnbuckle. It is a very important piece of hardware that helps in adjusting the length of the rods in the spring hanger application so that space utilization is optimized. In this article, we will explore the design, types, applications, advantages, and installation of turnbuckles.
What is a Turnbuckle?
A turnbuckle is a device consisting of two threaded eye bolts, one on each end of a metal frame, which can be adjusted by turning the central body. This mechanism allows for precise tensioning and loosening of cables, ropes, or rods, making it ideal for applications requiring adjustment under load. It is a rigging device. A turnbuckle is also known as a stretching screw or bottlescrew.
ASME B30.26 defines a turnbuckle as an adjustable device consisting of three primary components: a body, a right-hand threaded end fitting, and a left-hand threaded end fitting.
Component Parts of a Turnbuckle
A turnbuckle usually consists of the following parts:
- Body: The central component that connects the two threaded ends. It often features a hexagonal or square shape to facilitate gripping with a wrench.
- End Fittings: Typically include eyes, hooks, or threads, which connect the turnbuckle to the materials being tensioned. Each turnbuckle will have two end fittings, one with right-hand threading and the other with left-hand threading.
- Threading: Usually made with coarse or fine threads that allow for easy adjustment. The pitch of the threads affects how much tension is applied with each turn.
Some applications can use nuts or gem nuts. The nut is used to tighten down the threaded part on the body to help prevent the device from loosening on threading. However, gem nuts are preferred only in non-critical applications, as in critical applications the nut can create extra strain on the threads. Hence, in critical applications, a lock wire is used instead to prevent the loosening of threads, specifically in vibrating applications.
Fig. 1 shows a typical turnbuckle along with its parts:
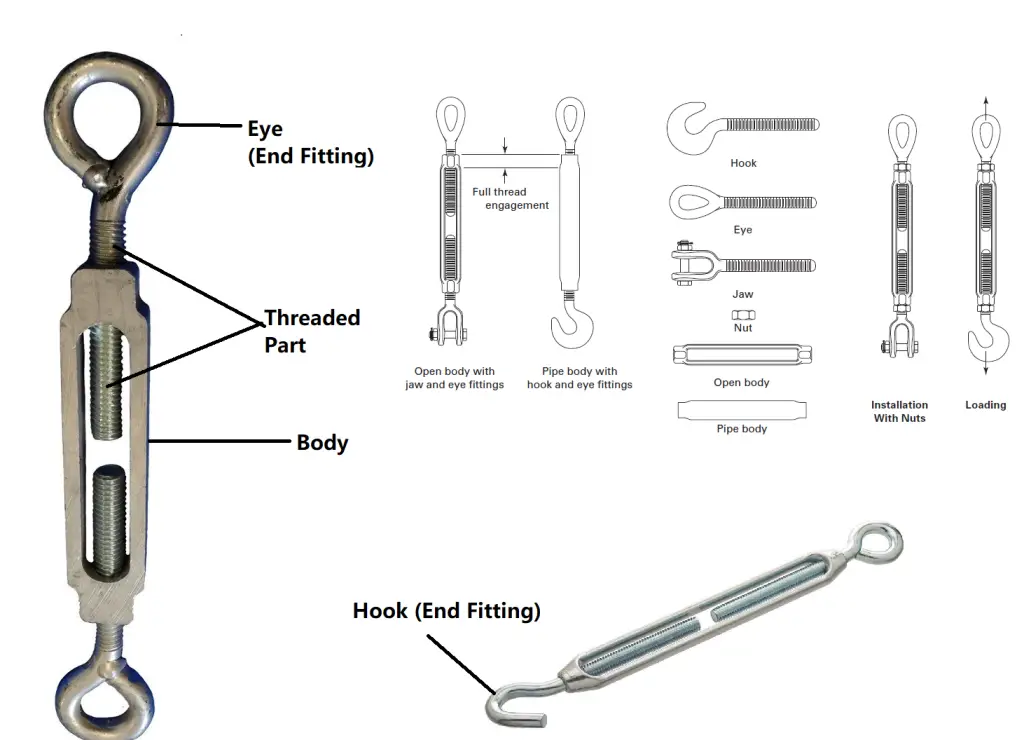
Materials of a Turnbuckle
Turnbuckles are made from various materials, depending on their intended application:
- Steel: Common for heavy-duty applications, providing high strength and durability.
- Stainless Steel: Ideal for marine environments due to its corrosion resistance.
- Aluminum: Lightweight and suitable for applications where weight reduction is critical.
- Plastic: Used in specific lightweight applications.
Types of Turnbuckles
Turnbuckles come in various shapes and sizes to suit different needs. Based on the body construction, they are of two types:
- Open Body Turnbuckle: Features a U-shaped frame, allowing for easy visual inspection and adjustment.
- Closed Body Turnbuckle: More robust, providing extra protection for the threaded rods, and used in high-load applications.
Fig. 2 shows open-body and closed-body type turnbuckles.
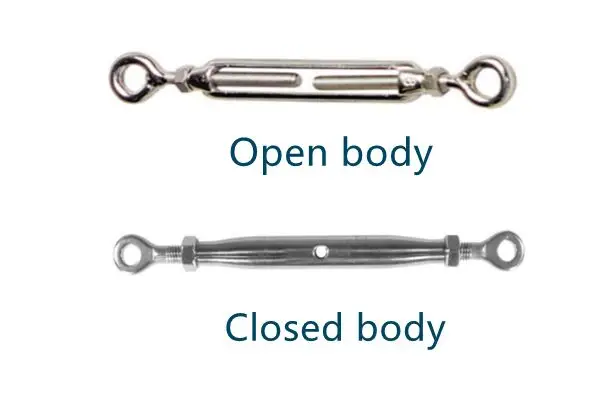
Again, depending on the end attachment, there are various types of turnbuckles.
- Jaw and Jaw Turnbuckle: Comes with jaws on both ends, making it suitable for quick and secure connections.
- Hook and Hook Turnbuckle: Features hooks on both ends, ideal for applications where quick disconnection is necessary. Normally used for temporary connections.
- Eye and Eye Turnbuckle: Equipped with eyes for bolt connections, commonly used in rigging and construction.
- Hook and Eye Turnbuckle
- Eye and Jaw Turnbuckle, etc
Fig. 3 shows the turnbuckle types depending on the end-fitting attachment.
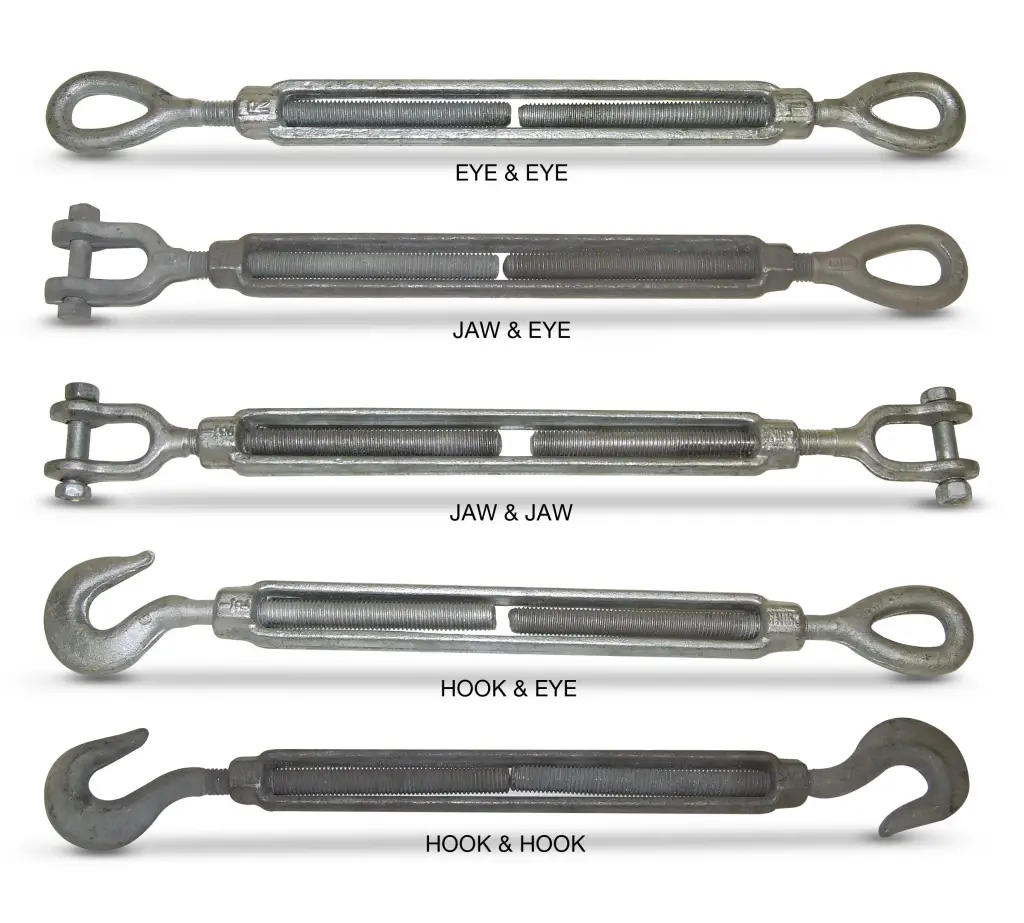
Applications of Turnbuckles
Turnbuckles are used in a wide range of applications across various industries:
1. Piping Industry
In the piping industry, turnbuckles are essential for tensioning and securing pipe supports, braces, and hangers, ensuring that piping systems remain stable and aligned under various load conditions. They provide the necessary adjustability to accommodate the thermal expansion and contraction of pipes, which is crucial for maintaining system integrity and preventing stress-related failures. By allowing for precise tension adjustments, turnbuckles help distribute loads evenly across support structures, thereby enhancing the overall safety and longevity of piping installations in both industrial and commercial applications.
2. Construction
In construction, turnbuckles are often used to provide tension in structural cables, such as guy wires for tall structures, ensuring stability and support. They are also used in scaffolding systems to adjust the tension in braces.
3. Marine
In marine applications, turnbuckles secure rigging on boats and yachts. They allow sailors to adjust the tension of sails and ensure proper alignment of masts, contributing to safety and performance.
4. Agriculture
Farmers use turnbuckles for fencing and tensioning wire or cable in livestock enclosures, ensuring secure and durable installations.
5. HVAC and Electrical
Turnbuckles are used in HVAC systems to tension ductwork, ensuring efficient airflow and structural integrity. Similarly, they can help secure electrical cables in place.
6. Sports and Recreation
In sports, turnbuckles are often found in gym equipment and climbing gear, providing necessary tension and safety features.
7. Theater and Events
Event planners utilize turnbuckles to rig lights, banners, and other equipment, ensuring secure placements and safety in dynamic environments.
8. Aircraft
In aircraft construction, particularly during the early years of aviation, turnbuckles played a crucial role in maintaining structural integrity. Biplanes often utilized turnbuckles to adjust the tension of the structural wires that braced their wings, ensuring optimal performance and safety. Additionally, turnbuckles are extensively employed in flight control systems to manage the tension on flexible cables. To prevent them from loosening due to vibration, these turnbuckles are typically secured with lock wire or specially designed wire clips.
9. Shipping
In the shipping industry, turnbuckles are vital for tensioning a vessel’s rigging and securing lashings. A specific variant known as a bottle screw features an enclosed tubular body, making it ideal for managing the stresses and demands of maritime applications. These devices help ensure that rigging remains taut and cargo is safely secured during transit, enhancing both safety and stability at sea.
How Do Turnbuckles Work?
Turnbuckles operate on a straightforward yet effective mechanism designed to adjust the tension between two points. At their core, turnbuckles consist of a central body with two threaded ends, allowing for easy tensioning and loosening of cables, ropes, or rods.
- Threaded Ends: Each end of the turnbuckle features a threaded fitting (such as an eye, hook, or jaw) that connects to other components. These threads are usually made with a coarse or fine pitch to allow for precise adjustments.
- Central Body: The central part of the turnbuckle can be turned to either increase or decrease the length between the two ends. By twisting the body clockwise, the ends move closer together, increasing tension; conversely, turning it counterclockwise creates slack.
- Adjustment Mechanism: As you turn the central body, the threads engage, causing the fittings to either draw closer or move apart. This adjustability allows for fine-tuning of tension, which is critical in applications where load and alignment are crucial.
- Locking Mechanisms: To prevent unintentional loosening from vibrations or movement, turnbuckles often incorporate locking features such as lock wire or wire clips. These secure the turnbuckle in place once the desired tension is achieved.
Overall, turnbuckles are an efficient and reliable means of managing tension and alignment in various applications, from construction to rigging and beyond.
Advantages of Using Turnbuckles
- Adjustability: The primary advantage of turnbuckles is their adjustability, allowing for fine-tuning of tension levels.
- Strength: Made from durable materials, turnbuckles can withstand significant loads, making them suitable for demanding applications.
- Versatility: Available in various sizes and designs, they can be used across multiple industries and applications.
- Ease of Use: Simple to install and adjust, turnbuckles require minimal tools for operation.
- Cost-Effective: With their longevity and durability, turnbuckles represent a cost-effective solution for many tensioning needs.
What is the meaning of the take-up length of a turnbuckle?
The total length of the end fitting that can screw in and out of the body to take up tension is known as the take-up length of the turnbuckle.
How is the load-bearing capacity of a turnbuckle decided?
The load-bearing capacity of a turnbuckle depends on the thread diameter. With an increase in the thread diameter, the load-bearing capacity increases.
How is a turnbuckle identified?
As per ASME B30.26, in each turnbuckle, the name of the manufacturer and the size or rated load must be marked. The rated load is marked as the working load limit, and this must not be exceeded at any moment. If the size and rated load are missing, the turnbuckle should not be used.
How are turnbuckles used?
Turnbuckles are utilized in various applications to adjust and maintain tension in cables, ropes, or rods, ensuring stability and alignment in structures. In construction, they are commonly used to secure scaffolding and support structures, providing the necessary tension to withstand loads and environmental factors. In the marine industry, turnbuckles are essential for rigging sails and masts, allowing sailors to fine-tune the tension for optimal performance. They are also found in agricultural settings for securing fencing and in HVAC systems for stabilizing ductwork. By enabling precise adjustments, turnbuckles contribute significantly to safety and functionality across these diverse applications.
How to Install a Turnbuckle?
Tools Required
- Wrench or pliers
- Safety goggles
- Tape measure
- Level (for construction applications)
Step-by-Step Installation Guide
- Prepare the Area: Ensure the installation site is clear and has adequate space for tensioning.
- Measure the Distance: Determine the distance between the points you intend to connect with the turnbuckle.
- Attach End Fittings: Securely connect the end fittings to the appropriate surfaces, ensuring they are rated for the load.
- Insert the Turnbuckle: Thread the turnbuckle between the two fittings, ensuring it is properly oriented.
- Adjust the Tension: Use a wrench to turn the body of the turnbuckle. Turning it clockwise increases tension, while counterclockwise decreases it.
- Check Alignment: Use a level to ensure everything is aligned properly. Adjust as necessary.
- Secure Connections: Once the desired tension is achieved, double-check all connections and secure them as needed.
Turnbuckles are vital components in numerous applications, providing adjustable tension and stability. Understanding their design, types, and applications can help you make informed decisions about their use in various projects.