Vortex flow meters have become an integral part of industrial measurement technology. Their ability to measure fluid flow rates accurately and reliably makes them invaluable in various applications, from water treatment to chemical processing. The Vortex Flow Meter is one of the various types of volume flowmeters that are used frequently in the oil and gas industry to measure the flow inside a pipe. This device performs its best when introducing moving parts poses a problem. The main advantage of Vortex flow meters is that
- Sensitivity to process conditions variations is low
- low wear compared to other types as there are no moving parts and
- applicable for a wide range of fluids, i.e. liquids, steam, and gases.
In this comprehensive guide, we will delve into the principles of vortex flow measurement, their design and operation, applications, advantages, and limitations.
What is a Vortex Flow Meter?
A vortex flow meter is a device used to measure the flow of fluids—liquids and gases—based on the principle of vortex shedding. When a fluid flows past an obstruction, it creates alternating vortices downstream of the obstruction. The frequency of these vortices is proportional to the flow rate, allowing for accurate measurements.
How Vortex Flow Meters Work
Vortex meters are frequency meters that work based on the vortex principle. A bluff body (disturbing element) is placed in the middle of the pipe inside each vortex flowmeter that disturbs the flow causing an obstruction. Downstream of the obstruction, a mechanical sensor is placed which can measure the pressure differences (frequency) in the flowing fluid.
The Principle of Vortex Shedding
The principle of vortex shedding was first described by the German scientist Heinrich Gustav Magnus in the 19th century. When a fluid encounters an obstruction, it generates swirling eddies or vortices on either side of the obstruction. These vortices alternate sides, creating a pattern of vortices that can be measured.
The frequency of vortex shedding (f) can be described by the following formula:
f=K⋅Q/d2
Where:
- K is a constant dependent on the shape of the obstruction,
- Q is the volumetric flow rate,
- d is the diameter of the obstruction.
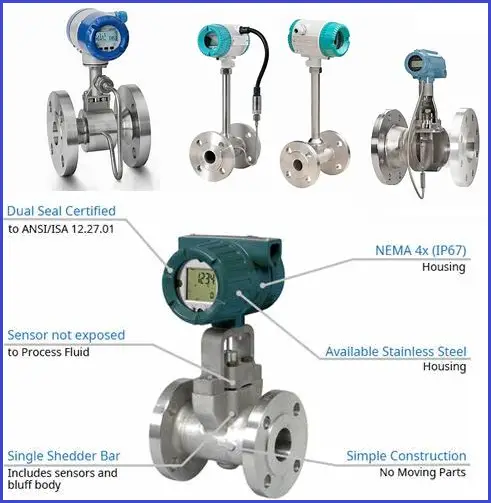
Components of Vortex Flow Meter
On average, every vortex meter consists of the following electronic parts-
- Shedder Bar: The obstruction in the flow path that generates vortices.
- Sensor: Detects the frequency of the vortices. It can be a piezoelectric or capacitive sensor.
- Transmitter: Converts the frequency signal into a flow rate reading, which is displayed on a digital interface.
- Body: The casing that holds the internal components and connects to the piping system.
- Pick-up elements,
- Microprocessor
- AC-pre amplifiers,
- Noise abatement features,
- AC-amplifier with filters,
- Schmitt Trigger,
Factors Affecting Vortex Meter Performance
In general, Vortex Meter performance is influenced by
- corrosion of upstream piping
- sheddar bar geometry changes due to erosion or wax deposits
- positional changes of sheddar bar when improperly secured
- Hydraulic noise, etc.
Types of Vortex Flow Meters
Vortex flow meters come in various configurations to suit different applications.
Full-bore Vortex Flow Meters
Full-bore vortex flow meters are designed for use in pipelines with a consistent diameter. They provide high accuracy and are commonly used in larger industrial applications.
Insertion Vortex Flow Meters
Insertion vortex flow meters are designed for applications where space is limited. They can be inserted into existing pipes without the need for extensive modifications, making them suitable for retrofitting.
Vortex Flow Meter Design
A vortex flow meter is typically constructed from 316 stainless steel or Hastelloy and consists of a bluff body, a vortex sensor assembly, and transmitter electronics, which can also be mounted remotely. These meters are commonly available in flange sizes ranging from ½ inch to 12 inches. For installations under six inches, the cost of vortex meters is competitive with that of orifice meters. Wafer body designs (flangeless) tend to be the most economical, while flanged meters are preferred for hazardous fluids or high-temperature applications.
Various bluff body shapes—such as square, rectangular, T-shaped, and trapezoidal—have been tested to optimize performance. Research indicates that while linearity, limitations at low Reynolds numbers, and sensitivity to velocity profile distortions show only slight variations with bluff body shape, certain design criteria are essential. The width of the bluff body must be a sufficient fraction of the pipe diameter to ensure that the entire flow contributes to vortex shedding. Additionally, the upstream face should feature protruding edges to stabilize the lines of flow separation, regardless of flow rate. The length of the bluff body in the direction of flow should also be a specific multiple of its width.
Most modern vortex meters utilize piezoelectric or capacitance sensors to detect pressure oscillations around the bluff body. These sensors generate a low-voltage output signal that matches the frequency of the oscillations. They are modular, cost-effective, easy to replace, and capable of functioning across a broad temperature range—from cryogenic liquids to superheated steam. Sensors can be positioned either inside the meter body or externally. Wetted sensors are directly affected by vortex pressure fluctuations and are housed in durable cases to resist corrosion and erosion.
External sensors, often piezoelectric strain gauges, detect vortex shedding indirectly by measuring the forces exerted on the shedder bar. These external sensors are preferred for applications involving highly erosive or corrosive fluids, as they help lower maintenance costs. Meanwhile, internal sensors offer better rangeability and flow sensitivity and are less affected by pipe vibrations. The electronics housing is generally rated for explosion and weatherproofing and contains the electronic transmitter module, connection terminals, and optionally, a flow-rate indicator and/or totalizer.
Vortex Flow Meter Styles
Smart vortex meters offer more than just flow rate measurements; they deliver a digital output signal packed with valuable information. The built-in microprocessor can automatically adjust for insufficient straight pipe lengths, variations between the meter’s bore diameter and the mating pipe, thermal expansion of the bluff body, and changes in the K-factor when the Reynolds number falls below 10,000.
These intelligent transmitters also come equipped with diagnostic routines to detect component failures and other issues. They can run testing procedures on demand to identify problems with both the meter itself and the overall application, aiding in ISO 9000 compliance.
Some vortex flowmeters are capable of measuring mass flow. One design achieves this by simultaneously measuring both the vortex frequency and the strength of the vortex pulses. This dual measurement allows for the calculation of fluid density and mass flow, with an accuracy of within 2% of the span.
Another innovative design features multiple sensors that track vortex frequency along with the temperature and pressure of the process fluid. Using this data, it calculates both density and mass flow rate, achieving an accuracy of 1.25% for liquids and 2% for gases and steam. This meter serves as a cost-effective alternative for users needing temperature and pressure data, eliminating the need for separate transmitters.
Important Features of the Vortex meter
It provides a linear digital (or analog) output signal simplifying equipment installation as the use of separate transmitters or converters is not required. The accuracy of the meter is quite good over a wide flow range. However, this range is dependent upon operating conditions.
The shedding frequency is a function of the bluff body dimensions. Being a frequency system, There is no drift.
In the absence of any moving or wearing components, It provides improved reliability and reduced maintenance. Also, there are no manifolds or valves to cause leakage which in turn results in safe installation even for hazardous or toxic process fluids.
For the sensors with high sensitivity, the same vortex meter can easily be used for both gas and liquid services. Additionally, whether the meter is being used on gas or liquid medium the vortex meter calibration is virtually independent of the process conditions like density, pressure, viscosity, temperature, etc.
It comes with a low installation cost for pipes less than 6-inch size. However, meters above 12 in. (300 mm) have a high cost compared to an orifice system and their limited output pulse resolution. Meters below 0.5 in. (12 mm) diameter is not practical.
Vortex Flow Meter Selection and Sizing
- The operating conditions (process fluid temperature, ambient temperature, line pressure, and so on) should be comparable with the meter specification.
- With respect to chemical attack and safety, the meter-wetted materials (including bonding agents) and sensors should be compatible with the process fluid.
- The vortex meter maximum and minimum flow rates for the specified application need to be established.
- Consequently, the flow range for any application depends totally upon the operating fluid viscosity, density, and vapor pressure, and the application’s maximum flow rate and line pressure.
When selecting a vortex flow meter, consider the following factors:
- Fluid Type: Ensure the meter is compatible with the type of fluid being measured (liquid or gas).
- Flow Range: Verify that the flow meter can handle the expected flow rates.
- Pipe Size: Choose a meter that fits within the diameter of the existing pipeline.
- Temperature and Pressure: Ensure the meter can withstand the operating conditions.
- Installation Requirements: Consider the ease of installation and any additional components needed.
Advantages of Vortex Meter
- Applicable for liquids, gases, and steam, making them versatile.
- Low wear.
- low installation and maintenance costs.
- Low sensitivity to variations in process conditions.
- Long-term accuracy and repeatability.
- With no moving parts, vortex flow meters require less maintenance compared to other types of flow meters.
- Wide process temperature range applicability
- They can withstand high pressures and temperatures, making them suitable for harsh industrial environments.
- Application on a variety of pipe sizes.
- Vortex flow meters provide accurate measurements, often within ±1% of the actual flow rate.
Vortex Flow Meter Limitations
- Not suitable for very low flow rates
- Not recommended for batching or intermittent flow applications. Vortex flow meters can be affected by turbulence, which may lead to inaccuracies.
- Minimum upstream and downstream straight length requirement
- Not suitable for sludge and slurry services.
- Not suitable for Multiphase flow.
- The obstruction can create a pressure drop in the flow system.
Vortex Flow Meter Applications
Vortex flowmeters work best with clean, low-viscosity, and medium to high-speed fluids. Some of the main uses include:
- General water applications
- Liquid chemicals & pharmaceuticals
- Natural gas metering
- Steam measurement
- The flow of liquid suspensions
Types of Vortex Flow Meter Sensors
The vortex flowmeter has a bluff body inside it to create vortices. The Sensors measure these vortices to calculate the equivalent flow rate. Various types of sensors are available as listed below
- Mechanical sensor
- Thermal sensing
- Capacitive sensor
- Piezoelectric sensor
- Strain gauge sensor
- Ultrasonic sensor
Installation Recommendations
- Before installing a vortex flowmeter flow range must be known.
- A well-developed and symmetrical flow velocity profile, free from any distortions or swirls is required for Vortex flow meters. For this reason, most vortex flowmeter manufacturers recommend a minimum of 30 pipe diameters (D) downstream of control valves and 3 to 4 pipe diameters between the meter and downstream pressure taps. Temperature elements should be small and located 5 to 6 diameters downstream.
- For oversized process piping, concentric reducers and expanders may be required.
- These can be installed vertically, horizontally, or at any angle, but the pipe has to be kept in a flooded condition.
- Mating flanges should have the same diameter and smooth bore as the flowmeter. Weld neck flanges are preferred, and reducing flanges should not be used. The inner surface of the mating pipe should be free from mill scale, pits, holes, reaming scores, and bumps for a distance of 4 diameters upstream and 2 diameters downstream of the meter. The bores of the meter, the gaskets, and the adjacent piping must be carefully aligned to eliminate any obstructions or steps.
- The piping on both sides of the meter should be properly supported to eliminate excessive pipe vibration.
To conclude, Vortex flow meters are a reliable and versatile choice for flow measurement in various industries. Their ability to provide accurate readings with minimal maintenance makes them a preferred option for many applications.
Very helpful
Great content. Easy to understand!