In the world of piping and pressure vessel engineering, small details can have a significant impact on the integrity and safety of a system. One such detail is the weep hole—a small but essential feature that plays a key role in ensuring proper functionality and preventing leaks in critical systems. In this article, we’ll explore what a weep hole is, its functions, and why it is an indispensable part of pressure vessel and piping design.
What is a Weep Hole?
A weep hole is a small opening that is strategically placed in pressure vessels, piping systems, or reinforcement pads. In pressure vessel and piping engineering, the weep hole’s primary function is to allow gas or fluid to escape, preventing dangerous pressure build-up and ensuring the structural integrity of the system. Though it’s a simple feature, it serves several crucial purposes during both construction and operation. Weep holes in piping are also known as a tell-tale holes or vent holes. Fig. 1 below shows an example of week-hole for better explaining it
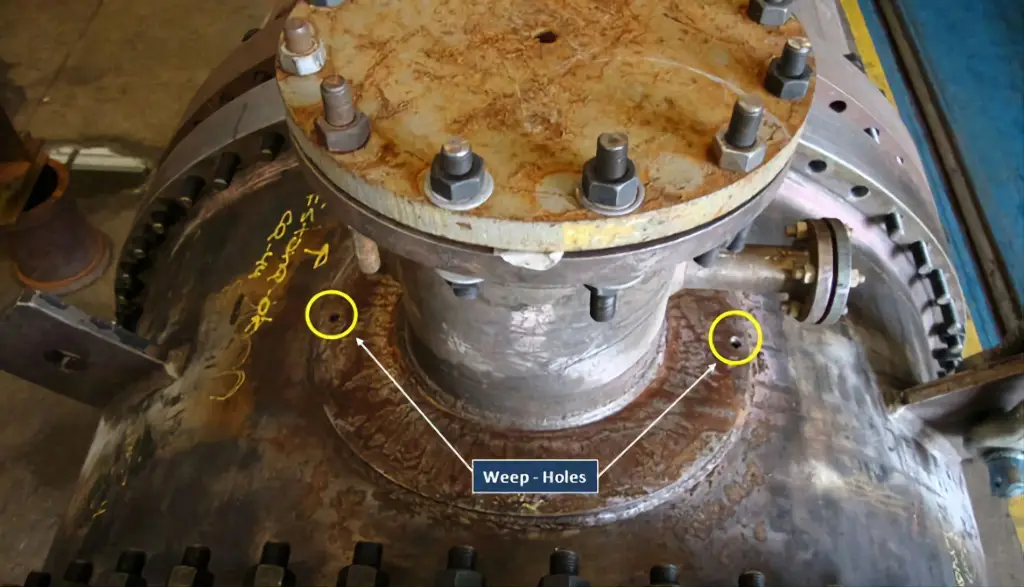
The Role of Weep Holes in Pressure Vessel and Piping Systems
Weep holes are typically integrated into reinforcement pads or welded connections on pressure vessels and piping systems. These pads are added to strengthen areas where nozzles or branches are welded onto the main vessel. However, cutting holes in a pressure vessel to install nozzles can weaken the structure. To compensate for this weakness, reinforcement pads are added, but without a proper means of venting trapped gases during welding, pressure can build up and cause issues. That’s where the weep hole comes in.
Here’s how weepholes function in pressure vessel and piping systems:
1. Venting Gases During the Welding Process
One of the main functions of a weep hole is to act as a vent during the welding of a reinforcement pad. When welding a pad to a nozzle or branch, gases and smoke can become trapped in the space between the pad and the vessel. If these gases are not allowed to escape, pressure can accumulate and cause safety hazards or welding defects. The weep hole provides an outlet for these gases, allowing them to escape during the welding process and preventing the reinforcement pad from becoming a “jacketed” vessel. This venting ensures that the welding process is completed safely, with no risk of pressure-related complications.
Once the welding and pressure testing are complete, the weep hole is sealed to ensure that no further gas or fluid can escape during operation.
2. Enabling Pressure Testing
After installation, weep holes also serve a critical role in pressure testing. The weep hole is typically threaded to accommodate a test gauge, such as a 1/4″ NPT thread. This allows engineers to perform an air or soap test to check for leaks in the system. By applying pressure through the test gauge, it’s possible to detect any leaks around the nozzle and reinforcement pad connection.
If a leak is detected, corrective measures can be taken before the system is put into service. The weep hole thus provides an effective means of testing the integrity of the welds and ensuring that the pressure vessel or piping system is leak-free and safe to operate.
3. Acting as a Telltale for Future Leaks
In the event that a leak occurs in the future, the weep hole acts as a tell-tale, providing early detection of potential issues. If a leak develops beneath the reinforcement pad—due to a crack, corrosion, or other failure—the weep hole allows any gas or liquid to escape, signaling that there may be a problem.
This early detection is vital, as it allows maintenance teams to address issues before they escalate into more severe problems that could compromise the safety or functionality of the system. The weep hole, in essence, serves as a built-in monitoring tool, offering a simple but effective way to spot leaks early.
4. Preventing Dangerous Pressure Build-Up
Another essential function of the weep hole is to prevent the dangerous buildup of pressure within the system. If a leak occurs but goes unnoticed for a period, pressure may begin to accumulate inside the vessel or pipe. Left unchecked, this pressure could lead to further damage or even catastrophic failure. The weep hole ensures that any pressure buildup is relieved gradually, reducing the risk of such failures. By allowing gas or liquid to escape through the hole, the system remains under control even when minor leaks develop.
Sealing the Weep Hole After Testing
Once the pressure test is completed and no leaks are detected, the weep hole is sealed. Typically, this is done by welding the hole shut to prevent any future leakage. Sealing the weep hole ensures that the system remains airtight and safe under operational pressures.
Weep holes are a small yet crucial parts in piping and pressure vessel engineering. Their primary functions—venting gases during welding, enabling pressure testing, providing early leak detection, and preventing pressure build-up—contribute to the safety, durability, and functionality of critical systems. Whether used in the construction phase or as part of ongoing system monitoring, weep holes ensure that pressure vessels and piping systems remain secure and efficient throughout their service lives.
Incorporating weep holes into design and construction is an effective strategy for maintaining structural integrity and reducing the risk of system failures, making them an indispensable feature in the engineering of pressure vessels and piping systems.
Thanks for your article.
It is useful and interesting.