There are no better alternatives to piping and pipeline systems for carrying fluids. But most piping and pipeline systems are subjected to corrosion which reduces the life span and sometimes creates failures. Corrosion is one of the major threats to both piping and pipeline systems. There are two types of piping corrosion; Internal corrosion by the fluid and external corrosion by the environment and thermal effects. Internal corrosion is usually compensated during the design stage by considering extra pipe thickness or by providing internal lining. However, most of the time the external pipe and pipeline corrosion remain unnoticed. In this article, we will explore more about external pipe and pipeline corrosion and some of the means to prevent/reduce external corrosion.
Piping systems are usually designed for a life span of 20 to 25 years and pipeline systems for 10 to 40 years. To ensure that the system works smoothly throughout its design life, the pipe must be protected from corrosion. There are ways by which the extent of external corrosion can be reduced.
The pipe external corrosion that occurs in a pipe or pipeline system can be categorized into two groups.
- Pipe external corrosion due to Prevalent Environmental Condition
- External pipe corrosion on pipe support points due to rubbing (friction) during pipe thermal growth.
In this article, we will learn about corrosion under pipe supports.
Corrosion Under Pipe Supports (CUPS)
An industrial piping system typically rests on supporting structures at intervals predetermined by engineering specifications. These supports can be made from concrete, steel, wood, etc. Such piping systems often vibrate and move due to expansion and contraction (both seasonally and between day and night), rotating equipment such as pumps and compressors, fluid flow, etc. As a result, and due to the physical contact between a pipe and its supporting structure and these types of movements, these contact regions or points often rub and scratch off a pipe’s protective coating. Over time, this removes that protective coating entirely, leaving expensive piping bare and exposed to the elements such as humidity, heat, salt, oxygen, etc.
There is a reduction in airflow in the area where the pipe and support meet, which causes moisture to remain for longer periods. As a result of all these factors, corrosion starts to set in.
Once a pipe starts to corrode, corrosion cells slowly but steadily spread, eating the pipe from the outside in, until it punctures and chemicals leak out, causing lost assets at least, and catastrophic failure and the loss of life at worst.
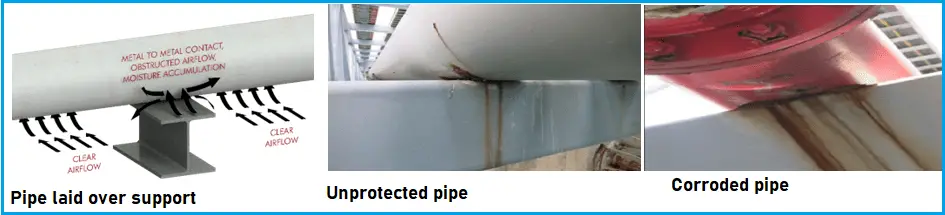
Solving this problem typically involves either protection or inspection and remediation. Inspection can be costly, while remediation oftentimes involves line shutdown and safety hazards, in addition to the actual cost of remediation. Proper protection eliminates this problem before it occurs. To protect piping systems from corrosion, numerous solutions have been developed over the past few decades, with varying degrees of success, failure, and cost.
Existing Solutions for Corrosion under Pipe Supports
Numerous attempts have been made over the past few decades to protect piping systems from corrosion at the pipe support contact points (CUPS). Metal wear plates that cradle a pipe are either fully
welded or tack-welded to a pipe at these contact regions to protect them from friction, and they can be an effective solution.
However, these metallic types of saddles do not stop corrosion, not to mention that the installation process requires line shutdown and welding permits, which would halt production for the duration of the procedure. Metallic wear pads can also become a safety hazard if moisture is trapped in crevices between the pad and the pipe, causing the formation of hidden corrosion cells.
Metal round bars have also been used to raise pipes above their supports to promote airflow. However, such bars point-load the pipe and cause increased stress at the point of contact. This causes more problems than it solves. Their plastic counterparts often fail and break off, or simply cause the same point-loading and damage.
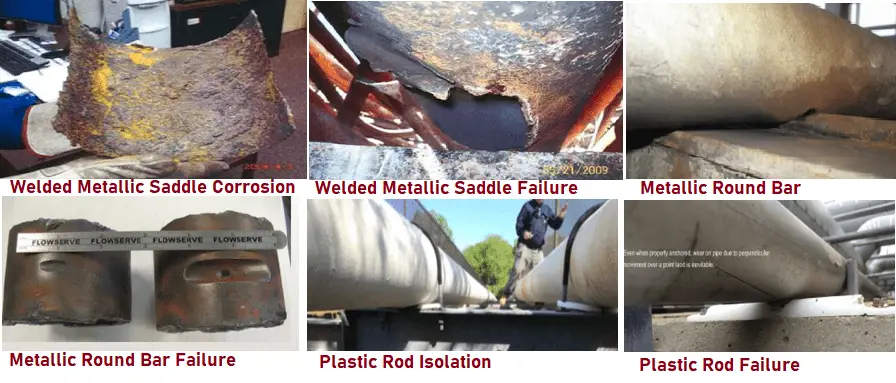
Rubber, Neoprene, TEFLON, and PTFE flat sheets are sometimes wrapped around a pipe in those regions to isolate it from its supporting structures. However, these sheets often slide off, fall off, or are torn apart due to high friction forces, thus exposing the pipe to the elements again. In the end, they all lead to corrosion.
All these solutions, including traditional FRP, wear pads that cradle a pipe and use epoxy to be fastened to a pipe, usually require special inspection procedures to verify their effectiveness over time. Inspection devices and processes, including X-Ray, EMAT, radar, lasers, etc., are costly. Lifting pipes and recoating them at these weakening points is even more costly.
Traditional FRP Wear Pads
Since the design of the SmartPads resembles that of epoxied-on FRP wear pads, we will give these pads a bit more attention and discuss their strengths and weaknesses in greater detail. Epoxied-on, or glued-on, FRP wear pads are a proven and effective solution to combat Corrosion Under Pipe Supports. The pads effectively separate and support the contact region of a pipe without point loading and damaging the pipe over time.
They offer advantages over their metallic counterparts in that there are no metallic components, and as such, they do not require welding permits or line shutdowns.
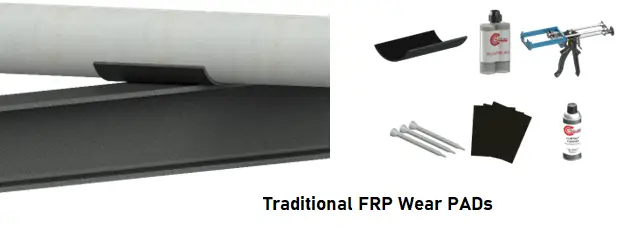
However, FRP wear pads do have a few drawbacks, especially when compared to SmartPads design, as follows:
- The installation process is laborious and can take 15 to 60 minutes, depending on the experience of the installer and various environmental factors.
- Thorough and meticulous pipe surface cleaning and roughening are required for the epoxy to properly adhere to the pipe.
- The installation process requires an additional 24 hours of cure time for the epoxy to effectively bond the pad to the pipe.
- The epoxy must fully cover the inner surface of the pad, and a sealing perimeter bead of epoxy around the entire pad is also required to prevent water molecules from entering the pad/pipe interface. Dirt and other impurities, as well as imperfect workmanship, can all allow water molecules to enter between the pad and the pipe, rendering the pads useless in protecting pipes from corrosion. Replacing or repairing damages caused by trapped moisture can cost thousands to millions of dollars.
- The use of epoxy is particularly cumbersome and messy in the summer and can be almost impossible to use in extremely cold weather conditions.
- Faulty installations are possible; installer experience is critical.
- The process requires several components to be maintained on hand.
- The process may require a paint touchup afterward.
The SmartPads System
The SmartPads System is an innovative solution made from components and materials that have been on the market for many years. However, these components have either been redesigned or are combined in a new and innovative manner to better solve the CUPS problem, at a fraction of the overall cost of competing solutions. Some components are used as-is, while others required some intelligent design modifications to suit the problem at hand and to create a better and more effective pipe corrosion protection solution.
In short, the SmartPads System protects piping systems from CUPS in the following manner:
- The SmartPads themselves are all-composite FRP wear pads with special design modifications, including two recessed grooves to allow SmartBands to sit recessed into the pad’s body. The recesses anchor the bands firmly in place while protecting them from being damaged by the pipe support.
- A closed-cell Hydroseal gasket is pre-installed on the inner surface of each SmartPad. These gaskets are capable of offering NEMA 4 watertight seal when compressed.
- The SmartPad, with its Hydroseal gasket, is placed underneath the pipe at the pipe support point to isolate it from its supporting structure and to protect it from wear.
- Composite SmartBands are looped around each SmartPad into the recessed grooves, and composite buckles are attached to the SmartBands.
- The smart tool is then used to apply a high rate of tension to tighten the SmartBands, thus compressing the Hydroseal gasket. This, along with the pipe’s compressive load, creates a NEMA 4 water-tight seal, effectively eliminating the possibility of moisture ingress between the pad and the pipe.
- Finally, the built-in clipping mechanism of the SmartTool is used to cut off excess banding.
- The installation process takes only seconds.
- The SmartPads can be removed, in seconds, by cutting off the SmartBands to visually inspect the pipe. They can then be reinstalled, again in seconds, using the original SmartPad and gasket.
- The SmartPad’s body will also protect the pipe’s surface from friction at the contact region, thus preserving the pipe’s protective coating.
SmartPads System Components
The SmartPads System consists of four main components, as follows:
- Composite (FRP) SmartPad
- Hydroseal Gasket
- SmartBand & Buckle (all composite)
- Smartwool
- Chemical Resistant Option: Teflon Strips
1- Composite (FRP) SmartPad
The SmartPads are made from a true Laminated Vinyl Ester Composite material. They are designed, manufactured, and tested specifically to be used as pipe supports. The composite material consists of many layers of continuous strand mat laminate (see below), impregnated with top-quality vinyl ester resin.
Most manufacturers of FRP wear pads re-purpose low-cost filament wounds FRP duct or FRP pipe/tubing. These are designed to carry corrosive internal media but were never designed to be used as pipe supports.
The SmartPad’s fiber-reinforced composite material has a high load capacity rating and a low friction surface. This allows the SmartPad to effectively support and protect a pipe as it slides over a beam or support location. The composite material is UV stable and load tested to ensure peak performance in the most demanding applications such as marine, off-shore, and other highly corrosive environments.
2- Hydroseal Gasket
The SmartPad’s Hydroseal gasket is the key component for preventing water molecules from entering the interface between a pad and a pipe to cause corrosion. The gasket consists of a closed-cell structure resembling a memory foam mattress for pipes. Once compressed, the gasket conforms to the pipe’s outer surface, effectively dampening vibration and improving impact resistance.
The key feature of the Hydroseal gasket is the watertight NEMA 4 seal it creates, when it compresses, between a pipe and the SmartPad’s exoskeleton. This solves the prevailing problem associated with FRP wear pads and similar solutions that depend on epoxy to create a watertight seal. The gasket system eliminates the chances of moisture getting trapped between the pad/pipe interface. Once moisture is taken out of the equation, a corrosion cell cannot form. Installer error in an epoxied-on system could lead to moisture traps and severe crevice corrosion issues that could remain hidden and undetected for years; a problem the patented system remedies.
3- SmartBands
The SmartBands are used to fasten SmartPads to pipes. SmartBands are heavy-duty, continuous-strand fiberglass-reinforced polymer straps that do not have any metallic components or parts. When the bands are tensioned using the SmartTool, they will be securely fastened and will not slip or fall off. The only way to remove them is to cut them off. A large amount of tension, combined with the weight of the pipe itself, will cause the Hydroseal gasket to become compressed. This creates the NEMA 4 watertight seal that prevents water molecules from collecting between the pads and the pipe, which causes corrosion (CUPS) over time.
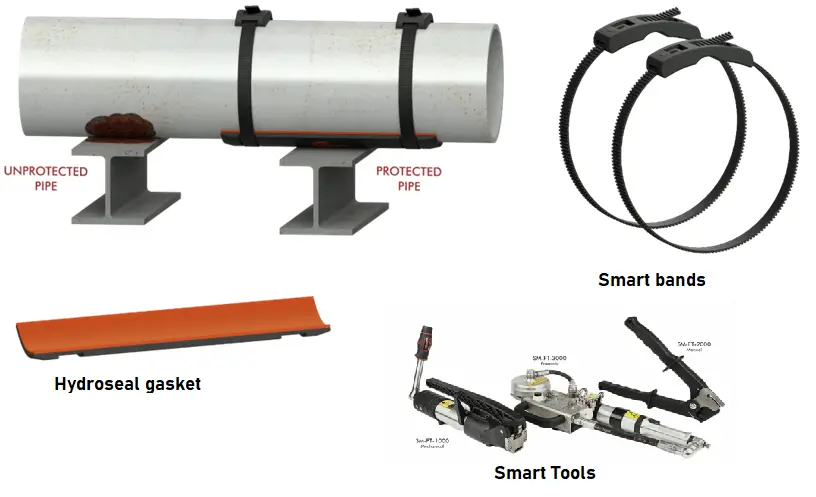
The teeth on each SmartBand will prevent the release of tension over time. This means the NEMA 4 seal will remain as long as the SmartPad is installed, and for the duration of its lifecycle, between 20 and 30 years, and possibly more.
4- SmartTool
The SmartTools is specially designed to tighten the SmartBands, which in turn fastens the SmartPads to the pipe with the necessary tension to be retained for the lifetime of the system. The tool, in all its variants, is capable of creating more than enough force to compress the Hydroseal gasket to create a NEMA 4 watertight seal, without even factoring in the weight of the pipe itself. This mechanism prevents corrosion from ever forming between the pad/gasket and the pipe.
The tools are made from high-grade composite and metallic materials capable of applying high rates of force without damage or deformation. Their design entails ergonomic hand grips, for both convenience and proper operation. A built-in mechanism to cut off excess banding is included, for both convenience and speed of operation.
SmartTools come in three varieties: Manual for quick operation, mechanical for precise application of specific force ratings per engineering standards, and pneumatic for quick installation of large numbers of SmartPads.
5- Optional: TEFLON Strips, Chemical Resistant Option
Some chemical processes involve highly corrosive materials that may damage the SmartPad or the Hydroseal gasket. As such, a TEFLON strip can be applied to the perimeter of the Hydroseal gasket to protect it as well as the edges of the SmartPad from such corrosive chemicals. A wide variety of materials can be utilized for this purpose, with TEFLON being the most common. This strip is represented by the white material at the perimeter of the model.
SmartPads System Benefits
The SmartPads System is the latest of many competing solutions designed to solve the expensive problem of corrosion under pipe support (CUPS). While each solution has its pros and cons, the SmartPads System offers numerous advantages and benefits that no other solution offers or combines. Among such benefits are:
- Heavy-duty, all-composite material
- Eliminates metal-to-metal contact
- Prevents external corrosion in piping systems at the pipe support points
- Epoxyless SmartPads offer effective corrosion protection benefits without the problems associated with epoxied-on FRP wear pads
- Installs in seconds
- Quick removal and reinstallation
- Allows visual inspection for corrosion, in seconds
- 100% install success rate
- NEMA 4 watertight seal between pipe and pad/gasket
- Removable: In seconds, allowing future visual inspections at reduced labor costs (approx. half the overall cost)
- Reusable: Cost-effective and green solution
- Versatile: Offers a wide range of gasket materials to meet specific applications, including corrosive chemicals resistant options
- Dampens vibration and noise
- Installs on live lines
- No welding permits or line shutdown required
- -60°F to 400°F (-51°C to 204°C) operating temperature
Speed of Installation
The SmartPads System has no viable competitor when it comes to ease and speed of installation. The pads install in seconds, while other solutions entail the long processes of welding or the application of epoxy or adhesives. For example, epoxied-on FRP wear pads can take 15-30 minutes to install, plus an additional 24 hours or more of epoxy cure time, depending on ambient temperature, humidity, and other environmental factors. Installer experience also plays a major role in the successful installation of these pads. The SmartPads System does not require any cure time. Also, installers are not required to perform any touch-up work to seal the pad to the pipe, since no epoxy is involved. Furthermore, the self-sealing Hydroseal gasket is designed to reduce the risk of a faulty installation, making the system even safer and more efficient.
Additionally, and in the rare occasion a SmartPad, for one reason or another, is installed incorrectly, or installed at the wrong location, it can be easily removed and re-installed, with minimal time and cost requirements. The same applies if a SmartPad must be removed for visual inspection purposes; this process will only take seconds. Epoxied-on FRP wear pads cannot be removed once the epoxy cures, even for inspection purposes, unless chiseled off. Welded metallic wear pads will be even harder to remove.
SmartPads in Operation
The SmartPad System has been in service since 2018 in facilities near the Gulf of Mexico. Currently, a few major customers are deploying the system in pilot programs, for both assessment purposes and full adoption. Among those customers are Chevron, Formosa, and Nutrien, all located in the Gulf of Mexico or near coastal regions. Further information about smart pads systems can be found by clicking here
Online Video Courses on Piping Support
To learn more about piping support design and engineering you can opt for the following video course.