Advanced Process Control or APC refers to various techniques and technologies that interact with process control systems. Advanced process controls are often deployed on top of the basic process controls built around PID control. It is a cost-effective way to optimize plant performance without changing the hardware. Today APC is almost a commodity in refineries and large petrochemical complexes, like ethylene crackers and polymer plants. In this blog post we will discuss about the working and benefits of Advanced Process Control.
What is Advanced Process Control?
Advanced Process Control (APC) is a control solution that increases process performance. APC communicates with the plant’s distributed control system (DCS) or programmable logic controllers (PLC) as a level-two optimization application via an OPC server that closes the loop between plant information and field actuators.
Enabling APCs to operate more efficiently requires a combination of regular tunings and a comprehensive approach that addresses sensors, devices, and control loops, as well as educating and training control-room operators on the latest techniques. With the recent advances in computing power (and lower computing costs), APCs can be tuned using machine-learning models, and advanced analytics can produce responsive insights from large amounts of historical data, increasing the speed of the tuning process and reducing human bias or intervention.
How Advanced Process Controls Work
The way organizations utilize control logic can be visualized as a pyramid. APCs sit near the top, executing set points with base-layer controllers (BLCs) such as programmable logic controllers or distributed control systems (Figure 1). In this sense, APCs facilitate communication between system-level controls, subsystems (sensors and instruments), and equipment (the actual machinery).
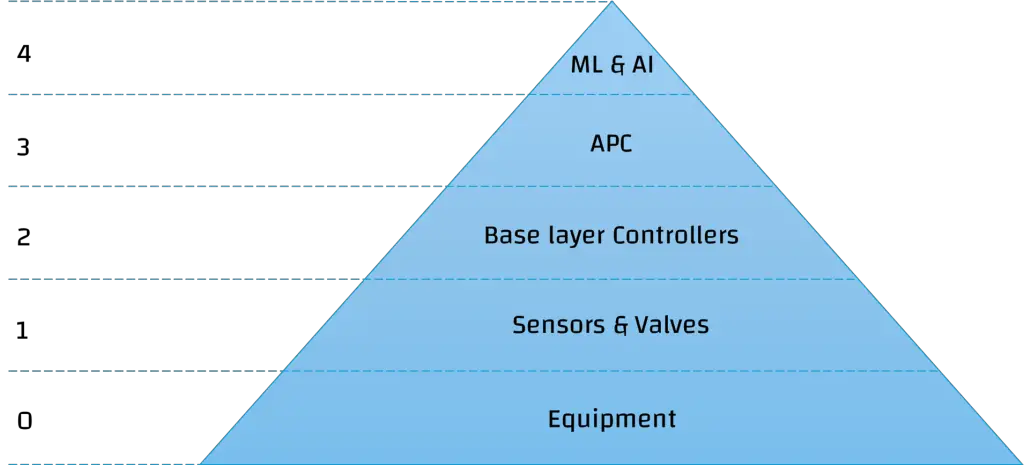
APCs are only as good as the set-point targets and constraints inputted by operators and the quality of measured process variable data. Yet, many companies have neglected to review their set points for years.
Others simply don’t have the required in-house capabilities to maintain their APCs and are therefore dependent on vendors. Managing these relationships requires clearly defined strategies, and companies that already struggle with optimization are sometimes left in the dark. Relying solely on an already-lacking, in-house maintenance strategy for underlying control loops, equipment, and sensors will inevitably result in less-than-ideal APC performance.
Advantages of Advanced Process Controls
There are many benefits APC can offer you. These are the most common benefits generated by APC systems on many different industrial processes:
- Reduced process variations beyond what is possible with traditional PID control.
- More hands-off operation. Under normal operating conditions, operators would not need to touch the process at all.
- Operate the plant always at the optimum. This can be at the maximum throughput, the lowest specific energy consumption, the point with the highest margins, or combinations of the above.
- APC respects under all conditions the process limits resulting in improved safety
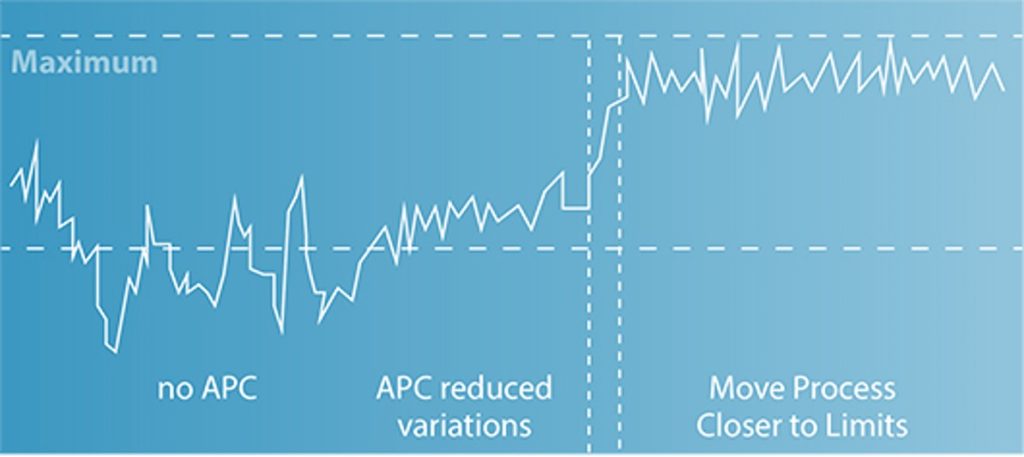
APC enables you to optimize your plant performance without changing the hardware. This makes APC solutions very cost-effective.
Conclusion
Large process revamps can increase the production capacity by 10% to 40% at the cost of sometimes a hundred million dollars/euros. The capacity increase is more in the range of 1% to 5% at the cost of a few hundred thousand dollars/euros.
Besides pure production increase or lower specific energy consumption APC also brings other benefits:
- More stable operations, meaning less variations.
- Less operator interventions
- Reduced alarms
- Less wear and tear on the equipment resulting in longer run lengths, less downtime
- a better understanding of the process