An anti-surge valve, also known as a surge-anticipating valve, is a type of control valve (surge relief valve) used in fluid systems to prevent overpressure and pressure surges that can damage equipment or cause system failure. It is typically used in systems that have rapidly changing flow rates, such as in turbocharged engines, compressors, and pumps. The valve is designed to open and release pressure when the system pressure exceeds a pre-determined set point, allowing the system to operate within a safe pressure range and preventing damage to the system.
Functions of an Anti-Surge Valve
The main function of an anti-surge valve is to protect equipment and systems from overpressure and pressure surges that can occur during rapid changes in flow rate. Some of the specific functions of an anti-surge valve include:
- Preventing damage to the equipment: by releasing pressure when the system pressure exceeds a set point, the valve helps to prevent damage to the system and its components.
- Maintaining system stability: by regulating pressure, the valve helps to maintain the system stability and prevent system failure.
- Improving system efficiency: by preventing pressure surges, the valve can improve system efficiency by reducing the amount of energy required to operate the system.
- Reducing noise: by releasing pressure, the valve can also reduce noise in the system caused by pressure surges.
- Minimizing downtime: by protecting the system from overpressure and pressure surges, the valve helps to minimize downtime and reduce maintenance costs.
- Controlling the flow: anti-surge valves can be used to control the flow of fluid or gas in the system.
- Protecting compressors and pumps: anti-surge valves are commonly used in systems that have rapidly changing flow rates, such as in turbocharged engines, compressors, and pumps.
Working of Anti Surge Valves
An anti-surge valve works by monitoring the system pressure and opening to release pressure when the pressure exceeds a pre-determined set point. The valve is typically installed in the system at a location where the pressure is highest and most susceptible to surges.
The valve typically consists of a valve body, a valve seat, a spring, and a piston or diaphragm. When the system pressure is within the safe range, the spring keeps the valve closed, and the piston or diaphragm is held against the valve seat, preventing flow through the valve.
When the system pressure exceeds the set point, the pressure acts against the piston or diaphragm, compressing the spring and lifting the valve of the seat. This allows the system pressure to be released through the valve, reducing the pressure to a safe level.
When the pressure drops back to the set point, the spring forces the valve back onto the seat, closing the valve and stopping the flow. Some anti-surge valves are also equipped with a control system that can automatically adjust the set point to match the changing conditions of the system, while others have manual adjustments.
Anti-surge valves are typically designed to open and close quickly, in order to respond quickly to pressure changes and protect the system from overpressure and pressure surges. Fig. 1 below shows typical anti-surge valves.
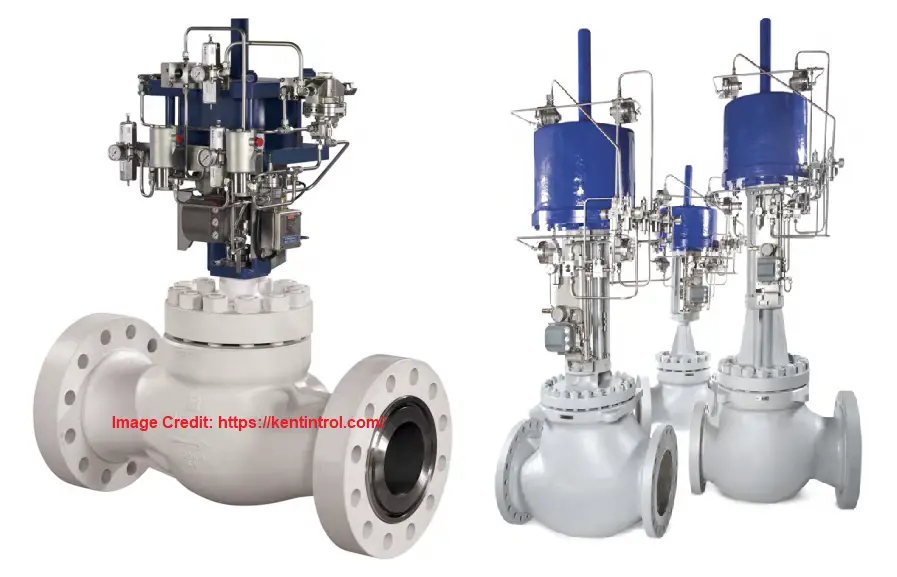
Anti Surge Valve Requirements
Anti-surge valves have several requirements that need to be considered when selecting and installing them in a system:
- Set point: the set point of the valve is the pressure at which the valve will open and release pressure. It is important to select a set point that will protect the system and its components from overpressure and pressure surges.
- Flow rate: the valve must be able to handle the flow rate of the system in order to effectively release pressure. The valve size and type must be selected based on the flow rate of the system.
- Pressure drop: the valve must be able to release pressure without creating a significant pressure drop in the system. The pressure drop must be minimized in order to maintain system efficiency. The design shall be sufficient to handle high-pressure drops if the situation arises.
- Response time: the valve must respond quickly to pressure changes in order to protect the system from overpressure and pressure surges. The response time of the valve must be fast enough to meet the needs of the system.
- Material: the valve material must be compatible with the fluid or gas in the system in order to prevent corrosion or damage to the valve.
- Environment: the valve must be able to withstand the environmental conditions of the system, such as temperature, vibration, and external impacts.
- Control: the valve must be equipped with a control system that can automatically adjust the set point to match the changing conditions of the system or manual adjustments.
- Safety: the valve must be designed and installed in a way that ensures safety for the operators and maintenance personnel.
- Maintenance: the valve must be designed for easy maintenance and repair, to minimize downtime and reduce maintenance costs.
- Cost: the cost of the valve must be considered in relation to the overall cost of the system and the potential savings from preventing damage and downtime.
- Good Stroke Speed: the anti-surge valve must be having good stroke speed
- Size: the valve shall be properly sized to control the surge.
- Valve Construction: To handle extreme service conditions, the construction must be robust.
Design of Anti Surge Valve
Designing an anti-surge valve involves several steps, including:
Define the system requirements: The first step in designing an anti-surge valve is to define the requirements of the system, including the set point, flow rate, pressure drop, response time, and material compatibility.
Determine the surge volume: The surge volume is the volume of fluid that needs to be released by the anti-surge valve in order to prevent overpressure and pressure surges. This can be calculated by using system models and simulations.
Select the valve size and type: Based on the surge volume, the valve size and type can be selected. The valve size should be large enough to handle the flow rate and the type should be appropriate for the fluid or gas in the system.
Consider the control system: An anti-surge valve must be equipped with a control system that can automatically adjust the set point to match the changing conditions of the system. It could be manual adjustment too.
Consider the environment: The valve must be able to withstand the environmental conditions of the system, such as temperature, vibration and external impacts.
Testing: Once the valve has been designed and built, it should be tested to ensure that it meets the requirements of the system and is able to effectively release pressure and prevent overpressure and pressure surges.
It’s important to note that anti-surge valves are a critical component in systems that have rapidly changing flow rates, and the design should be carried out by experienced engineers and based on established standards and guidelines.
Anti-Surge Valve Specification
To specify an anti surge valve the following parameters must be defined in the datasheet:
- Valve Size
- Valve Style
- Pressure Rating
- Body Material
- Actuator Type
- Valve Trim Details
- Valve End Connections
- Temperature and Pressure ranges
- Shut Off characteristics
- Rated Valve Coefficient, Cv
- Leakage Class
- Time for a full stroke
- Predicted Noise at the maximum flow
- Action on failure
Manufacturers of Anti-Surge Valves
There are many manufacturers of anti-surge valves worldwide, some of the well-known ones include:
- Dresser Masoneilan
- Fisher Control Valves
- Flowserve
- KSB
- Metso
- Neles
- Pentair
- Spirax Sarco
- Velan
- Beker Hughes
- Emerson Automation Solutions.
These manufacturers offer a wide range of anti-surge valves in different sizes, types, and materials to meet the needs of different systems and applications. They also provide technical support and service to ensure proper installation, operation, and maintenance of the valves. It’s important to note that the selection of the manufacturer and supplier should be based on their reputation, brand, certifications, standards compliance, and technical support service.
Anti Surge Valves in Compressors
Anti-surge valves in compressors are used to prevent overpressure and pressure surges that can occur in systems with rapidly changing flow rates. Click here to learn about Centrifugal compressor Surge and Control. The valve is typically installed in the compressor system at a location where the pressure is highest and most susceptible to surges.
When the compressor is working, the flow of gas is steady and the pressure remains within a safe range. However, when the compressor is shut off or when the flow rate suddenly decreases, the pressure in the system can rise rapidly. This is called a “surge” and if not controlled, it can cause damage to the compressor and the system.
An anti-surge valve in a compressor system functions by monitoring the system pressure and opening to release pressure when the pressure exceeds a pre-determined set point. This allows the pressure to be released, reducing it to a safe level and preventing damage to the compressor and the system.
Anti-surge valves in compressors are designed to open and close quickly, in order to respond quickly to pressure changes and protect the system from overpressure and pressure surges. They are also equipped with a control system that can automatically adjust the set point to match the changing conditions of the system, ensuring the safe and efficient operation of the compressor.
Why are the illustrations blanked out?
Yes, same question for me …