ASTM A182 is a widely recognized specification for forged or rolled alloy and stainless steel pipe flanges, fittings, valves, and other components. ASTM A182 material is mainly used in high-temperature and high-pressure applications. This standardized specification, developed by the American Society for Testing and Materials (ASTM), outlines the mechanical and chemical properties required for the manufacturing of these critical components. In this blog post, we will delve into the features, applications, and benefits of ASTM A182, highlighting its significance in various industries.
Grades of ASTM A182 Materials
ASTM A182 covers a wide range of grades for forged or rolled alloy and stainless steel pipe flanges, forged fittings, and valves. The grades of ASTM A182 material are designated by a combination of letters and numbers. Here are some of the commonly used grades:
- ASTM A182-F1: Low alloy steel is typically used for low-temperature service.
- ASTM A182-F5: Chromium-molybdenum alloy steel with enhanced high-temperature strength. Suitable for elevated temperature applications.
- ASTM A182-F9: Chromium-molybdenum alloy steel with improved creep resistance and resistance to high-temperature corrosion. Often used in refineries and power plants.
- ASTM A182-F11: Low alloy steel with enhanced creep resistance. Available in three classes: Class 1, Class 2, and Class 3.
- ASTM A182-F22: Chromium-molybdenum alloy steel with excellent creep strength and resistance to oxidation and corrosion.
- ASTM A182-F91: High strength, low alloy steel with good toughness and high-temperature strength. Suitable for power generation and petrochemical applications.
- ASTM A182-F304: Austenitic stainless steel with 18% chromium and 8% nickel. It is the most commonly used stainless steel grade.
- ASTM A182-F316: Austenitic stainless steel with 16-18% chromium, 10-14% nickel, and 2-3% molybdenum. It offers improved corrosion resistance compared to F304.
- ASTM A182-F321: Titanium-stabilized austenitic stainless steel with a similar composition to F304 but with added titanium for enhanced resistance to intergranular corrosion.
- ASTM A182-F347: Niobium-stabilized austenitic stainless steel with improved resistance to sensitization and intergranular corrosion.
- ASTM A182-F51 (Duplex Stainless Steel): A dual-phase stainless steel with a balanced combination of ferrite and austenite phases. It offers high strength and improved resistance to stress corrosion cracking.
- ASTM A182-F53 (Super Duplex Stainless Steel): A highly alloyed stainless steel with excellent corrosion resistance and high strength.
- ASTM A182-F55 (Super Duplex Stainless Steel): A super duplex stainless steel grade with enhanced resistance to corrosion and high mechanical strength.
Table 1, 2, and 3 provides all the grades of ASTM A182 material.
Chemical Composition of ASTM A182 Materials
ASTM A182 covers a broad range of materials, including alloy steels, stainless steels, and superalloys, each with its own unique composition and mechanical properties. Fig. 1 below shows the chemical composition of some of the ASTM A182 material grades.
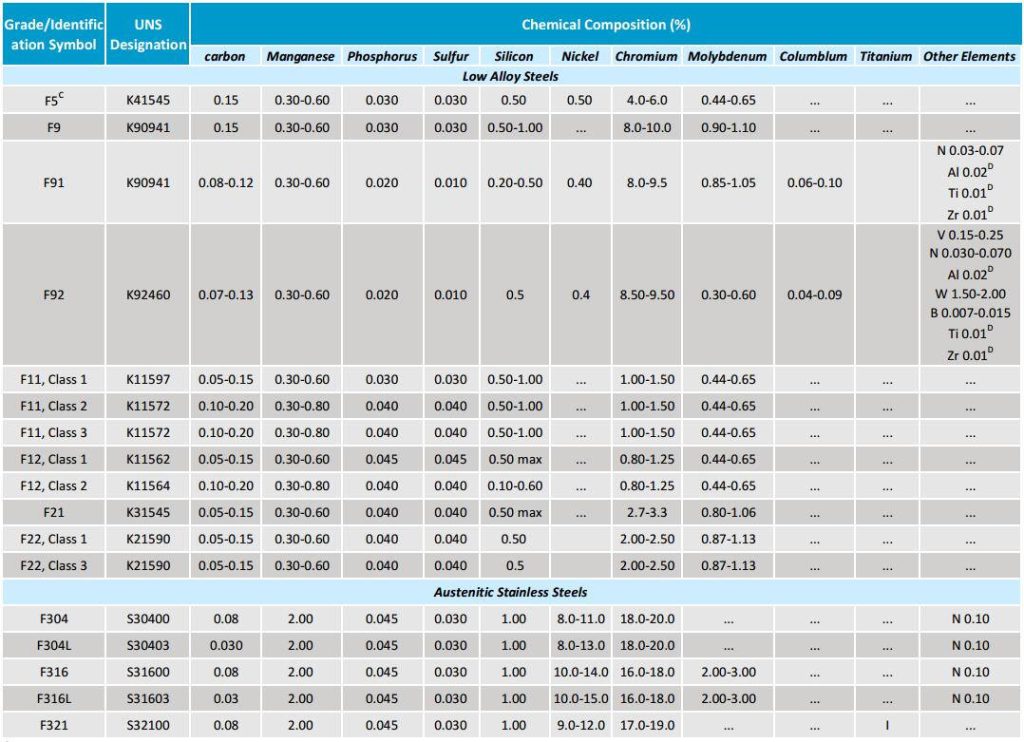
Mechanical Properties of ASTM A182 Materials
The alloy steels (grades F1 to F91) are known for their excellent strength and toughness, while stainless steels (grades F304, F316, F321, etc.) offer exceptional corrosion resistance. Superalloys like Inconel, Hastelloy, and Monel possess high-temperature strength and oxidation resistance. The mechanical properties specified by ASTM A182, such as tensile strength, yield strength, elongation, and hardness, ensure the reliability and performance of the components manufactured from these materials.
The mechanical properties of some of the ASTM A182 alloy grades are provided below:
Grade Symbol | Tensile Strength, min, ksi | Tensile Strength, min, [MPa] | Yield Strength, min, ksi [MPa] | Elongation in 2 in. [50 mm] or 4D, min, % | Reduction of Area, min, % | Brinell Hardness Number, HBW, |
---|---|---|---|---|---|---|
F 1 | 70 | [485] | 40 [275] | 20 | 30 | 143–192 |
F 2 | 70 | [485] | 40 [275] | 20 | 30 | 143–192 |
F 5 | 70 | [485] | 40 [275] | 20 | 35 | 143–217 |
F 5a | 90 | [620] | 65 [450] | 22 | 50 | 187–248 |
F 9 | 85 | [585] | 55 [380] | 20 | 40 | 179–217 |
F 10 | 80 | [550] | 30 [205] | 30 | 50 | . . . |
F 91 Types 1 and 2 | 90 | [620] | 60 [415] | 20 | 40 | 190–248 |
F 92 | 90 | [620] | 64 [440] | 20 | 45 | 269 max |
F 93 | 90 | [620] | 64 [440] | 19 | 40 | 250 max |
F 115 | 90 | [620] | 65 [450] | 20 | 40 | 190–248 |
F 122 | 90 | [620] | 58 [400] | 20 | 40 | 250 max |
F 911 | 90 | [620] | 64 [440] | 18 | 40 | 187–248 |
F 11 Class 1 | 60 | [415] | 30 [205] | 20 | 45 | 121–174 |
F 11 Class 2 | 70 | [485] | 40 [275] | 20 | 30 | 143–207 |
F 11 Class 3 | 75 | [515] | 45 [310] | 20 | 30 | 156–207 |
F 12 Class 1 | 60 | [415] | 32 [220] | 20 | 45 | 121–174 |
F 12 Class 2 | 70 | [485] | 40 [275] | 20 | 30 | 143–207 |
F 21 | 75 | [515] | 45 [310] | 20 | 30 | 156–207 |
F 3V, and F 3VCb | 85–110 | [585–760] | 60 [415] | 18 | 45 | 174–237 |
F 22 Class 1 | 60 | [415] | 30 [205] | 20 | 35 | 170 max |
F 22 Class 3 | 75 | [515] | 45 [310] | 20 | 30 | 156–207 |
F 22V | 85–110 | [585–780] | 60 [415] | 18 | 45 | 174–237 |
F 23 | 74 | [510] | 58 [400] | 20 | 40 | 220 max |
F 24 | 85 | [585] | 60 [415] | 20 | 40 | 248 max |
FR | 63 | [435] | 46 [315] | 25 | 35 | 197 max |
F 36, Class 1 | 90 | [620] | 64 [440] | 15 | . . . | 252 max |
F 36, Class 2 | 95.5 | [660] | 66.5 [460] | 15 | . . . | 252 max |
Grade Symbol | Tensile Strength, min, ksi | Tensile Strength, min, [MPa] | Yield Strength, min, ksi [MPa]B | Elongation in 2 in. [50 mm] or 4D, min, % | Reduction of Area, min, % | Brinell Hardness Number, HBW, |
---|---|---|---|---|---|---|
F 6a Class 1 | 70 | [485] | 40 [275] | 18 | 35 | 143–207 |
F 6a Class 2 | 85 | [585] | 55 [380] | 18 | 35 | 167–229 |
F 6a Class 3 | 110 | [760] | 85 [585] | 15 | 35 | 235–302 |
F 6a Class 4 | 130 | [895] | 110 [760] | 12 | 35 | 263–321 |
F 6b | 110–135 | [760–930] | 90 [620] | 16 | 45 | 235–285 |
F 6NM | 115 | [790] | 90 [620] | 15 | 45 | 295 max |
F XM-27Cb | 60 | [415] | 35 [240] | 20 | 45 | 190 max |
F 429 | 60 | [415] | 35 [240] | 20 | 45 | 190 max |
F 430 | 60 | [415] | 35 [240] | 20 | 45 | 190 max |
Grade Symbol | Tensile Strength, min, ksi | Tensile Strength, min, [MPa] | Yield Strength, min, ksi [MPa] | Elongation in 2 in. [50 mm] or 4D, min, % | Reduction of Area, min, % | Brinell Hardness Number, HBW, unless otherwise indicated |
---|---|---|---|---|---|---|
F 304 | 75 | [515] | 30 [205] | 30 | 50 | . . . |
F 304H | 75 | [515] | 30 [205] | 30 | 50 | . . . |
F 304L | 70 | [485] | 25 [170] | 30 | 50 | . . . |
F 304N | 80 | [550] | 35 [240] | 30 | 50 | . . . |
F 304LN | 75 | [515] | 30 [205] | 30 | 50 | . . . |
F 309H | 75 | [515] | 30 [205] | 30 | 50 | . . . |
F 310 | 75 | [515] | 30 [205] | 30 | 50 | . . . |
F 310MoLN | 78 | [540] | 37 [255] | 25 | 40 | . . . |
F 310H | 75 | [515] | 30 [205] | 30 | 50 | . . . |
F 316 | 75 | [515] | 30 [205] | 30 | 50 | . . . |
F 316H | 75 | [515] | 30 [205] | 30 | 50 | . . . |
F 316L | 70 | [485] | 25 [170] | 30 | 50 | . . . |
F 316N | 80 | [550] | 35 [240] | 30 | 50 | . . . |
F 316LN | 75 | [515] | 30 [205] | 30 | 50 | . . . |
F 316Ti | 75 | [515] | 30 [205] | 30 | 40 | . . . |
F 317 | 75 | [515] | 30 [205] | 30 | 50 | . . . |
F 317L | 70 | [485] | 25 [170] | 30 | 50 | . . . |
F 72 | 80 | [550] | 36 [245] | 35 | 50 | 217 |
F 73 | 93 | [640] | 43 [295] | 40 | 50 | 217 |
F 347 | 75 | [515] | 30 [205] | 30 | 50 | . . . |
F 347H | 75 | [515] | 30 [205] | 30 | 50 | . . . |
F 347LN | 75 | [515] | 30 [205] | 30 | 50 | . . . |
F 347LNCuB | 75 | [515] | 30 [205] | 30 | 50 | . . . |
F 348 | 75 | [515] | 30 [205] | 30 | 50 | . . . |
F 348H | 75 | [515] | 30 [205] | 30 | 50 | . . . |
F 321 | 75 | [515] | 30 [205] | 30 | 50 | . . . |
F 321H | 75 | [515] | 30 [205] | 30 | 50 | . . . |
F XM-11 | 90 | [620] | 50 [345] | 45 | 60 | . . . |
F XM-19 | 100 | [690] | 55 [380] | 35 | 55 | . . . |
F 20 | 80 | [550] | 35 [240] | 30 | 50 | . . . |
F 44 | 94 | [650] | 44 [300] | 35 | 50 | . . . |
F 45 | 87 | [600] | 45 [310] | 40 | 50 | . . . |
F 46 | 78 | [540] | 35 [240] | 40 | 50 | . . . |
F 47 | 75 | [525] | 30 [205] | 40 | 50 | . . . |
F 48 | 80 | [550] | 35 [240] | 40 | 50 | . . . |
F 49 | 115 | [795] | 60 [415] | 35 | 40 | . . . |
F 56 | 73 | [500] | 27 [185] | 30 | 35 | . . . |
F 58 | 109 | [750] | 61 [420] | 35 | 50 | . . . |
F 62 | 95 | [655] | 45 [310] | 30 | 50 | . . . |
F 63 | 80 | [550] | 32 [220] | 25 | . . . | 192 max |
F 64 | 90 | [620] | 40 [275] | 35 | 50 | 217 max |
F70 | 70 | [480] | 25 [175] | 35 | . . . | HRB 90 max |
F 904L | 71 | [490] | 31 [215] | 35 | . . . | . . . |
F700 | 80 | [550] | 35 [240] | 30 | . . . | 192 |
FNIC | 65 | [450] | 25 [170] | 30 | . . . | . . . |
FNIC10 | 65 | [450] | 25 [170] | 30 | . . . | . . . |
FNIC11 | 65 | [450] | 25 [170] | 30 | . . . | . . . |
F1925 | 87 | [600] | 43 [295] | 30 | . . . | . . . |
F1925N | 94 | [650] | 43 [295] | 35 | . . . | . . . |
F 50 | 100–130 | [690–900] | 65 [450] | 25 | 50 | . . . |
F 51 | 90 | [620] | 65 [450] | 25 | 45 | . . . |
F 52 | 100 | [690] | 70 [485] | 15 | . . . | . . . |
F 53 ≤ 2 in. [50 mm]G Class 1 | 114 | [785] | 76 [525] | 30 | . . . | 310 max |
F 53 ≤ 2 in. [50 mm]G Class 2 | 116 | [800] | 80 [550] | 15 | . . . | 310 max |
F 53 > 2 in. [50 mm] | 106 | [730] | 75 [515] | 15 | . . . | 310 max |
F 54 | 116 | [800] | 80 [550] | 15 | 30 | 310 max |
F 55 | 109–130 | [750–895] | 80 [550] | 25 | 45 | . . . |
F 57 | 118 | [820] | 85 [585] | 25 | 50 | . . . |
F 59 | 112 | [770] | 80 [550] | 25 | 40 | . . . |
F 60 | 95 | [655] | 65 [450] | 25 | 45 | . . . |
F 61 | 109 | [750] | 80 [550] | 25 | 50 | . . . |
F 65 | 109 | [750] | 80 [550] | 25 | . . . | . . . |
F 66 | 94 | [650] | 65 [450] | 30 | . . . | 290 max |
F 67 | 90 | [620] | 65 [450] | 18 | . . . | 302 |
F 68 | 87 | [600] | 58 [400] | 25 | . . . | 290 max |
F 69 | 94 | [650] | 65 [450] | 30 | . . . | . . . |
F 71 | 101 | [700] | 72 [500] | 15 | . . . | 321 |
ASTM A182 Flanges
ASTM A182 flanges are widely used in piping systems to connect pipes, valves, and other equipment. These flanges are available in various types, including welding neck, slip-on, blind, socket weld, threaded, and lap joint flanges. They are designed to withstand high-pressure and high-temperature environments, making them suitable for applications in oil and gas, petrochemical, power generation, and other heavy industries. The dimensional standards specified by ASTM A182 ensure the compatibility and interchangeability of flanges across different manufacturers.
ASTM A182 Fittings
ASTM A182 fittings are used for joining or adapting pipes of different sizes or shapes within a piping system. These fittings include elbows, tees, reducers, couplings, and unions. With their excellent mechanical properties and corrosion resistance, A182 fittings provide leak-free connections and maintain the integrity of the piping system. These fittings can be butt-welded, socket-welded, or threaded, depending on the application requirements.
ASTM 182 Valves
ASTM A182 valves are critical components in controlling the flow of fluids in pipelines. They are available in a wide range of designs, such as gate valves, globe valves, ball valves, and check valves. The materials specified by A182 ensure the valves’ durability, reliability, and resistance to erosion, corrosion, and high-temperature environments. These valves find extensive use in industries like oil and gas, chemical processing, power generation, and water treatment.
Applications and Benefits
ASTM A182 materials and components find applications in various industries, including oil and gas, petrochemical, power generation, chemical processing, marine, and aerospace. The key benefits of ASTM A182 materials include:
Strength and Durability:
ASTM A182 materials exhibit high strength, allowing them to withstand extreme operating conditions and pressures. Their excellent durability ensures long-term performance and minimizes maintenance requirements.
Corrosion Resistance:
Stainless steel grades specified in ASTM A182 offer outstanding resistance to corrosion, ensuring the integrity of the components even in aggressive environments.
Wide Temperature Range:
A182 materials are designed to perform at elevated temperatures, making them suitable for applications involving high-temperature fluids or gases.
Versatility:
The broad range of alloys and stainless steels specified by A182 allows for selecting the most suitable material for specific applications, balancing factors such as strength, corrosion resistance, and cost.
What is ASTM A182 F316L material and what are its applications?
ASTM A182 F316L is a specification for forged or rolled alloy and stainless steel pipe flanges, forged fittings, and valves intended primarily for high-temperature and corrosive service. F316L is the low-carbon version of F316, which means it contains a lower carbon content to improve weldability and reduce the risk of carbide precipitation in the heat-affected zone during welding.
The material composition of ASTM A182 F316L includes:
- Carbon (C): Maximum 0.03%
- Manganese (Mn): Maximum 2.00%
- Phosphorus (P): Maximum 0.045%
- Sulfur (S): Maximum 0.030%
- Silicon (Si): Maximum 0.75%
- Chromium (Cr): 16.0-18.0%
- Nickel (Ni): 10.0-15.0%
- Molybdenum (Mo): 2.0-3.0%
The addition of molybdenum enhances the corrosion resistance of F316L, particularly in chloride-containing environments. This makes it suitable for various applications in industries such as chemical processing, petrochemical, oil and gas, pharmaceutical, food and beverage, and marine.
Here are some common applications of ASTM A182 F316L:
- Chemical Processing: F316L is widely used in chemical plants for handling corrosive chemicals, acids, and solvents. It is suitable for applications such as reactors, heat exchangers, valves, and piping systems.
- Petrochemical Industry: F316L is commonly utilized in the petrochemical industry for equipment and piping systems that handle aggressive media, high temperatures, and high pressures. Examples include refinery equipment, distillation columns, and pipelines.
- Oil and Gas: F316L is employed in offshore and onshore oil and gas applications due to its excellent resistance to chloride-induced stress corrosion cracking (SCC). It is used in pipelines, valves, fittings, and wellhead equipment.
- Pharmaceutical Industry: F316L meets the stringent requirements of the pharmaceutical industry for clean and hygienic processing environments. It is used in equipment such as storage tanks, piping systems, and pharmaceutical-grade valves.
- Food and Beverage Industry: F316L is preferred in food processing and beverage production due to its corrosion resistance and low risk of contamination. It is utilized in equipment like tanks, piping, heat exchangers, and fittings.
- Marine Applications: F316L is resistant to corrosion in seawater environments, making it suitable for marine applications. It is used in shipbuilding, offshore platforms, and desalination plants.
Conclusion
ASTM A182 plays a vital role in the manufacturing of alloy and stainless steel pipe flanges, fittings, valves, and other components used in critical applications. Its comprehensive specifications ensure the mechanical and chemical properties required for reliable performance in high-temperature and high-pressure environments. By incorporating ASTM A182 materials, industries can ensure the strength, durability, and corrosion resistance of their piping systems, contributing to enhanced safety and operational efficiency.