What is Autopipe?
Autopipe is a computer-based engineering program to determine pipe stresses, pipe support design, flange analysis, and equipment nozzle load analysis under dynamic and static load conditions. Autopipe incorporates piping codes such as ASME, British standard, European, NEMA, ASCE, API, and WRC guidelines that are useful in providing a comprehensive analysis of a piping system in addition to 30 piping codes. Autopipe has three editions namely Standard, Nuclear and Advanced. The advanced version provides advanced analysis which is not available in the standard version of Autopipe. Whereas on the other hand, the nuclear version includes all the advanced features, JSME PPC thermal and nuclear transient analysis, and nuclear ASME in classes 1, 2, and 3. Autopipe is well-established software commercially available since 1986. The owner of Autopipe software is Bentley.
What is Caesar II?
Caesar II introduced in 1984 by Intergraph Corporation is the most widely used software for pipe stress analysis. Caesar II allows accurate and quick analysis of piping systems that are subjected to thermal, weight, pressure, seismic, and wind. Caesar II can be used to analyze piping systems of any complexity or any pipe size. It is licensed by almost all the engineering firms of the world. Currently, the software is owned by Hexagon.
AutoPipe vs Caesar II
To find out the differences between AUTOPIPE and CAESAR II we will consider a sample model and study the features of both software. The model shown in Fig. 1 is a pump system where Pump A is Point 1 or Pump B is Point 90 and both Pump A and B are in the operation. Here point 170 is connected to a vessel that is oriented in the Z-axis and at the same point we have entered a flexible anchor defined by CAESAR under the option that shows WRC297 and by AUTOPIPE we have under the option that shows user flexibility.
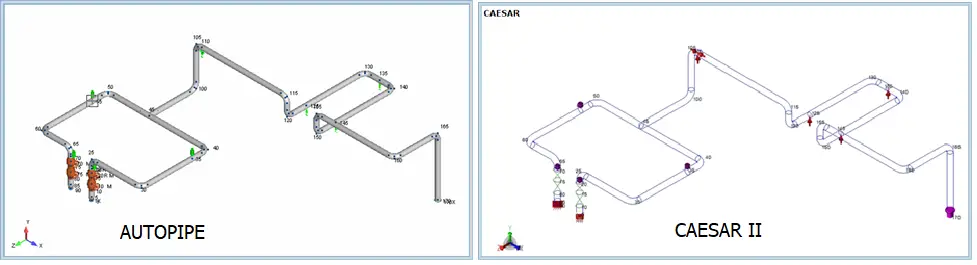
Preparing Load Cases
Both CAESAR and AUTOPIPE perform the same task by providing the user with the stress analysis results based on the load cases that are applied to a geometric model of a particular piping system. However, there is little fundamental difference between both applications on how to load combinations are combined.
One of the fundamental differences between CAESAR and AutoPIPE is the load sequence versus load vector superposition.
Consider the following example:
- L1 W+P1+T1 (OPE) is equivalent to AutoPIPE load case as GRT1P1
- L2 W+P1 (SUS) is equivalent to AutoPIPE load case as GR+Max P
- L3 L1-L2 (EXP) is equivalent to the AutoPIPE T1 case
AutoPIPE load sequence approach does not require intermediate equations like L3 that is found in CAESAR II. This reduces the complexity of load combinations and the length of the output report. Also, AutoPIPE has more advanced non-linear analysis with load sequencing (without iteration problem) and therefore the users can expect more accurate non-linear results than other programs.
In Caesar II, there is an additional Hanger load Case variable H for using Spring hangers but Autopipe automatically takes care of the same in the calculation.
Changing Global Parameters
Global changes to various parameters like pressures, temperatures, materials, etc can be done in both applications. But there are a few differences between both of them as shown below:
In Caesar II, there is no multiple copy/paste and column sort option. One can modify one cell at a time.
Autopipe is bi-directionally synchronized with the plot, It can make global changes across multiple cells of like data. It can sort any column into logical data groups. Autopipe selects multiple ranges of components with graphical highlights. It has real-time graphical plot updates with multi-level undo and redo. It has customized printing. It behaves like Microsoft Excel, unlike Caesar Like spreadsheet.

Changing Support Friction
In Caesar, we have to change friction values one by one or can be replaced by find and replace values similar to excel.
In Autopipe, in the support grid, one can double-click click column heading in order to save the data. One can select multiple cells to make changes or can select one complete column and then select one cell by holding the CTRL key. Then we can enter a new value in the first cell and press CTRL+Enter
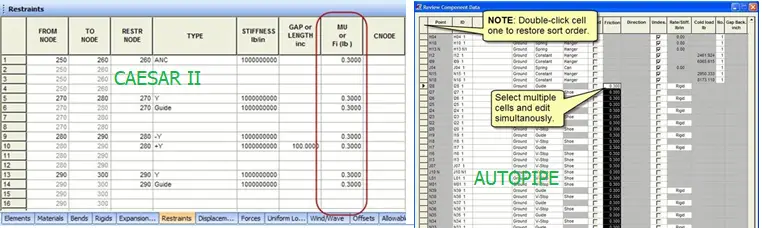
Changing Process Parameters in the Model
Caesar II uses a list spreadsheet as shown in Fig. 4
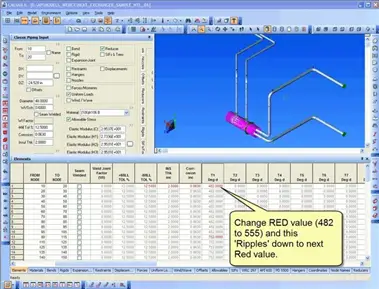
Autopipe makes global changes to parameters like pressure and temperature.
Other Differences between Autopipe & Caesar II
Other differences between Caesar II and Autopipe are tabulated below:
AutoPIPE | Caesar II |
AutoPIPE uses an Alpha-numeric node numbering system. | Caesar II uses only a numeric node numbering system. |
In Autopipe, up to 99 levels of Undo and Redo option is available. | In Caesar II, undo and redo option is lost once the input module is exited. |
AutoPipe allows users to input up to 100 sets of pressure and temperatures. So for complex systems, one can prepare as many load cases as he wants in a single file. | Caesar II allows only 9 sets of temperature and pressure inputs. So for complex systems where many temperature cases are required one needs to prepare two or more caesar files to simulate all operating load cases. |
In Autopipe, within a single interface, all editions of codes are available and one can easily access any code edition with ease. | For Caesar II, the user has to purchase different software versions to work on different code editions. |
Autopipe allows users to open more than one Autopipe window with the same license on the same PC. | Caesar II allows only one Caesar II working window. |
Autopipe does not allow users to modify friction stiffness value to alter the results. | In Caesar II, modification of friction stiffness value is possible in the configuration setting. |
AutoPIPE considers rigid bodies to be 100 times stiffer than the connecting pipe material. | CAESAR II multiplies the pipe wall thickness by 10 to make it rigid, keeping the pipe inside diameter, and the weight of the element unchanged. |
Informative one.thanks for sharing
can you share a detailed load cases difference between Caesar and auto pipe.
like gravity case of autopipe is equal to SUS case of caesar sort of
Hi, Interesting Good. Correct me if I am wrong, in conclusion that AutoPipe is more user-friendly and result-oriented.
Does autopipe have ISO 14692 code support?
Do you have a comparative START-PROF vs. AutoPIPE?
Thank you for sharing such a detailed information.