The hardness of a material is its ability to resist localized permanent deformation, penetration, scratching, or indentation. So, it is an important parameter in engineering. Hardness testing provides a means to quantify the hardness of a material, and it is a key element in many quality control procedures and R&D work. Several methods are available for hardness testing. However, Brinell, Rockwell, Vickers, Knoop, Mohs, Scleroscope, and the Files test are the most widely used hardness tests. In this article, we will learn about the Brinell Hardness Test, its procedure, related formulas, applications, advantages, and standards.
1. What is the Brinell Hardness Test?
The Brinell Hardness Test method is the most commonly used hardness measurement technique in the industry. In the Brinell Hardness Testing, the hardness of a metal is determined by measuring the permanent indentation size produced by an indenter. Harder materials will generate shallow indentations while softer materials will produce deeper indentations. This test method was first proposed by Swedish engineer Johan August Brinell in 1900 and according to his name, the test is popular as the Brinell Hardness Test. This test is also popular as the Hb hardness test or the BHN hardness test.
ASTM E10 defines the Brinell hardness test as an indentation hardness test performed in a verified machine by forcing a tungsten carbide indenter into the test material surface.
2. Brinell Hardness Test Procedure
The Brinell Hardness Test is performed in a Brinell Hardness Test Unit. In this test method, a predetermined force (F) is applied to a tungsten carbide ball of fixed diameter (D), held for a predetermined time period, and then removed. The spherical indenter creates an impression (permanent deformation) on the test metal piece. This indentation is measured across two or more diameters and then averaged to get the indentation diameter (d). Using this indentation size (d), the Brinell Hardness Number (BHN) is found using a chart or calculated using the Brinell hardness test formula.
The equipment used for Brinell Hardness Testing is:
- Brinell Hardness Testing Machine
- Indenter Sphere, and
- Brinell microscope to measure the generated impression.
2.1 Brinell Hardness Testing Machine:
The Brinell Hardness Testing Machine (Fig. 1) consists of a loading system that includes leavers, weights, a hydraulic dashpot, and a plunger enclosed in the body of the machine. The test material is kept on the adjustable anvil. Using the lever, the spherical ball indenter descends on the material with a predecided force that can be read on the screen. The machine typically has a hydraulic system that ensures the load is applied uniformly and can be held for a specific dwell time.
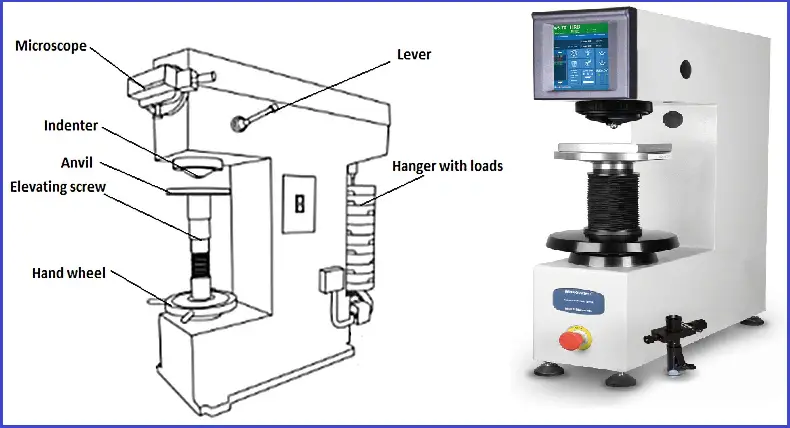
For softer metals, the force used is less than for harder metals. The force value varies from 1 kgf to 3000 kgf. Common test forces range from 500 kgf often used for non-ferrous materials to 3000 kgf for steels and cast irons.
2.2 Indenter Sphere
The indenter used in the Brinell hardness test is usually a hardened steel or carbide ball. There are four sizes of the indenter used for the Brinell hardness test. They are 1 mm, 2.5 mm, 5 mm, and 10 mm in size. The choice of diameter depends on the hardness of the material being tested.
To obtain the same BHN with different ball diameters, geometrically similar indentations must be produced. It is possible if F/D2 is maintained constant.
2.3 Measurement Tools
After the indenter is removed, the diameter of the indentation is measured using optical equipment, such as a microscope or a camera system.
3. Steps for The Test
3.1 Sample Preparation
To ensure accurate results, the test surface must be flat, smooth, and free from contaminants. Surface preparation may involve grinding or polishing the material.
3.2 Conducting the Test
- Positioning the Sample: Secure the material sample in the testing machine.
- Selecting the Indenter: Choose the appropriate ball diameter based on the material hardness.
- Applying the Load: Gradually apply the specified load using the machine. The load should be maintained for a predetermined dwell time, usually between 10 to 15 seconds.
- Removing the Load: After the dwell time, the load is removed carefully.
- Measuring the Indentation: Use the appropriate measurement tool to accurately determine the diameter of the indentation.
3.3 Calculation of BHN
Using the measured values of F, D, and d, apply the BHN formula as per Fig. 2 to calculate the Brinell Hardness Number.
4. Brinell Hardness Test Formula
Once the average indentation diameter is measured the Brinell Hardness Number (BHN or HBW) can be calculated using the following Brinell hardness test formula:
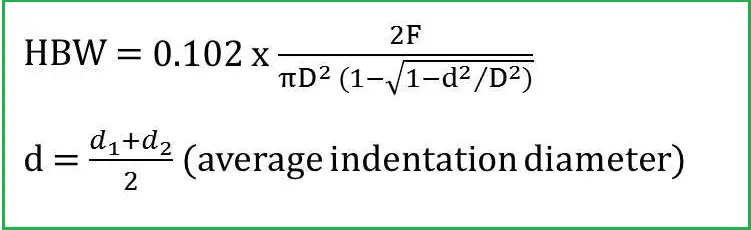
Here,
- F=Applied force, in kgf
- D=diameter of indenter, in mm
- d=diameter of indentation, in mm
Note that, the term HBW stands for Hardness Brinell Wolfram carbide.
Wolfram carbide (= tungsten carbide) underlines the use of tungsten carbide balls, as opposed to the (softer) steel balls previously used (HBS).
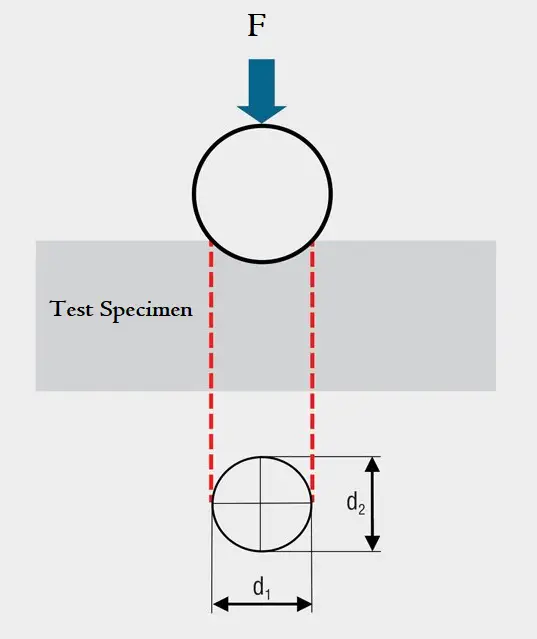
The minimum Test Specimen thickness is at least 10 times the indentation depth as per ASTM standard and the same is at least 8 times the indentation depth as per ISO standard.
5. Unit of Brinell Hardness
The BHN or HB values are mostly reported using only the number. So, it seems there is no unit for the Brinell Hardness Number. But that is not true. The unit of Brinell hardness is kgf/mm2. The same is quite clear from the above-mentioned HBW formula. The force term (F) in the numerator has a unit of kgf and the diameter term (D) has a unit of mm. In the SI unit system, the unit of hardness is N/m2
6. Specifying Brinell Hardness Number
While specifying a Brinell hardness number (BHN or HB), the test conditions used to obtain the number must be specified. The standard format for specifying is “HBW 10/3000”. “HBW” refers to a tungsten carbide ball used as an indenter, as opposed to “HBS”, which means a hardened steel ball. The “10” is the ball’s diameter in millimeters. The “3000” is the force in kilograms force.
Sometimes, the Brinell hardness is also specified as “XXX HB YYD2” where
- XXX is the force to apply (in kgf)
- YY specifies the material type (5 for aluminum alloys, 10 for copper alloys, 30 for steels).
Thus the Brinell hardness of a typical steel could be written: 250 HB 30D2. The following image from Wikipedia provides some typical Brinell Hardness Values of common materials.
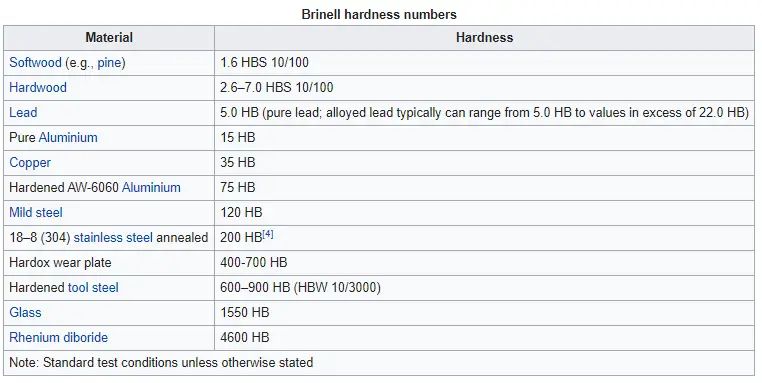
7. Requirements for Brinell Hardness Testing
- Before the test, the sample must be cleaned thoroughly. Preferable if the test surface is machined, ground, and polished to get better indentation measurement.
- Proper indenter (Steel ball or carbide Ball) as per requirement needs to be selected.
- The applicable force needs to be determined beforehand.
- The load on the specimen is to be maintained for the exact period of time.
- The indents must be positioned to keep sufficient clearance from the specimen edge and between the individual indents.
8. Standards for the Brinell Hardness Test
The widely used standards for the Brinell Hardness Test in industries are:
- ASTM E10: ASTM E10 specifies the test method for the Brinell hardness of materials, ensuring consistency and reliability in testing across various industries.
- ISO 6506: The Brinell hardness test is standardized under ISO 6506. This standard outlines the testing procedures, equipment specifications, and calculation methods.
- JIS Z 2243
9. Factors Influencing the Brinell Hardness Test Results
The measured value of BHN can be influenced by the following factors:
9.1 Material Properties
The microstructure and hardness of the material can significantly affect the indentation size. Softer materials will have larger indentations, while harder materials will show smaller indentations.
9.2 Load Selection
The load must be appropriately selected based on the hardness of the material. Too high a load can cause excessive deformation, while too low a load may not produce a measurable indentation.
9.3 Indenter Size
The diameter of the indenter influences the test results. A larger indenter can provide a more representative measurement for materials with a heterogeneous structure.
9.4 Dwell Time
The duration for which the load is applied (dwell time) can affect the indentation size, especially in materials that undergo time-dependent deformation (creep).
10. Advantages and Disadvantages of the Brinell Hardness Test
The Brinell Test method has many advantages:
- The hardness of rough samples can be measured which is difficult with other methods.
- Application of high test load (up to 3,000 Kg) is possible.
- Wide measuring range due to availability of a range of indenter sizes and loads
- A Brinell hardness tester can determine the hardness of all types of metals.
- Provides reliable results.
- The formula for calculating BHN is straightforward, making the test accessible for various industrial applications.
However, the Brinell test method has some disadvantages as well:
- There could be measuring errors due to the use of optical instruments.
- Surface imperfections can interfere with the test result if the surface is not prepared thoroughly.
- The requirement of a flat surface makes this test redundant for cylindrical surfaces.
- For materials above 650 HBW 10/3000, the Brinell hardness test is not recommended.
- The process can be relatively slow compared to other hardness testing methods, especially in high-throughput environments.
11. Brinell vs Rockwell Hardness Test | Difference between Rockwell and Brinell Hardness Test
The main difference between the Brinell and Rockwell Hardness Test is provided in the table below:
Brinell Hardness Test | Rockwell Hardness Test |
In Brinell Hardness Test the indenter is a spherical Tungsten Carbide Ball | For the Rockwell Hardness Test, the Indenter is a Small Steel Ball (HRB) or a diamond cone (HRC) |
Hardness greater than 650 HB can not be measured with the Brinell Scale setup. | There is no such limitation in Rockwell hardness testing. |
Large Indentation | Small Indentation |
The Brinell hardness test measures the diameter of the indentation to calculate the hardness value. | Depth of indentation is measured for calculating Rockwell hardness. |
High Load | Lower Load |
The Brinell hardness testing method is a comparatively slow method. So, the method is time-consuming. | Rockwell hardness testing is a Quicker process. Hence, it is an efficient method. |
Surface preparation is required for Brinell hardness testing. | No surface preparation is required for Rockwell hardness testing. |
Generally used for thicker materials. | Suitable for thin and thick materials. |
Versatile, suitable for a wide range. | Best for softer metals and alloys. |
The main governing standard for Brinell Hardness Testing is ASTM E10. | The main governing standard for Rockwell Hardness Testing is ASTM E18. |
12. Brinell, Rockwell, and Vickers Hardness Conversion Table
The approximate conversion of Brinell, Rockwell B & C, and Vickers hardness is provided below for sample only. One more column indicating approximate equivalent tensile strength is also added.
Brinell Hardness (HB)-3000Kg-10 mm Ball | Rockwell Hardness (HRC)-150Kg Brale | Rockwell (HRB)- 100Kg 1/16″ Ball | Vickers Hardness (HV)- Diamond Pyramid 120 Kg | Approx. Tensile strength (N/mm²) |
800 | 72 | |||
780 | 71 | |||
760 | 70 | |||
752 | 69 | |||
745 | 68 | |||
746 | 67 | |||
735 | 66 | |||
711 | 65 | |||
695 | 64 | |||
681 | 63 | |||
658 | 62 | |||
642 | 61 | |||
627 | 60 | |||
613 | 59 | |||
601 | 58 | 746 | ||
592 | 57 | 727 | ||
572 | 56 | 694 | ||
552 | 55 | 649 | ||
534 | 54 | 120 | 589 | |
513 | 53 | 119 | 567 | |
504 | 52 | 118 | 549 | |
486 | 51 | 118 | 531 | |
469 | 50 | 117 | 505 | |
468 | 49 | 117 | 497 | |
456 | 48 | 116 | 490 | 1569 |
445 | 47 | 115 | 474 | 1520 |
430 | 46 | 115 | 458 | 1471 |
419 | 45 | 114 | 448 | 1447 |
415 | 44 | 114 | 438 | 1422 |
402 | 43 | 114 | 424 | 1390 |
388 | 42 | 113 | 406 | 1363 |
375 | 41 | 112 | 393 | 1314 |
373 | 40 | 111 | 388 | 1265 |
360 | 39 | 111 | 376 | 1236 |
348 | 38 | 110 | 361 | 1187 |
341 | 37 | 109 | 351 | 1157 |
331 | 36 | 109 | 342 | 1118 |
322 | 35 | 108 | 332 | 1089 |
314 | 34 | 108 | 320 | 1049 |
308 | 33 | 107 | 311 | 1035 |
300 | 32 | 107 | 303 | 1020 |
290 | 31 | 106 | 292 | 990 |
277 | 30 | 105 | 285 | 971 |
271 | 29 | 104 | 277 | 941 |
264 | 28 | 103 | 271 | 892 |
262 | 27 | 103 | 262 | 880 |
255 | 26 | 102 | 258 | 870 |
250 | 25 | 101 | 255 | 853 |
245 | 24 | 100 | 252 | 838 |
240 | 23 | 100 | 247 | 824 |
233 | 22 | 99 | 241 | 794 |
229 | 21 | 98 | 235 | 775 |
223 | 20 | 97 | 227 | 755 |
216 | 19 | 96 | 222 | 716 |
212 | 18 | 95 | 218 | 706 |
208 | 17 | 95 | 210 | 696 |
203 | 16 | 94 | 201 | 680 |
199 | 15 | 93 | 199 | 667 |
191 | 14 | 92 | 197 | 657 |
190 | 13 | 92 | 186 | 648 |
186 | 12 | 91 | 184 | 637 |
183 | 11 | 90 | 183 | 617 |
180 | 10 | 89 | 180 | 608 |
175 | 9 | 88 | 178 | 685 |
170 | 7 | 87 | 175 | 559 |
167 | 6 | 86 | 172 | 555 |
166 | 5 | 86 | 168 | 549 |
163 | 4 | 85 | 162 | 539 |
160 | 3 | 84 | 160 | 535 |
156 | 2 | 83 | 158 | 530 |
154 | 1 | 82 | 152 | 515 |
149 | 81 | 149 | 500 | |
147 | 80 | 147 | 490 | |
143 | 79 | 146 | 482 | |
141 | 78 | 144 | 481 | |
139 | 77 | 142 | 480 | |
137 | 76 | 140 | 475 | |
135 | 75 | 137 | 467 | |
131 | 74 | 134 | 461 | |
127 | 72 | 129 | 451 | |
121 | 70 | 127 | 431 | |
116 | 68 | 124 | 422 | |
114 | 67 | 121 | 412 | |
111 | 66 | 118 | 402 | |
107 | 64 | 115 | 382 | |
105 | 62 | 112 | 378 | |
103 | 61 | 108 | 373 | |
95 | 56 | 104 | ||
90 | 52 | 95 | ||
81 | 41 | 85 | ||
76 | 37 | 80 |
13. Relation between Brinell Hardness (BHN) and Tensile Strength
Note that, There is no concrete method of accurately converting the Brinell hardness numbers on one scale to Brinell hardness numbers on another scale, or to other types of hardness numbers, or to tensile strength values. Such conversions are, at best, approximations and, therefore should be avoided.
In general, with an increase in Brinell Hardness values the tensile strength also increases. There is an approximate formula that can be used to convert BHN to tensile strength (UTS) or vice versa. The relationship between BHN and UTS is based on Meyer’s index (n) from Meyer’s law devised by Eugene Meyer.
The approximate formula for calculating tensile strength for known BHN values for carbon steel material is given as follows:
- Tensile Strength, PSI=515 X BHN (For Brinell numbers <= 175)
- Tensile Strength, PSI=490 X BHN (For Brinell numbers > 175)
Note that, the above approximate formulas are not applicable for nonferrous metals.
14. Table of Brinell Hardness Numbers
The Brinell Hardness Numbers Table can easily be generated by solving the formula given above for different load and diameter conditions. A typical table of Brinell hardness numbers is produced in Fig. 5 below from ASTM E10 Table X1.1.
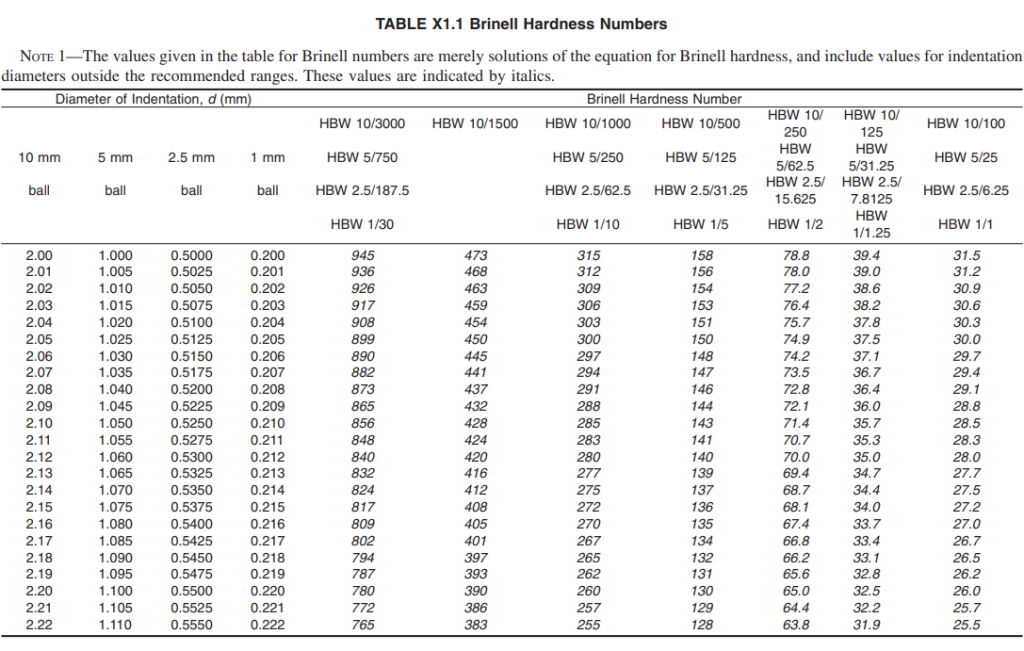
15. Uses of Brinell Hardness Test
Some of the applications of the Brinell hardness test are mentioned below:
- Industrial Applications: Industries such as automotive, aerospace, and construction utilize the Brinell hardness test for product validation and performance assessment.
- Quality control: The Brinell hardness test is commonly used in manufacturing and quality control to ensure that materials meet specific hardness requirements. For example, it can be used to test the hardness of steel components used in automotive, aerospace, or construction applications.
- Material selection: The Brinell hardness test can be used to compare the hardness of different materials and to select the most appropriate material for a specific application. For example, it can be used to compare the hardness of different types of steel or to compare the hardness of steel and aluminum alloys.
- Heat treatment evaluation: The Brinell hardness test can be used to evaluate the effectiveness of heat treatment processes on metals. For example, it can be used to determine whether a specific heat treatment has achieved the desired level of hardness.
- Research and development: The Brinell hardness test is also used in research and development to investigate the properties of new materials and to develop new materials with specific hardness properties.
- Failure analysis: The Brinell hardness test can be used in failure analysis to determine the cause of material failures. For example, it can be used to determine whether a component can fail due to insufficient hardness or to identify areas of a component that have been subjected to excessive stress.
Overall, the Brinell hardness test is a valuable tool for measuring the hardness of materials and is widely used in a variety of applications in industry, research, and development.
16. Frequently Asked Questions
What is the Brinell Hardness Scale?
Brinell hardness scale is a designation to identify the specific combination of ball diameter and applied force used to perform the Brinell hardness test.
What is the Brinell hardness test?
The Brinell hardness test is a method used to measure the hardness of materials, particularly metals and alloys. It involves pressing a hard spherical indenter into the material under a specific load and measuring the diameter of the resulting indentation.
What types of materials can be tested with the Brinell method?
The Brinell test is suitable for a wide range of materials, particularly metals and alloys with coarse or uneven grain structures. It is commonly used for steel, cast iron, and other metals.
How long should the load be applied during the test?
The load should typically be applied for a dwell time of about 10 to 15 seconds, although this can vary based on the material being tested.
Can the Brinell hardness test be performed on small samples?
The Brinell test is generally not recommended for small or thin samples due to the size of the indentation produced. For such cases, alternative methods like Rockwell or Vickers hardness tests may be more appropriate.
What standards govern the Brinell hardness test?
The Brinell hardness test is governed by several standards, including ISO 6506 and ASTM E10, which outline the procedures, equipment specifications, and calculation methods.
Is the Brinell hardness test a destructive test?
Yes, the Brinell hardness test is considered a destructive test because it leaves a permanent indentation on the material being tested.
What industries commonly use the Brinell hardness test?
The Brinell hardness test is widely used in industries such as metallurgy, automotive, aerospace, and construction, primarily for quality control and material selection purposes.