What is PDMS?
PDMS or Plant Design Management System is a highly popular Engineering Design software developed by AVEVA. Its easily customizable user-friendly feature and multi-user supports in the multi-discipline environment make it the number 1 choice for many renowned engineering, design, and construction projects in the onshore and offshore industry. PDMS possesses separate modules for piping, equipment, structure, ducting, and cable trays. The software can be easily customized based on client specifications and catalogs and has a fully colored 3D environment.
What is PDS?
PDS or Plant Design Systems is an intelligent computer-based plant design engineering software package developed by Intergraph (Currently Hexagon). Starting from the year 1980, PDS is believed to be one of the pioneers of the 3D design industry. PDS can be used for projects ranging from small-scale revamp jobs to multibillion-dollar onshore and offshore platforms, refineries, chemical, and petrochemical plants.
PDMS vs PDS; Differences
From the above paragraphs, it is clear that both PDMS and PDS can be used for the design of any project. But most of the time designers ask, Which one is better between PDS and PDMS? According to user experience and technical flexible functionality, PDMS is far better than PDS. The following table will list down major differences between them.
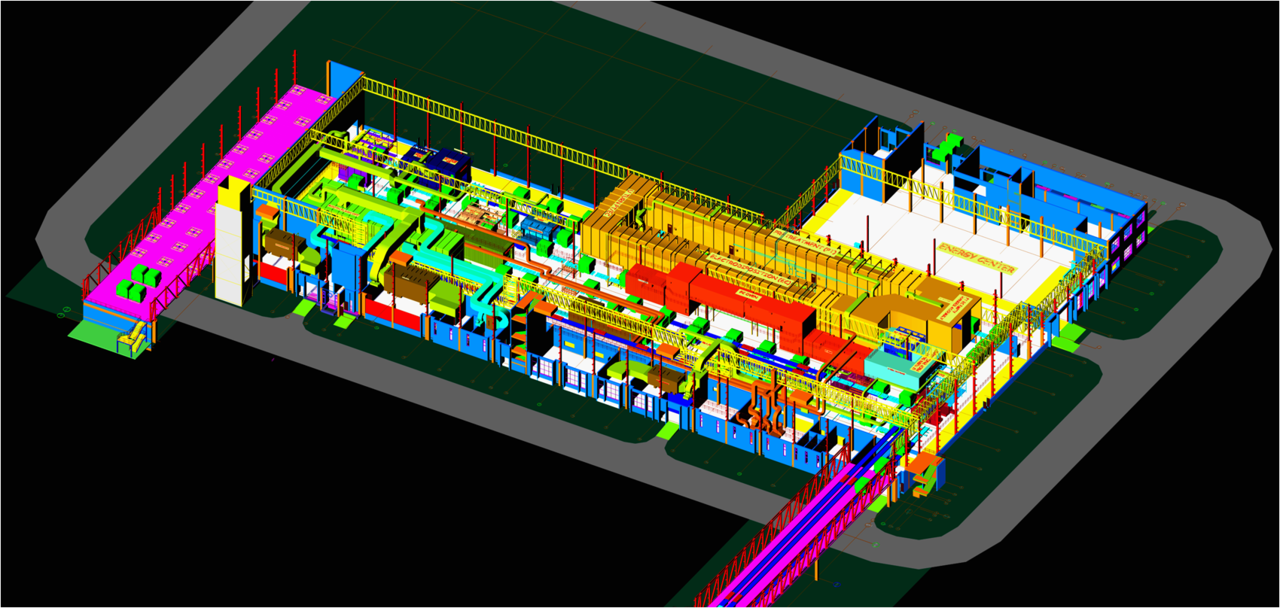
Sr. No | Parameter | PDMS | PDS |
1 | Modeling & Design Environment | PDMS provides working in a shared or wire-line 3D environment. It has a higher level of visualization on the desktop for all engineering disciplines. Fully multidisciplinary 3D model. | Predominantly wire-line in day-to-day work. PDS can design in full-color shade but it is a static image. Image rotation or zooming is not possible. In PDS, HVAC, Raceway, etc. have separate applications. |
2 | Access Control | The access control of specific disciplines or objects in PDMS is easier. | Access control in PDS is much more difficult. |
3 | Data Handling | In PDMS, there is no limit on the job size. The software runs smoothly and at high speed. | PDS forces the designer to split big projects. Dependency of admin works is more with more complexity. |
4 | Database Architecture | PDMS database is open and easily accessible using the toolkits provided. The user simply navigates around a hierarchical project structure of the invisible PDMS database. The major advantage of the multi-disciplinary database of PDMS is that the interference checking between those disciplines will not have errors due to stepped data release. | PDS holds information in model files. The graphical information is stored in .dgn files. Associated with this are the .drv files with some attribute data and the link from the graphical files to the oracle database. Standard SQL links to Oracle are used to write and read information from the database. On multi-disciplined smaller projects, the user can not swap between different disciplines in the same reference file as the application ware (GUI) is different between different disciplines. The only option for the user is to come out and re-enter the system which wastes time. |
5 | Attribute Data | In PDMS the attribute data is stored in the same database as the graphical information and is protected from the user by the applications. | The oracle database is linked with the element via hidden stored user data. Items can be given the same name. Therefore there is no integrity of data. The .drv file which is an ASCII file can be edited in a standard editor outside of the system. |
6 | Revision Management | According to project procedures, PDMS is fully customizable to ensure available data is always fully controlled. Features like Change history, revision status, change highlighting on deliverables, rollback of database to any previous version, etc. are strong points of PDMS | PDS does not provide such features |
7 | Creating projects from previous old projects | User-friendly for extracting and re-using data from old projects. | Need PDS experts to extract and reuse old project data. |
8 | Mass Manipulation of Item | Easy | Very Difficult |
9 | Administration Effort | Less. PDMS allows work breakdown of projects for modification. PDMS has internal data access control as well as external. | High. PDS does not have such work breakdown features. There is no internal data management in PDS. Access permission to files is done at an operating system level. |
10 | 2-D Integration | AutoCAD | Micro-station |
11 | Global Work Capability | Work and data can be easily shared globally across multiple locations | Limited |
12 | Compatibility with Latest Microsoft Technology | Compatible | Not-Compatible |
13 | Automatic Drawing Extraction | Can be configured | Not Possible |
14 | Creation of user-defined command | Possible | Not-Possible |
15 | Project Resource (No of Licence and Man hour ) Cost | 20 to 40% less as compared to PDS | more |
16 | Online Clash Checking | Possible | No Online clash detection facility |
17 | Exact 3D Clash Location | Provide. PDMS maintains a spatial volume map of the design while users are working. All disciplines are available for checking at any time and automatic sketches of a clash can be output. PDMS can also recognize the difference between ‘touches’ and normal clashes. | Does not provide. PDS is not based on solid geometry. It defines envelope files and is a batch-only function because the clash check program draws circles around the clashes and must, therefore, open the Micro-station drawing (model file) with write access. Also, PDS cannot have negative volumes which result in many ghost clashes. |
18 | Insulation modeling | possible | No insulation specification with the thickness table is available. Provided only as a reference to the pipe. |
19 | Modification of job | Easy. PDMS is very flexible and allows to drag and modify piping sections. Some useful options for positioning piping items to the ‘Top Of Steel’ or ‘Bottom Of Pipe’ are available in PDMS. | Difficult. In PDS you can not declare a clearance from another item when positioning a component other than snapping on the graphic representation of an element. |
20 | Online data consistency checking | Complete consistency check with the report is possible | Not possible |
21 | Export to Design Review Tools | Superior | Inferior |
22 | File Size | Database size is less than PDS. Database by PDMS are up to 70% smaller than the PDS database for the same project | Size is more as for each item information is stored individually. |
23 | Bill of Material (BOM) | As the more complete model of the parts, BOM extracted is more accurate | Less Accurate |
24 | Corruption Problem | PDMS being a single integrated database, there is no link to corruption problems | Many PDS customers regularly experience database linkage corruption because of its standard multi-write relational Oracle database. Once information is written, it is impossible to undo or quit the work session. |
25 | Productivity | more | less |
Few more useful resources for you..
PDMS Video Tutorial/Lessons for Beginners
Piping Design Basics- Isometric Drawings
Tutorial on Pipe Modeling using AVEVA E3D software
How to import an AVEVA E3D or PDMS model into START-PROF Piping Stress Analysis Software
Video: AVEVA PDMS and Piping Stress Analysis Software PASS/START-PROF Two-way Integration
About the Author: Part of the article is authored by Mr. Amir Razmi, an International dynamic and multi-functional chemical engineer with more than 14 years of experience in engineering and EPC of oil and energy projects from pre-contract activities to execution, and closeout.
thanks for very informative article , i m wondering how is job market demand for each software especially in USA market. PDMS might be more expensive software so small companies desire to use PDS. what is your opinion?
Is this a time warp back to the year 2000? Pdms has been replaced by e3d sand pds replaced by s3d back in the mid 2000s. There’s still a lot of legacy projects using them but for modern design the later packages are far superior.
Please upload more Tutorial videos for E3D software.
Both PDS and PDMS are antiquated.
Personally a believer in Plant 3D for the following reasons:
– Very flexible
– Can be cloud based
– Integrated P&ID’s making consistancy checks with P&ID as leading
– Easy to configure reporting
– Integration with Inventor / other 3D softwares
– takes an afternnon to create a pipe spec (PDMS / PDS up to 2 weeks)
– multiple users working at the same time with an automatic updated
Admittedly it was too graphic back in the early years, but has only got better and in my view surpasses PDMS and PDS. A complete software package.
Costs also only a fraction of the price of PDMS / PDS, where you pay a small fortune for each module per license.
la différence entre AVEVA E3D et PDS
Anup, information is so nice and understandable in one reading. pls keep sharing.