A Pump or Pumping system is the major equipment in any process or power plant. So the equipment should operate properly to give the best output in terms of performance. However, there are many factors that influence the pump’s performance. Out of those, the main (major) factors which affect the performance of the pump are:
- Impeller design
- Improper priming
- Insufficient NPSH
- Reduced capacity
- Wrong direction of rotation
- Clogging of suction pipeline and impeller
- Improper shaft alignment
- Packing troubles
- Noisy operation
This article will explain these points in short.
Impeller Design
- Backward curved blades, β2<90°
- Forward curved blades, β2>90°
- Radial blades, β2=90°
The following table provides a guideline for pump performance with various blades.
Backward curved blades, β2<90° | Forward curved blades, β2>90° | |
No of blades | 12-16 | 60 |
Blade angle, β2 | 40° | 145° |
Hydraulic efficiency | 80% | 70% |
Power consumption | low | high |
application | Changing operating condition | Fixed duty operation |
losses | low | high |
Improper Priming
All the air in the pipeline should be expelled completely
Precautions to eliminate trouble :
- The pump should be primed completely before starting
- The suction pipe should be 1m below the lowest water level
- It should be completely airtight
- Eccentric reducers should be used if necessary to avoid air pockets in the pipeline
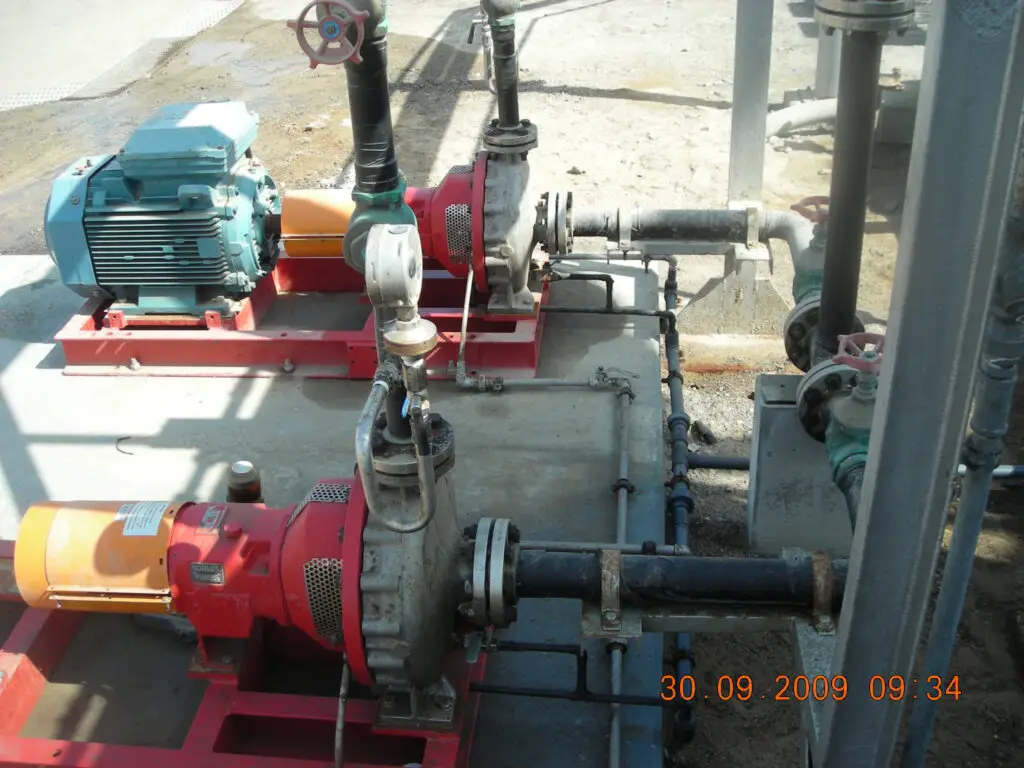
Insufficient NPSH
- NPSH= (Patm-Pv)/ ρg – hs – hfs
- NPSH depends on the temperature of the operating liquid
- Variation in water level is considerable – The lowest level should be taken into account for NPSH determination
- Frictional losses should be kept minimum by selecting a suitable diameter.
- It is commonly accepted the static head in the pump will be maintained at 6.7m for water with a temperature of 10-20°c
- NPSH available > NPSH required
Reduced Capacity
- One of the main reasons for the reduced capacity is increased head
- Total head > designed head
- The pump or the impeller should be changed to obtain the rated capacity
Wrong Direction of Rotation
- This cause the rated capacity and head will not be obtained
- The pump fails often to operate
- Remedy :
- arrow cast is indicated in the pump casing
- care should be taken while mounting the impeller
Clogging of Suction Pipeline
- The suction pipe is clogged by some bricks, wood often
- The strainer is clogged by paper, leaves
- To rectify this pipeline should be inspected periodically
Improper Shaft Alignment
- It is due to the misalignment of the motor and pump shaft
- It results in vibration and noisy operation
- To avoid this two shafts should be aligned properly
Noisy Operation
- Air leakage in the pump
- Shaft misalignment resulting in the vibration
- Cavitations
- They can be reduced by a proper dynamic balance of the shaft and impeller
- The cavitations are reduced by properly designing the pump with suitable NPSH
Few more resources for you..
Pumps & Pumping Systems: A basic presentation
Cause and Effect of Pump Cavitation
NPSH for Pumps: Explanation and Effect
Water Hammer Basics in Pumps for beginners
Can you give me your mobile number. Because if I will have any quary then I will asy to you . I’m Satish Aswar I Chemical Engineer.
Main problem is pump is not matching with piping. Calculate correct head required and select right pipe diameter.
System design is more important. Most of the time pump is recommended by manufacturer and he may select a borderline size to reduce price to get order.
NPSH sometimes overlooked and permanent problems will be created.
It has happened in a petrochemical plant and only way to solve was buy new pump,suction piping etc. ( 1000 M3/hr pump)
Good information, I want to know some time pump loose it’s pressure & not devloped. What’s the reason???
I have certain additions :
1)wrong direction of rotation can damage the pump and its mechanical seal. The impeller or the seal sleeve can come out loose depending on their design. Also there would be extreme vibration.
2) Shaft alignment : improper management of housing temperatures of the pump can result in misalignment. Proper cooling or heating of the pump to be ensured.
1)When Star-Delta connection is installed wrongly, can it Causes the pump to consume low power and having low(Bad) factor?
2) what are the impacts to the pump when its starting method(star-Delta) of the motor is installed wrongly?
I am not a MOTOR guy, but I got some insight about how pumps work and what factors affect out energy consumption. Thanks for the blog article.