High-frequency welding is a special type of welding technique used to join thermoplastic materials together. This is also popular by names Radio Frequency Welding, RF Welding, or HF Welding Process. Industries like packaging, automotive, textiles, medical equipment manufacturing, etc widely use high-frequency welding processes. The process utilizes high-frequency electromagnetic waves to create heat and pressure, which enables the fusion of the materials for joining.
This welding methodology has been in use since the 1930s. Recently HF welding has become increasingly popular because of its ability to create quick and effective bonded components with precision. In this article, we will learn the steps, applications, advantages, and working of high-frequency welding.
Steps for High-Frequency Welding Process
In general, the following steps are used for the high-frequency welding process.
- Preparation: The materials to be welded are prepared by cleaning and aligning the edges that need to be joined. This ensures proper fusion and a strong bond.
- Clamping: The prepared materials are held together firmly using clamps or a pneumatic system. This helps in maintaining alignment during the welding process.
- Application of high-frequency energy: An electrode, typically made of copper, is placed on one side of the joint, while a grounding plate is placed on the other side. High-frequency electric current is then passed through the electrode, creating an oscillating electromagnetic field.
- Heating and Melting: The high-frequency electromagnetic field induces molecular movement and generates heat within thermoplastic materials. This heat causes the material to soften and melt along the joint line.
- Pressure and Fusion: Once the material reaches the desired melting point, pressure is applied to the joint using the clamping mechanism. The combination of heat and pressure ensures intimate contact between the melted surfaces, promoting fusion. The material cools and solidifies, forming a strong bond.
- Cooling and Finishing: After the welding process is completed, the joint is allowed to cool down, stabilizing the newly fused area. Depending on the application, additional steps such as trimming or finishing may be performed to achieve the desired final product.
Working of High-Frequency Welding Process
In HF Welding, a high-frequency generator is used to produce electrical energy. An electrode supplies this energy to the material. The energy helps the molecules of the material to start moving, which in turn generates heat. Eventually, the material softens by the heat and thereby fuses together and is joined by applying pressure. No outside heat is required for the welding process. Once the joining surface cools under maintained pressure, they create a strong weld. Refer to the image (Fig. 1) below that explains the working of the high-frequency welding process.
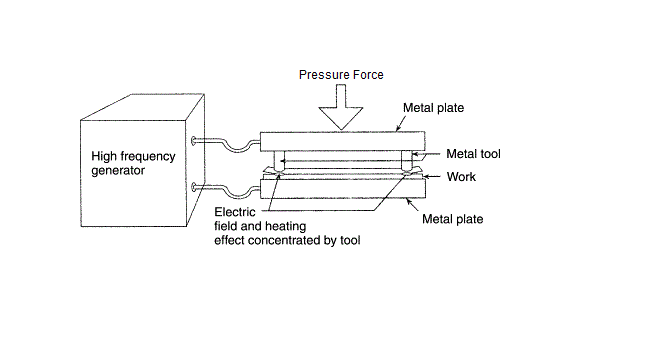
Advantages of High-Frequency Welding
High-frequency welding offers several advantages such as:
- Fast cycle times,
- Inexpensive tooling,
- Efficient energy utilization,
- Clean environment-friendly process,
- Reliable technology,
- Repeatable multi-layer welding,
- Strong, durable, and consistent welds.
It is commonly used for manufacturing items such as inflatable products, PVC and PU fabrics, tents, banners, conveyor belts, automotive interior components, and medical bags, among others.
Factors Affecting High-Frequency Welding
The high-frequency welding process is dependent on the following parameters:
- Electrical power
- Application of Pressure
- Welding time
- Time for cooling
Depending on the specific need, optimal parameters are decided.
Applications of High-Frequency Welding
High-frequency welding finds applications in various industries due to its ability to create strong and reliable bonds between thermoplastic materials. Some of the common applications of high-frequency welding include:
Packaging Industry:
High-frequency welding is widely used in the packaging industry for manufacturing products such as blister packs, clamshell packaging, clear plastic boxes, and various types of bags and pouches. It provides airtight and secure seals, ensuring product integrity and protection. The food industry also uses HF welding as the airtight seal help in preserving food products.
Automotive Industry:
High-frequency welding is employed in the automotive sector for producing various components, including door panels, instrument panels, seat covers, sun visors, and airbags. It allows for precise and durable joining of different materials, such as PVC, leather, and fabrics. The strong and durable bond that high-frequency welding creates, is a requirement for many automobile components.
Textile Industry:
High-frequency welding is utilized in the textile industry for creating waterproof and airtight seams in fabrics. It is commonly used in the production of outdoor equipment like tents, awnings, tarpaulins, inflatable structures, and protective clothing.
Medical Industry:
High-frequency welding plays a crucial role in the production of medical equipment and supplies. It is used to manufacture items such as blood and IV bags, urine bags, medical mattress covers, surgical gowns, and various other medical devices. The welding process ensures sterility and leak-proof seals.
Stationery and Leather Goods:
High-frequency welding is applied in the production of stationery items like folders, binders, and wallets. It enables the creation of precise and durable seams in leather, PVC, or synthetic materials.
Air and Liquid-Tight Containers:
High-frequency welding is commonly used to manufacture containers, tubes, and tanks that require airtight or liquid-tight seals. These containers can be used for storing liquids, chemicals, or gases.
Advertising and Signage:
High-frequency welding is employed in the production of large-scale banners, billboards, and signage. It enables the creation of strong and weather-resistant seams, ensuring durability and longevity.
Electronics Industry:
High-frequency welding is used for manufacturing electronic components and devices. It facilitates the joining of plastic parts, connectors, and housings, ensuring secure and precise assembly.
These are just some of the examples of the wide range of applications for high-frequency welding. Its versatility, speed, and ability to create strong bonds make it a valuable technique in industries that work with thermoplastic materials.
High-Frequency Welding Machine
High-frequency welding machines have revolutionized the joining of thermoplastic materials, offering industries a powerful and efficient method for creating strong and reliable bonds. This advanced technology has found applications in diverse sectors such as packaging, automotive, textiles, and medical equipment manufacturing. In this article, we will explore the workings of a high-frequency welding machine, its key components, and the benefits it offers to various industries.
Understanding High-Frequency Welding Machines:
High-frequency welding machines, also known as radio frequency (RF) welding machines, utilize electromagnetic waves to generate heat, enabling the fusion of thermoplastic materials. These machines operate at frequencies typically ranging from 27 to 40 MHz, producing an oscillating electromagnetic field that induces molecular movement within the materials, resulting in localized heating and subsequent fusion.
Key Components:
A high-frequency welding machine consists of several essential components:
Generator:
The generator is the heart of the machine, responsible for producing high-frequency electric energy. It converts the input power into a high-frequency output, typically in the radio frequency range.
Electrode System:
The electrode system includes an electrode and a grounding plate. The electrode, usually made of copper, is placed on one side of the joint, while the grounding plate is positioned on the other side. These components allow for the passage of high-frequency electric current and the creation of an oscillating electromagnetic field.
Clamping Mechanism:
The clamping mechanism ensures that the materials to be welded are held firmly together during the welding process. It maintains proper alignment and facilitates the application of pressure for fusion.
Cooling System:
As high-frequency welding generates heat, a cooling system is employed to prevent overheating of the machine. This system may include water or air cooling mechanisms to maintain optimal operating temperatures.
Dea Sir,
I have High frequency plastic welding machine for inflatable toys production purposes.
But Problem is sealing dies mold sparking too much. if possible kindly help me.