Piping Thermal Insulation is very important for saving energy costs and maintaining the process fluid temperature at the required level. In case, thermal Insulation is appropriately chosen and used so that it is Non-complaining, Maintenance-free, and Patient workhouse, It looks after the economy with tremendous savings in energy costs, the safety of personnel, and smoother process control.
On the other hand, insufficient or poor piping insulation or deterioration of existing thermal insulation can be a cause of huge energy loss. So most of the time, thermal Insulation is defined as, “A major tool in improving energy availability”. The thermal insulation material is also important to achieve low thermal conductivity and low thermal inertia.
The basic objective of thermal insulation is to retard the flow of heat:
- From a hot surface to a cold environment or
- From a warm environment to a cold surface
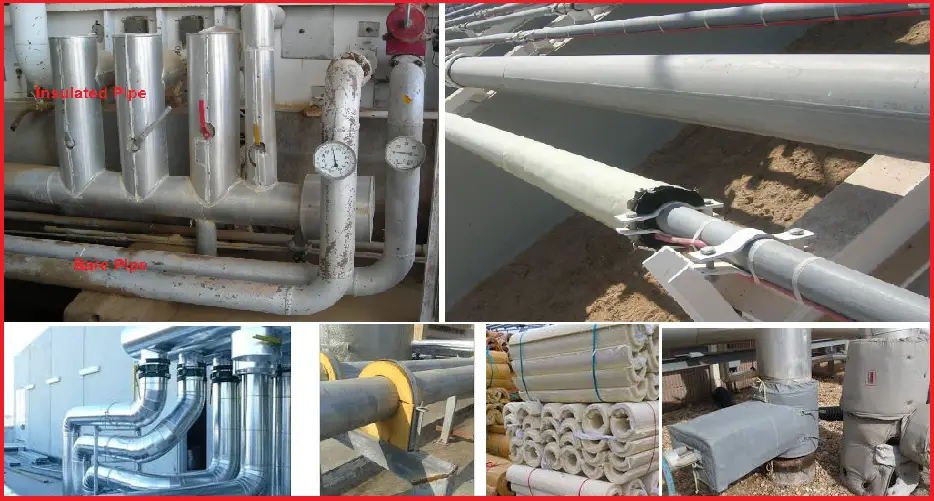
Energy Loss from Hot Surface Without Thermal Insulation
Fig. 1A and Fig. 1B below show a typical example of heat losses from the piping surface if the pipe is not insulated.
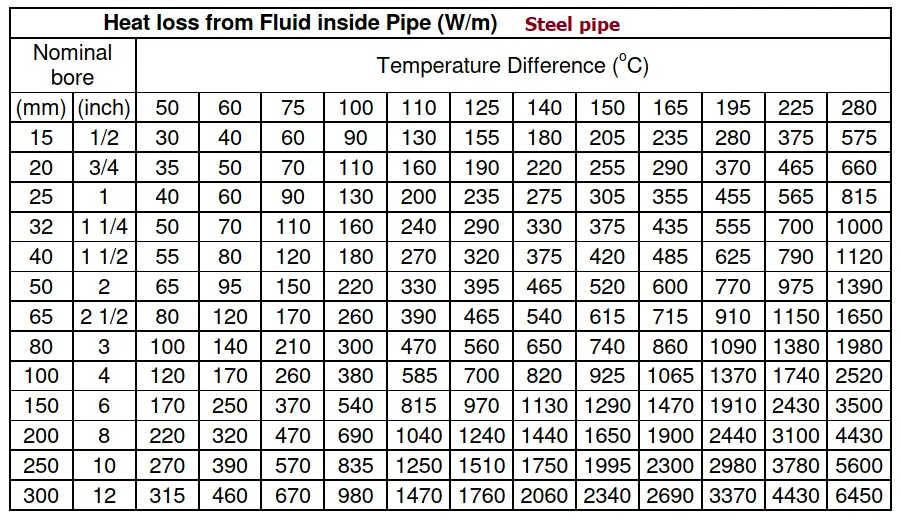
The heat loss values are normally corrected by the correction factor for certain applications.
Economic Reasons for Thermal Insulation:
Piping thermal insulation
- Reduces fuel consumption, and hence overall operational cost so day-to-day economic benefits.
- Reduces capacity requirements for heating/cooling systems (boiler, refrigeration unit, etc)
- Savings in Capital costs
Even though the basic requirement for providing thermal insulation is Economic, still it is not the sole criterion. The process requirement controls the usage of thermal insulation.
Process Reasons for using thermal Insulation:
- Reduces the temperature drop of fluid in a heated system
- Reduces temperature gain of fluid in the refrigerated system.
- Reduces boil-off rate in a volatile liquid storage system
- Assist in maintaining thermal balance in the reaction system
- In the heated system, it lowers temp. of exposed surfaces-protects workmen from burn hazard
- Provides fire protection for plant, equipment & piping
- Reduces capacity requirements for heating/cooling systems (boiler, refrigeration unit, etc)
Economic Thickness for Thermal Insulation
The thermal insulation thickness for which the total cost (insulation material cost + energy cost) is minimum is termed as economic thickness. Refer to Fig. 2 below which shows the total cost for a typical plant. Similar curves are plotted to find out the economic thermal insulation thickness.
By virtue, Insulation shall resist heat transfer by:
- Radiation
- Convection
- Conduction
Types of Thermal Insulation
- Mass-type insulation: Based on interposing a mass of material with a built-in capacity to retard heat flow
- Reflective Insulation: Based on providing a series of the reflective surface with the intervening space s evacuated
- Microporous Insulation: Based on a combination of Mass & Reflective technologies.
Physical Properties of Thermal Insulation Materials
Significant physical parameters of thermal insulating materials can be divided into:
- Thermal Properties
- Chemical Properties
- Commercial Factors
Thermal Properties:
The basic thermal parameters that thermal insulation materials should possess are:
- Temperature resistance
- Thermal conductivity
- Thermal diffusivity, and
- Thermal shock resistance
Chemical Properties of Insulating Material:
Major Chemical properties of insulating materials are:
- Compatibility with the metal surface
- Compatibility with environmental media
- Deterioration arising out of the chemical action
- Life of insulation material
Points to remember while selecting thermal insulating materials:
- Alkalinity (pH) or acidity
- Chemical Reactivity/passivity
- Coefficient of Expansion / Contraction
- Compressive Strength & Breaking Load
- Abrasion Resistance
- Combustibility
- Most importantly, THERMAL CONDUCTIVITY
Thermal Conductivity Vs Density:
The thermal conductivity of a material provides the heat loss per unit area per unit insulation thickness per unit temperature difference. The unit of measurement is W-m2/m°C or W-m/°C. With an increase in temperature, the thermal conductivity of materials increases. That is why the thermal conductivity for thermal insulation materials is always specified at the mean temperature (mean of hot and cold face temperatures). Fig. 3A provides a curve showing the relation between thermal conductivity and density of the thermal insulation material.
Refer to Fig. 3B below which provides some typical thermal conductivity values for hot and cold insulation materials.
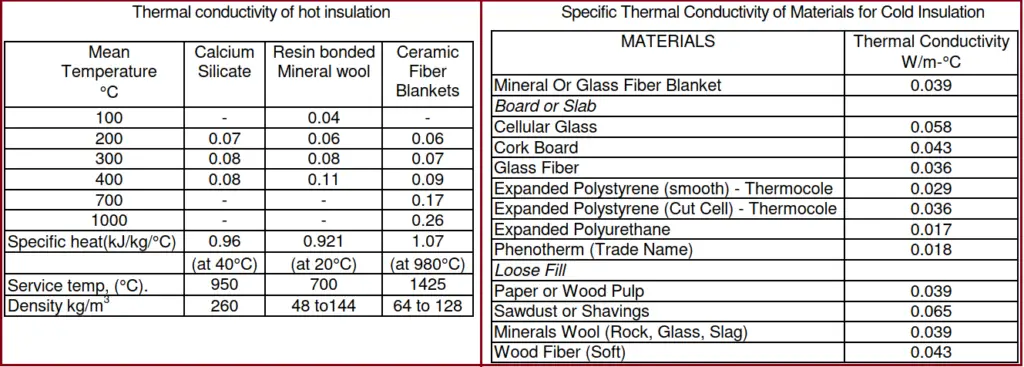
Widely used Hot Insulating Material:
- Mineral Wool
- Ceramic Fibre
- Calcium Silicate
Widely used Cold Insulating Materials:
- Expanded Polystyrene Foam (EPS)
- Extruded Polystyrene Foam (XPS)
- Polyurethane Foam (PUF)
- Poly-isocyanurate Foam (PIR)
- Foam glass
- Phenolic Foam
- Thermocol
Among the above-listed materials, Polyurethane and Polyisocyanurate have assumed the highest importance because these possess many superiorities as compared to others. Both of these materials can be used as Pre-formed shapes or installed in-situ-by Pouring or by spraying.
Insulation Finishes:
The outer part of insulation is normally provided with:
- Weather barriers-claddings
- Weather and Vapor retarder, Indoor coverings, and finishes
All of these have only one basic function which is to protect the insulation material from severe external exposure media.
Thermal Insulating System Design
The insulation system should perform to the expected level, undiminished over its life.
- This needs full data on material behavior under all conditions of exposure.
- In particular, we need to know what would make a material lose its properties.
Thermal calculations need a representative value of Thermal Conductivity for the design
- Standard materials like Rockwool and Calcium Silicate have well-established Design ‘k’ values.
- Limiting Service Temperature of use
- In pipe applications, weight becomes critical. Abrasion is also a major problem with some materials.
Calculation of Thermal Insulation Thickness
The most basic piping model with thermal insulation is shown in Fig. 4. where r1 denotes the pipe outside radius and r2 shows the radius of the Pipe including insulation.
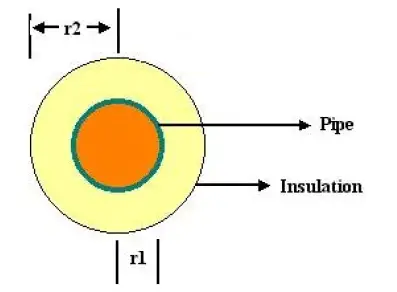
In the calculation of thermal insulation, the first step is to calculate the heat loss from the pipe.
Heat loss from a surface is expressed as H = h X A x (Th-Ta) Where
- h = Heat transfer coefficient, W/m2-K
- H = Heat loss, Watts
- Ta = Average ambient temperature, K
- Ts = Desired/actual insulation surface temperature, ºC
- Th = Hot surface temperature (for hot fluid piping), ºC & Cold surface temperature for cold fluids piping)
For horizontal pipes, the heat transfer coefficient can be calculated by:
h = (A + 0.005 (Th – Ta)) x 10 W/m2-K
For vertical pipes,
h = (B + 0.009 ( Th – Ta)) x 10 W/m2-K
Here A, and B are coefficients that can be obtained from the table in Fig. 5

Tm = ( Th + Ts)/2
- k = Thermal conductivity of insulation at a mean temperature of Tm, W/m-oC
- tk = Thickness of insulation, mm
- r1 = Actual outer radius of the pipe, mm
- r2 = (r1 + tk)
- Rs = Surface thermal resistance =1/h oC-m2/W
- Rl = Thermal resistance of insulation =tk/k ºC-m2/W
The heat flow from the pipe surface and the ambient can be expressed as follows
H = Heat flow, Watts= (Th-Ta)/(Rl+Ra)=(Ts-Ta)/Rs
From the above equation, and for a desired Ts, Rl can be calculated. From Rl and the known value of thermal conductivity k, the thickness of insulation can be calculated.
Equivalent thickness of insulation for pipe, Etk = (r1+tk) X ln{(r1+tk)/r1}
Some more resources for you:
Piping insulation: Important Considerations for Piping Engineer
Corrosion under insulation: A Presentation
very good information , thank you
Great reading and extremely comprehensive post – pretty much covers everything…
How do I know if a line number requires insulation or not and what does the suffix IH and NI mean
IH means insulation and NI means no insulation
Sooooooper❤️
What is R_a ?
thanks for the good information
N Saravanakkumar
Thanks!