Nitrogen blanketing is the process of supplying the N2 (or other inert gas) gas to the vapor space of a container to control its composition. It provides improved process safety and better product quality, along with a longer equipment life cycle. Nitrogen blanketing practices can be applied to a wide variety of container sizes. The process is widely used for storage tanks, and because of that, nitrogen blanketing is often termed tank blanketing, tank padding, or nitrogen padding. In this article, we will explore more about nitrogen blanketing: its procedure, purpose, application, and controls.
What is Nitrogen Blanketing?
Nitrogen blanketing is the process of supplying the storage tank with an inert gas (the most economical), such as nitrogen, to counteract the effect of oxygen (and other reactive gases) on the storage material, which is usually liquid. When purging the vessel with inert or inert gas, the vessel material does not come into contact with oxygen. This extends product life and mitigates potentially explosive conditions by reducing the risk of chemical reactions, corrosion, and fire hazards.
Applications of Nitrogen Blanketing
Nitrogen blanketing is used in all industries wherever flammable or explosive products are used or generated. Some of the industries that widely use nitrogen padding methods are:
- Chemical Plants and Petrochemical Industries: In these sectors, nitrogen blanketing is crucial for preventing unwanted chemical reactions and ensuring the stability of sensitive products. It helps maintain the purity of chemicals and pharmaceuticals by preventing contamination.
- Oil and Gas Industry: Nitrogen blanketing is employed to safeguard storage tanks and pipelines containing volatile substances. It prevents the formation of explosive mixtures and minimizes the risk of corrosion.
- Food Processing: To extend shelf life and preserve the quality of food and beverages, nitrogen blanketing is used in packaging and storage. It helps prevent oxidation, which can lead to spoilage and degradation.
- Electronics Manufacturing: Nitrogen blanketing is used in the manufacturing of electronic components to prevent oxidation and contamination of sensitive materials.
- Pharmaceutical industries
- Petroleum Refining plants
- Aerospace industries
- Ships and Transformers
- Chemical and Petrochemical Transportation Industry,
- Chemical tankers
- Personal Care, Cosmetics, and Semiconductor.
Gas blanketing is used to protect a diverse range of products, including but not limited to adhesives, catalysts, chemicals, fragrances, fuels, industrial coatings, inks, deionized water, fats and oils, flavors, foods, juices, pharmaceuticals, photographic chemicals, solvents, volatile combustibles, sealants, soaps, and water for injection.
Purpose of Nitrogen Blanketing
The blanket helps to maintain constant inert conditions for the product in the container. The goal is to prevent explosion, discoloration, polymerization, and other unwanted quality changes. Here, the flow and pressure of the inert gas stream and/or the oxygen level in the exhaust gas will control the operation. The main benefits that a nitrogen blanketing system provides are:
- Increased safety by reducing the explosion possibility by reducing the amount of oxygen in the vapor space of a chemical storage tank.
- The reduced potential of fire and explosion.
- Increased equipment life by reducing the corrosion possibility due to oxygen and moisture reactions.
- Reduced chances of product degradation by creating the blanket.
- Reduced possibility of product property alteration.
- Decreased product evaporation
- Enhanced overall efficiency of industrial processes by eliminating contamination.
Nitrogen blanketing can be applied to a variety of container sizes from a multi-million-gallon tank to a large or smaller container. Although blanketing is a factory practice, there is scope for improvement. Bad choices may add costs, increase nitrogen wastage, or increase plant emissions.
Nitrogen Tank Blanketing Procedure
Before diving into the nitrogen blanketing procedure, let’s recapitulate some of the basics. We all know that a fire happens when all three elements; an ignition source, fuel, and oxygen are present. Removing any of these three elements will remove the possibility of fire. The space above the tank contains a mixture of air and steam from flammable materials that are being stored, eg solvents.
Mixtures of solvent vapors and air will only ignite and burn if the vapor mixture is within the flammability of the solvent and an ignition source is present. This can lead to tragic consequences such as serious injury to people.
Static charges can develop within the system or within the solvent itself, creating a source of ignition although storage tank facilities may be electrically grounded to reduce the probability of ignition.
A storage tank can be made inert in any of the following three ways:
- Limiting the Oxygen Concentration (LOC) of the vapor space
- Reducing the fuel concentration below the Lower Explosion Limit (LEL), or
- Increasing the fuel concentration above the Upper Explosion Limit (UEL).
The manufacturer’s Material Safety Data Sheet (MSDS) provides the values of LEL and UEL for a chemical. LOC values are often found in chemical industry handbooks and guides such as the National Fire Protection Association (NFPA) Guide. Flammability limits of mixtures of gases, combustibles, and inert substances for high temperature and pressure can be determined by computational methods.
Refer to Fig. 1, which provides a sample example of a flammability envelope for Hydrogen in Air. The combustion will not take place beyond the LOC.
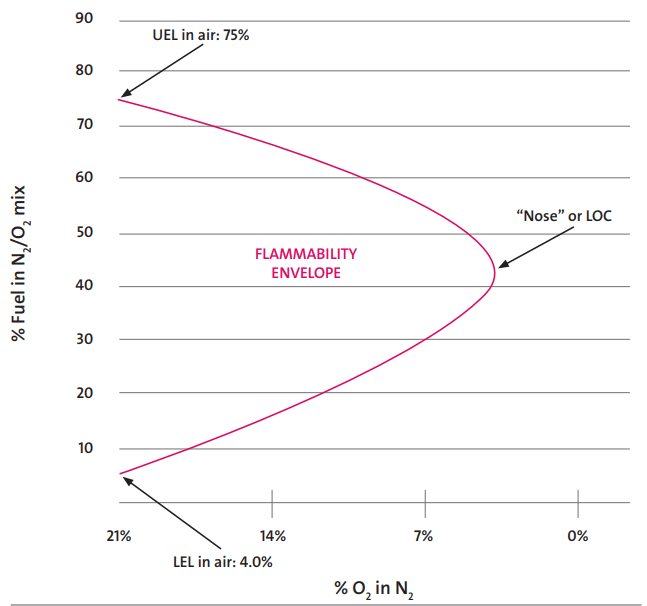
When considering a new or improved blanketing design, the first factor to take into account is the type of tank. This will determine if blanketing is required or not. The following rules apply to the storage tanks for the nitrogen blanketing philosophy.
- When a fixed roof tank stores any flammable material, nitrogen blanketing must be applied.
- Floating roof tanks do not need tank padding.
- Internal floating roof tanks or covered floating roof tanks occasionally need nitrogen blanketing as there is the possibility of vapor build-up.
Fig. 2 explains the above concept of storage tanks requiring nitrogen blanketing.
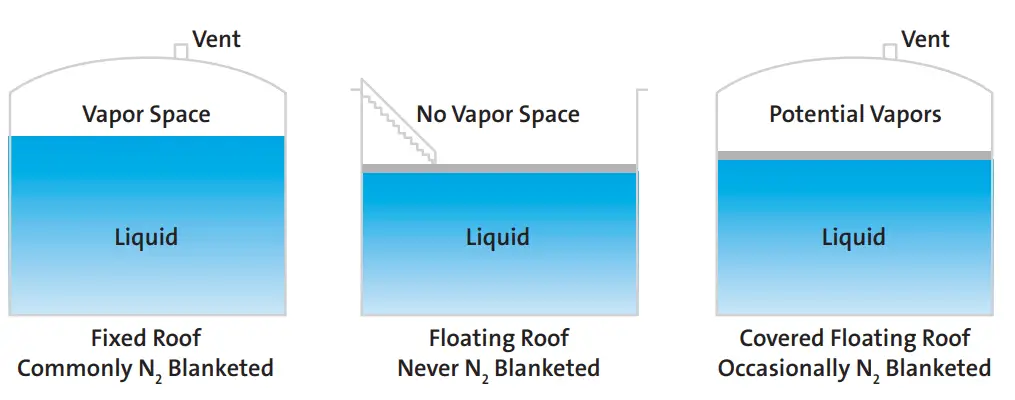
In addition to the storage tanks and similar vessels, a number of sealed tanks like Non-pressurized spaces may also require blanketings, such as a pneumatic conveyor, powder and dust hoppers, or controlled atmospheric tanks.
The nitrogen blanketing procedure maintains a concentration of nitrogen within the padded tank/vessel. It also prevents the reintroduction of oxygen and other gaseous contaminants within that region. The nitrogen blanketing procedure usually employs the following methods:
- Automatic pressurized vessel purging
- Continuous pressurized nitrogen blanketing using manual controls
- Oxygen concentration measurement and variation
- Dual oxygen concentration and pressure monitoring
- Maintaining a steady pressure of gaseous nitrogen and eliminating oxygen.
Nitrogen Control by Continuous Purge
The continuous purge system uses a continuous flow of nitrogen, which is simple to do but can lead to high nitrogen consumption. Nitrogen can also remove vapor in the headspace and put more uploads factory emissions management system. In addition, air may enter empty space if the tank is empty too quickly and the liquid level drops too quickly. Despite these problems, this type of system continues to be used because It’s very simple and quick to make. Replace this method with pressure or concentration control can lead to savings.
Nitrogen Control by Pressure Control
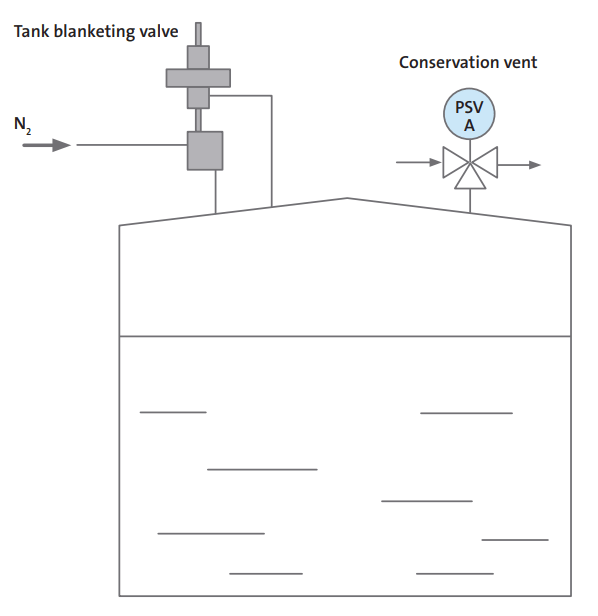
Pressure control systems are used for closed tanks, that can hold pressure. A valve detects pressure in the headspace of the tank and supplies nitrogen accordingly. Headspace pressure control can be set quite low; less than an inch in the water column is enough. When the tank is discharged, the liquid level is dropped, pressure is reduced, and nitrogen is added. When the tank fills, the pressure increases, and nitrogen escapes through the vent valve.
Nitrogen Blanketing Calculation
Simple Calculations for nitrogen requirement are shown where basically, the nitrogen requirements of blanketed tanks have two parts:
- Nitrogen as required by the flow, or material flow through the tank(NW); and
- Nitrogen is required by heat breathing or the increase and decrease of the liquid level due to external temperature (NTB). Of these two sections, usually, the NTB is significantly larger.
The equations mentioned in Fig. 4 are used to calculate the N2 requirement for the Nitrogen blanketing process.
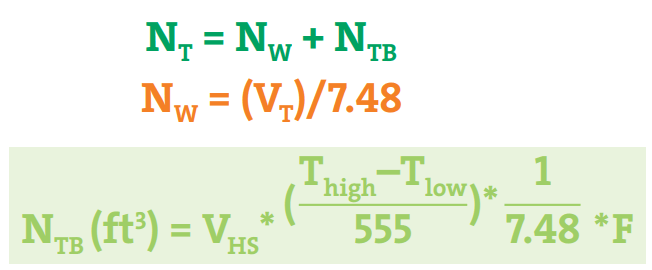
Here,
- NT= Total volume of nitrogen required per month (ft3)
- NW = Required Nitrogen by the material flow through the tank (working throughput)
- NTB = Required Nitrogen by the rise and fall of the liquid level owing to the external temperature conditions (thermal breathing)
- VT= total gallons discharged from the tank per month
- VHS = Average empty headspace (gal)
- Thigh = Maximum temperature in the tank (°F)
- Tlow = Minimum temperature in the tank (°F)
- F = Estimated number of temperature swings per month
- 555 = A constant (˚R) pertaining to the vapor space expansion factor
- 7.48 = Gallons to the cubic feet conversion factor
Components of a Nitrogen Blanketing System
A nitrogen blanketing system is designed to create and maintain an inert atmosphere within a container, tank, or pipeline to prevent contamination, oxidation, and other issues. The primary components of a nitrogen blanketing system include:
1. Nitrogen Supply
- Nitrogen Generator: Produces nitrogen on-site from ambient air, usually through processes like pressure swing adsorption (PSA) or membrane separation. It ensures a continuous supply of nitrogen.
- Nitrogen Cylinder or Tank: Stores nitrogen gas if it is supplied in bulk or as a compressed gas.
2. Flow Control Components
- Flow Meter: Measures the rate at which nitrogen is being introduced into the system. This ensures that the right amount of nitrogen is supplied to maintain the desired blanket.
- Regulator: Controls the pressure of the nitrogen gas before it enters the container or system. It ensures that the pressure is maintained at a level slightly above atmospheric pressure to prevent ingress of air.
3. Pressure Control Components
- Pressure Relief Valve: Protects the system from overpressure conditions by releasing excess nitrogen if the pressure exceeds a preset limit.
- Pressure Transmitter/Sensor: Continuously monitors the pressure within the container or system. It provides real-time data for maintaining the correct nitrogen blanket.
4. Blanketing and Purging Components
- Blanketing Valve: Controls the flow of nitrogen into the container to maintain the desired pressure and blanket level.
- Purging System: Used for initial nitrogen purging to remove any existing air or contaminants before the blanketing process begins.
5. Monitoring and Control Systems
- Control Panel: A centralized unit that integrates various sensors, meters, and control valves. It allows operators to set and adjust parameters such as pressure and flow rate.
- Alarm System: Provides alerts for abnormal conditions such as pressure deviations or equipment malfunctions, ensuring timely intervention to maintain system integrity.
6. Safety Devices
- Check Valve: Prevents backflow of nitrogen or other substances into the nitrogen supply lines, ensuring system safety and reliability.
- Ventilation System: Ensures that any excess nitrogen or displaced gases are safely vented to avoid hazardous conditions or buildup.
7. Additional Components
- Filters: Remove particulates and contaminants from the nitrogen supply to prevent damage to sensitive equipment and ensure the purity of the inert atmosphere.
- Temperature Control: Some systems include temperature regulation components if the process is sensitive to temperature variations.
Importance of Nitrogen Blanketing Valve
A nitrogen blanketing valve is a specialized valve used in nitrogen blanketing systems to control the flow of nitrogen gas into a container, maintaining an inert atmosphere. Its primary function is to regulate the pressure inside the container, ensuring it remains slightly above atmospheric pressure to prevent the ingress of air, moisture, and contaminants. This helps protect sensitive products from oxidation, contamination, and potential hazards, while also safeguarding equipment and ensuring safe and efficient operations.
In conclusion, nitrogen blanketing is a vital technique in modern industry, providing safety, quality, and efficiency benefits across a range of applications. Whether in chemical processing, food production, electronics manufacturing, or oil and gas, nitrogen blanketing plays a crucial role in ensuring optimal conditions and safeguarding valuable assets.
Reference and Further Studies
To learn more about the subject refer to the following article: https://www.chemicalprocessing.com/assets/wp_downloads/pdf/nitrogen-blanketing-keeps-employees-and-equipment-safe.pdf
The N2 should be released in the tank directly above the tanks liquids level. I agree on a nitrogen blanket but placing it in the flash zone (area of most vapor release from liquids) is key. You are guaranteed a total inert space being purged this way. At Xtreme Tank Technologies we have developed such a process. This tank tool that releases nitrogen in the exact correct spot is a type 1 fire extinguishing tool as well. Releasing your fire foam with zero splash and most importantly releasing fire foam that is 100% efficient because the fire foam never travels through the tank fire temperature.
i have got few more question on N2 blanketing.
Appreciate if i can get contact details to reach and discuss.
Hi
if it is possible, Please send me this pdf to my email
Thank you
I have a drum 2ft x 7ft (diameter x height) which stores used transformer oil. The drum has a 2 inch pipe on top open to atmosphere. So Pressure/vacuum caused inbreathing/out breathing is not a concern. We want to apply nitrogen padding to keep the air out.
Hi
I came across your post. It’s awesome, dude.
hi
Very nice information you have given, It was amazing.
I am Mechanical Engineer and it is very helpful for me.
Great Information shared!
Thank you for useful information ,
nice info.
Hello. I’m Salvador Renteria. Back in 1985, I presented a technical paper dealing with Nitrogen Blanket Systems that are used to isolate ambient air from contaminating ultrapure water stored in fiberglass tanks. The design is such that it kept ambient air from entering into the top of the storage tank which could then contaminate the deionized water inside the tank. I presented the paper at the Semiconductor Pure Water Conference in San Francisco in 1985. The host for the conference was Margaret Balaz. She owned a company that was probably named Balaz Laboratories. Anyway, the title of the paper was Nitrogen Blanket Systems for High Purity Tanks. Could you email me so that can send my you my paper in PDF form? I would like your opinion on the paper. Thank you in advance. Salvador Renteria, Horizon City, Texas 79928. Cel: 915-727-3540.
Dear Sir,
During loading methanol into storage tank, does the N2 is back into tank or purge to atmosphere?
I’m safety engineer by 32 years experience on offshore. Ì informed somebody who was checking n2 blanking system on top of a Three ethylene glycol, died due to breathing n2 leakage.
N2 in large scale could be too dangerous.
Great information, thank you.
Someone previously asked, but is there a way to get this as a PDF file to my email?
Thanks in advance if possible!
I see that Harris County, Texas is applying nitrogen blankets to 20, 25 and 30k diesel and gasoline tanks to control corrosion and monitor in real time moisture in tank empty spaces. Interesting stuff.
Hi
Need to understand whether it is okay to commission the N2 blanketing system after which fill the tank with product which will displace the vapor space. Is there any concern taking these approach.