A pinch valve is a flex-body valve with a flexible tube that can be pushed together or “pinched” mechanically through a mechanism or through fluid pressure to create a full closure of the flow path. The flow passage of these valves is straight without crevices and moving parts. The soft body of the pinch valves has the ability to seal around the trapped solids. This property makes pinch valves ideal for handling slurries, foodstuffs, and pharmaceuticals. Other industries where pinch valves find application are:
- Cement industry
- Plastic industry
- Pneumatic Conveying industry
- Wastewater industry/Sewage treatment plants
- Ceramic Industry
- Environmental Industry
- Chemical industry
- Mining industry
- dosing and weighing systems
- Commercial vehicle industry
- Bulk and solid handling industry, etc.
Also known as clamp valves, pinch valves are designed to control or shut off the flow from abrasive, granular, fibrous, or corrosive media. The Pinch Valve finds its wide application as an isolating or regulating valve for sludges, dust, emulsions, gaseous materials, powder, compressed air, granulates, pellets, etc.
Working principle of a Pinch Valve
A pinch valve has three major parts: (i) a housing, (ii) an elastomeric rubber sleeve, and (iii) end connections. The elastomeric tube is fitted into the housing from the inlet to the outlet with a pinch bar mechanism and is the only component to be in contact with the flowing media. The end connections can be screwed, bolted, or threaded at each end to provide support and connection.
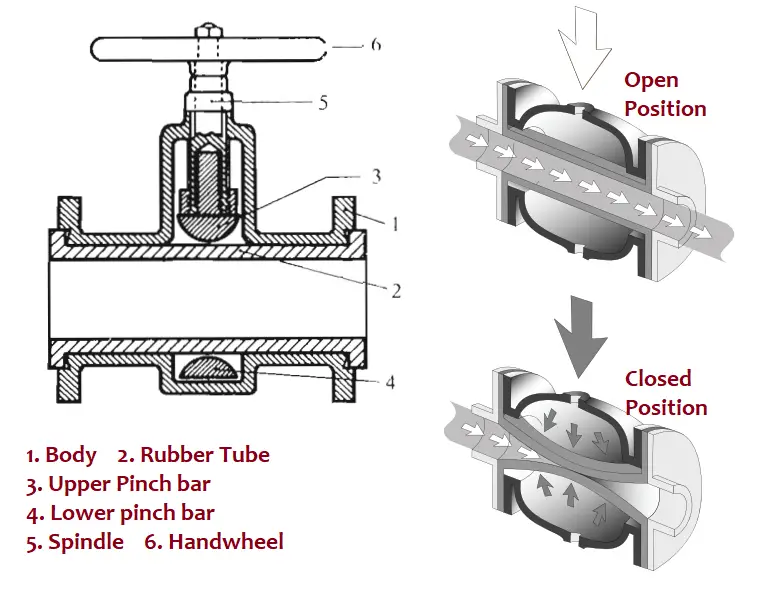
The pinch mechanism can be of various types. A simple screw-operated mechanism with a pinch only on one side of the tube or a differential screw with two pinching mechanisms. Mechanical mechanisms using air or hydraulic pressure to squeeze the tube can also be used.
In normal conditions, the pinch valve is open. When air or hydraulic pressure is applied to the valve, it pushes down the elastomeric rubber sleeve, creating a pinching effect. When the sleeve is fully pinched, the flow is restricted, and the valve is closed. The rubber sleeve in a pinch valve has the capability to trap the particles around it, providing an excellent shut-off.
When the external pressure is released, the force of the flowing media and the rebounding property of the rubber completely open the valve. This fully opened valve provides free flow passage for the media that prevents the valve from blockage. As the media only comes in contact with the rubber tube, the media remains isolated which ensures no contamination.
Types of Pinch Valves
Depending on the body construction, pinch valves are of two types:
Open pinch valves: Usually mechanically pinched valves are of open type without metal body casing. For inspecting the valve body visually and physically during operation, the open construction of pinch valves is used. This is the most simple design but the liner is exposed to the environment.
Enclosed pinch valves: Enclosed-body pinch valves look similar to globe valves from outside. The housing is actually a protective casing for the liner. The pinching mechanism is housed inside the metallic casing.
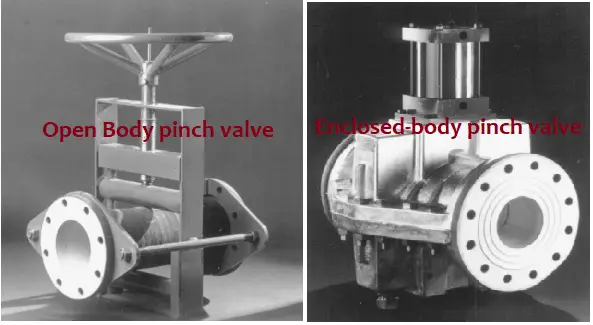
Depending on the pinching mechanism pinch valves can be of the following types:
- Manual Pinch Valve
- Air-Operated Pinch Valve and
- Hydraulic pressure-operated pinch valve.
Pinch Valve Sleeves
The sleeves of pinch valves can be of various types including standard, double-wall for abrasive applications, cone sleeves for throttling purposes, and variable orifice sleeves for improved flow characteristics. Fig. 3 below shows these pinch valve sleeves.
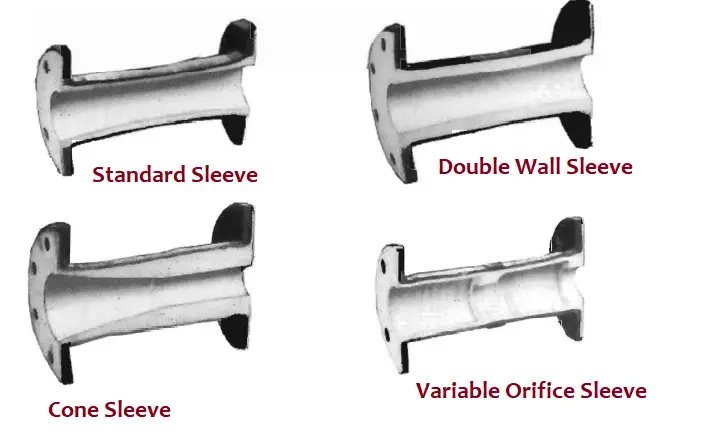
Selection of Pinch Valves
There are various important parameters that must be considered while selecting a pinch valve for a particular application. Some of these parameters are:
Pinch valve body material: Lightweight body material is preferred. The elastomeric sleeve should be carefully selected as it comes in direct contact with the flowing fluid. Usual rubber materials are EPDM, NBR, natural rubber, silicone, food quality rubber, GRS, Neoprene, Butyl, Buna-N, PTFE, FDA, Hypalon, etc. Good abrasion resistance to prevent damage is required.
Opening and Closing Pressure: For proper functioning of the pinch valve, the following pressure differentials must be considered:
- Opening: The operating pressure should be more than the control pressure. The typical control pressure while the opening is 0 bar. Enough pressure differential is required so that the operating pressure is able to open the sleeve.
- Closing: During the closing of the pinch valve, the control pressure has to be more than the operating pressure. In absence of enough pressure differential, the control pressure may not be able to overcome the operating pressure and close the valve by pushing the sleeve.
Design temperature: The valve material should be able to withstand the minimum and maximum temperatures that are expected for the application.
Size and Pressure Rating of Pinch Valves
Pinch valves can be used in a wide range of liquid and liquid-solid mixtures. However, the acceptable size of solids depends on the valve size and the precise design and construction of the tube. Pneumatic and hydraulic-powered versions are suitable for pressures up to 49 Barg. The common size and pressure rating of pinch valves are provided in the table below:
Size | Maximum Pressure, Barg |
DN15 to DN20 | 12 |
DN25 to DN150 | 10 |
DN200 | 8.5 |
DN250 to 300 | 6.9 |
DN350 | 5.1 |
DN400-DN600 | 3.4 |
Advantages of Pinch Valve
With its unique design, a pinch valve provides various advantages like:
- Suitable for use with abrasive and corrosive media
- Low-weight, compact, simple, robust, & straight through design
- Minimum turbulence and friction
- Straight flow path without clogging by the media
- No contamination
- Quick opening and closing time
- Low maintenance cost
- Self-cleaning
- Easy replacement of the rubber sleeves
- Very good sealing properties
- Low energy consumption
- Low wear on the sleeve due to streamlining and laminar flow pattern.
Disadvantages of Pinch Valves
However, there are some disadvantages of pinch valves like
- The pinch valve is not suitable for high-temperature applications as elastomeric material has a limitation on temperature resistance.
- The rubber sleeve can collapse or deform on high-pressure differential and the valve may not open fully.
- The pinch valve is not suitable for vacuum applications.
- Not suitable for pulsating flow.
Hi Anup Kumar Dey,
I’ve enjoyed your write up on the pinch valve. My company Elasto-Valve Rubber Products makes them as well and I’m currious to know what ASTM standard does pinch valve fall under espacillay when it comes to certification and safety codes for pressure rating.
Eric
Dear Sir
We would like to buy pinch valves for our innovative project
Please reply
Thanks
M C David
Mob/ WhatsApp
8157885283
India